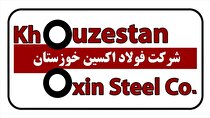
به گزارش میمتالز، وی با اشاره به فعال بودن باتریهای شماره یک و سه کک سازی ذوب آهن، اظهار داشت: باتری شماره ۳ کک سازی که درسال ۱۳۹۱ فعالیت خود را آغاز نمود، پس از گذشت چند سال از بهره برداری، بامشکل دفرمگی، پیچیدگی ونشتی گاز از ناحیه دربها مواجه گردید. طبیعتا جایگزینی دربها با تکنولوژی روز دنیا یعنی دربهای فلکسیبل، مستلزم خروج میزان قابل توجهی ارز از کشور و صرف هزینه بالای هفت و نیم میلیون دلار بود. ضمن اینکه بواسطه تحریمهای ظالمانه انجام این امر در کوتاه مدت نیز میسر نبود.
یزدان پناه گفت: مدیریت عالی کارخانه در یک تصمیم واقدام جسورانه، ساخت این دربها را در داخل شرکت رقم زد. در ابتدا دفتر فنی بخش تولیدات کک ومواد شیمیایی، طی ۵ ماه کار شبانه روزی وبا صرف ۴ هزار نفر ساعت نیروی کارشناسی و تهیه ۲۵۰ شیت نقشه به روش مهندسی معکوس مراحل طراحی وتهیه نقشههای مورد نیاز را به اتمام رساند. پس از آن مراحل ساخت این دربها درمجموعه کارگاههای ساخت مدیریت مهندسی نت آغاز گردید. در این کارگاهها، کلیه مراحل ساخت از جمله ساخت مدل، فرم گیری، ریخته گری، برشکاری، آهنگری، جوشکاری، اسکلت فلزی، ماشین کاری، عملیات حرارتی و مونتاژ انجام گردید.
مدیر مهندسی نت ذوب آهن گفت: در ساخت این دربها، تمامی مراحل پروسههای تولید به طور کامل در کارگاههای ساخت ذوب آهن انجام شد و خوشبختانه موفق شدیم از اواخر سال ۹۷ که مراحل طراحی به پایان رسید تا مهرماه سال ۹۹، جمعا تعداد ۱۶۸ عدد درب را ساخته وجهت مراحل نسوزچینی ونصب، تحویل بهره بردار نماییم.
وی افزود: شاید بسیاری از هموطنان عزیزمان تصورشان از درب، یک قطعه ساده باشد، اما باید اشاره نمود که دربهای فلکسیبل از پیچیدگی بسیار زیادی در ساخت برخوردار هستند. دربهای سمت ماشین باتری کک سازی، از تعداد ۱۳۰۰ عدد قطعه با تنوع ۲۳۰ نوع قطعه تشکیل شده است. ریخته گری این قطعه بسیار مشکل و جنس این قطعه، چدن گرافیت فشرده (کامپکت) است. طول دربهای فلکسیبل ۷ متر میباشد و با توجه به اینکه نسبت ضخامت قطعه به ارتفاع بسیار کم هست، در طی فرآیند ریخته گری همواره نگرانی از بابت خطر ترک خوردگی و پیچیدگی و عدم رسیدن ذوب به نقاط مختلف قطعه وجود داشت؛ که خوشبختانه با دانش فنی کم نظیر پرسنل کارگاه ریخته گری ومدلسازی که در کشور زبانزد همگان میباشد، خوشبختانه هر ۱۶۸ درب فلکسیبل با کیفیت بالا ساخته شد و توانستیم به جمع چند کشور معدود دنیا که سازنده این دربها هستند بپیوندیم.
یزدان پناه با بیان اینکه هزینه ساخت این دربها در داخل کشور و بر اساس محاسبات واحد فنی اقتصادی مدیریت مهندسی نت، حدود یک چهارم قیمت خرید از خارج ارزیابی شده است، گفت: مهمترین مشکل قبل از نصب این دربها، نشت گاز کک بود که آلودگی زیست محیطی برای همکاران شاغل در ناحیه باتریها و نیز ساکنین محترم شهرهای همجوار به همراه داشت. خوشبختانه نشتی این گازها به طور کامل مرتفع شد و این گاز مجدداً در پروسه تولید استفاده میشود. ضمن اینکه اجرای پروژه فوق، تنظیم مناسبتر دمای باتری وکاهش زمان پخت کک وبازیافت مواد اولیه در چرخه تولید را نیز بهمراه داشت. طبیعتا مشکل دربهای طرح قدیم نیز که نیاز به حضور مستمر اپراتور جهت تنظیم دربها را داشت مرتفع گردیده واز ویژگی ارزشمند دربهای فلکسیبل (رگلاژ وتنظیم مستمر بدون نیاز به حضور اپراتور) بهره لازم گرفته شد.
وی افزود: یکی از ویژگیهای خاص و متمایز ذوب آهن اصفهان در مقایسه با صنایع فولادی دگر در کشور، قابلیت استفاده کامل از گازهای فرآیندی است که در سیکل تولید ایجاد میگردد که این ویژگی ارزشمند در سایر صنایع وجود ندارد. به بیان دیگر در ذوب آهن اصفهان گازهای حاصل از فرآیند تولید در بخشهای کوره بلند و کک سازی، مجدداً و به صورت کامل در سایر بخشها (کورههای نورد و نیروگاه ها) وبعنوان سوخت مکمل بهمراه گاز طبیعی مورد استفاده قرار میگیرد که علاوه بر ذخیره انرژی، مصرف گاز طبیعی را به میزان قابل توجهی کاهش خواهد داد.
مدیر مهندسی نت ذوب آهن با اشاره به اینکه رضایتمندی ساکنین محترم شهرهای همجوار همواره از اهمیت ویژههای برای مجموعه ذوب آهن برخوردار بوده است، اضافه نمود که اجرای پروژه مزبور وتعویض کلیه دربهای طرح قدیم وجایگزینی با دربهای فلکسیبل، رضایتمندی ساکنین محترم شهرهای اطراف را به همراه داشته است، گفت: یکی از موارد مهم که همواره مورد تاکید مدیریت محترم عامل قرار میگرفت، ساخت دربهای فکسیبل در حداقل زمان ممکن بود؛ لذا کارگاههای ساخت ذوب آهن اصفهان، از زمان شروع ساخت دربهای فلکسیبل، حتی یک روز ساخت این قطعه را متوقف نکردند و بصورت شبانه روزی و کار در ایام تعطیل، ساخت این دربها را مطابق با گراف زمانبندی پیش بینی شده دنبال نمودند.
وی افزود: ۷۴ عدد درب سمت کک که در مجاورت بیشتری با شهرهای اطراف بودند در مرحله اول تعویض شدند و در مرحله دوم تعداد ۷۴ عدد درب سمت ماشین هم تعویض گردید و تعداد ۲۰ عدد درب هم به عنوان رزرو ساخته شد.
وی در ادامه پخش زنده تلویزیونی اخبار ساعت ۲۰ به ویژگیهای منحصر به فرد مدیریت مهندسی نگهداری و تعمیرات و کارگاههای ساخت ذوب آهن اصفهان پرداخت و گفت: این مدیریت متشکل از سه معاونت تعمیرات، ساخت و بازرسی فنی است. معاونت تعمیرات، عهده دار تعمیرات شبانه روزی، تعمیرات اضطراری، تعمیرات اساسی وهمینطور متولی اجرای کلیه پروژههای حوزه معاونت بهره برداری میباشد.
مدیر مهندسی نت ذوب آهن گفت: در سال ۱۳۹۹ مجموعاً ۱۷۰۰ تعمیرات جاری یا شبانه روزی، ۸۵ مورد تعمیرات اساسی و ۵۲ پروژه کلان در سطح حوزه بهره برداری انجام شد. این مجتمع عظیم صنعتی خوشبختانه در اجرای کلیه تعمیرات مورد نیاز کارخانه، بطور صد در صد خودکفا شده است و اجرای هر گونه تعمیرات وبازسازی در سطح کارخانه بومی سازی شده است که طبیعتا دستیابی به این افتخار بزرگ، برازنده مجموعه بزرگ ذوب آهن اصفهان با قدمت بیش از نیم قرن است.
وی از مجموعه کارگاههای معاونت ساخت این مدیریت بعنوان کارخانجات ساخت که امکانات کم نظیری را در سطح کشور دارند، یاد نمود وافزود: این معاونت عهده دار ساخت و تعمیر کلیه تجهیزات و قطعات مکانیکی میباشد و همچنین طراحی، تکنولوژی، برنامه ریزی و کنترل کیفی قطعات کارخانه را انجام میدهد. همچنین این معاونت، عهده دار نظارت بر کنترل کیفی ساخت قطعات مورد نیاز ذوب آهن در کلیه شرکتها و کارخانجات طرف قرارداد در سطح کشور را برعهده دارد. ایشان افزود طی سال ۱۳۹۹ در مجموعه کارگاههای ساخت، رکورد ساخت ۳۷۰ هزار قطعه در طول سال را ثبت کردیم.
وی تنوع بسیار بالای ماتریال و استفاده از قریب به ۵۳۰ نوع ماتریال مختلف در کارگاه اسکلت فلزی وآهنگری واز طرف دیگر تنوع وزنی قطعات در این کارگاه از ۲۰۰ گرم تا ۱۵۰۰۰۰ کیلوگرم و یا وجود دستگاههای منحصر به فرد در کشور در کارگاه ماشینکاری وعملیات حرارتی نظیر کاروسل بزرگ با قطر کاری ۸ متر وارتفاع ۵ متر و وزن قطعه ۱۴۰ تن وتنوع بیش از ۹۵۰ نوع ابزار در این کارگاه ونیز توانمندی تعمیر انواع مکانیزمهای سنگین در کارگاه تعمیر تجهیزات سنگین را از ویژگیهای ارزشمند این مجموعه توصیف نمود.
یزدان پناه اظهار داشت: در معاونت بازرسی فنی، کلیه تجهیزات مکانیکی، نوار نقالهها، جرثقیلها، آسانسورها، مکانیزمهای روانکاری، پایش وضعیت مکانیزمهای دوار یا CM، تستهای غیر مخرب در سطح کارخانه مورد بازرسی فنی همکاران این واحد قرارمی گیرد.
مدیر مهندسی نت ذوب آهن گفت: در این شرکت برخلاف رویه رایج در بسیاری از صنایع کشور، قریب به ۹۰ درصد تجهیزات و قطعات مورد نیاز در داخل کارخانه ودر کارگاههای ساخت تولید میشود. در این راستا باید گفت، در کارگاه مدل سازی ذوب آهن، که اولین کارگاه متمرکز مدل سازی در کشور میباشد، تا به امروز تعداد ۱۸ هزار مجموعه مدل ساخته شده است و انبار مدلهای ما در ذوب آهن به عنوان شهر مدلها شناخته میشود. در کارگاه ریخته گری، قابلیت ریخته گری برای بیش از ۱۵۰ مارک متنوع وجود دارد که هیچ کارگاه وکارخانهای در ایران این وسعت عملکرد را ندارد.
وی افزود: در کارگاههای ساخت علاوه بر ۱۶ قسمت داخلی، به ۲۴ شرکت و کارخانه داخل کشور نیز خدمات ارائه میشود. یعنی علاوه بر تامین نیازهای کارخانه ذوب آهن، در شرایط ظرفیت خای تجهیزات وکارگاهها، توانمندی رفع نیازهای تجهیزاتی سایر صنایع کشور نیز وجود دارد.
یزدان پناه در دقایق پایانی مصاحبه به عملیات ریومپینگ وبازسازی ونوسازی واحدهای اصلی کارخانه ذوب آهن و دستاوردهای حاصل شده در این زمینه نیز پرداخت و گفت: در ابتدای سال ۱۳۹۸ ریومپینگ ایستگاه ریخته گری شماره ۷ با استفاده از توان داخلی و توسط نیروهای مهندسی نت وبخش فولادسازی صورت پذیرفت که طی آن بجز تجهیزات زیربنایی ایستگاه عمده تجهیزات مکانیکی، انرژیتیک، ساختمانی، برقی واتوماسیونی تحت عملیات بازسازی وبروزرسانی ومدرنیزاسیون قرار گرفت.
همچنین در سال گذشته بازسازی کامل کوره بلند شماره یک به اتمام رسید وطی بازسازی کوره بلند شماره یک صرفا برای پروژه واگن توزین احجام اجرایی توسط مدیریت مهندسی نت مشتمل بر تهیه تعداد ۲۰۰۰ شیت نقشه،۱۱۰۰ تن عملیات دمونتاژ ومونتاژ تجهیزات جدید بود. بر این اساس مدیریت عالی ذوب آهن اصفهان با تجربیات کسب شده طی پروژههای مختلف واز جمله انجام موفقیت آمیز احداث ایستگاه ریخته گری شماره ۵ وریومپینگ ایستگاه ریخته گری شماره ۷ وبازسازی ونوسازی کوره بلند شماره یک واحداث کوره بلند شماره ۳ و. اعلام فرموده اند که ذوب آهن اصفهان با بومی سازی فعالیتهای مربوط به احداث وبازسازی واحدهای موجود وبومی سازی نمودن آنها، توانایی کامل ساخت ایستگاههای ریخته گری و کوره بلند را دارا میباشد.
منبع: ماین نیوز