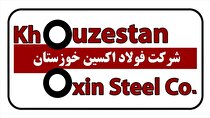
به گزارش می متالز به نقل از عصر مس آنلاین، امور تحقیق و توسعه مجتمع مس سرچشمه امسال در پروژههای تحقیقاتی خود در کنار استفاده از دانشگاهها و مراکز علمی و پژوهشی، تلاش کرده بیش از گذشته از توان تحقیقاتی خود شرکت ملی صنایع مس ایران استفاده کند. «حسن صحرایی پاریزی»، مدیر امور تحقیق و توسعه مجتمع مس سرچشمه میگوید در 76 پروژه تحقیقاتی سال جاری این حوزه 65 درصد پروژهها دانشگاهی و 20 درصد به پروژههای پرسنل داخل شرکت اختصاص دارد. او همچنین میگوید این پروژهها درراستای رفع نیازهای شرکت و خط تولید و آینده توسعهای شرکت برنامهریزی شدهاند. مشروح این گفتوگو را در ادامه میخوانید.
برای امسال 76 پروژه تحقیقاتی تعریف شده که بخش عمده آنها مربوط به خط تولید است. محور اصلی این پروژهها نیز در قالب استراتژیهای کلان شرکت مس است و مباحثی مثل کاهش قیمت تمامشده، افزایش ظرفیت تولید، ارتقای دانش فنی، بهینهسازی مصرف مواد و حاملهای انرژی و بهبود شرایط زیستمحیطی را شامل میشود. بهجز این موارد که سیاستهای محوری ما در تعریف پروژههاست، سیاست دیگر ما این است که مشارکت همه همکاران را در انجام پروژههای تحقیقاتی داشته باشیم؛ هم همکاران امور تحقیق و توسعه و هم سایر پرسنل شرکت بهخصوص پرسنل خط تولید. امسال یک سیاست دیگر را نیز دنبال میکنیم و آن اصلاح پروژههای دانشجویی است؛ درواقع تلاش ما این است که بهرهوری این پروژهها افزایش یابد.
در سال 95 بیش از 80 درصد پروژههای ما دانشجویی بود و حدود 7 تا 8 درصد توسط پرسنل و مجموعه داخل شرکت انجام میشد اما امسال 65 درصد پروژهها دانشجویی و 20 درصد مربوط به پروژههای داخلی است. درواقع میتوان گفت در بخش پروژههای داخلی با یک رشد 2 تا 3 برابری روبهرو هستیم.
بله، اگر اجازه بدهید تعدادی از پروژههای شاخص را نام ببرم و بگویم هر کدام چگونه بر سیاستهای کلان اثرگذار بودهاند. یکی از پروژههای مهم که در سال 1396 به پایان رسید افزایش عیار مس کنسانتره نهایی فلوتاسیون کارخانه پُرعیارکنی یک مجتمع مس سرچشمه با انتقال مس کنسانتره نهایی و اضافه کردن یک مرحله شستوشو بود. همانطور که میدانید هرچه معدن عمیقتر میشود عیار سنگ معدن کاهش می یابد. وقتی سنگی با عیار کمتر به کارخانه تغلیظ منتقل شود قطعاً روی عیار کنسانتره نهایی تأثیر میگذارد و باعث افت عیار کنسانتره میشود که در مراحل بعد هم مشکل ایجاد میکند. پروژهای که انجام شد، با افزودن یک مرحله شستوشو یعنی تلاش برای خارج کردن کانیهای مزاحم از سیستم باعث شد تا عیار کنسانتره نهایی حدود 2.5 درصد افزایش پیدا کند و این افزایش باعث افزایش مس محتوای کنسانتره میشود. این پروژه از جهات مختلف مانند افزایش تولید، افزایش بهرهوری و کاهش هزینه تمامشده (به این علت که بیشتر هزینهها ثابت هستند، بنابراین با افزایش عیار بهصورت مستقیم قیمت تمامشده کاهش می یابد) تأثیرگذار بوده است.
یک پروژه در واحد الکترووینینگ کارخانه لیچینگ مجتمع مس سرچشمه داشتیم. در این بخش از یکسری آندهای سربی استفاده میشود که از محل خط محلول خورده و غیرقابل مصرف میشدند. بنابراین پروژهای برای بررسی علل خوردگی این آندها تعریف کردیم. این آندها دو نوع هستند؛ بخشی وارداتی است و بخش دیگر هم توسط یک شرکت در کرمان تولید میشود. آندی که در کرمان تولید میشد را از لحاظ توزیع عناصر در آلیاژ و خواص و ساختار بررسی کردیم و دیدیم که آند داخلی طول عمر کمتر و خوردگی بیشتری دارد، متوجه علل آن هم شدیم و به یک دستورالعمل رسیدیم که برای ریختهگری آندهای داخلی بهنحویکه طول عمر آنها بیشتر شود، قابل استفاده است.
بله، اتفاقاً یکی از پروژههای سال گذشته ما اصلاح و بهینهسازی لانس مشعلهای ستلر کوره فلش مجتمع مس سرچشمه بود. تغییر تکنولوژی به فلش که در سال 1396 انجام شد یک پیشرفت بزرگ بود. یکی از مشکلاتی که در این کوره به وجود آمده بود دِفُرمه شدن لانس مشعلهای ستلر بود. ما برای حل این مشکل با کمک دانشگاه شهید باهنر کرمان پروژهای در جهت بهینهسازی لانسها تعریف کردیم و انجام دادیم. این کار در کارگاه مکانیک دانشگاه شهید باهنر انجام گرفت و لانسها بهینهسازی شدند و اکنون بدون مشکل در حال کار کردن در کوره فلش هستند.
بله، پروژه مهمی در زمینه کاهش تبخیر آب داشتیم. همانطور که میدانید مجتمع مس سرچشمه در منطقه گرم و خشک قرار دارد به همین دلیل در هر جا که سطح آب باز داشته باشیم تبخیر آن بالا است. برآورد شده تبخیر بالقوه در این منطقه 2.2 متر در سال است. این در حالی است که سطح مخازن آب روباز ما حدود 2 میلیون مترمربع است که اگر در سال 2.2 متر تبخیر داشته باشیم، سالی بیش از 4 میلیون مترمکعب تبخیر در مجموعه اتفاق میافتد. برای جلوگیری از این اتفاق روشهای مختلفی بررسی شد؛ از استفاده از مواد شیمیایی گرفته تا استفاده از پوششها. چند پوشش مناسب هم برای پوشاندن سطح آبها ارائه شد که میزان تبخیر را تا 70 الی 80 درصد و حتی در جاهایی تا 92 درصد کاهش میدهد. با توجه به اهمیت آب، این پروژه از مهمترین پروژههای زیستمحیطی ما به حساب میآید.
چند پروژه مهم دیگر هم در سال گذشته انجام شد که لازم است اشارهای به آنها نیز داشته باشم؛ یکی از این پروژهها، پروژه اندازهگیری قطر و چک کردن مدور بودن مفتول در حال حرکت با استفاده از تکنولوژی پردازش تصویر است. آخرین مرحله تولید مس در پالایشگاه است و بعد از آن مرحله ریختهگری است که در آن مفتول تولید میشود. این مفتولها باید قطر ثابت و شرایط خاصی داشته باشد چون اگر اینگونه نباشد گرید مفتول پایین میآید و قیمت آن کاهش میابد. ما با نصب تعدادی دوربین و تکنولوژی پردازش تصویر قطر مفتول را ثابت نگه میداریم که اثر خوبی روی تولید مفتول در ریختهگری داشته است. همچنین کاهش ضایعات و دورریز آنها و افزایش کیفیت مفتول تولیدی بر اساس استاندارد B49، کاهش گاز مصرفی و... را با استفاده از این تکنولوژی داشتهایم که موجب صرفهجوییهایی هم شده است.
از دیگر پروژهها، پروژه حذف آنتیموان از الکترولیت پالایشگاه با استفاده از رزین است؛ میدانیم که همراه مس عناصر فلزات سنگین هم در معدن وجود دارد. بعضی از این عناصر در مرحله فرآوری مس مزاحمت ایجاد میکند. یکی از این مزاحمتها در پالایشگاه حضور آنتیموان است که بهطورکلی راندمان پالایشگاه را کاهش میدهد و راهحل آن هم خارج کردن این آنتیموانها از چرخه تولید مس است. برای این کار طرحی ارائه شد برای استفاده از رزین که طرح در مقیاس آزمایشگاهی تا 90 درصد موفق به حذف آنتیموان شد. این هم ازجمله پروژههای خوب ما بود که هم موجب کاهش اسید مصرفی پالایشگاه، هم افزایش راندمان پالایشگاه و افزایش کیفیت کاتد خواهد شد.
پروژه دیگری که در این زمینه داشتیم بررسی سرمایش سرباره جهت حصول به بهترین شرایط ورود به کارخانه فرآوری است. میدانیم سالانه مقدار قابل توجهی سرباره تولید و انبار میشود. این سربارهها دارای مقداری مس هستند که میتوان ازطریق فلوتاسیون آن را بازیابی کرد. اما شرایط سرد کردن باید به نحوی باشد که سختی و در نتیجه میزان انرژی مصرفشده برای خردایش آن کاهش پیدا کند تا بازیابی مس از آن مقرونبهصرفه باشد. پروژهای که در این زمینه ارائه شد بهترین روشهای سرمایش را برای بازیابی مس ارائه داد تا بتوانیم استخراج مس از سرباره را به بهترین نحو ممکن انجام دهیم.
پروژه پایش، عیبیابی و استانداردسازی کارخانه تغلیظ هنوز هم ادامه دارد و فاز دوم آن در حال انجام است. این پروژه بهصورت دو دوره دوساله در نظر گرفته شده است که الان در دوره دوم آن هستیم. هماکنون عوامل دانشگاه شهید باهنر که در کارخانه تغلیظ مستقر هستند روی فرآیندهای این کارخانه کار میکنند تا آنها را به شرایط استاندارد برسانند. این پروژه باعث کاهش مصرف آب، افزایش عیار مس کنسانتره و افزایش راندمان میشود که همه اینها بر قیمت تمامشده و میزان تولید مؤثر است.
پروژه سرد کردن سرباره از جمله طرحهای تحقیقاتی توسعهای بهحساب میآید. در بحث معدن و در جهت توسعه معادن مهمترین طرحی که داریم طرح اکتشاف ذخایر پنهان است که از سال 1396 شروع شده است و دو مرحله نمونهبرداری طی آن انجام شده؛ بهطوریکه اساتید دانشگاه دو هفته در منطقه مستقر بودند، بررسیهای لازم انجام شد و نمونهها به دانشگاه بریتیش کلمبیا برای آنالیزهای لازم فرستاده شد. امیدواریم تا پایان امسال نتیجه این کار در منطقه سرچشمه مشخص شود. برای منطقه آذربایجان هم قرار است قرارداد طرحی مشابه بسته شود. البته برای این کار نیاز است دانشگاهی داخلی با دانشگاه بریتیش کلمبیا همکاری داشته باشند تا بتوانیم بحث اکتشاف ذخایر پنهان را در آنجا نیز پیگیری کنیم. البته بخشی از پروژهها مربوط به توسعه آینده شرکت نیست اما در طرحهای توسعه فعلی در حال اجرا هستند؛ مانند همان پروژه لانس کورههای فلش که در دست اجرا است. بهطور کلی امور تحقیق و توسعه همکاری نزدیکی هم با بخش توسعه و هم با بخش تولید دارد.
پروژه تبخیر که پیشتر به آن اشاره کردم جزو پروژههای مهم در چشمانداز 1400 است. در پروژه استانداردسازی کارخانه تغلیظ هم مسأله آب مدنظر بوده و تمام تلاشمان بر این است که در این زمینه با توجه به خشک بودن منطقه مصرف آب را به حداقل برسانیم.
یکی از طرحهایی که برای تجاریسازی آن اقدام شد، پروژه استحصال رنیوم از غبار کورههای خاتونآباد بود که خوشبختانه تجاریسازی شد. امسال هم در حال بهینهسازی همین طرح هستیم؛ روشی که اکنون در حال استفاده است روش رسوب دادن رنیوم است و ما عمدتاً دنبال روشهای جدید هستیم که با استفاده از رزین بتوانیم این کار را انجام دهیم که هم باعث افزایش کیفیت محصول میشود، هم راندمان تولید را بالا میبرد و هم از نظر زیستمحیطی مفید است. طرح حذف آنتیموان نیز در مقیاس آزمایشگاهی بسیار موفق بوده و توانستهایم تا 90درصد آنتیموان را حذف کنیم و امیدواریم بتوانیم این طرح را هم امسال در مقیاس صنعتی به انجام برسانیم.
امور تحقیق و توسعه نقش مهمی در این زمینه دارد؛ زیرا هر قطعهای که میخواهد ساخته شود نیازمند یک پروژه تحقیقاتی مختص به خود است. بهعنوان مثال دو سال قبل طراحی و ساخت کمانه باکت شاول با همکاری امور تحقیق و توسعه و امور معدن انجام گرفت که با هزینه کمی در حدود 50 الی 60 میلیون طراحی و ساخته شد. این کمانه الان نزدیک دو سال در حال کار است و هزینه طراحی و ساخت آن در مقایسه با نمونه خارجی بسیار اندک بوده است.
در حال حاضر نیز چند پروژه مشابه در قسمتهای مختلف مجتمع در حال انجام است؛ به عنوان مثال دو پروژه در معدن داریم که یکی بررسی علل شکست راک و پینیون شاول است که باید ضمن بررسی علل شکست تلاش کنیم تا قطعهای بهجای آن طراحی و ساخته شود. پروژه دیگر مطالعه و بررسی میزان سایش کف اتاق بار کامیونهای معدن مس سرچشمه است. به دلیل حمل سنگ معدن کف کامیونها ساییده میشود. ما اکنون در حال تحقیق هستیم تا ورقی را برای پوشش کف کامیون پیشنهاد دهیم که سایش کف کامیونها را کاهش دهد. این پروژه در کاهش هزینههای معدن بسیار تأثیرگذار است. یک پروژه دیگر هم در زمینه بازیابی عناصر کمیاب داریم که احتمال میدهیم در باطلههای معدن و تغلیظ چنین عناصری وجود داشته باشند و ما هم بنا داریم که در این زمینه نهایت تلاش خود را برای استحصال این عناصر انجام دهیم.