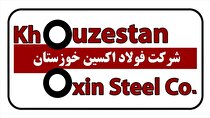
به گزارش میمتالز، در طول سال ۱۳۹۹ رشد قیمتهای حدود سه برابری پلیمرها را شاهد بودیم پس اگر تولیدکنندهای سعی میکرد در تمام فرصتهایی که پیش میآمد اقدام به خرید و دپوی مواد اولیه کند قطعا در ماههای بعد با دغدغه کمتری در بازار اقدام به تولید محصولات خود کرده و سادهترین فرآیند پوشش ریسک نوسان قیمت مواد اولیه را به کار میگرفت.
ولی از اسفند سال ۱۳۹۹ تاکنون بازار مواد اولیه وارد فاز کاهش قیمت شده و استراتژی نگهداری مواد اولیه که در ماههای قبل یک فرصت و نقطه قوت برای تولیدکنندگان محسوب میشد حال به یک تهدید جدی بدل شده است. حتی اگر شاهد روند افزایشی قیمتها با درصد پایین هم باشیم تفاوتی در شرایط ایجاد نخواهد کرد. با توجه به اهمیت بهای مواد اولیه در قیمت تمام شده تولیدات، معمولا کاهش این نرخ آسیب بیشتری به تولیدکنندگان صنعت پلاستیک میزند، چون علاوه بر اینکه عقبگرد و تعویق تقاضا به دلیل انتظار کاهش قیمت از دیدگاه مصرفکننده رخ میدهد؛ از طرف دیگر منجر به یک رقابت منفی از سوی تولیدکنندگان به منظور کاهش موجودی انبار محصولات نهایی با بهای تمامشده بیشتر میشود که این دو مورد منجر به ایجاد یک چرخه پیوسته بین کاهش تقاضا و کاهش نرخ پیشنهادی خواهد شد. مدیریت کنترل موجودی مواد اولیه یکی از مهمترین مباحث در مدیریت زنجیره تامین به شمار میرود و تعیین نقطه سفارش مجدد نیز در مدیریت کنترل موجودی تاثیرگذار است. با توجه به اهمیت زیادی که محققان به تعیین نقطه سفارش مجدد به منظور کاهش هزینههای سازمان و جلوگیری از پیامدهای نداشتن موجودی کافی برای تولید محصولات یا افزایش موجودی راکد قائل شدهاند، در هر صنعت و سازمانی با توجه به شرایط مالی و فناوری و سهم بازار از روشهای مختلفی برای تعیین نقطه سفارش مجدد استفاده میشود. در گذشته از روشهای سادهتری مانند مکانیزم سفارشدهی دوظرفی و امروزه از روشهای مختلف برای طراحی مدلها و الگوریتمهایی برای پیشبینی زمان سفارش مجدد تامین مواد اولیه استفاده میشد که برخی از این مدلها در صنایع خاص به بهبود عملکرد و کاهش هزینههای نگهداری و ممانعت از نداشتن موجودی در هنگام اضطرار منجر شده است. موجودی در سیستمهای تولیدی مدرن مسالهای است که مدیران همه ردهها با آن ارتباط نزدیک دارند. موسسات بسیاری به دلیل انتخاب غلط خط مشی موجودی یا اشتباهات اجرایی در وضعیت بحرانی قرار میگیرند. گاهی دیده میشود موسسهای با بحران بزرگ در اختیار نداشتن نقدینگی مواجه است در حالی که واحدهای ساخت، موجودی پراکنده غیرضروری به صورت کالای نیمه ساخته دارند که در صورت تبدیل به پول، به راحتی مشکل عدم نقدینگی را رفع میکند. در بعضی موسسات نیز در حالی که موجودی مواد اولیه به حد کافی است، دیده میشود که تمام بخش ساخت به علت نبود چند قطعه بیاهمیت، متوقف است.
صاحبنظران معتقدند اطلاعات مانند چسب عمل میکند که اجزای زنجیره تامین را در کنار هم نگاه میدارد. اساسیترین اصل برای پاسخگویی به مشتری، قابل رویت بودن ابتدا تا انتهای زنجیره تامین است. قاعدهای وجود دارد که بیان میکند داشتن موجودی انبار؛ مانع شنیدن صدای بازار توسط اجزای زنجیره تامین میشود و انعطافپذیری را کاهش میدهد. پاسخ سریع، در واقع اطلاعات را با موجودی جایگزین میکند. مسلما جمعآوری اطلاعات به تنهایی کافی نیست. اطلاعات باید تحلیل و به اشتراک گذاشته شود. برای تمام این فعالیتها، فناوری اطلاعات و ارتباطات (ICT) نقشی غیرقابل انکار و جایگزینی دارد.
متاسفانه مزایای داشتن موجودی انبار، هزینههای بسیار زیاد دربردارند که معمولا بیش از ۲۰ درصد ارزش کل موجودی انبار نگهداری شده در طول یکسال است. در واقع تولید در مقیاس اقتصادی، صرفهجویی در هزینههای مازاد است و زمانی رخ میدهد که تولید با حجم بالا بتواند هزینههای واحد را کاهش دهد.
مدیریت مواد اولیه به دلیل اینکه با جریان کلی مواد در یک سازمان سروکار دارد تاثیر شگرفی بر هزینههای نهایی یک محصول دارد. جریان کلی مواد میتواند از تامینکننده به واحد تولیدی و درنهایت به مراکز توزیع بسط پیدا کند. محدوده مدیریت جریان مواد شامل مسوولیتهای طرحریزی، تملک، انبارش، جابهجایی و کنترل مواد و محصول نهایی است. هدف از کنترل موجودی، نگهداری کالا به منظور رفع نیاز در زمان مناسب به اقتصادیترین شیوه است. سطح اقتصادی موجودی را میتوان با تحقیق و یافتن نقطه تعادل بین عناصر هزینه تعیین کرد. اهم روشهای ارزشیابی مربوط به کنترل موجودی عبارتند از (۱) روش کنترل چشمی، (۲) روش دو ظرفی، (۳) روش سفارش با فاصله زمانی ثابت، (۴) مقدار سفارش ثابت، (۵) روش ABC و ... پس از بیان برخی از مفاهیم اصلی کنترل موجودی حال به سوال اصلی خود برمیگردیم که شرکتها باید چه استراتژی را برای مدیریت تامین مواد اولیه به کار گیرند تا در این فضای عدم قطعیت که تولیدکنندگان هر روز با یک اتفاق یا تصمیم یا قانون جدید روبهرو میشوند بتوانند با خطای کم تصمیمات صحیحی در حوزه تامین و نگهداری مواد اولیه اتخاذ کنند. به منظور مدیریت درست میزان موجودی پیشنهاد میشود یک فرآیند مدون در سازمان تعریف شود تا تیم تصمیمگیرنده بتواند بر اساس اطلاعات حاصله از این فرآیند تصمیمات درست و به موقعی در جهت مدیریت موجودی مواد اولیه بگیرد که رئوس پیشنهادی این فرآیند میتواند به صورت زیر باشد:
۱) تعیین یک یا ترکیب چند روش محاسبه نقطه سفارش از بین روشهای متداول موجود
۲) تعیین یک یا ترکیب چند روش محاسبه نقطه ذخیره احتیاطی از بین روشهای متداول موجود
۳) تعیین دوره گردش مواد اولیه و محصول براساس نوع کسبوکار
۴) پایش دورهای نقطه سفارش مجدد از نظر عدم ایجاد کسری مواد در پروسه تولید
۵) پایش مستمر و ارائه گزارش روزانه یا هفتگی قیمت مواد اولیه در بورس کالا و همچنین قیمت مواد اولیه در بازار آزاد
۶) بررسی دورهای تغییرات نرخ ارز
۷) بررسی دورهای قیمت جهانی نفت
۸) بررسی دورهای قیمت جهانی مواد اولیه
بعد از استخراج اطلاعات بیان شده باید اطلاعات در قالب جلسات با حضور افراد خبره صنعت بررسی شده و تصمیمگیری حداکثر هفتگی برای تعیین استراتژی هفته آتی شرکت در مورد مواد اولیه صورت گیرد. اجرای فرآیند عنوان شده میتواند به شفافسازی پیشبینی فضای آتی کسبوکار و گرفتن تصمیم درست برای تیم تصمیمسازی کمک کند.
منبع: دنیای اقتصاد