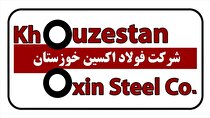
به گزارش میمتالز، رامین کیهان بیان کرد: ماموریت شرکت فولاد غدیر نیریز، مشارکت در توسعه صنعتی و اقتصادی کشور با تکمیل زنجیره ارزش فولاد است. چشمانداز این شرکت، تبدیل شدن به یکی از تولیدکنندگان برتر کشور با تکیه بر محرومیتزدایی و توسعه صنعتی منطقه تعریف شده است. از ظرفیتهای فولاد غدیر نیریز، میتوان به شرایط توسعه زنجیره فولاد با توجه به حمایت سهامدارن، سیاستهای کلان کشور، پروژههای در دست اجرا و پیشبینی شده، ظرفیتهای معدنی منطقه، نزدیکی به معادن مواد اولیه و نیروی انسانی جوان و متخصص اشاره کرد. گفتنی است که این شرکت از بهمن ماه ۱۳۹۶ یک واحد احیا مستقیم در حال کار با تکنولوژی پرد با ظرفیت اسمی ۸۰۰ هزار تن را در اختیار دارد. همچنین دو پروژه مهم فولادسازی با ظرفیت یک میلیون تن و گندلهسازی با ظرفیت دو میلیون و ۵۰۰ هزار تن نیز در این شرکت در حال اجرا هستند.
وی افزود: روشهای متعددی در جهان برای تولید آهن اسفنجی ابداع شدهاند و با توجه به شرایط موجود، مورد استفاده قرار میگیرند که از مهمترین آنها میتوان به روشهای «HYL»، پروفر، «SL/RN»، احیای مستقیم میدرکس و احیای مستقیم پرد اشاره کرد. ایران یکی از بزرگترین تولیدکنندگان آهن اسفنجی در جهان است. غنی بودن کشور به لحاظ منابع سنگآهن، مزیت نسبی بالایی را برای تولیدکنندگان در این حوزه فراهم میکند. نقطه عطف این حوزه را شاید بتوان در ثبت تکنولوژی ایرانی پرد توسط شرکت مهندسی معادن و فلزات «MME» در سال ۲۰۰۶ جستوجو کرد. این تکنولوژی که به عنوان روشی بهینهسازی شده برای تولید آهن اسفنجی مطرح میشود، آخرین تکنولوژی ارائه شده در زمینه احیای مستقیم است و توانسته است بسیاری از مشکلات و محدودیتهای سایر تکنولوژیها را رفع کند و باعث بهبود فرایند احیا شود. شرکت فولاد غدیر نیریز، یکی از شرکتهایی است که در واحد احیای مستقیم خود از این روش بهره میبرد و به نتایج قابل توجهی نیز در این حوزه دست یافته است.
معاون بهرهبرداری شرکت فولاد غدیر نیریز در ارتباط با انواع فرآیندهای تولید آهن اسفنجی، عنوان کرد: اساس کار روش «HYL» که نام آن از اولین کمپانی سازنده مکزیکی به نام «HYSA» گرفته شده، استفاده از گاز احیاکننده حاصل از تغییر فرم گاز طبیعی به بخار آب و استفاده از آن در راکتور ساکن است. پروفر نیز یک کمپانی آلمانی و ارائهکننده روشی برای تولید آهن است که البته این روش مورد استقبال قرار نگرفت و کمتر از ۱۰ درصد از آهن تولید شده به روش احیای مستقیم از این روش به دست میآید. در این روش، سنگآهن غربال شده به صورت لمپ و یا پلت از بالا به داخل یک تنوره استوانهای، شارژ و توسط جریان گاز احیایی که در جهت مخالف سنگآهن حرکت میکند، احیا میشود. گاز احیایی نیز از تغییر فرم مخلوطی از گاز طبیعی و گاز استفاده شده در تنوره تولید میشود. در روش «SL/RN» از کورههای دوار استفاده میشود. تحقیقات اولیه آن پس از جنگ جهانی دوم انجام گرفت و شرکتهای مختلف اروپایی و آمریکایی در شکلدهی این روش نقش داشتهاند که نام این فرایند نیز از همین موضوع نشات گرفته است. سنگآهن در این فرایند به صورت کلوخه یا گندله همراه با زغال ککنشو و مقداری آهک و دولومیت از یک طرف کوره افقی دوار وارد آن میشود. کوره در اثر سوختن زغال و ورود هوا و نرمه زغالسنگ، تا حدود یک هزار درجه سانتیگراد گرم میشود. مواد شارژ شده، در قسمت اول کوره پیشگرم و در قسمت دوم تا ۹۲ درجه فلزی احیا میشوند.
کیهان اضافه کرد: در روش احیای مستقیم میدرکس، گاز احیای گرم از قسمت پایین ناحیه احیا کوره وارد آن میشود، به طرف بالا حرکت میکند و سپس گاز احیای مصرف شده از بالای کوره خارج میشود. آهن اسفنجی داغ احیا شده پس از عبور از ناحیه احیا کوره و قبل از تخلیه شدن تا ۴۰ درجه سانتیگراد خنک میشود. خنک کردن آهن اسفنجی داغ، توسط یک جریان گاز بر خلاف جهت حرکت آهن احیا شده انجام میگیرد. گفتنی است که در حال حاضر بخش عمده تولید آهن اسفنجی در دنیا، با تکنولوژی میدرکس انجام میشود. روش پرد (PERED) نیز یک تکنولوژی ایرانی است که توسط شرکت «MME» در سال ۲۰۰۶ در کشور آلمان، ثبت شد و عملکرد آن علیرغم تشابه در برخی موارد پایه با تکنولوژی میدرکس، به سبب تغییرات انجام شده در بعضی نقاط فرایندی و تجهیزاتی متمایز است. با راهاندازی اولین پروژه این طرح در سال ۱۳۹۶ در شادگان و نیز در میانه، نیریز و بافت، شکوه و اقتدار این طرح ایرانی نمایان شد.
وی در ارتباط با تکنولوژی پرد تاکید کرد: در تکنولوژی پرد، مواد اولیه یا خوراک کوره (گندله یا همان اکسید آهن به همراه آب آهک)، از بالای کوره توسط نوار نقاله به داخل کوره شارژ میشوند. در ناحیه احیا، بار کوره با سرعت یکنواختی حرکت میکند و عمل احیا نیز طی مدت زمان ۶ تا هشت ساعت انجام میشود. در فرایند احیای اکسید آهن به روش پرد (جداسازی اکسیژن آهن به وسیله گازهای احیایی هیدروژن و مونواکسیدکربن)، گاز احیا با درجه حرارت ۸۸۵ درجه سانتیگراد و ترکیب کنترل شده از پورتهای باستل وارد ناحیه احیایی کوره میشود. این منفذها توسط آجرهای نسوزکاری در کانالهای درونی کوره به گونهای طراحی شدهاند که گاز پس از ورود به کانالها از طریق این دریچهها، به سمت پایین (جلوگیری از پر شدن پرتها توسط گندله) و مرکز کوره هدایت شود. این عمل باعث میشود که گاز به طور یکنواخت داخل کوره منتشر شود و به سمت بالا جریان یابد. گاز احیا در خلاف جهت حرکت اکسیدهای آهن در کوره و به صورت متناوب به سمت بالا حرکت میکند و این امر باعث تسریع در واکنش احیای درون کوره میشود. گفتنی است که بخش عمده واکنش احیا، در قسمت مرکزی و بالایی کوره صورت میگیرد. با توجه به گرماگیر بودن فرایند احیای اکسید آهن، گرمای لازم برای انجام واکنشهای احیا و همچنین رساندن دمای اکسید آهن شارژ شده تا دمای واکنشپذیر، توسط گرمای گاز احیا تامین میشود.
معاون بهرهبرداری شرکت فولاد غدیر نیریز خاطرنشان کرد: همان طور که پیشتر نیز اشاره شد، به دلیل وجود استیم درام «Steam drum» و سیستم کنترل بخار به صورت جداگانه، تنظیم نسبت هیدروژن به CO به شکل بهتری انجام میشود که این مسئله باعث شده است تولید بیشتری در مقایسه با روش میدرکس حاصل شود؛ بنابراین با این روش، مصرف برق را نیز میتوان نسبت به روش میدرکس تا حدودی بهبود بخشید؛ اگرچه مقایسه این دو تکنولوژی به سبب سابقه و تعدد کارخانههای موجود در دنیا منطقی به نظر نمیرسد، اما در سطح کلان و با توجه به سابقه بهرهبرداری چندساله، میتوان این تکنولوژی را از لحاظ فرآیندی همردیف و حتی در بعضی موارد بهتر از تکنولوژی میدرکس دانست.
کیهان اضافه کرد: تلاش پرسنل شرکت و تغییرات مثبت انجام شده نظیر کاهش آب بلودان «Blowdown» و همچنین کاهش مصرف برق در ازای هر تن تولید، در کنار مزایای تکنولوژی پرد از جمله بستر احیایی وسیعتر نسبت به میدرکس، کاهش توقفات ناشی از مشکلات بردن فیدرها، تنظیم پارامترهای فرآیندی به دلیل کنترل بخار به صورت جداگانه و ... سبب شدهاند که مصرف انرژی در سطح پایینتری نسبت به مابقی واحدها قرار گیرد و چالشهای زیستمحیطی نیز کاهش یابند.
وی در پایان یادآور شد: تاثیر این روش را در فرایند تولید و سودآوری شرکت، از دو جنبه میتوان بررسی کرد. نخست، بر اساس عملکرد حدود پنج ساله در چهار شرکت داخلی که این تکنولوژی در آنها به کار گرفته شده و نتایج آن درحوزههای مصرف، کیفیت، بهرهوری و شاخصهای اقتصادی موجود است و میتوان آن را در حالت کلی قابل قبول ارزیابی کرد، اما مسئله مهم، در سیکل هزینههای بهرهبرداری به خصوص در دوره تعویض کاتالیست و لولههای تیوب ریفرمر و نسوز باید جستوجو شود که با توجه به بازه زمانی مورد بحث، قابل ارزیابی نیست و همچنان باید به انتظار نشست.
منبع: فلزات آنلاین