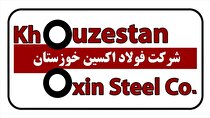
هماکنون فولادهای پیشرفته با استحکام بالا و آلیاژهای آلومینیومی، دو رقیب اصلی در صنعت خودروسازی بهشمار میروند.
از نقطهنظر هزینه تولید برای خودروسازان باید اذعان کرد که بنا به تخمینهای ارائهشده، هزینه کاهش وزن هر کیلوگرم از خودرو با استفاده از فولادهای پیشرفته با استحکام بالا، بین ۲ تا ۲/۵ دلار و با استفاده از آلیاژهای آلومینیومی، بسته به نوع آلیاژ، بین ۳ تا ۶ دلار برآورد شده است. این رقم برای آلیاژهای منیزیمی و کامپوزیتهای کربنی حتی بیشتر شده و به سطح ۱۶دلار نیز میرسد. از اینرو خودروسازان باید متحمل هزینههای بیشتری برای کاهش وزن خودروهای خود شوند. درحالیکه در گذشته، هزینه هر کیلوگرم کاهش وزن در خودروها، رقمی بین یک تا ۲ دلار بود، این مقدار امروزه بین ۴ تا ۱۲ دلار افزایش یافته و انتظار میرود با کاهش بیشتر وزن خودروها، کاستن هر کیلوگرم از وزن خودروهای سبک جدید، هزینههای بیشتری را حتی تا ۲۰ دلار برای خودروساز به همراه داشته باشد. این هزینه بالا در کاهش وزن، بهطور عمده محدود به خودروهای لوکس و گرانقیمت خواهد بود. بدین ترتیب انتظار میرود آلومینیوم و فولادهای پیشرفته در سالهای آینده همچنان سهم ۲۰ تا ۳۰درصدی خود را در هر خودرو حفظ کنند.
رضا زائرحیدری، تحلیلگر بازار فولاد و مواد اولیه درباره ضرورت پیش رفتن به سمت تولید فولادهای پیشرفته که در خودروسازی کاربرد دارند، گفت: فولادهای سبک یا پیشرفته(Advanced High-Strength Steels) (AHSS)، در حقیقت این نسل جدید فولاد با مقاومت ۳برابر و وزن ۴۰درصد، کمتر امروزه کاربرد بسیاری دارند. در کشور ما از این دست فولادها تولید نمیشود یا به صورت خیلی محدود در حال تولید است. وی در پاسخ به این پرسش که تا چه اندازه ضرورت دارد که به سمت فولادسازی سبک پیش برویم، گفت: در کل تمامی فرمولهای فولادسازی در حال تغییر است. شما اگر آمار کشورهای پیشرفته را مشاهده کنید، متوجه میشوید تولیدات فولادی با وزنهای متداول امروزی هر سال در حال کاهش است، چراکه وزن محصول کاهش پیدا میکند، اما در مقابل ارزش آن افزایش مییابد. وی در ادامه خاطرنشان کرد: البته درحالحاضر مهمتر از وزن فولاد خواص فولاد مانند مقاومت است که دارای اهمیت است. زائرحیدری با این توضیح که در خودروسازی مقاومت فلز به کار برده شده در آن از اهمیت بالایی برخوردار است، عنوان کرد: آلومینیوم سبکتر است، ولی شکلپذیری خوبی ندارد و برای ماشینهای جدید مناسب نیست. بنابراین آلومینیوم نتوانست جایگاه واقعی خود را در صنعت خودرو بیابد، اما آلیاژهای فولاد و آلومینیوم میتواند ترکیب بهتری ایجاد کند. وی با اشاره به تولید فولادهای پیشرفته در ایران خاطرنشان کرد: درحالحاضر هیچ واحد فولادی در ایران فولاد سبک تولید نمیکند. البته یک واحد در فولاد مبارکه ورقهای سرد را به گالوالوم تبدیل میکند که به نسبت عملکرد خوبی دارد. اما در کل تولید بالایی در این زمینه در کشور وجود ندارد. درحالیکه در دنیا هرچه بیشتر به سمت تولید فولادهای سبک پیش میروند، ما نیز باید بتوانیم به سمت تولید فولادهای سبک پیش برویم. این کارشناس فولاد در پاسخ به این پرسش که آیا برای پیش رفتن به سمت فولادهای سبک باید فولادسازیهای جدید ایجاد کرد یا میتوان همین فولادسازیها را تجهیز کرد، گفت: میتوان همین فولادسازیها را تجهیز کرد، در فرآیند تولید اینگونه فولادها ساختار مولکولی فولاد را تغییر میدهند و مادهای با مقاومت تیتانیوم تولید میکنند، اما پس از آن تغییرات شدید میشود و شاید نتوان با همین واحدها پیش رفت. در کشورهای آسیایی مرکز تحقیقات پوسکو در کرهجنوبی در این زمینه پیشتاز است. زائرحیدری با اشاره به صرفهجویی که در تولید فولادهای پیشرفته روی میدهد، عنوان کرد: در تولید فولادهای خاص میتوان ۵۰ درصد صرفهجویی کرد و این یعنی میلیاردها دلار صرفهجویی. وی با تاکید بر این موضوع که تولید فولاد معمولی به نوعی وقت و هزینه تلف کردن است، عنوان کرد: تولید فولاد معمولی به نوعی وقت تلف کردن بهشمار میرود. کارخانههای ما متاسفانه برای تحقیق و توسعه هزینه نمیکنند، یعنی ما در زمینه متالورژی دانشمند، با مفهومی که شرکتهایی مانند پوسکو یا به عنوان مثال هیوندایی استیل دارند، نداریم. البته فناوریهای جدید انحصاری هستند، یعنی بهراحتی لیسانس آن را به کسی نمیدهند. وی تاکید کرد: به عقیده من، ما به مرکز تحقیقات فولاد نیاز داریم، البته منظورم دانشگاه نیست، بلکه جایی است که روی فولادهای جدید تحقیق شود.
با این حال در ایران نیز اقداماتی از این دست انجام شده است؛ به طور مثال شرکت فولاد مبارکه در زمینه فولادهای پیشرفته کارهای مطالعاتی و اجرایی خود را آغاز کرده است. در اینباره مجید رضاپور، مدیرعامل شرکت صنایع ورقهای پوششدار تاراز عنوان کرد: خودروهای جدید براساس فولاد خاص و پیشرفته ساخته میشود که سبکتر هستند. فولاد مبارکه نیز در این زمینه پیشگام شده و در یک سال گذشته بین این مجتمع فولادی با پژو سیتروئن قرارداد بسته شده که تمام نشان (برند)ها و محصولات جدیدی که پژو سیتروئن در ایران تولید میکند، با فولادهای آلیاژی کششی با استحکام بالا تولید شود. رضاپور در ادامه خاطرنشان کرد: در یک سال گذشته مطالعاتی برای تولید این فولاد از سوی فولاد مبارکه آغاز شده است. موضوع قابل توجه در تولید این نوع فولادها، تولید نورد گرم و سرد است. یک سری مطالعات در نورد گرم مطرح است که درحالحاضر امکانات آن موجود نیست. البته پروژه نورد گرم مجتمع فولاد که به پروژه شهید خرازی معروف است توانایی تولید این ورقها را دارد. وی در ادامه خاطرنشان کرد: زمانی که به تولید نورد گرم دست پیدا کردیم و با توجه به نورد سردی که در مجتمع فولاد است، میتوانیم نورد سرد آن را نیز تولید کنیم. این پروژه در حال مطالعه، اجرا و قرارداد است. مدیرعامل شرکت صنایع ورقهای پوششدار تاراز در پاسخ به این پرسش که درحالحاضر هیچ تولیدی برای ورقهای سبک ندارید، عنوان کرد: در برخی گریدهای خاص مانند ایاف و... درحالحاضر توانایی تولید داریم و در کارخانه ورق خودروی چهارمحال و بختیاری بنا است یک دوره آزمایشی تولید داشته باشیم تا بعدها بتوانیم تولید انبوه داشته باشیم. رضاپور در ادامه یادآور شد: البته برای سایر کیفیتها نیز قرار است یک پروژه جدید تعریف شود و در این زمینه مجتمع فولاد در حال مطالعه برای این کیفیتهاست. حالا یا در خود مجتمع فولاد یا در مکان دیگری مکانی برای احداث در نظر گرفته خواهد شد تا بتوانیم خط گالوانیزه جدید با تولید ورقهای سبک راهاندازی کنیم. وی در ادامه تاکید کرد: تا ۱۴۰۴میلادی براساس توافقی که با پژو سیتروئن شده، قرار است تمام محصولات که از طریق این شرکت تولید میشود، برمبنای ورقهای جد۰/۶میلیمتر استفاده میشود که با همان خواص کیفی اما با استحکام و مقاومت در برابر ضربه تولید میشود. مدیرعامل شرکت صنایع ورقهای پوششدار تاراز در پاسخ به این پرسش که درحالحاضر چه میزان واردات این ورقها انجام میشود، گفت: بخشی از این ورقها را ایرانخودرو و سایپا وارد میکند. البته درحالحاضر تمام قطعات داخلی خودروها که گالوانیزه است را میتوانیم تولید کنیم و ایرانخودرو نیز استفاده میکند. اما سایپا از ورقهایی که گالوانیزه نیست، استفاده میکند. با این حال در مدلهای جدید مقرر شده که به سمت ورقهای جدیدتر و سبکتر پیش برویم.رضاپور در ادامه با اشاره به اینکه این ورقها در وزن خودرو چه تاثیری دارند، گفت: زمانی که اتاق ماشین ۱۰۰درصد از ورق تامین میشود، حدود ۸۰۰ تا ۸۵۰ کیلوگرم فلز در آن بهکار برده میشود. اما درحالحاضر استانداردهای جهانی به سمت ۶۰۰ تا ۵۵۰کیلوگرم فلز سوق داده میشود. به هر میزان از وزن فلز در خودرو کاسته شود، به همان میزان هم مصرف سوخت کاهش پیدا میکند.