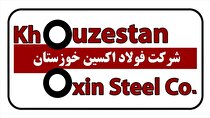
به گزارش میمتالز، با توجه به این موضوع که شرکت تامین شرکت ملی مس یک زنجیره کامل است، بدون شک بومیسازی در تمام بخشهای این زنجیره به خوبی طی سالهای گذشته روی داده است.
مدر برنامهریزی و نظارت شرکت ملی صنایع مس ایران با اشاره به این موضوع که زنجیره تامین مس در شرکت ملی مس یک زنجیره کامل است، گفت: زنجیره تامین مس شامل گروه اکتشافات، دارا بودن معادن فعال و پویا، استخراج سنگ معدن، فرآیند فرآاوری، کارخانههای ذوب تا تولید محصول نهایی کاتد، کاملترین زنجیره تامین است که به نوبه خود یک زنجیره کامل بهشمار میرود. در این زنجیره طی سالهای گذشته بومیسازی به نحو مطلوبی انجام گرفته است.
سعد عبدی در ادامه خاطرنشان کرد: در این شرکت بیش از ۹۰ درصد نسوز مورد نیاز کورهها و ۸۵ درصد قطعات مکانیکی پرمصرف و بیش از ۶۵ درصد قطعات برقی و۶۰ درصد قطعات الکترونیکی ابزار دقیق بومیسازی شدهاند. از سوی دیگر، خریداران شرکت اعم از داخلی و خارجی به تولیدات شرکت مس بسیار علاقهمند هستند. همچنین کیفیت تولیدی محصولات شرکت فراتر از استانداردهای ثبت شده جهانی است، بنابراین زنجیره تامین شرکت، زنجیره تامین قابلاتکایی است. در حال حاضر نیز بیش از ۲هزار سازنده و بیش از ۴هزار تامینکننده قطعات و تجهیزات خارجی و داخلی و خدماتدهنده داریم.
عبدی در ادامه با اشاره به شروع نوآوری در صنعت مس عنوان کرد: نوآوری و بهرهگیری از فناوریهای جدید در صنعت مس همواره از سالیان قبل در شرکت رسوخ کرده و در ادامه در ۱۰ سال اخیر با اصلاحات همهجانبه خطوط تولید، پویایی و شکوه شرکت محفوظ شده است، برای نمونه در کنار کارخانه تغلیظ فاز یک سرچشمه، دو فاز دیگر به عنوان فاز ۲ با فناوریهای جدید اروپایی راهاندازی شده یا کورههای قدیمی ریورب ذوب را کلا از مدار خارج کرده و از فناوری فلش با سوخت کمتر، نیاز به تعمیرات به مراتب کمتر، نیروی انسانی متخصصتر و با ارزشافزوده بالاتر استفاده کردهایم.
وی در ادامه تاکید کرد: مهمترین موضوع این است که تمام این فناوریها با حفظ محیطزیست همراه بوده است، برای نمونه بهرهگیری از کورههای با فناوری جدید حتما باید در کنار کارخانه اسیدسولفوریک باشد که خوشبختانه در شرکت ملی مس این کار انجام شده و در سالگذشته نیز بیش از ۷۰۰ هزار تن فروش اسیدسولفوریک داشتهایم.
مدیربرنامهریزی و نظارت شرکت ملی صنایع مس ایران در پاسخ به این پرسش که برای راهاندازی تمام طرحهای شرکت مس در تمام فازهای توسعه آن تا چه اندازه از توان داخلی بهره گرفتهاید و در این راستا بومیسازی انجام شده است، گفت: باید این موضوع را بپذیریم که در توسعههای خود برخی فناوریها در حال بهروز شدن هستند و لازم است این فناوریها را به دست آوریم، بنابراین ضرورت دارد که برای به دست آوردن این فناوریها ارتباط بیشتری با دنیا داشته باشیم.
عبدی در ادامه افزود: کارخانههای دنیا در حال بهروز شدن هستند و تجهیزات آنها کوچکتر و توانمندیهای آنها چند برابر شده است. در زمینه فلوتاسیون و کنسانترهسازی با توجه به اینکه به مرور عیار خاک معادن در حال کاهش است، بنابراین بیشتر فناوریها در حال بهروز شدن هستند. برخی تجهیزات و نحوه قرارگیری و سایزبندی و حتی مواد شیمیایی آنها تغییر کرده است، از این رو باید همزمان با این تغییرات جلو رفت تا مجبور نباشیم با فناوری ۱۰سال پیش کارخانههای خود را تجهیز کنیم.
وی در ادامه توضیح داد: کارخانههای پیشرفته دنیا با عیار ورودی مس کمتر از ۳/ ۰درصد کار میکنند، ولی فناوری آنها به گونهای است که غنیشوندگی آنها بالای ۶۰ برابر خاک ورودی رسیده است. پیادهسازی این سیستمها با این فناوریها از الزامات امروز شرکت مس بهشمار میرود و در استراتژی ابلاغی شرکت آمده است.
مدیر برنامهریزی و نظارت شرکت ملی صنایع مس ایران در ادامه خاطرنشان کرد: شرکت مس، حدود ۵۵ تا ۶۰درصد حجمی شامل استراکچر و تجهیزات طرحهای خود را از داخل تامین میکند، هرچند بیش از ۴۰ درصد باقیمانده نیز در حقیقت همان فناوری بهکار گرفتهشده در سطح دنیاست. با وجود تمام این شرایط، شرکت مس در زمینه بومیسازی یک شرکت پیشرو بهشمار میرود.
عبدی با اشاره به تاریخچه بومیسازی در شرکت ملی مس عنوان کرد: این شرکت روند بومیسازی را از سال ۱۳۷۳ به صورت جدیتر شروع کرد که در آن زمان باوجود تحریمها، یک نهضت بومیسازی را راهاندازی و از سال ۱۳۷۳ تا ۱۳۸۴ حدود ۶۵۰۰ قطعه را داخلیسازی کرد، این در حالی است که بین سالهای ۱۳۸۴ تا پایان سال ۱۳۹۱بیش از ۸ هزار قطعه بومیسازی شد، یعنی در مدت مذکور سالانه حدود ۱۲۰۰ قطعه جدید داخلیسازی شده است. البته ممکن است این پرسش مطرح شود که چه اتفاقی در این بازه زمانی روی داده است؟ در این راستا باید عنوان کرد که از یکسو دانش فنی ما افزایش یافت و از سوی دیگر سازندگان ما توان خود را ارتقا داده و کیفیت محصولات خود را افزایش دادند. علاوه بر این، فرهنگ بومیسازی نیز در داخل رسوخ بیشتری پیدا کرد و باورها به بار نشست.
وی در ادامه افزود: البته باید یادآور شوم که بومیسازی فراتر از ساخت داخل است و شامل دانش فنی، طراحی، ساخت، ارتباطات علمی و ... میشود و به نوعی ساخت داخل بخشی از بومیسازی محسوب میشود. زمانی که یک فناوری داخلیسازی میشود، به نوعی بومیسازی آغاز شده است. در نهایت در بومیسازی، فرهنگسازی امر بسیار مهمی تلقی میشود، چراکه باید باور قطعی داشته باشیم که میتوانیم قطعهای را بسازیم و آن را جایگزین قطعه خارجی کنیم، حتی اگر قرار باشد نصف کالای خارجی، عمر داشته باشد، اما در ادامه فعالیتها، میتوان آن را ارتقای کیفی داد، چراکه ارتقای کیفی جایگاه بسیار مهمی در بومیسازی دارد.
عبدی با اشاره به این موضوع که برجام با تمام جوانب آن، دو پیامد دیگر نیز به همراه داشت، عنوان کرد: پس از برجام و با ورود اروپاییها، بومیسازی در کشور کمرنگتر شد که پیش از برجام بسیار پررنگ شده بود، بهگونهای که بین سالهای۱۳۸۴ تا۱۳۹۱ همانگونه که پیشتر عنوان شد، شرکت ملی مس در اوج بومیسازی قرار داشت و تعداد قطعاتی که برای نخستینبار آنها را بومیسازی کردیم بیش از ۸ هزار قطعه جدید بود که سالانه با این ۱۲۰۰ قطعه جدید بیش از ۳۵۰۰ قطعه و تجهیز بومیسازی شده به خطوط تولید ارسال میشد. از سال ۱۳۹۲ تاکنون فقط ۴ هزار قطعه جدید بومی شده و به آمار قبلی اضافه شده است. با توجه به گسترش این موضوع در پهنه کشور و نیز در سایر شرکتهای بزرگ بود که مقام معظم رهبری بحث داخلیسازی را مورد توجه جدی قرار دادند.
وی در ادامه به پیامد دوم اشاره کرد و گفت: پیامد دوم برجام آن بود که طی دو سال برقراری برجام به سرعت فناوری جدید برخی قطعات و تجهیزات را وارد کردیم یا با دیدن فناوری آنها با مهندسی معکوس داخلیسازی انجام دادیم که نتیجه بهکارگیری این قطعات، افزایش زمان بین دو تعمیر و کاهش قابل ملاحظه زمان تعمیر بود، در نتیجه عمر قطعه افزایش یافت و توقف دستگاهها بسیار کمتر شد که افزایش تولید را در پی داشت.
منبع: دنیای اقتصاد