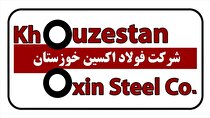
به گزارش میمتالز، هفدهمین همایش ملی و یازدهمین جشنواره نظام پیشنهادها با حضور شرکت فولاد هرمزگان برگزار شد و طرح «فرآوری گرم سرباره کورههای قوس الکتریکی» عنوان طرح برتر و واحد فولادسازی و ریختهگری مداوم این شرکت توانست واحد سازمانی برتر را در این جشنواره از آن خود کند.
برای این منظور گفتوگویی را با معاون بهرهبرداری، مدیر فولادسازی و ریختهگری مداوم، مدیر HSE، مدیر خدمات فنی و پشتیبانی، رئیس ذوب کوره و LF و رئیس نت فولادسازی و پیشنهاددهنده برتر شرکت فولاد هرمزگان جهت بررسی مزایای طرح یادشده انجام دادیم که در ادامه خواهید خواند:
سید اصغر مدنی، معاون بهرهبرداری: بدون شک به بار نشستن پروژه «فراوری گرم سرباره کورههای قوس الکتریکی» نمونهای موفق از پیادهسازی نظام پیشنهادها در سازمان است
یکی از اهدافی که سال گذشته در حوزه بهرهبرداری شرکت فولاد هرمزگان تعریف کردیم، افزایش کمیت و کیفیت محصولات بود. یکی از مشکلات افزایش کمیت، توقفات سرباره بود و این موضوع یکی از عوامل مهمی به شمار میرفت که شرکت را از تولید و رسیدن به اهداف مدنظر بازمیداشت. البته بیشتر فولادسازان دیگر هم با مشکل توقفات سرباره مواجهاند.
پیشنهاد «فراوری گرم سرباره کورههای قوس الکتریکی» حدود سه سال قبل از سوی یکی از کارشناسان کوره شرکت با هدف پیشگیری از توقفات جمعآوری سرباره ارائه و پس از طی فرایندی اجرا شد. خوشبختانه از این طریق توانستیم از توقفات ناخواسته پیشگیری کنیم؛ بهنحویکه یکی از عوامل کسب رکوردهای شهریور تا آذرماه نتیجه اجرا شدن این پیشنهاد بوده است.
اگرچه در آغاز، انتظار ثبت نتایج درخشانی از اجرای این پروژه نداشتیم، اما خوشبختانه مرحله اجرا با موفقیت طی شد و بهطور قطع با آیندهنگری به شرایط بهتری نیز خواهیم رسید. افزایش تولید یکی از اهداف استراتژیک سازمان محسوب میشود و مایه خرسندی است که با اعتماد به نظرات همکاران، در حال تحقق اهداف سازمان هستیم. بدون شک پروژه فوق نمونه موفق اثربخشی پیادهسازی نظام پیشنهادها در سازمان است.
سرعت تولید شرکت فولاد هرمزگان از سال ۱۳۹۴ بهطور قابلملاحظهای افزایش یافت و با این افزایش سرعت، از یک سو تناژ سرباره تولیدشده افزایش و از سوی دیگر، مدتزمان در اختیار تیم جمعآوری سرباره کاهش پیدا کرد. در نتیجه بهتدریج، توقفات ناشی از جمعآوری سرباره بیشتر شد و با معضلی به نام اسکول مواجه شدیم که در چاله سرباره به دلیل کمبود زمان و سایر مشکلات تشکیل میشد.
بخشهای مختلف تولید و حملونقل صنعتی فعالیتهای زیادی جهت کاهش این مشکلات بهویژه کاهش توقفات جمعآوری سرباره انجام دادند. اقداماتی مانند زیرسازی چاله سرباره، گذاشتن اسلب بتنی، استفاده از بتن نسوز در چاله سرباره و… صورت گرفت؛ بااینحال اقدامات یادشده تأثیر چندانی بر سرعت جمعآوری سرباره نگذاشت.
واحد حملونقل صنعتی نیز در جهت آمادهبهکاری مکانیسمها تلاشهای زیادی کرد؛ اما با توجه به روند روبهرشد سرعت تولید، معضل جمعآوری سرباره بیشازپیش آشکار میشد. بهطور مثال، در سال ۱۴۰۰، توقفات به ۵.۵ دقیقه به ازای هر ذوب افزایش پیدا کرد و همین امر به کاهش ۸۰ هزار تنی تولید در شرکت منجر شد. به این ترتیب بخش عمدهای از وقت تیم تولید بر رفع مشکل جمعآوری سرباره و چاله سرباره متمرکز شد تا اینکه یکی از مسوولین کوره ایدههایی در این زمینه مطرح کرد و با بررسی همهجانبه آن، دریافتیم که ایده موردنظر قابلیت اجرا دارد.
از طرفی یک تیم تحقیقاتی خارج از شرکت نیز در زمینه موضوع سرباره کار کرده بود؛ بنابراین تیمهای داخل و خارج شرکت طی جلسات متعدد و با ارائه طرحهای مختلف و اجرای موقت آنها، نهایتاً موفق به ارائه طرح نهایی شدند. طرحهای اولیه با ریسکهای زیادی همچون توقف و انفجار همراه بود، اما خوشبختانه با حمایتهایی که از تیم تحقیقاتی به عمل آمد، طرحهای مختلفی در طول سه سال و نیم ارائه شد. پس از ارائه هر طرح، نیاز داشتیم بستر و زیرساختهای اجرا و تست اولیه آنها را برای تیم پیشنهاددهنده بهصورت شبانهروزی فراهم کنیم. این عوامل باعث طولانی شدن زمان ارائه و تست طرحها شد.
خوشبختانه در ابتدای سال جاری با در نظر گرفتن طرحها و ابتکارات گوناگون پیشنهادشده، موفق شدیم مشکل چاله سرباره را بهصورت اساسی حل کنیم.
بهجرئت میتوان گفت طرح «فراوری گرم سرباره کورههای قوس الکتریکی» یکی از پیشنهادهای رتبه یک صنعت فولاد حتی در کل کشور است، زیرا در هیچیک از شرکتهای فولادی مشابه داخلی و حتی خارجی، طرح فراوری گرم سرباره آن هم بهصورت آنلاین اجرا نمیشود. طرح یادشده یکی از پیشنهادهای بدیع و خلاقانهای بود که در شرکت فولاد هرمزگان به اجرا درآمد. از دستاوردهای این پروژه میتوان به افزایش میزان تولید و بهتبع آن ثبت رکوردهای متعدد در چهار ماه متوالی از شهریور تا آذرماه اشاره کرد.
در پایان از مدیرعامل و معاونت بهرهبرداری به دلیل حمایتهای همهجانبه از این ایده خلاقانه، تشکر و قدردانی میکنیم. با رویکرد مدیریت مشارکتی که در فولاد هرمزگان وجود دارد، این انگیزه در میان کارکنان به وجود آمده است که در همه فعالیتها مشارکت کنند و مسائل و فرایندهای سازمان را در مسیر رو به بهبود و در جهت اهداف استراتژیک سازمانی پیش ببرند.
یکی از پرریسکترین فعالیتهای شرکت فولاد هرمزگان، تخلیه سرباره پشت کوره است. پیش از اجرای این طرح بهطور میانگین در هر ماه شاهد سه حریق در پشت کوره بودیم که این اتفاق به توقف تولید منجر میشد.
طرح «فراوری گرم سرباره کورههای قوس الکتریکی» علاوه بر مزایایی که برای افزایش راندمان فولادسازی و تولید داشت، به کاهش ریسک در فولادسازی، ارتقای ایمنی، کاهش حوادث و حریقهای ناشی از تخلیه سرباره و مکانیسمهای در حال فعالیت پشت کوره و در نتیجه کاهش خسارتهای ناخواسته نیز منجر شده است.
جمعآوری سرباره مشکلات بسیاری نظیر توقفات تولید، خرابی تجهیزات و ماشینآلات را به همراه داشت. چراکه سرباره در هنگام تخلیه و جمعآوری دمای بالایی دارد. حذف توقفات و خسارتهای ناشی از آن میتواند در راندمان و ایجاد ارزشافزوده اقتصادی بیشتر سازمان مؤثر باشد.
با توجه به اجرای طرح ارائهشده و با تلاش همکاران در مجموعه فولادسازی و خدمات فنی و پشتیبانی و تغییر شکل سرباره از حالت مذاب به نیمهجامد، مشکل جمعآوری سرباره تقریباً حل شد. با کاهش دمای سرباره، جمعآوری آنها بهمراتب راحتتر از قبل شد. همچنین توقفات تولید بهشدت کاهش یافت؛ بهگونهای که در یکی از ماهها، تنها حدود یک تا دو ساعت توقف تولید رخ داد. زمانهایی که بابت تخلیه و جمعآوری سرباره از بین میرفت، تماماً به تولید محصول اختصاص یافت و در ماههای اخیر رکوردهای کمنظیری در تعداد ذوب و حجم تختال تولید شده به ثبت رسید.
از ابتدای سال جاری تا کنون و بهویژه پس از اجرای این طرح با تأمین بهموقع ماشینآلات و تجهیزات موردنیاز، از فرایند و روند تولید پشتیبانی کردیم تا در پایان سال شاهد تحقق اهداف سازمان باشیم.
در سالهای گذشته معمولاً بهطور میانگین حدود ۱۰۰ هزار تن از تولید محصول را به دلیل جمعآوری سرباره در زیر کورهها از دست میدادیم. خوشبختانه به دلیل نوآوری و خلاقیتی که توسط کارشناسان در واحد ذوب شکل گرفت، موفق شدیم تناژ ازدسترفته به دلیل توقفات سرباره را جبران کنیم. همچنین توانستیم برخی از شاخصهای کلیدی مانند مصرف انرژی کورهها، میزان مصارف، افزایش سرعت تولید، کاهش زمان Power On را بهبود بخشیم.
با ارائه طرح «فراوری گرم سرباره کورههای قوس الکتریکی» توقفات تولید حذف شد و بهتبع آن ۹۰ درصد توقفات ناشی از شاتدان سالیانه تولید نیز انجام نخواهد شد. ظرفیت تولید شرکت فولاد هرمزگان مطابق با تکنولوژی خط ریختهگری طراحیشده یک میلیون و ۵۰۰ هزار تن در سال است که با اجرای این پروژه، ظرفیت تولید تا یک میلیون و ۷۰۰ هزار تن افزایش خواهد یافت.
پروژه مذکور برای نخستین بار در ایران انجام شد. پیش از اجرای پروژه، علاوه بر توقفات مکرر کورهها که ناشی از جمعآوری سرباره بود، از نظر آسیب دیدن بسیاری از تجهیزات، حجم تولید و ایمنی نیز دچار مشکلات جدی بودیم و، چون برنامهریزی فعالیتهای تعمیراتی در توقفات اضطراری ناشی از سرباره وجود نداشت، بهصورت کامل نمیتوانستیم از این توقفات بهره ببریم و آمادهبهکاری تجهیزات را افزایش دهیم. خوشبختانه با خلاقیتی که کارشناسان شرکت فولاد هرمزگان انجام دادند، تمامی مشکلات کاهش پیدا کرد.
با کاهش و حذف توقفات اضطراری و اجرای پروژه اصلاح و بهینهسازی دستورالعملهای تعمیراتی (PMO) و مدیریت توقفات برنامهریزیشده، حدود ۶ درصد بازدهی زمانی کورهها افزایش یافت. همچنین با افزایش آمادهبهکاری و افزایش تولید کورهها میزان تولید ماهانه شرکت نیز بهطور قابلتوجهی افزایش یافت. در حال حاضر پروژه PMO به پایان رسیده و توقفات برنامهریزی و اضطراری نیز کاهش یافتهاند.
از سال ۱۳۹۴ که افزایش تولید در دستور کار قرا گرفت، شرکت با مشکل جمعآوری سرباره کورههای قوس الکتریکی مواجه شد. توقف فعالیت کوره هنگام جمعآوری سرباره، روند تولید را نیز متوقف میکند. در تونل سرباره، پس از اینکه جمعآوری سرباره با مشکل مواجه میشد، ناچار به دپوی سرباره بودیم. این مشکل چند مسئله حاد به وجود میآورد. مثلاً هنگام خروج سرباره از کوره قوس، با توجه به اینکه باید با حالت رمپ خارج شود، گاهی مسیر خروج دچار مشکل میشود و به سمت دیوارهها حرکت میکند. با برخورد سرباره با دیواره، تخریب و سوراخ شدن دیواره اتفاق میافتد و با نفوذ آن به زیر زیرساختها، وارد آمدن آسیب به تجهیزات و سایر مشکلات ایمنی و اقتصادی ناشی از توقف تولید اجتنابناپذیر بود.
نکته قابلتوجه دیگر این است که جمعآوری سرباره کورهها سالانه حدود یک ماه از دست رفتن زمان تولید و تحمیل هزینههای دیگر به شرکت را در پی داشت. حل کامل این مشکل از ابتدای سال ۱۳۹۸ با ارائه این پیشنهاد از سوی اینجانب آغاز شد و در کارگروهی، پیشنهادهای واصله مطرح و تمام جنبههای آن مورد بررسی قرار میگرفت. تا اینکه اواخر سال ۱۳۹۸ پس از بررسی تمام جنبهها، طرحی تحت عنوان طرح فراوری گرم سرباره کورههای قوس الکتریکی بهصورت آنلاین (HPS) ارائه شد و مورد تأیید قرار گرفت و تست و اجرای آن از ابتدای سال ۱۳۹۹ آغاز گردید. در این کارگروه، تمامی مسائل فنی بهدقت بررسی میشد. ازآنجاکه طرح یادشده جدید بود، ریسک اجرای نسبتاً زیادی داشت. بااینحال مدیریت شرکت تمامی این ریسکها را پذیرفتند و تمامی مراحل طرح با موفقیت اجرا شد.
خوشبختانه پس از اجرای پروژه مذکور مشکلات قبل برطرف شد. هنوز ۱۰۰ درصد پروژه اجرا نشده است، اما با همین میزان پیشرفت نیز به رکوردها و افزایش تولید قابلتوجهی دست یافتهایم.
در رابطه با اجرای طرح مذکور تحقیقات گستردهای صورت گرفت و از سه سال و نیم گذشته تا کنون روی این پروژه کار کردیم و خوشبختانه به نتایج خوبی دست یافتیم. البته اجرای این پروژه که تاکنون ۵۰ درصد پیشرفت داشته ریسک نسبتاً زیادی داشت و با موانع متعددی همراه بود که این مشکلات تنها با حمایتهای مدیریت شرکت برطرف شده و نتایج بسیار خوبی برای فولاد هرمزگان به همراه داشته است. امیدواریم با ادامه این حمایتها بتوانیم پروژه را بهصورت کامل اجرا کنیم و نتایج درخشانتری برای شرکت به ارمغان آوریم.
منبع: خبرگزاری تسنیم