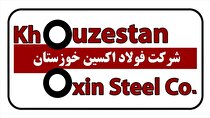
به گزارش میمتالز، در فرآیند تولید، توقفهای ناگهانی که از کار افتادن تجهیز را در پی دارد همواره باعث از دست رفتن سود ناشی از تولید میشود؛ به همین دلیل، یکی از اقداماتی که برای افزایش آمادهبهکاری واحدهای ریختهگری فولاد مبارکه انجام شده است، پروژه «کاهش توقفات اضطراری سیستم مکش بخار ماشینهای ریختهگری» است که در قالب اجرای پروژه بهینهسازی با موفقیت انجام شد.
پس از پایان موفقیتآمیز این پروژه که میتواند سالانه از توقفات ناخواسته و زیان اقتصادی زیادی جلوگیری کند، مسوول اجرای این پروژه و برخی از دیگر کارشناسان ناحیه فولادسازی و ریختهگری فولاد مبارکه به دیدگاههای خود در این زمینه پرداختند که ماحصل آن را در ادامه میخوانید.
علیرضا رستگار، تکنسین دفتر برنامهریزی و کنترل نت ریختهگری مداوم و مسوول پروژه اظهار داشت: توقف ناگهانی تولید به دلیل از کار افتادن تجهیز باعث از دست رفتن سود ناشی از تولید میشود. زمانی که یک تجهیز به مرحله خرابی و توقف میرسد، میزان و عمق آسیب و فرسودگی آن به مرحله شدیدتری رسیده است؛ بنابراین تعمیر آن نیز سختتر و پرهزینهتر است و مدتزمان بیشتری نیز طول میکشد. همچنین با توجه به این موضوع که عمدتاً این نوع خرابیها در زمانهای پیشبینینشده پیش میآیند، مدتزمانی که صرف شناسایی میزان خرابی و کشف عیب، تدارک نیروی متخصص جهت انجام تعمیر و تهیه قطعات موردنیاز آن میگردد نیز به مدتزمان توقف ناشی از آن خرابی اضافه خواهد شد. ازآنجاکه خط تولید در حالت عادی برای کار پیوسته در مدتزمان معینی برنامهریزی میگردد، توقف مکرر و راهاندازی مجدد خط باعث صرف زمان و بهتبع آن افزایش ضایعات و کاهش کیفی و کمی تولید میگردد.
بهمنظور کاهش توقفات تولید، مدیریت و کاهش هزینههای قطعات یدکی، کاهش هزینه و نفرساعت نیروی تعمیراتی و سهولت فعالیتهای تعمیراتی، پس از مطالعات و برگزاری آنالیزهای خرابی، با استفاده از توان و تخصص کارشناسان دفتر کنترل تعمیرات ناحیه و تعمیرات ریختهگری، پروژه تغییر طرح سیستم اگزوز فن ماشینهای ریختهگری در اولویت قرار داده شد و با همکاری تعمیرگاه مرکزی، عملیات ساخت انجام گردید و در توقف تعمیراتی ماشین ۴ با موفقیت نصب شد و مورد بهرهبرداری قرار گرفت.
در این راستا شایسته است از حمایتهای مدیریت ناحیه فولادسازی و ریختهگری مداوم، حُسن اعتماد رئیس و مجموعه پرتلاش تعمیرات ریختهگری، تولید، تعمیرگاه مرکزی و کلیه واحدهای درگیر تشکر و قدردانی کنم.
سید مجتبی غیوری، رئیس دفتر برنامهریزی و کنترل فرآیند نت واحد ریختهگری مداوم گفت: کاهش توقفات و افزایش آمادهبهکاری تجهیزات اولویت این واحد است. بسیاری از اقدامات شاخص این واحد طی سالهای گذشته مربوط به تعمیرات خطوط تولید بوده که برنامهریزی آن در دفتر برنامهریزی و کنترل فرآیند نت انجام میگردد. در همین راستا میتوان تعیین زمان شروع برگزاری جلسات تخصصی تعمیرات اساسی جهت انجام فعالیتهای تعمیراتی، تهیه فهرست قطعات یدکی موردنیاز در تعمیرات و ارسال به واحدهای تعمیراتی، تهیه دستورالعملهای فنی جهت اجرای فعالیتهای پیشبینیشده در تعمیرات و تحلیل خرابی RCA را از اقدامات مهم این واحد برشمرد. هدف از اجرای این رویه تحلیل علل ریشهای وقوع عیوب و حوادث و تعیین راهکارهایی جهت جلوگیری از تکرار آنها، کاهش شدت اثر و یا ردیابی زودهنگام عیوب است. با انجام و پایش وضعیت تجهیزات و با توجه به اهمیت تولید و بهمنظور کاهش توقف سیستم اگزوز فن ماشینهای ریختهگری، پروژه تغییر طرح از پیلوبلاک به بیرینگ هوزینگ مورد مطالعه قرار گرفت و پس از پیگیریها و انجام محاسبات به بهرهبرداری رسید و به این ترتیب به میزان قابلتوجهی، هزینه توقفات تولیدی، قطعات یدکی و نفرساعتهای تعمیراتی کاهش یافت.
رضا ترک علی عسکری، رئیس تعمیرات ریختهگری خاطرنشان کرد: امروزه با توجه به افزایش کارخانههای تولید فولاد در کشور و رقابت در بازارهای داخلی و خارجی، افزایش کمی و کیفی تولید با کمترین هزینه، افزایش بهرهوری و بهبود فرآیندهای تولیدی از اهمیت بسیار زیادی برخوردار است. در این راستا، شناخت دقیق مشکلات و چالشها و رفع آنها با کمترین هزینه در کوتاهترین زمان ممکن بسیار مهم و ضروری است و در اولویت کاری همکاران واحد ریختهگری مداوم قرار دارد. مشکلات مکرر در سیستم اگزوزفن ماشینهای ریختهگری به سبب طراحی اولیه و حساسیت بسیار زیاد تجهیزات و اِلمانها و همچنین تعمیر و نگهداری دشوار و گسترده تجهیز، سالیان سال از بزرگترین دغدغهها و چالشهای این واحد بوده و توقفات زیادی را نیز به همراه داشته است. بر همین اساس، تغییر در طراحی این سیستم با محوریت دفتر فنی تعمیرات در دستور کار قرار گرفت و پس از بررسیهای گسترده و تلاشهای جمعی همکاران و استفاده از ظرفیتهای داخلی شرکت، طراحی و ساخت سیستم جدید انجام شد و در شاتدان ماشین ۴ ریختهگری مورد بهرهبرداری قرار گرفت. از مزایای اجرای این پروژه تعمیر و نگهداری بسیار سادهتر، کاهش چشمگیر خرابیهای تجهیزاتی، کاهش مصرف قطعات و هزینههای جانبی و نفرساعت فعالیتهای تعمیراتی و نهایتاً کاهش توقفات و افزایش آمادهبهکاری ماشین اشاره کرد.
روحالله قیصریهای نجفآبادی، سرپرست برنامهریزی کارگاه مکانیک اظهار داشت: بهمنظور کاهش زمان توقفات غیرقابلپیشبینی، سیستم جدید اگزوزفن ماشینهای ریختهگری پس از طراحی توسط دفتر فنی تعمیرات ریختهگری و بررسیهای لازم در واحد تعمیرگاه مرکزی، با استفاده از تجربه و دانش داخلی شرکت ساخته و مونتاژ شد و در تعمیرات ماشین ۴ ریختهگری نصب گردید و مورد بهرهبرداری قرار گرفت.
با توجه به شناخت عوامل مؤثر در انجام پروژه فوق و حساسیتهای این تجهیز مهم و استراتژیک، ساخت کیسینگ در واحد اسکلت فلزی آغاز شد و پس از ساخت و دادهبرداریهای لازم، تجهیز در کارگاه مکانیک با حساسیت و دقت هرچهتمامتر مونتاژ گردید. با انجام این پروژه علاوه بر کاهش توقفات خط تولید، به میزان قابلتوجهی خرابی تجهیزات که عمدتاً استراتژیک نیز هستند کاهش مییابد و انجام این مهم در نهایت باعث افزایش بهرهوری و سودآوری سازمان خواهد شد.
محمد معظم، کارشناس قطعات یدکی واحد ریختهگری مداوم تشریح کرد: یکی از شاخصهای بررسی و کنترل وضعیت نگهداری و تعمیرات خط ازجمله پیشرفت، بهبود یا تضعیف روند آن بررسی و رصد مصرف قطعات یدکی در بازههای زمانی مختلف است؛ به شکلی که در صورت عدم نگهداری صحیح و افزایش ناگهانی مصرف قطعات و با اتمام موجودی انبار و عدم تأمین بهموقع، علاوه بر افزایش هزینه و کاهش سوددهی، خطر توقف نیز خط تولید را تهدید میکند.
پس از رصد و بررسیهای انجامشده در مصرف بیرینگ این تجهیز و مشاهده روند افزایشی آن و تحلیل ریشهای مساله، در قالب یافتن راهحلی برای رفع مساله و جلوگیری از تکرار آن، موضوع تغییر یاتاقانبندی و سیستم روانکاری مطرح شد و با مطالعه سیستمهای موجود و بررسی مزایا و معایب در کاربردهای مشابه، تغییر سیستم به بیرینگ هوزینگ (حمام روغن) انجام گردید. پس از انجام و بهرهبرداری این طرح مصرف بیرینگهای مورداستفاده از متوسط ۱۰ عدد به ۲ عدد در سال کاهش یافت و با استفاده از بیرینگهای سادهتر با یکپنجم قیمت بیرینگهای گرانقیمت قبلی، کاهش قابلملاحظه هزینه نگهداری و افزایش چشمگیر قابلیت اطمینان و آمادهبهکاری تجهیز حاصل گردید.
علاوه بر موارد ذکرشده، توان جذبی سیستم نیز کاهش داشته و همان کارایی قبلی با مصرف برق کمتر و جریان پایینتر (۱۷ درصد جریان کمتر از قبل) و در عین حال خرابیهای کمتر موتور حاصل شده است.
حسین شیرمحمدی، تکنسین تعمیرات ریختهگری مداوم گفت: توسعه کمی و کیفی محصولات و خدمات و همچنین بهکارگیری و توسعه توانمندیهای تحقیقاتی، طراحی، مهندسی و ساخت داخل از مهمترین هدفهای این پروژه بود که با تلاش و همت جمعی و اعتماد مدیریت به پتانسیلهای داخلی، این مهم به دست آمد و بعد از بهرهبرداری از این سیستم، برگ زرین دیگری به دستاوردهای تیم تعمیرات ریختهگری مداوم افزوده شد. ماحصل این پروژه کاهش چشمگیر توقفات و هزینه ناشی از تعمیرات تجهیز است.