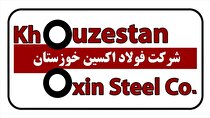
به گزارش میمتالز، فرآیند ریختهگری پیوسته رایجترین نحوه تولید فولاد است. در سالهای اخیر، بیش از ۹۶ درصد فولاد با فرآیند ریختهگری پیوسته تولید شده است. طیف وسیعی از محصولات مانند اسلبهای نازک، اسلبهای ضخیم یا بیلتها را میتوان با این فرآیند تولید کرد.
در یک نمای کلی شماتیک از فرآیند ریختهگری پیوسته T فلز مذاب از پاتیل به تاندیش منتقل شده و از آنجا به داخل قالب جریان مییابد. قالب با آب خنک گردیده و فلز مذاب در حین حرکت رو به پایین منجمد میشود. فرآیند انجماد از سطح بیرونی رشته شروع میشود. از طریق خنکسازی بیشتر در ناحیه خنککننده ثانویه، تمام فلز مذاب منجمد میشود، بهطوریکه در مشعل برشکاری کاملاً بهصورت جامد شده است. در طی این فرآیند بین قالب و مشعل برشکاری، عیوب سطحی ممکن است رخ دهد. این عیوب برای کیفیت محصول فولادی مضر هستند. اسلبهای بیکیفیت باید تحت عملیات پسفرآوری (برای مثال با سنگزنی یا رویهبرداری (اسکارفینگ) قرار گیرند. پسفرآوری هزینهها را بالا میبرد و وزن محصول نهایی را کاهش میدهد. اگر کیفیت یک اسلب خیلی پایین باشد، باید اسقاط (قراضه) شود.
برای پیشبینی و جلوگیری از بروز عیب، اپلیکیشن یا برنامه کاربردی “Cracks Preventer” توسعه داده شده است کهعیوب سطحی را قبل از وقوع پیشبینی میکند. از سیگنالهای قالب، منطقه خنککننده ثانویه و پایگاه داده L۲ (سطح ۲ اتوماسیون) برای پیشبینی عیوب استفاده میکند. با پیشنهاد اقدامات مقابلهای مناسب، میتوان از عیوب جلوگیری کرد. این کار، از اپراتورها در تولید محصولات باکیفیت بالا حمایت میکند و منتج به عملیات پسفرآوری کمتر و اسقاط کمتر اسلبها و در نهایت کاهش هزینههای تولید و انتشار کمتر CO ۲ میشود.
عیوب ریختهگری از قبیلترکهای طولیمیتوانند کیفیت اسلب را کاهش دهند یا به بیرونزدگی مذاب از رشته در حال ریختهگری (بریکوت) منجر شوند. برای شناسایی این عیوب ریختهگری در کارهای قبلی تلاش زیادی برای یافتنراهحلهاییصورت گرفته است که بتواند آن عیوب را شناسایی و از آنها جلوگیری کند. بخش زیر یک دید کلی در مورد آخرین وضعیت پیشرفت در تشخیص عیب ارائه میدهد.
در تحقیق Liu و همکاران، یک میدان (فیلد) دما بر اساس سیگنالهای دمای اندازهگیری شده از سیستم پایش دما تهیه شده است.
با کمک یک الگوریتم فرآوری تصویر کامپیوتری، تشکیل و تغییر مکان یک ترک طولی در ترموگراف ثبت میشود. به این منظور نواحی غیرعادی با استفاده از الگوریتم بخشبندی از نواحی عادی جدا میشوند. بر اساس مناطق بخشبندی شده، ویژگیهای ترک طولی استخراج شده وبا ویژگیهای یک فرآیند تولید ثابت (برای مثال، سرعت ریختهگری ثابت) وویژگیهای یک فرآیند تولید غیرثابت (مانند کاهش دادن سرعت ریختگی) ترکیب میشوند. نتیجه این است که ترکهای طولی الگوی خاص خود را دارند، که به این معنی است که این نوع عیب را میتوان با اطمینان نسبی تشخیص داد.
یکی دیگر از روشهای کلاسیک تشخیص ترکهای طولی، استفاده از تجزیه و تحلیل جز اصلی بر اساس تحقیق Lieftucht و همکاران است. در اینجا، دماهای اندازهگیری شده از سیستم پایش قالب که برای مثال توسط ترموکوپلها تعیین میشوند، مورد استفاده قرار میگیرند. فرض بر این است، ترکهای طولی با الگوهای دما بیان میشوند.
اولین مرحله فیلتر کردن سیگنالها است. در این زمینه، تنها حالتهای فرآیند ثابت انتخاب میشوند. این بدان معنی است که حالتهایی مانند شروع ریختهگری و پایان آن نادیده گرفته میشوند و در معرض تجزیه و تحلیل جز اصلی قرار نمیگیرند. این مرحله نتایج اندازهگیریاشتباهیرا که برای مثال توسط ترموکوپلهای معیوب ایجاد میشود، پاک میکند.
در مرحله دوم، تجزیه و تحلیل جز اصلی بر روی دادههای آموزشی اعمال میشود که شامل سیگنالهای ترموکوپل نرمال شده است. نتیجه این تجزیه و تحلیل جز اصلی بردارهای ویژه غیرهمبسته است که واریانس در مجموعه دادههای آموزشی (دادههای آموزشی برای آموزش الگوریتم یادگیری ماشین استفاده میشود که باید نشاندهنده دادههایی باشد که الگوریتم در دنیای واقعی با آن مواجه میشود.) را نشان میدهد. با اعمال تجزیه و تحلیل جز اصلی برای دادههای جدید، مقایسه واریانسها امکانپذیر است. این مقایسه پیشبینیهایی را امکانپذیر میکند که آیا یک ترک طولی رخ میدهد یا خیر. در مرحله سوم و چهارم، از تجزیه و تحلیل گرادیاندماهای ترموکوپل برای تعیین نوع ناهنجاری و محل آن استفاده میشود.