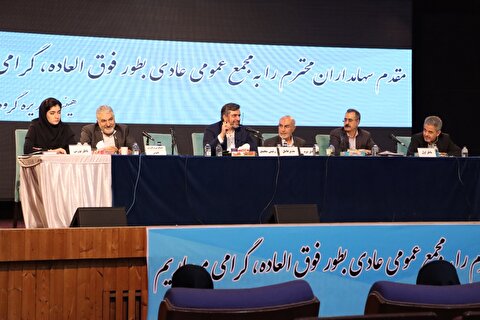
به گزارش می متالز، اکنون نوبت به اولین فرآیندهای مهمی که برای خارج کردن کربن اضافی از چدن به کار رفتند، رسیده است. از همین رو، در این گزارش، به بررسی روند تکامل روش بسمر پرداخته شده است.
در اواخر قرن 18 میلادی، در سال 1784، فردی به نام هنری کورت (Henry Cort) روشی را پیشنهاد داد که طی آن، چدن خام ریختهگری شده به آهن کارشده تبدیل میشد. در این روش که به پارویی (puddling) معروف است، از یک کوره انعکاسی برای ذوب آهن استفاده میشد. به این ترتیب که سوخت و سنگ آهن در تماس با یکدیگر قرار نداشتند و ناخالصیهای موجود در زغالسنگ، وارد آهن مذاب نمیشود. در این روش، اکسیژن از یک مجرا، وارد مذاب شده و پارو با هم زدن مذاب، اکسیژن را به داخل مذاب هدایت کرده و سبب سوختن و خروج آهسته کربن از ساختار چدن خام میشود. با کاهش کربن موجود در مذاب، نقطه ذوب افزایش پیدا میکند و به تدریج تکههای آهن منجمد شده در کوره جمع میشود. این تکهها پس از جمعآوری از کوره، پیش از نورد شدن، توسط چکش محکمی آهنگری میشوند تا استحکام مناسبی پیدا کنند. این روش، طرفداران بسیاری در انگلستان پیدا کرد، به طوری که تا سال 1860، حدود 3 هزار کوره پارویی در انگلستان مشغول به کار بودند.
رشد صنعت راهآهن در قرن 19 میلادی در اروپا و آمریکا، تقاضای تولید فولاد را بالا برد. رشد نیاز به فولاد، سبب شد که این صنعت که هنوز با مشکلات فرآیندهای کمبازده دست به گریبان بود، برای تولید بیشتر و ارزانتر، تحت فشار قرار گیرد. در آن زمان فولاد، هنوز خود را به عنوان فلز ساختمانی ثابت نکرده بود و تولید آن، هزینهبر و طولانی بود. این روند ادامه داشت تا اینکه در سال 1856 هنری بسمر، با وارد کردن اکسیژن به داخل مذاب چدن به روشی با بازده بالاتر دست یافت تا مقدار کربن آن را کاهش دهد و فولاد، کارپذیرتر شود. بسمر در طراحی روش خود، یک ظرف گلابیمانند به نام کنورتر در نظر گرفت که در داخل آن، آهن مذاب در حالی که اکسیژن به داخل آن دمیده میشود، تحت حرارت قرار میگیرد. با عبور اکسیژن از داخل فلز مذاب، کربن موجود در آهن اکسید شده و به صورت گاز دیاکسید کربن از مذاب خارج میشود. سرعت این فرآیند بالا و هزینه انجام آن، پایین بود به طوری که ظرف چند دقیقه، کربن و سیلیسیوم موجود در مذاب را خارج میکرد. مشکل این فرآیند، بیش از اندازه خارج کردن کربن و وجود اکسیژن باقیمانده در محصول نهایی بود. بههمین دلیل، بسمر مجبور شد تا راهی برای افزایش کربن مذاب خود و خارج کردن اکسیژن از آن بیابد.
در همین زمان، یک متالورژ بریتانیایی به نام رابرت موشت (Robert Mushet) ترکیبی از فلز منگنز، آهن و کربن را که با نام اشپیگل (speigeleisen) شناخته میشد، به کار برد. منگنز بهعنوان عنصری جهت خارج کردن اکسیژن از ساختار آهن مذاب بهکار رفت و کربن نیز برای جبران مشکل فرآیند بسمر، اضافه میشد. پس از معرفی شدن این روش، بسمر آن را به کنورتر خود اضافه کرد و به این ترتیب، کارایی روش بسمر بهشدت افزایش پیدا کرد و استفاده از آن رونق یافت. روند تغییر سهم فولادسازی این روش در گذر زمان، در نمودار 1 دیده میشود.
همانطور که در نمودار دیده میشود، استفاده از روش بسمر، طی سالهای 1881 تا 1900 به اوج خود رسید. با این حال، هنوز یک مشکل باقی مانده بود: بسمر نتوانست راهی برای خارج کردن ناخالصی فسفر از فولاد پیدا کند. بههمین دلیل، محصولات تولید شده از فولاد بسمر، شکننده بودند. از همین رو، استفاده از سنگ آهن تمامی معادن امکانپذیر نبود و تنها معادن سوئیس و ولز که فاقد فسفر بودند، برای تولید فولاد بهکار میرفتند.
در سال 1876، توماس برای حل مشکل فسفر، چارهای اندیشید. وی با افزودن یک محلول بازی (که حاوی سنگ آهک بود) به فرآیند بسمر، توانست فسفر را از چدن خام خارج کرده و وارد سرباره کند. معنای این نوآوری، این بود که بالاخره سنگ آهن تمامی معادن در همه جای دنیا، قابلیت تبدیل شدن به فولاد را داشتند. از همین رو، هزینه تولید فولاد بهشدت کاهش یافت و به تبع آن قیمت ریل راهآهن در بازه زمانی 1867 تا 1884 بیش از 80 درصد افت کرد.