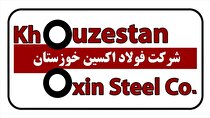
به گزارش میمتالز، عرصه صنعت و بهویژه فولادسازی، مانند تمام عرصههای دیگر کشور، بعد از انقلاب اسلامی متحول شد. قبل از انقلاب، تقریبا تمام تجهیزات خارجی بود. بعد از انقلاب هم تا حدی این واردات انجام میشد، ولی با بیشتر شدن تحریمها، مشکل فولادمردانِ فولادسازیها دوتا شد: یکی تأمین ماشینآلات و دیگری تأمین قطعات و تجهیزات. به مرور تأمین قطعات موردنیاز دستگاههای خارجی یکی از بزرگترین محدودیتهای ماشینآلات صنعت فولاد شد. علاوه بر این، توان تولید قطعات در داخل با تکیه به دانش و توان جوانان در داخل کشور، همواره برای مدیران کشور مطرح بوده است. از طرف دیگر هزینههای بالای قطعات و تجهیزات و در نتیجه نداشتن صرفه اقتصادی برای وارد کردن این قطعات باعث شد مدیران فولاد مبارکه، بهعنوان یکی از بزرگترین صنایع کشور، برنامههای جدیدی در دستور کار خود قرار دهند.
شرکت فولاد مبارکه یکی از پیشگامان صنعت کشور در بومیسازی قطعات و تجهیزات صنعت فولاد است. با توجه به وسعت و تنوع فعالیتهای این شرکت، بومیسازی در ابتدا کاری «نشد» به نظر میرسید، اما مهندسان و متخصصان فولاد مبارکه در عرصههای مختلف «نشدها» را به «شد» تبدیل کردند.
در شرکتی بزرگ مانند شرکت فولاد مبارکه، بهدلیل تنوع مأموریتها، هر کاری باید با ساختار خاص خود انجام شود. همین ساختارسازیهاست که شرکت فولاد مبارکه را در زمره بهترین شرکتهای فولادسازی دنیا قرار داده است. برای بومیسازی نیز ساختارهایی در نواحی تولیدی مختلف فولاد مبارکه تشکیل شد. ساختار بومیسازی در مدیریت دفتر فنی نگهداری و تعمیرات از چهار قسمت تشکیل شده است: برنامهریزی، مهندسی معکوس، مهندسی مجدد و کنترل کیفیت. در قسمت برنامهریزی پروژههای مختلفی تعیین میشود و برای هر پروژه، متخصصین مربوطه کارهای لازم را برای انجام فرایند برنامهریزی میکنند. در حقیقت اولین مرحله فاز شناسایی، آمادهسازی و اولویتبندی اقلام است. فاز بعدی فاز مهندسی یعنی تهیه و تکمیل مدارک فنی است. در این فاز تمام اطلاعات مربوط به قطعه یا قطعات جمعآوری میشود. مدارک فنی فقط نقشههای ساخت نیستند؛ بنابراین در این مرحله، روش یا روشهای تولید، اطلاعات مواد اولیه، روش بازرسی کنترل کیفیت و... به همراه کلیه استانداردهای موردنیاز فرایند برای ساخت و بازرسی قطعات و تجهیزات جمعآوری میشود. این کار باعث میشود علاوهبر تهیه مدارک فنی بهعنوان مرجع تأمین، ساخت یا تعمیرات قطعه یا تجهیزات، هزینهها برای شرکت فولاد مبارکه کاهش یابد و موجودی انبار برای قطعات ایجاد گردد تا تولید متوقف نشود. فاز بعد فاز شناسایی و ارزیابی فنی سازندگان جهت بومیسازی قلم موردنظر است تا بهترینهای هر حوزه برای تولید قطعه بومیسازیشده انتخاب شوند.
نکته قابلتوجه دیگر این است هر کاری باید از نظر اقتصادی سنجیده شود. برای همین فاز بعد که فاز اختصاص بودجه و ایجاد استعلام و سفارش است، فرایند بومیسازی را تا مرحله سفارش پیش میبرد. با تولید قطعه، کار هنوز تمام نشده است. فولادمردان متخصص در طراحی و تولید قطعات، کنترل کیفیت را برای رسیدن به بهترین نتیجه انجام میدهند. در اینجا برای اینکه کارهای گذشته بازنگری شود، واحدی به نام واحد مهندسی مجدد در ساختار گنجانده شده و هدف آن اصلاح فرایند یا بهروزرسانی و در نتیجه افزایش کارایی مجموعه است.
کسانی که با صنعت بهویژه صنایع بزرگ و حساسی مانند فولاد آشنا هستند، میدانند که این صنعت و قطعات و تجهیزات آن پیچیدگیهای خاص خود را دارد و فرایند تولید یک قطعه بسیار زمانبر و هزینهبر است، ولی هیچکدام از این اینها باعث توقف چرخ تولید فولاد مبارکه نشده است.
نزدیک به ۱۰ سال است که واحد بومیسازی شرکت فولاد مبارکه یکسره برای رسیدن به نتیجه تلاش میکند. این یک ادعا نیست و آمارها این موضوع را بهخوبی نشان میدهد. در این سالها مهندسین بومیسازی در فولاد مبارکه توانستهاند بیش از ۱۴۴ هزار قطعه و تجهیز را بومیسازی و آمادۀ بهرهبرداری کنند. این موضوع نشان میدهد مهندسین مکانیک، مواد، شیمی، پلیمر، کامپیوتر و... از دانش بالایی برخوردارند؛ چراکه قطعات و تجهیزات روز دنیا را تجزیهوتحلیل و آنها را با تکنولوژی روز تولید میکنند.
در نتیجه این تلاشها طبق آمارهای موجود، تعداد تجهیزات تهیهشده در شرکت بیش از ۹۰ درصد رشد داشته و در نتیجه آن، از خروج ارز از کشور نیز جلوگیری شده است. فقط در سال گذشته ۱۵۸۹ قطعه برای اولین بار در فولاد مبارکه ساخته شده و ۲ هزار و ۶۱۶ میلیارد تومان صرفهجویی مالی برای کشور به همراه داشته است. گفتنی است این قطعات با نمونههای خارجی قطعا قابلرقابت است.
فولاد مبارکه بهعنوان پیشگام و پیشرو عرصه بومیسازی قطعات صنعتی میتواند به الگویی برای بومیسازی ماشینآلات، قطعات و تجهیزات تبدیل شود. الگویی که میتوانیم با در نظر گرفتن آن، موانع موجود را از بین ببریم و در آیندهای نزدیک شاهد شکوفایی صنعت کشور و محقق شدن جهش تولید باشیم.