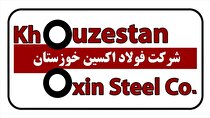
به گزارش می متالز، با توجه به پیشبینی افزایش متوالی قیمت مس طی چند سال آینده بررسی اقتصادی و مطالعه دقیق این روش، شاید در کشورهایی مثل شیلی و ایالات متحده آمریکا که صادرات کنسانتره را به تولید کاتد مس ترجیح دادهاند، تغییری در سیاستهای آنها ایجاد کند.
روشهای متعددی برای بازیابی طلا و نقره از پسماند واحد تولید مس وجود دارد؛ 1) سیانیداسیون مستقیم، 2) حرارتدهی و سیانیداسیون، 3) لیچینگ اکسایشی کامل و سیانیداسیون و 4) لیچینگ گوگرد، لیچینگ اکسایشی کامل و سیانیداسیون.
در روش سیانیداسیون مستقیم، پسماند واحد تولید مس تحت فرایند لیچینگ سیانیدی قرار میگیرد. این روش معایب بزرگی چون مصرف بسیار زیاد سیانید و بازیابی کم طلا را بههمراه دارد.
روش حرارتدهی و سیانیداسیون، برای حذف گوگرد عنصری و سولفیدهای باقیمانده، پسماند واحد تولید مس را ابتدا حرارت داده، سپس تحت فرآیند لیچینگ با سیانید قرار میدهند. معایب این روش نیازمندی به تمیزکردن گاز خروجی (خطر از دست رفتن طلا و نقره)، حجم بالای اسید تولیدی (حدودا برابر با کارخانه اسید واحد ذوب)، مشکلات زیستمحیطی (انتشار گاز) و هزینههای سرمایهای بالا است.
روش سوم، پسماند واحد تولید مس را تحت حرارت و فشار بالا فرآوری میکند تا گوگرد عنصری و سولفیدهای باقیمانده آن اکسید شوند. محصول این مرحله لیچینگ اکسایشی، با سیانید نیز شسته میشود. این روش نیز معایبی چون حجم بالای اسید رقیق مرحله لیچینگ اکسایشی، مصرف بسیار زیاد اکسیژن، نیازمندی به اتوکلاو بزرگ (هزینههای بالای سرمایهای و اجرایی) و بازیابی سخت نقره را در بردارد.
در روش چهارم، پسماند واحد تولید مس ابتدا با حلالهای آلی شسته میشود تا گوگرد عنصری آن از بین برود. گوگرد موجود در حلال خروجی این روش طی فرآیند تبخیر بازیابی شده و حلال مجددا به چرخه برمیگردد. سپس محصول مرحله اول طی لیچینگ اکسایش، گوگرد و مس باقیمانده خود را از دست داده و در نهایت با سیانید شسته میشود. معایب این روش شامل مشکلات فیلتراسیون پسماند لیچینگ گوگردی، هزینه زیاد حلالهای آلی، مشکلات بازیابی حلال و همچنین هزینههای سرمایهای و اجرایی زیاد است.
در مقایسه با روشهای فوق، فرایند بازیابی طلا سی.ای.اس.ال (CESL Gold Process) نرخ بازیابی قابل ملاحظه و معایب کمتری دارد. این روش پنج مرحله اصلی دارد که شامل 1) سیانیداسیون تحت فشار پسماند با اکسیژن سپس فیلتراسیون، 2) جذب کربن و بازیابی آن، 3) حذف مس با اسیدی کردن و رسوب CuSCN و سپس فیلتراسیون، 4) تبخیر و جذب HCN برای تشکیل مجدد NaCN برای بازیافت، و 5) تخریب سیانید با روشهای متداول میشود.
استفاده از فرایند تولید مس سی.ای.اس.ال (CESL Copper Process) در کنار واحد بازیابی طلا، نرخهای بازیابی خوبی به همراه دارد؛ مس، 96.7 درصد، طلا 92 درصد و نقره 87 درصد. از نقطه نظر اقتصادی، واحدی با تکنولوژی تولید مس و طلا سی.ای.اس.ال (CESL Copper & Gold Process) و تولید سالانه 554 هزار تن کنسانتره، 155 هزار تن مس، 178 هزار اونس طلا و یک میلیون و 158 هزار اونس نقره در نظر گرفته شده که هزینههای ذوب، پالایش، باربری، پالایش طلا و همچنین نقره جهت فروش کنسانتره (سناریوی اول) و پریمیوم و هزینههای باربری و بازاریابی جهت پالایش به روش سی.ای.اس.ال و فروش کاتد مس (سناریوی دوم) در برآورد هزینههای اجرایی این واحد لحاظ شده است. هزینههای اجرایی واحد سی.ای.اس.ال در نمودار 1 آورده شده است.
نمودار 2، مقایسهای میان هزینههای تحقق 2 سناریوی فروش کنسانتره و پالایش آن به روش سی.ای.اس.ال را نشان میدهد. نمودار 3 نیز، درآمد خالص این 2 سناریو را با هم مقایسه میکند. افزایش گردش وجوه نقدی در سناریوی دوم (بهرهگیری از پالایشگاه سی.ای.اس.ال) نسبت به سناریوی اول (فروش کنسانتره) ناشی از کاهش سالانه 64 میلیون دلار هزینه تحقق سناریو و افزایش سالانه 97 میلیون دلار درآمد خالص آن است.
با این تفاسیر، استفاده از این روش برای پالایش مس و همچنین بازیابی قابل توجه طلا و نقره به افزایش درآمدهای پروژههای آتی یا تغییر سیاست کشورهایی از قبیل شیلی و ایالات متحده آمریکا که سعی در فروش کنسانتره دارند، کمک شایانی خواهد کرد.