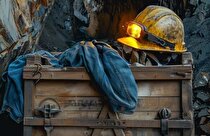
به گزارش می متالز، تابآوری هر صنعتی در گرو بالا رفتن توان آن دربرابر چالشهای درونی و بیرونی است. چالشهایی نظیر تحریم که ممکن است تأمین تجهیزات موردنیاز صنعت را دچار وقفه کند یا حوادث که خط تولید را متوقف میکند. شرکت ملی صنایع مس ایران با کلیدواژه «مقاومسازی تولید» در سالهای اخیر قدم در راه تابآور و مقاوم کردن خط تولید خود برداشته است و بومیسازی قطعات یکی از مهمترین تلاشها در این راستا بوده.
در کارگاه الکترومکانیک شهربابک در چند سال گذشته چندین قطعه بومی شدهاند که نظیرشان پیش از این در کشور وجود نداشته. ساخت بوبین ترمز مگنت جرثقیلهای 75تنی ذوب خاتونآباد، ساخت دستگاه تراش اسلیپ رینگ الکتروموتورها روتور سیمپیچی شده و ساخت دستگاه cut off سیمپیچی الکتروموتور سه اتفاق مهم در کارگاه الکترومکانیک هستند. «مهدی محمودیمیمند»، سرپرست کارگاه الکترومکانیک در گفتوگو با «تابآوری» درباره این اقدامات گفته است. او میگوید بومیسازی قطعات در کارگاه الکترومکانیک بیش از توان مهندسی نیازمند روحیه و اعتمادبهنفسی بود که همه اعضای این کارگاه، آن را با در کنار هم بودن به دست آوردند.
ما چهار سال است کارگاه الکترومکانیک شهربابک را راهاندازی کردهایم. راهاندازی یک کارگاه سیمپیچی، کار سنگینی است، اما با همت پرسنل، بهراحتی و با افق روشن جلو رفتیم و خوشبختانه به افقی که تعیین کرده بودیم، رسیدیم و حتی فراتر هم رفتهایم. بهرغم اینکه حدود چهار سال از راهاندازی کارگاه الکترومکانیک شهربابک میگذرد، اما بهدلیل برخی مشکلات، هنوز نتوانستهایم بیش از 70 درصد از تجهیزات لازم برای این کارگاه را بگیریم. البته این اتفاق یک مزیت داشت و موجب شد خودمان به سمت ساخت تجهیزات برویم. ازجمله تجهیزاتی که ساختیم، کورۀ خشککن الکتروموتور بود. در ادامه، یک پولیکش طراحی کردیم و به سمت ساخت هم پیش رفت، اما با رسیدن پولیکش جدید کار متوقف شد؛ همچنین یک بوبین خیلی حساس ساختیم که بهرغم مکانیزم سادهای که دارد، اما کارگاههای دیگر ازجمله کارگاه الکترومکانیک سرچشمه و کارگاههای خصوصی بیرون از شرکت، با توجه به عملکرد خاص کرینهای واحد ذوب خاتونآباد قادر به ساخت آن نبودند.
علت اینکه به سمت ساخت کوره رفتیم، این بود که بدون کوره، تنها میتوانستیم یکسری تعمیرات سطحی روی الکتروموتور انجام دهیم، اما اگر تعمیر از حدی بیشتر میشد و بهطور مثال سیمپیچ الکتروموتور دچار مشکل میشد، باید موتور را به سرچشمه منتقل میکردیم تا در کورههای سرچشمه فرایند انجام شود؛ بنابراین، با ساخت کوره، دیگر نیاز به انتقال موتور به سرچشمه نیست. درواقع زمانی را که برای انتقال از دست میدادیم، کاهش یافت؛ ضمن اینکه کورهای که حداقل 180 میلیون تومان قیمت داشت، با استفاده از مواد مستعمل و دورریختهشده، با هزینهکرد حدود سه میلیون تومان ساختیم که این رقم هم مربوط به خرید مشعل کوره بود.
بله، برای ساخت کوره، پرسنل کارگاه حدود یک هفته در قطعات ضایعاتی دپوی شرکت جستجو و مواد مورد نیاز را پیدا کردند، سپس کوره ساخته شد و اکنون دیگر به هیچ کارگاه دیگری نیاز نداریم و بهطور مثال سیمپیچی الکتروموتور را که سریعترین کار بود، اما بهدلیل انتقال به سرچشمه یا کارگاههای خصوصی شهر، دو روز طول میکشید، الان بهسرعت در کارگاه انجام میدهیم و در کنار آن به کارهای دیگر هم میرسیم.
پیش از آن نیز یک مگنت ترمز کرین ساختیم. کرینهای 75 تن، پاتیلهای بزرگی را که وظیفه جابجایی مذاب را دارند، نزدیک کوره میگذارند و مذاب را با حساسیت بالایی خالی میکند تا مواد مذاب به اجزای دیگر آسیب نزند. کرینها، دارای یک الکتروموتور قلاب اصلی هستند که بهدلیل حساسیت بالا، با دو ترمز مکانیکی و الکترونیکی کنترل می شوند که ترمز الکترونیکی بهوسیلۀ یک مگنت، حالت آهنربا پیدا میکند و بهصورت سیستم ترمز عمل میکند. در حین انجام کار، مگنت ترمز به دلیل تکانهای شدید دچار آسیبدیدگی میشد و تحویل سفارش مگنت جدید هم حدود ششماه طول میکشید تا از کشور چین وارد شود و چون تحریم بودیم، زمان بیشتر هم میشد. برای کارگاههای اطرف هم صرفۀ اقتصادی نداشت که این مگنت را بسازند. البته یک مگنت هم ساخته شد که رضایت کامل از آن نداشتیم؛ بنابراین، پرسنل ما با استفاده از مواد بازیافتی، مهندسی معکوس انجام دادند و مگنت را ساختند.
در ادامه، برای بار دوم که واحد بالابرها سفارش مگنت داد، پرسنل جنس سیم و لاک را بالاتر بردند و با یک میلیون تومان هزینۀ بیشتر، مگنتی ساخته شد که بسیار بهتر از نمونۀ اصلی کار میکند و دیگر سفارشها از کشور چین حذف شد. قیمت این مگنت خیلی زیاد نیست و شاید خرید آن در طول سال حدود 20 تا 30 میلیون تومان هزینه داشت، اما در کارگاه با یک میلیون تومان کار انجام شد؛ ضمن اینکه مهم، مدتزمانی بود که طول میکشید تا تجهیزات میرسید و تولید متوقف میماند. اما حالا دیگر همه اینها حذف شده است و دیگر دست نیاز به سمت کشورهای غیر دراز نمیشود.
بله، مهمترین دلیلی که پرسنل به این سمت رفتند، این بود که میخواستند یک حرکت انجام دهند. خوشبختانه از نیروهایی که جذب کردهایم؛ یک نفر حدود 15 سال سابقۀ سیمپیچی در کارگاههای خصوصی دارد و دو نفر دیگر هم سابقۀ سیمپیچی برای خودروهای سنگین صنعتی دارند. البته شاید سطح سواد آنها در حد دیپلم یا فوقدیپلم است و یکی از پرسنل به تازگی لیسانس گرفته، اما همت، ذهن باز و همکاری و وفاق با یکدیگر موجب شد به این موفقیتها دست پیدا کنیم.
کارگاه شهربابک تازه تأسیس شده و مشابه کارگاه سرچشمه که حدود 40 سال سابقۀ فعالیت دارد، نیست، اما خوشبختانه تاکنون کارهای بزرگی انجام دادهایم؛ ازجمله کار دوم، تراش اسلیپ موتور نوار 12 که این کار در ابتدا غیرممکن به نظر میرسید و کارشناسان کارگاه سرچشمه با توجه به قیمت بالای این الکتروموتور (500 میلیارد ریال) و همچنین نوع تعمیر مورد نیاز که کاملاً تخصصی و بسیار حساس بود، تأکید در ارسال آن به کارگاههای بزرگ تعمیراتی داشتند که با توجه به گلوگاهی بودن این قطعه در صورت ارسال آن به کارگاههای تهران یا مشهد حداقل 10 روز خط تولید مجتمع میدوک متوقف میشد. از طرفی شرکتهای خصوصی هم با توجه به محدود بودن اندازه و سایز دستگاه پرتابل، فقط قادر به تعمیر آن در محل شرکت بودند.
اما «حسین شریفی» یکی از کارشناسان متخصص این واحد آمادگی خود را برای ساخت دستگاه ساباسلیپ اعلام کرد و با تشکیل کارگروهی از پرسنل این و احد و کارگاه ساخت به سرپرستی آقای مهندس «سعید محمودی» و همکار زحمتکش ایشان جناب آقای «قاسمپور» که به حق استاد تمام در زمینه تراشکاری هستند، ظرف مدت یک هفته کار ساخت دستگاهی که برای اولین بار در ایران تهیه شده از ابتدا، طراحی، ساخت و تست به اتمام رسید. پس از نصب در محل هم با وجود موانع و با توجه به ریسک و قیمت الکتروموتور ظرف مدت هفت ساعت الکتروموتور مذکور رفع عیب شد و کاری یکتا در صنعت کشور رقم خورد که به زعم بسیاری از کارشناسان فن این طرح حتی در سطح خاورمیانه یکتاست.
انجام این کار چیزی سوای از سواد مهندسی میخواست، یعنی هم تجربه و هم یک دلِ پاک میخواست. با اتصال چند قطعه آهنی و با یک کار مهندسی سهلممتنع، دستگاه را طراحی و خوشبختانه نتیجه کار شگفت انگیز بود. جالب است وقتی استعلام این موتور را که گرفتهاند، گفته شد این موتور 650 میلیون تومان قیمت دارد؛ ضمن اینکه باید از خط تولید خارج میشد و چون یدک آن را نداشتند؛ خط تولید متوقف میشد.
خوشبختانه تاکنون هر سال یک کار جدید انجام دادهایم و با پرسنل عهد بستهایم علاوه بر کارهای روزمره، کارهای بزرگ هم انجام دهیم؛ چراکه کار روزمره، آدم را خسته میکند؛ بنابراین، علاقه داریم کارهای جدید را تجربه کنیم.
درنهایت به سراغ دستگاه سوم رفتیم. کار سرزنی الکتروموتور خیلی وقتگیر بود، تعداد نیروها هم کم بود؛ بنابراین، خیلی به موتور آسیب میزد و موجب میشد هر موتور بعد از سیمپیچی و تعمیر، اُفت کیفیت پیدا کند و کارکرد لازم را نداشته باشد.
با جستوجو در اینترنت بهدنبال ترجمۀ انگلیسی «سرزنی» گشتیم که متوجه شدم ترجمۀ آن «کاتآف» است. از طریق ایمیل با شرکتی تماس برقرار کردم و درخواست کردم نقشههای کاتآف را برای ما بفرستند که نقشهها به صورت تخصصی ارسال نشد.
پیش از این اقدام، وقتی دستگاهها را دیدیم، اعلام نیاز و حتی مرحلۀ تبدیل به درخواست نیز در مرحله تایید بود. خرید این دستگاهها در مرحلۀ امضای مدیر محترم بود که یکی از پرسنل گفت من این دستگاه را میسازم و با هماهنگی تیم قبلی (دستگاه تراش اسلیپ رینگ) یک هفته وقت خواست. نقشهها را به پرسنل تحویل دادم و بعد از یک هفته دیدم کار به خوبی در حال انجام است و در عین حال که کار خیلی زمانبر بود، و نقشهها هم کامل نبودند با تغییراتی کانل و اساسی دستگاه طی دو ماه طراحی و ساخته شد و اکنون خیلی بهتر از دستگاههای ساخت خارج کار میکند. در حالت معمولی و سنتی کار سرزنی الکتروموتور حدود دو روز طول میکشد، اما با دستگاهی که ما ساختیم، حدود 30 ثانیه طول میکشد. دستگاهی که در این کارگاه ساختیم، سهکاره است و این درحالی است که دستگاههای موجود در کشور، تککاره هستند؛ ضمن اینکه این دستگاه با مواد دورریختنی ساخته شده است. این دستگاه با دقت یک میلیمتر اقدام به سرزنی الکتروموتور میکند.
بله، روحیه و جو مثبتی که در کارگاه ایجاد شده است. در این کارگاه همه مثل یک خانواده در کنار همدیگر فعالیت میکنیم؛ ضمن اینکه دانش ما هم بسیار بالاست، پرسنل کارگاه آدمهای باهوشی هستند و خود من هم با جستوجو در اینترنت، مواردی که نیاز است را پیدا میکنم و پس از تحویل به پرسنل، با تمام قدرت کار را پیش میبریم. درواقع ما همه چیز برای موفقیتمان داریم.
ابتدا ناراحت بودیم که نمیتوانیم کارها را بهخوبی پیش ببریم؛ چراکه خط تولید معطل میماند. میدانستیم اگر سفارش فلان قطعه را به بازرگانی تحویل دهیم، تا خریداری و ارسال شود، حداقل یک سال طول میکشد؛ بنابراین، خودمان به سمت ساخت قطعات رفتیم تا در حداقل زمان ساخته شود. به مرور زمان اعتمادبهنفس ما افزایش یافت. شاید دفعۀ دوم که میخواستیم دستگاهی بسازیم، اندکی ترس داشتیم، اما اکنون مطمئن هستیم که دستگاهها بهنحو مطلوب ساخته میشوند. درواقع تحریم برای ما نتیجهاش بالا رفتن اعتمادبهنفس، توان علمی و عملی و روحیهمان بود؛ برای اینکه خودمان وارد عمل شویم و مشکلات را از پیش پا برداریم.