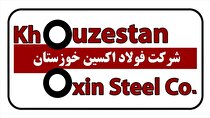
به گزارش می متالز، ایران بزرگترین تولیدکننده آهن اسفنجی جهان محسوب میشود؛ بهطوری که در سال گذشته حدود 25 درصد آهن اسفنجی جهان در ایران تولید شد. از این رو آهن اسفنجی، مهمترین خوراک فولادسازیهای ایران است؛ بهنحوی که در سال 2016، بیش از 89 درصد آهن خام تولید شده در ایران از ذوبِ آهن اسفنجی در کورههای قوس الکتریکی تهیه شد. در نمودار 1، حجم تولید آهن اسفنجی در ایران، آورده شده است.
همانطور که در نمودار مشاهده میشود، روند تولید آهن اسفنجی در ایران از سال 2007، صعودی بوده است؛ بهطوری که طی 10 سال اخیر، تولید آهن اسفنجی ایران، در مجموع 114 درصد رشد داشته است. با توجه به اهمیت این ماده در ایران، تاریخچه و تکنولوژی تولید آن مورد بررسی قرار گرفته است.
آهن اسفنجی، حاصل احیای مستقیم و بدون ذوب گندله در کورههای احیای مستقیم است که بهدلیل شکل متخلل آن به آهن اسفنجی معروف شده است. در روش احیای مستقیم، آهن جامد، بهطور مستقیم و بدون نیاز به ذوب، از اکسید آهن تولید میشود. اغلب فرآیندهای احیای مستقیم، بر پایه گاز یا زغالسنگ بنا نهاده شدهاند. خوراک کورههای احیای مستقیم، سنگ آهن 10 تا 30 میلیمتر یا گندله سنگ آهن است. تولید آهن اسفنجی، در واقع جایگزینی برای تولید فولاد به روش کورهبلند است. این محصول که حاوی بیش از 94 درصد آهن است، در کوره قوس الکتریکی، ذوب و تصفیه میشود. از آنجایی که این روش، در ظرفیت تولیدهای پایینتری از تولید فولاد قابل استفاده است، یک راه مناسب برای تولید فولاد در حجمهای به مراتب پایینتر از کوره بلند محسوب میشود.
نخستین پتنت تولید آهن اسفنجی، در سال 1792 در کشور انگلستان ثبت شده است. در این روش، از کوره دوار استفاده شده است. این روش در قرن 19 میلادی توسعه یافت؛ بهطوری که از سال 1920 بیش از 100 طرح مختلف برای تولید آهن اسفنجی اختراع و اجرایی شد که اغلب آنها ناموفق بودند. دوره مدرن تولید آهن اسفنجی، از تاریخ 5 دسامبر 1957 آغاز شد. در این روز، فولادسازی بزرگ هایسلا (Hylsa) برای نخستین بار از فرآیند هایل (HYL) برای احیای مستقیم گندله استفاده کرد. در این فرآیند، از گاز طبیعی بهعنوان احیاکننده استفاده میشود. در تاریخ 17 مِی 1969 کارخانه فولادسازی اورگن (Oregon Steel)، برای نخستین بار از کوره میدرکس برای تولید آهن اسفنجی استفاده کرد.
در روشهایی که برای احیای مستقیم از زغالسنگ استفاده میکنند، از کوره افقی دوار استفاده میشود. در این کوره، زغالسنگ و خوراک سنگ آهن، هر 2 از یک دریچه وارد محوطه احیا میشوند. این کوره، زاویه کمی با افق دارد و مدام در حال چرخش به دور محور خود است. در حین اختلاط، به دلیل دمای بالا (800 تا 1050 درجه سانتیگراد) کربن موجود در زغالسنگ اکسید شده و اکسید آهن را به آهن احیا میکند.
این روش، مشابه پخت گندله، از کوره استوانهای عمودی استفاده میکند. با سرازیر شدن خوراک از بالا به پایین، گاز احیاکننده از پایین به بالای کوره دمیده میشود و فرآیند احیا انجام میشود. فشار گاز در کوره هایل، حدود 5 تا 6 اتمسفر و دما بین 800 تا 850 درجه سانتیگراد است در حالی که در فرآیند میدرکس، فشار گاز، به 1 تا 1.5 اتمسفر کاهش یافته است. در کوره میدرکس، پیش از کوره، بر سر راه گاز احیاکننده بازگردانده شده (Circulated)، یک بخش ریفورمر (Reformer) قرار داده شده است. در این بخش، محصولات جانبی احیای مستقیم آهن، یعنی بخار آب و گاز دیاکسید کربن، به همراه گازهای هیدروژن و مونواکسید کربن واکنش نداده، دوباره بازیافت میشوند تا مصرف انرژی کاهش یابد. در ریفورمر، گاز طبیعی وارد شده و علاوه بر گرم شدن، به همراه دیاکسید کربن و بخار آب حاصل از فرآیند احیا، به صورت کاتالیزوری به گاز احیاکننده تبدیل میشود. این گاز احیاکننده وارد کوره عمودی شده و آهن اسفنجی تولید میکند.