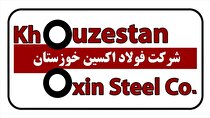
به گزارش می متالز به نقل از روابط عمومی مجتمع مس سرچشمه، مبنای کار تغلیظ در فرآوری مس، خردایش، آسیاب، فلوتاسیون و آبگیری است. در حوزه فرآوری و تغلیظ مواد معدنی محتوی مس، سه شرکت صاحبنام Metso، Outotec و FLSmidth بهعنوان معتبرترین شرکتها شناخته میشوند. تکنولوژی بهکار رفته ازسوی شرکتهای Outotec و FLSmidth به یکدیگر نزدیکتر است و تکنولوژی Metso تفاوتهایی با تکنولوژی دو شرکت دیگر دارد. در هر صورت، اساس کار تمامی تکنولوژیها در مرحله تغلیظ شناور کردن مواد معدنی دارای مس است، تا این ماده از باطله جدا شود. در زمینه ذوب نیز تکنولوژیهای Flash Smelting، Noranda، Mitsubishi، Ausmelt و SKS فرآیندهای خاص خود را برای ذوب کنسانتره مس طی میکنند. درباره تکنولوژیهای ذوب، تفاوتهایی که از سوی صاحبان تکنولوژی ایجاد شده، گستره وسیعتری را در بر میگیرد.
تکنولوژی قدیمی مورد استفاده از سوی شرکت ملی صنایع مس ایران در ذوب سرچشمه، کورههای انعکاسی (Reverbratory) بود که با تکنولوژی جدید Flash جایگزین شد. درباره خاتونآباد نیز از ابتدا از تکنولوژی Flash استفاده شد که در سال آینده با جدیدترین فناوری کوره فلش Outotec بهروزرسانی خواهد شد. بهرغم تنوع روشها در ذوب مس در دنیا، دلیل استفاده شرکت ملی صنایع مس ایران از تکنولوژی Flash، استقبال جهانی از این روش است؛ به نحوی که بیش از 50 درصد مس دنیا با این روش تولید میشود. این استقبال جهانی را میتوان اعتباری برای مناسب بودن روش Flash دانست. این تکنولوژی علاوه بر اینکه دوستدار محیطزیست است، میتواند ظرفیتهای بالایی را در تولید پوشش دهد که منجر به کاهش بهای تمام شده ذوب هر تن کنسانتره میشود.
روشهای هیدرومتالورژی نسبت به فرآیندهای پیرومتالورژی، بیشتر دوستدار محیطزیست هستند. تکنولوژیهای اقتصادی در این حوزه، شامل فرآوری کانسنگهای اکسیدی مس است. میزان استفاده از فرآیندهای هیدرومتالورژیکی برای فرآوری کانسنگهای سولفیدی یا کنسانتره سولفیدی مس، بسیار محدود است. البته دلایل مختلفی باعث شده روند تحقیق و توسعه در زمینه استفاده از فرآیندهای هیدرو برای فرآوری کنسانتره سولفیدی مس، با جدیت بسیار دنبال شود که نتیجه آن، معرفی برخی تکنولوژیهای جدید در مقیاس صنعتی از سوی برخی شرکتهای صاحبنام است. بهطور مثال، شرکت Glencore یکی از این شرکتهایی است که تکنولوژی نسبتاً جدید Albion را برای لیچینگ کنسانترههای سولفوری مس (با روش هیدرومتالورژی) ابداع کرده است. کنسانترههای سولفوری را نمیتوان بهراحتی با استفاده از اسیدسولفوریک لیچ کرد، این کار از راندمان مناسبی برخوردار نیست (برخلاف خاکهای اکسیدی). در فرآیند Albion، با استفاده از آسیابهای IsaMill مواد محتوی مس در اندازههای بسیار کوچک مورد خردایش قرار میگیرد. در نهایت با بهینهسازی شرایط فرآیندی از جمله دما و فشار و استفاده از اکسیژن، مس مورد استخراج قرار میگیرد. امروزه اغلب تولیدکنندگان مس ترجیح میدهند کنسانتره خود را با روش ذوب فرآوری کنند. روشهای هیدرومتالورژی در فرآوری کنسانترههای سولفیدی کمتر مورد استفاده قرار میگیرد.
درباره پالایش نیز تکنولوژی ISA در پالایشگاه خاتونآباد و سرچشمه مورد استفاده قرار گرفته که مدرنترین و کارآمدترین تکنولوژی در این بخش از فرآیند تولید مس بهشمار میآید. در صنایع پاییندستی نیز از کورههای Asarco برای ذوب کاتد استفاده میشود. ماشین ریختهگری Hazelett نیز برای تولید مفتول مورد استفاده قرار میگیرد. نکته قابل توجه آنکه تکنولوژی تولید مفتول در شرکت ملی صنایع مس ایران، آمریکایی است و دسترسی به قطعات یدکی و همچنین امکان بهروزرسانی خط تولید در ایران دشوار است. این امر باعث شده تجهیزات بهکار رفته عموماً کارآیی مناسب را نداشته باشند؛ بنابراین تغییر تکنولوژی تولید مفتول، میتواند یک راهحل مناسب برای حل مشکلات موجود باشد.
مسیر تکامل تکنولوژی، عموماً بهبود بسیاری از پارامترهای اقتصادی و فنی تولید را نسبت به نسلهای قبلی خود بههمراه دارد. این بهبود باعث افزایش بهرهوری و رشد شاخصهای اقتصادی و تسهیل شرایط بهرهبرداری میشود که از عوامل اصلی هستند که توجه صاحبان صنایع را برای انتخاب یک تکنولوژی به خود جلب میکند. پر واضح است که این امر در نهایت اثر خود را در افزایش بهرهوری تولید و کاهش بهای تمام شده محصول نشان میدهد. یکی دیگر از نکات مهمی که در بهروزرسانی فناوریها مورد توجه قرار میگیرد، بهبود شاخصهای زیستمحیطی است. توجه به محیطزیست یکی از مهمترین دغدغههای حال حاضر بسیاری از صنایع جهان است. این عامل در بهروزرسانی تکنولوژی نیز اهمیت زیادی دارند. بهعنوان مثال، استفاده از تکنولوژی کوره فلش در شرکت ملی صنایع مس ایران منجر به افزایش ظرفیت تولید و کاهش مصرف انرژی و سوختهای فسیلی شده است. با وجود کاهش قابل ملاحظه غلظت گازهای دی اکسید کربن و منوکسید کربن، غلظت گاز دیاکسید گوگرد در روش کوره فلش بسیار بالاتر از کوره انعکاسی است که در نتیجه، تولید اسید سولفوریک را نیز از نظر فرآیندی اقتصادیتر و از نظر فنی راحتتر میکند.
همانطور که پیشتر اشاره شد، در فرآیندهای هیدرومتالورژی بیشتر به جوانب زیستمحیطی صنعت توجه میشود که این موضوع، یکی از دلایل اصلی توجه و تمرکز به توسعه این نوع از فرآیندهای تولید است. شاید در آیندهای نه چندان دور، آلایندگی پایینتر این نوع از تکنولوژیها و قابلیتهای دیگر آن نظیر امکان فرآوری مواد کمعیار و کانیهای چندعنصری، موجب سبقت گرفتن آنها از تکنولوژیهای ذوب شود.
در یک دهه گذشته، شرکت ملی صنایع مس ایران در بخش ذوب، پالایش و همینطور تغلیظ، اقدام به تأمین تکنولوژی، راهاندازی واحدهای جدید و نوسازی برخی واحدهای قدیمی کرده است. تغییر تکنولوژی کوره انعکاسی به Flash در مجتمع سرچشمه، یکی از اقدامات پیچیده و مهم برای شرکت ملی صنایع مس ایران بود. پیچیدگی این موضوع بهدلیل توسعهای (Brown-Field) بودن این پروژه بود. در پروژههای سرمایهگذاری با ماهیت جدید (Green Field)، شرکت سرمایهگذار پروژه را در یک محدوده مشخص و بدون نگرانی از تداخل کاری با دیگر بخشهای موجود در یک منطقه یا مجتمع صنعتی اجرا میکند. اما در طرحهای با ماهیت توسعهای، پروژه ماهیت اصلاحی و جایگزینی تکنولوژی جدید دارد که باید کنار یا درون یک مجموعه تولیدی فعال اجرا شود که دغدغههایی از نظر احتمال بروز حادثه برای عوامل پروژه و بهرهبردار و همچنین اختلال در فرآیند تولید را باعث میشود. یکی دیگر از دغدغهها درباره پروژههای Brown-Field، زمان راهاندازی و سوئیچ کردن به سیستم جدید و برقراری ارتباط با مجموعههای مشترک است.
بهعنوان نمونه، در پروژه ذوب سرچشمه، تردد ماشینآلات بزرگ حمل مواد مذاب و سایر فعالیتهای بهرهبردار میتوانست باعث اختلال در کار و نیز ایجاد شرایط مخاطرهآمیز برای عوامل پروژه شود. فعالیت عوامل پروژه نیز میتوانست در روند تولید مشکل ایجاد کند. البته با تدابیر در نظر گرفته شده، پروژه تغییر تکنولوژی به کوره Flash خوشبختانه و به لطف خداوند، بدون هیچگونه حادثهای برای عوامل پروژه و بهرهبردار انجام شد. البته توقفاتی در تولید برای راهاندازی ذوب جدید Flash ایجاد شد؛ چراکه بخشی از تجهیزات دو کارخانه مشترک بود و گریزی از توقف در روند تولید وجود نداشت تا شرایط برای جابهجاییهای لازم ایجاد شود. وضعیت بهوجود آمده ناشی از اجرای توافق برجام، انتقال تکنولوژی و اجرای این طرح را تسهیل کرد و این انتقال چندان با مشکلات ناشی از تحریم روبهرو نشد. درباره تأمین تجهیزات و انتقال ارز نیز چالش چندانی بهوجود نیامد.
در سه مورد از پروژههای مهم شرکت مس (اسید سرچشمه و خاتونآباد و همینطور کارخانه ذوب خاتونآباد) نیز خوشبختانه تأمین تجهیزات قبل از تحریمهای اخیر انجام شد و امروز تجهیزی که نیاز به انتقال داشته باشد، باقی نمانده است. ممکن است شرکت در ادامه و در برخی خدمات مانند استفاده از مهندسان خارجی ناظر برای نصب و راهاندازی (Supervisor) با مشکلاتی روبهرو شود، اما با تکیه بر تخصص کارشناسان داخلی و در صورت نیاز استفاده از متخصصان سایر کشورهای دوست بر مشکلات فائق خواهیم آمد. موضوع اصلی تأمین تجهیزات بوده که بهطور کامل انجام شده است. در اجرای پروژههای فرآوری چنانکه پیشتر ذکر شد، اساس تکنولوژیهای بهکار رفته (بهویژه در واحدهای تغلیظ) شباهت بسیاری با یکدیگر دارند و تنها در بعضی از مکانیزمها و تجهیزات، تفاوتهایی دیده میشود. بسیاری از متخصصان شرکت ملی صنایع مس ایران تسلط کاملی بر بهرهبرداری از این تجهیزات دارند که منجر به عملکرد مطلوب واحدهای تابعه شرکت شده است. در زمینه بهینهسازی و بومیسازی فرآیندها، فعالیتهای گستردهای انجام شده و بهطور جدی و موثر نیز در حال پیگیری است.
بومیسازی یکی از موضوعات کلیدی است که دههها درباره آن صحبت و به آن پرداخته شده است. این مقوله را باید به بومیسازی تجهیزات و قطعات و همینطور بومیسازی دانش فنی تقسیمبندی کرد. برای بومیسازی قطعات، تلاشهای بسیاری در شرکت ملی صنایع مس ایران انجام شده و میشود و پیشرفتهای ملموسی نیز تا کنون حاصل شده است. اما نبود رویکرد سیستماتیک در این زمینه باعث شده هنوز مشخص نباشد که بومیسازی چه قطعات و تجهیزاتی در صنعت مس یا سایر صنایع، توجیه فنی و اقتصادی دارد و در چه مواردی، بدون توجیه است؛ به عبارتی هنوز دانش و اطلاعات کافی را برای هدفگذاری در این حوزه نداریم. این مبحث در مقوله بومیسازی دانش فنی تولید نیز در سطح چالشبرانگیزتری قابل مشاهده است. اصولاً دولتها یا نهادهای دولتی در کشورهای در حال توسعه، پایهگذار سازمانهایی هستند که در قالب بخش خصوصی یا دولتی، محور جذب و بومیسازی تکنولوژیهای روز دنیا باشند. بررسی عملکرد شرکتهای صاحب تکنولوژی در کشور چین، شاید الگوی مناسبی برای مطالعه روند انتقال تکنولوژی و بومیسازی آن باشد. چین از یک سو بازار بزرگی برای تکنولوژیهای مختلف تولید بهشمار میرود و از سویی دیگر، نگرش سیستماتیک برای انتقال و بومیسازی تکنولوژی در این کشور حاکم است. وجود همزمان هر یک از اجزای فوق (بازار مناسب و نگرش سیستماتیک)، لازمه دستیابی به هدف مورد بحث است و صرفاً با سرمایهگذاری و نگرش سیستماتیک در این حوزه، نمیتوان اقتصادی بودن فرآیند انتقال و بومیسازی تکنولوژیهای تولید را در یک کشور توجیه کرد.
در ایران، واحدهای تحقیق و توسعه و برخی شرکتهای مهندسی، پتانسیل لازم را برای پایهگذاری مسائل مرتبط با این حوزه در اختیار داشته و دارند؛ ولی نبود ساختار سیستماتیک در این حوزه، نگرش جدی به فرآیند تحقیق و توسعه و همچنین ضعف اقتصادی شرکتهای مشاور، باعث شده کشور در کمتر حوزهای بتواند بهطور مدون نسبت به گردآوری دانش و بسط و توسعه فناوریها اقدام کند. به موارد فوق، مقوله محدودیت بازار داخلی را نیز باید اضافه کرد. طبعاً در چنین محیطی نمیتوان انتظار پویایی لازم را برای بومیسازی تکنولوژیها داشت و ما همچنان در حوزههایی که حتی فضا و بازار لازم برای عرضاندام داریم، در قالب یک مصرفکننده صرف تکنولوژی و واردکننده آن، ظاهر خواهیم شد.
نوع تفسیر و برداشت از انتقال تکنولوژی بسیار مهم است. بهعنوان مثال، آیا منظور این است که شرکت ملی مس که از تکنولوژی Flash برای واحدهای ذوب خود استفاده میکند، در ادامه بتواند خود کوره Flash بسازد یا اینکه در فرآیند بهرهبرداری تسلط کافی داشته و نیاز به صاحب تکنولوژی نداشته باشد. به نظر میرسد برداشت منطقی، موضوعی بین این دو باشد. یعنی تسلط کافی و کامل برای بهرهبرداری، رسیدن به ظرفیت اسمی یا حتی عبور از آن و نیز ساخت داخل بهویژه در بخش تجهیزات پرمصرف که تأثیر قابلتوجهی بر قیمت تمام شده خواهند داشت. اینکه تمامی تجهیزات را بهطور کامل بومیسازی کنیم، چندان منطقی به نظر نمیرسد. همانطور که پیشتر اشاره شد، باید داخلیسازی هر تجهیزی، توجیه فنی و اقتصادی داشته باشد. حتی صاحب فناوری نیز برخی قطعات مورد نیاز برای ساخت یک تجهیز فناورانه را از محل دیگری تأمین میکند که شاید دسترسی به دانش ساخت آن برای او نیز یا وجود نداشته یا از منظر اقتصادی توجیه لازم را نداشته باشد. در نتیجه انتظار اینکه تمام تجهیزات از صفر تا صد در داخل ساخته شود و مورد بهرهبرداری قرار گیرند، خیلی معقول نیست. بنابراین تسلط کامل بر نحوه بهرهبرداری و تأمین بخشی از تجهیزات پرمصرف، خود به معنای بومیسازی تا مرحلهای مناسب است. همانطور که اشاره شد، در برخی موارد طراحی و ساخت بعضی تجهیزات به هیچوجه برای مصرفکننده صرفه و توجیه اقتصادی ندارد. نتیجه اینکه تسلط کافی در بهرهبرداری از تکنولوژی وارد شده، افزایش بهرهوری، استفاده بهینه و اقتصادی از تکنولوژیهای جدید یا خودکفایی در کپی کردن یک تکنولوژی، هر کدام منظوری متفاوت را در انتقال تکنولوژی میرساند که بهطورقطع گزینه دوم نمیتواند راهکاری منطقی و مناسب باشد.
از دیگر موارد مهمی که درباره انتقال تکنولوژی باید بدان توجه شود، تسلط به مباحث فنی و حقوقی این فرآیند است چراکه این مسائل هنگام عقد قرارداد انتقال تکنولوژی، میتواند به واردکننده آن کمک بیشتری کند. برخورداری از استراتژی روشن و مشخص، پیشنیاز اصلی انتقال تکنولوژی است. هدف اصلی از انتقال تکنولوژی و برنامههای آتی در زمینه آن باید بهروشنی بررسی شود. حتی شاید نیاز باشد یک سازمان مشخص برای انتقال تکنولوژی بهعنوان متولی این امر در نظر گرفته شود و این امر نیازمند توجه ویژه است. در ادامه نوبت به مسائل حقوقی و قراردادی میرسد که تسلط بالایی را به حقوق و قراردادهای بینالملل میطلبد. در این حوزه نیز کاستیهایی در داخل کشور و در بسیاری صنایع وجود دارد که لازمه توجه بیشتر در این زمینه است.
بهعنوان کلام آخر باید گفت که شرکت ملی صنایع مس ایران، شرکتی تولیدمحور است. توجه اساسی این شرکت، به تولید در بهترین و بیشترین حالت ممکن است. پس از تولید اولویت شرکت بر اجرای پروژههای توسعهای معطوف شده است. با توجه به قدمت فعالیت شرکت ملی صنایع مس ایران و سرمایهگذاریهای انجام شده، این شرکت میتواند راهی که شرکتهایی مانند Glencore رفتهاند را بپیماید. شرکت ملی صنایع مس ایران یکی از بزرگترین تولیدکنندگان و تاجران مواد معدنی بهویژه مس در جهان است که در حال حاضر به یکی از صاحبان تکنولوژی در جهان تبدیل شده است. باید توجه داشت که ذخایر معدنی کشور هرقدر هم عظیم باشند، روزی به پایان خواهد رسید. شرکت ملی صنایع مس ایران میتواند با بهرهگیری از امکاناتی که ذکر آن رفت بهعنوان یکی از بازیگران اصلی عرضه فناوریهای مورد نیاز صنایع مس در جهان مطرح شود. طبعاً دستیابی به چنین هدفی نیازمند بهبود ساختارها، سیاستگذاری صحیح و رفتار سیستماتیک با این مقوله و همچنین ایجاد بازار مناسب برای محصولات تکنولوژیک است. کشورهای همسایه ایران، ذخایر بزرگ و دستنخوردهای از مس را در اختیار دارند. اگر صحیح و حسابشده به این صنعت توجه کنیم، میتوانیم در افقی بلندمدتتر، هم در حوزه تولید محصولات زنجیره مس و هم در مقوله دستیابی و بهکارگیری تکنولوژیهای روز دنیا، در بازاری بسیار وسیعتر از آنچه هماکنون در اختیار داریم، قد علم کنیم.