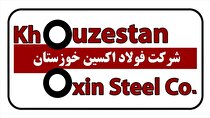
به گزارش میمتالز، ارتباط دانشگاهها با صنایع میتواند یکی از راه حلها باشد. علوم تدریسشده در دانشگاهها و تحقیقاتی که دانشجویان و استادان دانشگاه روی تجهیزات روز دنیا دارند میتواند به صنعت تزریق شده و منجر به ایجاد انقلاب در صنعت فولاد شود. این ارتباط در سالهای اخیر تقویت شده است. در صورتی که بتوان علوم نوین تدریسشده در فضای دانشگاه را با صنعت تلفیق کرد میتوان بسیاری از تجهیزات را بومی سازی کرد و در داخل کشور ساخت.
شرکتهای دانشبنیان نیز به عنوان یکی از حلقههای واسط دانشگاه و صنعت میتوانند نقش مهمی در بومیسازی ایفا کنند. این شرکتها با پرورش ایدههای نو و خلاقانه و اجازه آزمون و خطا در فضای آزمایشگاه، این ایدهها را برای ورود به صنایع آماده میکنند. حمایت از شرکتهای دانشبنیان مستقیما به بهره ور شدن صنایع و همچنین بومی سازی منجر خواهد شد. امروزه ارتباط شرکتهای دانشبنیان با فولادسازان بهبود یافته و اعتماد فعالان حوزه آهن و فولاد به این شرکتها افزایش یافته است.
در روزهایی که خروج ارز از کشور به اقتصاد ضربه میزند و از طرف دیگر نیاز به ارز در داخل کشور احساس میشود، بومی سازی یکی از راههایی است که میتواند از خروج ارز از کشور جلوگیری کند و در استفاده از ارز صرفهجویی شود. هر یک از قطعات و تجهیزاتی که در داخل کشور تولید میشود و در خطوط تولید زنجیره فولاد مورد استفاده قرار میگیرد، موجب صرفهجویی در بخشی از ارزی که قرار بر خروج آن از کشور بود، میشود. از طرف دیگر دانش تولید و تجهیز توسط مهندسی داخلی به نسلهای بعد منتقل میشود. انباشت دانش در کشور میتواند آن را به ثروتی بیبدیل تبدیل کند که قابلیت صادرات آن و ارزآوری از این طریق وجود داشته باشد. در این صورت میتوان زنجیرههای ارزش سایر کشورها را تجهیز کرد و از انباشت دانش، ثروتآفرینی کرد. طبیعتا بومی سازی زنجیره فولاد در کشور با مشکلاتی مواجه است که برطرف کردن آنها به عزم ملی بستگی دارد. فعالان حوزه آهن و فولاد با هم بستگی میتوانند این موانع و چالشها را برطرف کرده و با تمام سرعت به سمت اهداف ترسیمشده حرکت کنند.
مهدی رفیع زاده، سرپرست واحد بومی سازی فولاد هرمزگان به بررسی برخی از چالشهای بومی سازی در زنجیره فولاد پرداخت و عنوان کرد: یکی از چالشهایی که در مجموعه فولاد هرمزگان با آن مواجه هستیم، شناخت و ارزیابی سازندگان قطعات و نوآوران است. شرکتهایی که امکان ساخت تجهیزات و تیپهای مختلف قطعات را دارند، شناختهشده نیستند و شناخت و ارزیابی آنها با هزینههای زیادی صورت میگیرد. ما برای حل این موضوع باید به دنبال راههایی کارآمد باشیم. در مجموعه فولاد مبارکه تجربیاتی ارزشمند انباشته شده است که یکی از راه حلهای ما استفاده از این تجربیات است. تجهیزاتی که در این مجموعه ساخته شده است راهگشای ما در برخی از مسائل بومی سازی است. یکی دیگر از راهحلها آشنایی با سازندگان تجهیزات و شرکتهای نوآور در نمایشگاه هاست. این شرکتها معمولا برندینگ خوبی ندارند و نمیتوانند به خوبی تواناییها و استعدادهای خود را به نمایش بگذارند.
ما با توجه به توانمندی این شرکتها اقدام به مشارکت با آنها میکنیم. وی در ادامه خاطرنشان کرد: اگر این شرکتها خود را با شیوههای بهتری معرفی کنند تا تلاش هایشان بیهوده نباشد و از طرف دیگر نیاز صنایع به راحتی برطرف شود، بسیاری از موانع بومی سازی رفع خواهد شد. پلتفرمی هم به نام کارلینک در یک سال اخیر معرفی شده است که هم فولادسازان میتوانند نیازهای خود را معرفی کنند و هم شرکتهای دانش بنیان و نوآور میتوانند این نیازها را شناسایی کرده و برای رفع آنها گام بردارند. رفیع زاده هم افزایی شرکتهای بزرگ زنجیره فولاد را عامل اصلی سرعت بخشیدن به روند بومی سازی دانست و اظهار کرد: این شرکتها میتوانند در این پلتفرم خود را معرفی کرده یا رزومه خود را برای فولادسازان ارسال کنند و در صورت تایید به ساخت و اصلاح تجهیزات بپردازند.
برای به ثمر رسیدن چنین پلتفرمهایی در جهت رسیدن به اهداف بومی سازی ترسیمشده در صنعت فولاد، نیاز به همت تمام شرکتهای زنجیره فولاد است. شرکتهای تولیدکننده باید تجارب خود را در اختیار دیگران قرار داده و برای دیده شدن بیشتر شرکتهای نوآور داخلی تلاش کنند. اگر این اتفاق رخ دهد، میشود راحتتر سازندگان داخلی را شناسایی و ارزیابی کرد.
سرپرست واحد بومی سازی فولاد هرمزگان روند بومی سازی در فولاد هرمزگان را تشریح کرد و گفت: در دوسال اخیر در مجموعه فولاد هرمزگان، ارزیابی شرکتهای نوآور در اختیار تیم بومی سازی قرار گرفته است. تلاش کردیم این ارزیابیها به بهترین شکل ممکن صورت گیرد تا توانمندترین شرکتها غربال شوند. در گام بعدی، کنترل کیفی و بازرسی تجهیزات ساختهشده در این مجموعه نیز به واحد بومیسازی فولاد هرمزگان سپرده شده است. این واحد با قوانین، مقررات و استانداردهای لازم تجهیزات ساختهشده را آنالیز میکند و نتایج آنالیز را بررسی میکند. کل روند تولید تجهیزات و قطعات با دقت در واحد بومیسازی انجام میپذیرد.
از ابلاغ ساخت قطعات و تجهیزات به سازنده، بازرسی قبل از ساخت، بازرسی حین ساخت، تحویل نهایی و تست نهایی تجهیز و عملکرد در فولادسازی، توسط واحد بومیسازی پایش میشود. تعهدات و ضمانتهای نهایی از شرکتها اخذ میشود تا بهره بردار بتواند تا سالها به خوبی از این قطعات استفاده کند؛ بنابراین کالاها با بیشترین حد اطمینان در فولاد هرمزگان نصب و بهره برداری میشوند.
وی در پایان به رشد چشمگیر این شرکت در بومی سازی قطعات و تجهیزات اشاره کرد و گفت: برای قطعات و تجهیزاتی که قبلا وارد میشدند و امروزه با توانمندی مهندسان ایرانی، در داخل کشور تولید میشوند، از سال ۹۹ تا سال ۱۴۰۰، بیش از ۴۰۰درصد رشد داشتیم. یعنی بهره مندی از تجهیزات بومی سازیشده در مجموعه فولاد هرمزگان بیش از ۴۰۰ درصد افزایش یافته است. در سال ۹۹، ۲۰۰هزار دلار صرفهجویی ارزی داشتیم و در سال ۱۴۰۰ این رقم به ۶میلیون و ۵۰۰هزار دلار افزایش یافت. با پایشها و ارزیابیها و تحولاتی که صورت گرفته، این رشد امکان پذیر شده است. طی ۹ ماه اول سالجاری نیز، ۷۵ کالا در فولاد هرمزگان بومی سازی شده است که معادل ۳۴ میلیون دلار صرفه جویی ارزی است.
منبع: دنیای اقتصاد