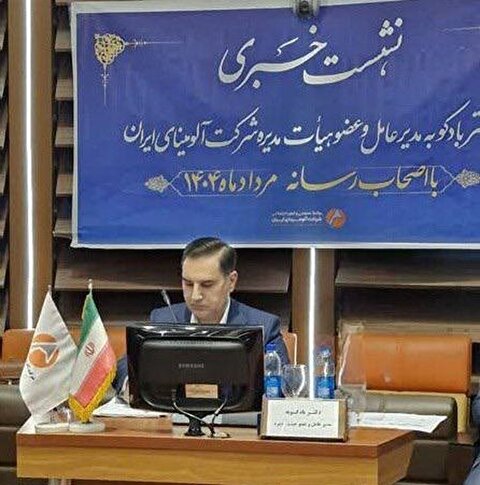
به گزارش می متالز به نقل از مس پرس، رئیس بخش اجرایی طرح اسید سولفوریک مجتمع مس سرچشمه با بیان این مطلب گفت: یکی از نوآوریهای کارخانۀ اسید، موارد مربوط به انرژی است؛ چراکه سیستم خنکسازی کارخانۀ اسید، براساس سیستم کولینگ تاور طراحی شده که در این سیستم، مصرف آب خیلی زیاد است؛ بنابراین، با توجه به کمبود آب در منطقه، تغییر تکنولوژی از کولینگ تاور به ایر کولر در دستور کار قرار گرفت که حدود 80 مترمکعب بر ساعت، آب صرفهجویی میشود.
معینالدینی در ادامه درباره فرآیند تولید اسید سولفوریک گفت: پس از خروج گاز از ناحیۀ صد و گرفتن تمام ناخالصیهای گاز و پایین آمدن درجۀ حرارت، گاز به ناحیۀ 200 منتقل میشود و در ناحیۀ 200، عملیات گرفتن رطوبت، تبدیل so2 به so3 و اسیدسولفوریک انجام میشود.
وی افزود: پس از آن اسید تولیدی که اسید 98.5 درصد است، بهوسیلۀ خطوط سنلساستیو، به چهار مخزن 5450 مترمکعبی منتقل میشود و ازآنجا اسید تولیدی به دو روش شامل روش تراک که چهار بازوی بارگیری است، برای مصرفکنندگان داخلی و بهوسیلۀ قطار به بندر، جهت صادرات منتقل میشود.
معینالدینی اضافه کرد: پس از راهاندازی کارخانۀ اسید، تمام گازهای منتشرشده از کورۀ فلش، توسط کارخانۀ اسید، به اسیدسولفوریک تبدیل میشود و آسمانی آبی، پاک و بدون هیچ گرد و غباری شاهد خواهیم بود.