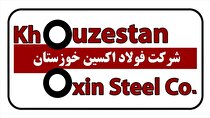
به گزارش میمتالز، با شتاب گرفتن کربنزدایی جهانی در صنایع با انتشار بالای کربن، بسیاری از تولیدکنندگان فولاد در بخش آهنسازی در حال برنامهریزی برای انتقال به فرآیندهای احیای مستقیم آهن (DRI) هستند تا به تولید سبزتر و پایدارتر دست یابند و انتشار CO۲ را تا ۹۰ درصد در مقایسه با روش مرسوم کوره بلند کاهش دهند.
هرچند مزایای زیستمحیطی تولید فولاد سبز واضح است، با این حال گذار به فرآیندهای DR و کوره قوس الکتریکی (EAF) مستلزم صرف هزینههای سرمایهگذاری قابل توجهی است. بنابراین، تولیدکنندگانی که در حال بررسی جنبههای مختلف پروژههای توسعهای جدید یا نوسازی سایتهای موجود خود هستند، باید بتوانند برای دستیابی به بازگشت سریع سرمایه (ROI) و اطمینان از قابلیت اقتصادی گذار به روشهای تولید پایدارتر، بهترین انتخابها را انجام دهند. برای تسریع دوره ROI پروژهها، تولیدکنندگان باید ریسک پروژه را کاهش دهند، تولید را بهسرعت آنلاین کنند و فرآیندهای خود را بهینه سازند تا اطمینان لازم حاصل شود که کارخانه آنها تا حد امکان ایمن و کارآمد عمل میکند.
پیادهسازی تکنولوژیهای با سطح اتوماسیون بالا برای عملکرد ایمن و کارآمد یک فرآیند با مسیر DR-EAF ضروری است. با راهحلهای دیجیتال پیشرفته به کاهش هزینههای عملیاتی، بهبود ایمنی کارگران، افزایش پایداری و بهرهوری و ارائه سریعتر بازگشت سرمایه کمک خواهد شد. سیستمهای کنترل توزیعشده، سیستمهای اطلاعات مدیریت انرژی و سیستمهای مدیریت دارایی، مبتنی بر فناوریهای اندازهگیری و کنترل هوشمند، اطلاعاتی حیاتی را فراهم میکنند که به سادهسازی فرآیندهای تعمیر و نگهداری، عیبیابی و بهرهبرداری کمک میکند. یک پروژه گرینفیلد فرصتی را برای پلنت فراهم میکند تا کاملاً «دیجیتال» متولد شود و بیدرنگ از اجرای فناوریهای جدید مانند سنسورهای هوشمند و تکنولوژیهای کنترل، نرمافزارها و سیستمهای عملیاتی پیشرفته، مدیریت دادههای ابری و تجزیهوتحلیل بهرهمند شود. پیادهسازی این فناوریها از همان ابتدا به تثبیت پایداری فرآیندها در آینده یاری میرساند و از تعالی عملیاتی بلندمدت پشتیبانی میکند، اما میتواند بر زمانبندی پروژه نیز تأثیر بگذارد؛ بنابراین بسیار حیاتی است که ذینفعان پروژه، اتوماسیونهای پیشرفته را هر چه زودتر در مرحله مهندسی و طراحی مدنظر قرار دهند.
اجرای فناوریهای پیشرفته برای اندازهگیریهای بسیار دقیق و قابلاعتماد در جهت بهینهسازی عملکرد یک کارخانه فولادی با قابلیتهای دیجیتالی هوشمندتر و پایدارتر ضروری است. برای مثال یک EAF به ابزار دقیقی نیاز دارد که بتواند پارامترها را با دقت و قابلیت اطمینان در محلهای مختلف اندازهگیری کند. نمونههایی از اینها شامل اندازهگیری سطح فولاد مذاب در کوره، اندازهگیری دما در سراسر EAF و تشخیص نشتی در سیستم آب خنککننده است. اندازهگیری سطح کوره میتواند بسیار چالشبرانگیز باشد، زیرا به دستگاهی نیاز دارد که بتواند در دماهای بسیار بالا بهطور قابلاعتماد کار کند و با تغییرات سریع سطح و وجود غبار و گاز در فضای دودآلود مقابله کند. به این منظور راهحلهایی مانند نسل جدید فرستندههای سطح غیرتماسی راداری ارائه شده است. هنگامی که این فرستندهها در داخل یک جعبه خنککننده با جریان نیتروژن نصب میشوند، تأثیرات فرآیند و دمای محیط را بر دستگاه کاهش میدهند. شرایطی مانند لرزش، رطوبت و گرما اندازهگیری دمای EAF را چالشبرانگیز میکند. این محیط سخت اغلب منجر به خرابی اتصالات فیزیکی میشود که میتواند منجر به خطاهای اندازهگیری زیاد، خطرات ایمنی و خاموشی برنامهریزینشده پرهزینه شود. برای مقابله با این چالش، میتوان از فرستندههای دمای بیسیم جدید استفاده کرد که آسیب کابل و لولهها را از بین میبرد و منجر به کنترل بهتر دما، کاهش هزینههای تعمیر و نگهداری و زمان کوتاهتر فرآیند میشود. نشت آب خنککننده میتواند عملکرد و کارایی کوره را به میزان قابل توجهی کاهش دهد و پتانسیل آسیب رساندن به تجهیزات کلیدی را نیز دارد، بنابراین تشخیص نشت بهموقع ضروری است. تشخیص نشت سریع و قابلاعتماد مستلزم نصب فلومترهای بسیار دقیق است. فلومترهای مغناطیسی پیشرو عملکردهای قابلقبولی در این زمینه نشان داده و دقت اندازهگیری آب خنککننده را تا ۰.۱۵ درصد در نرخ جریان ارائه میدهند. این امر تشخیص سریعتر و قابلاعتمادتر نشت و عملکرد کوره را بهبود میبخشد.
مزایای بهینهسازی فرآیند میتواند شامل افزایش در دسترس بودن و توان عملیاتی تجهیزات و کاهش قابلتوجه هزینههای انرژی و تنوع کیفیت محصول باشد. تولید DRI یک فرآیند شیمیایی ترکیبی است و بنابراین بیشتر شبیه یک کارخانه شیمیایی است تا یک کوره بلند سنتی. سیستم کنترل و ایمنی یکپارچه (ICSS) مناسبترین پلتفرم برای چنین کاربردهایی است. یک ICSS پیشرفته و مدرن، عملکرد خوبی برای فرآیند پیچیده تولید DRI ارائه میدهد، درحالیکه تطبیقپذیری، انعطافپذیری و سرعت آن امکان عملکرد بهینه کارخانه را تضمین میکند. شیرهای کنترلی همچنین با ایجاد امکان هدایت انتخابی گاز کوره، سوختهای گازی، بخار، هوای احتراق و گازهای دودکش با توجه به محل سیکلهای عملیاتی و همچنین راهاندازی سیستم آب مداربسته، نقش مهمی در بهینهسازی کارآیی فرآیند DRI دارند. طیف وسیعی از خدمات در محیطهای شدید و شرایط متغیر فرآیندی، ازجمله کاویتاسیون، سایش، نویز محیطی بالا، دمای بالا و افت فشار بالا، فرآیند DRI را به یک برنامه چالشبرانگیز برای شیرهای کنترلی تبدیل کرده است؛ بنابراین، انتخاب تجهیزاتی که با وجود این شرایط بهطور قابلاعتماد عمل کنند، یک نکته کلیدی برای تأمینکنندگان تجهیزات اتوماسیون است. فرآیندهای DRI و EAF گازهای سمی و قابلاحتراق مختلفی مانند مونوکسید کربن و هیدروژن تولید میکنند که خطرات ایمنی و زیستمحیطی آشکاری را ایجاد میکنند؛ بنابراین برای سازمانها حیاتی است که اطمینان حاصل کنند سیستمهای تشخیص گاز و سیستمهای تهویه قابلاعتماد وجود دارند. تأمینکنندگان فناوری اتوماسیون، تشخیص گاز نقطهای سیمی و بیسیم، تشخیص گاز مسیر باز و راهحلهای تشخیص نشت گاز اولتراسونیک را برای حمایت از تولیدکنندگان فولاد سبز ارائه میدهند. این راهحلهای ایمنیِ تشخیص گاز بهگونهای طراحی شدهاند که بهطور مداوم نشت گاز را قبل از اینکه منجر به شرایط حاد شود، پایش کنند و تشخیص دهند تا به حفظ ایمنی کارکنان و سایت کمک کنند.