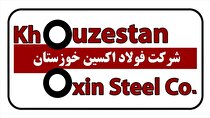
به گزارش می متالز، رضا حبیبی، با اشاره به رقابت منفی موجود در زمینه پروفیل و مقاطع آلومینیومی، اظهار داشت: بیشترین میزان رقابت منفی در حوزه صنعت آلومینیوم، مربوط به تولید پروفیلهای درب و پنجره میشود که برخی از شرکتهای تولیدکننده ثبت نشده و به صورت غیرقانونی فعالیت میکنند، فعالیت این دسته از شرکتها موجب رقابت منفی در بازار شده است.
وی عنوان کرد: اواخر دهه 80 بیشترین رونق تولید را داشتیم و عامل اساسی افزایش میزان تولید شرکت آلومتک در آن سالها، تعامل این شرکت با صنایع آلومینیوم جهانی بود؛ در آن زمان مرزها باز بود و تحریمها تا این اندازه ما را محدود نکرده بود، به همین خاطر واردات و صادرات به راحتی انجام میشد و این عامل، تاثیر زیادی بر افزایش ظرفیت تولید کارخانه آلومتک داشت.
مدیر بخش تولید راد و پروفیل شرکت آلومتک درخصوص ظرفیت تولید شمش خالص آلومینیومی در کشور، عنوان کرد: ظرفیت تولید شمش خالص آلومینیومی شرکت آلومینیوم ایران، جوابگوی نیاز تولیدکنندگان محصولات آلومینیومی نیست و اگر مرزهای وارداتی مواد اولیه باز شود، قطعا میزان تولیدات محصولات آلومینیومی نیز افزایش مییابد.
حبیبی با اشاره به اتلاف آلومینیوم در بخشهای مختلف تولید، توضیح داد: در بخش کوره، بیشترین میزان اتلافی مواد اولیه آلومینیومی را داریم و میزان ضایعات در این بخش بیشتر از سایر قسمتها است و در مراحل دیگر، ضایعات برگشتی داریم که به کوره برگردانده و دوباره ذوب و استفاده میشود.
وی با اشاره به میزان اتلاف مواد اولیه آلومینیومی در کوره، عنوان کرد: میزان اتلاف مواد به عوامل مختلفی مثل دمای کوره و شرایط داخلی کوره بستگی دارد که معمولا کمتر از دو درصد است که البته در حجم بالا این عدد، مقدار قابل توجهی از مواد اولیه شرکت را شامل میشود و به همین خاطر تمام تلاش ما این است که میزان ضایعات و تلفات را کنترل و کم کنیم.
مدیر بخش تولید راد و پروفیل شرکت آلومتک درخصوص تولید انواع اکستروژنهای ساختمانی و صنعتی در شرکت آلومتک، اظهار کرد: شرکت آلومتک قادر است انواع اکستروژنهای ساختمانی و صنعتی را تولید کند و در حال حاضر پروفیلهای صنعتی تولید میکنیم که به صورت لولهای در پستهای برق استفاده میشود، یکی از مقاطع تولیدی مجموعه ما همین باسبارها است.
حبیبی در ادامه افزود: لوله باسبارها مقاطع گردی هستند که دارای سایزهای 40 میلیمتر تا 250 میلیمتر است که تا 200 میلیمتر قطر خارجی و ضخامت 6 میلیمتر، در این کارخانه تولید میشود؛ قطر 250 میلیمتر و ضخامت 6 میلیمتر، پروژه جدیدی است که بر آن کار میکنیم و به زودی در آن به نتیجه خواهیم رسید.
وی درخصوص خطوط اکستروژن موجود در شرکت، بیان کرد: در زمینه تولید مقاطع و پروفیلها، دو دستگاه اکستروژن به ظرفیتهای 2200 تن و 1600 تن داریم که ظرفیت اسمی این دستگاهها 10 هزار تن در سال است که متاسفانه در این سالها با توجه به شرایط موجود کشور، تنها توانستهایم 4 هزار تن مقاطع و پروفیل به وسیله این دستگاهها تولید کنیم که این میزان تولید محدود به دلیل بازار مصرفی اندکی است که در این زمینه شاهد آن بودهایم.
حبیبی درخصوص مواد اولیه مورد استفاده در زمینه تولید مقاطع و پروفیلها، خاطرنشان کرد: مواد اولیه مورد استفاده در زمینه تولید مقاطع و پروفیلها، بیلتهای 7،6 و 8 اینچی است که شرکت آلومراد این بیلتها را تولید میکند؛ این کارخانه عموما، از آلیاژهای سری 6 هزار که شامل آلیاژهای 6063، 6101 و 6061 که در شرکت آلومراد تولید میشود، استفاده میکند.
وی در ادامه افزود: آلیاژهای سری 6101 و 6061 آلیاژهای صنعتی و 6063 آلیاژ ساختمانی است که البته در این کارخانه از آلیاژ سری دو هزار که بیشتر در صنایع نظامی کاربرد دارد، نیز استفاده میشود.
مدیر بخش تولید راد و پروفیل شرکت آلومتک درخصوص استفاده از آلیاژهای سری یک هزار، بیان کرد: از آلیاژهای سری یک هزار که آلومینیوم خالص است، بیشتر در مقاطعی که جریان الکترونیکی و استحکام پایینی مد نظر باشد، استفاده میکنیم.
حبیبی در ادامه مطرح کرد: برای تولید باسبارها نمیتوان از آلیاژ سری یک هزار استفاده کرد اما برای تولید برخی از مقاطع که جریان انتقال هادی در آنها، اهمیت دارد و خواص مکانیکی مدنظر نیست، میتوان از این دسته آلیاژ استفاده کرد.
وی درخصوص میزان ضایعات خط اکستروژن، عنوان کرد: دو درصد ضایعات، به اصطلاح ته بیلت است که در بخش اکستروژن ایجاد و براساس قطر بیلت، 7،6 و 8 اینچ میزان ضایعات سنجیده میشود. به طور مثال بیلت 8 اینچ کمتر از سه کیلو و بیلت 7 اینچ، کمتر از دو کیلو ضایعات ته بیلت دارد.
مدیر بخش تولید راد و پروفیل شرکت آلومتک درخصوص حجم ضایعات سرخط، بیان کرد: ضایعات سرخط، به شکل مقطع پروفیل بستگی دارد که هرچقدر مقطع حساستر و حجیمتر باشد، میزان ضایعات بیشتر و هرچقدر مقطع پروفیلی سادهتر باشد، ضایعات کمتری در طی فرآیند تولید، ایجاد میشود. ضایعات تولید شده در کارخانه آلومتک به کورههای کارخانه آلومراد برده و به شمش 6061 تبدیل میشود، تنها 2 درصد ضایعاتی که به سرباره یا خاک کوره تبدیل میشود، غیرقابل استفاده هستند.