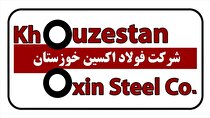
به گزارش می متالز، صنایعی چون فولاد و مس جزو صنایع پرمصرف نسوز هستند که حدود ۹۰درصد نیاز خود را بهوسیله تولیدکنندگان داخلی تامین میکنند. فعالان این حوزه معتقدند، صنعت نسوز به خوبی نیاز آنها را تامین میکند.
ایرج مختارپور، مدیر تعمیرات نسوز شرکت فولاد مبارکه درباره مصرف نسوز این شرکت اظهار کرد: فولاد مبارکه شرکتی است که بهطور تقریبی تمام زنجیره تولید فولاد را در اختیار دارد، از اینرو در این زنجیره کورههای بسیاری وجود دارد که نیاز به نسوز دارند. از ابتدای خط تولید فولاد، کورههای آهک، گندلهسازی و آهن اسفنجی با دمای بالای هزار درجه سانتیگراد کار میکنند. هر کورهای که به دمای بالای ۷۵۰سانتیگراد نیاز داشته باشد، به نسوز نیز احتیاج خواهد داشت.
مختارپور در پاسخ به این پرسش که شرکت فولاد مبارکه چه میزان نسوز مصرف میکند، گفت: شرکت فولاد مبارکه در ابتدای راهاندازی به ازای تولید هر تن فولاد ۳۰کیلوگرم نسوز مصرف میکرد اما با توجه به فعالیت مشترکی که بین شرکت فولاد مبارکه با تولیدکنندگان نسوز و همچنین مراکز پژوهشی و دانشگاهی انجام شده، بهتدریج این مصرف کاهش پیدا کرده است. وی ادامه داد: در سال۹۷ شرکت فولاد مبارکه میزان مصرف نسوز خود را به ۷.۶کیلوگرم برای هر تن فولاد کاهش داده، این درحالی است که میانگین مصرف جهان حدود ۱۵کیلوگرم به ازای تولید هر تن فولاد است. البته در ژاپن رکوردهای بالاتری نیز وجود دارد. بنابراین این ظرفیت در شرکت وجود دارد که به سمت کاهش مصرف نسوز بیشتری سوق پیدا کند. مختارپور در ادامه خاطرنشان کرد: در ابتدای راهاندازی شرکت بین ۷۵ تا ۸۰درصد نسوز از خارج تامین میشد اما درحالحاضر با اقدامهای انجام شده، قادر شده ۹۵تا ۹۶درصد نسوز موردنیاز خود را از داخل تهیه کند. این درصد اندک نسوز خارجی نیز مواد و قطعاتی است که فناوری تولید آنها در ایران موجود نیست.
مدیر تعمیرات نسوز شرکت فولاد مبارکه یادآور شد: البته با توجه به تحریمها، گامهای مهمی برای تولید این نسوزهای خارجی برداشته شده و هماکنون نیز بخشی از این نسوزها در حال بومیسازی هستند. مختارپور در پاسخ به این پرسش که فناوری واحدهای تولیدی تا چه اندازه روزآمد شدهاند، گفت: صنعت نسوز تنها صنعتی است که از ابتدای راهاندازی به صورت خصوصی اداره شده است، از اینرو صنعتی که به صورت خصوصی اداره شود، در زمینه روزآمد کردن فناوری و دانش خود سرآمد خواهد بود. اگر حدود ۹۵درصد نسوز در داخل تولید میشود، درحقیقت بخش خصوصی این تحقق را امکانپذیر کرده است. اما اگر بخشی از این نسوزها از خارج تهیه میشود، به این دلیل است که برخی از مواد اولیه این نسوزهای خاص در داخل موجود نیست. وی در پایان خاطرنشان کرد: اگر از محدودیتها بهدرستی استفاده شود، میتوانند تبدیل به فرصت شوند. تحریمها از این دست محدودیتهاست و صنعت فولاد و صنعت نسوز از این محدودیتها نهایت استفاده را بردهاند.
همچنین جواد مرادی، کارشناس واحد تعمیرات نسوز شرکت ملی صنایع مس ایران درباره استفاده نسوز در صنعت مس اظهار کرد: از نظر مصرف مواد نسوز، صنعت فولاد در ردیف نخست قرار دارد و میزان مصرف نسوز در صنعت مس نسبت به فولاد کمتر است. از آنجا که واحدهای مس کورههای کمتری دارند از مواد نسوز کمتری استفاده میکنند. مرادی در ادامه توضیح داد: بهطورکلی صنعت فولاد برای هر تن فولاد نیاز به ۱۸کیلو نسوز دارد، اما صنعت مس به حدود ۹کیلو برای تولید هر تن مس نیاز دارد، به عبارت دیگر به اندازه نصف صنعت فولاد، صنعت مس به نسوز نیاز دارد. وی در پاسخ به این پرسش که صنعت مس ایران در قیاس با میانگین جهانی چه میزان نسوز استفاده میکند، گفت: صنعت مس در ایران حدود ۳ تا ۳.۵کیلو از کشورهای پیشرفته مانند آلمان و ژاپن نسوز را مورداستفاده قرار میدهد. درمجموع تمامی کورههای فلش، الکتریکی، کنتاکتور و آندسازی بیشترین مصرف را دارند، اما در کورههای کنتاکتور شرکت ملی مس نرخ نسوز برابر با کشوری مانند ژاپن است. از اینرو چندان از کشورهای پیشرفته جهان عقب نیستیم. کارشناس واحد تعمیرات نسوز شرکت صنایع ملی مس ایران در ادامه درباره میزان مصرف نسوزهای داخلی توضیح داد: تا ۱۰سال پیش حدود ۶۰درصد مواد نسوز موردنیاز خود را از خارج تامین میکردیم اما این میزان درحالحاضر به ۹۰ تا ۹۵درصد رسیده است. مرادی در پاسخ به این پرسش که ۵ تا ۱۰درصد نسوزهای خارجی قابلجایگزینی با نسوزهای داخلی نیستند، عنوان کرد: برخی نسوزها خاص هستند و تولیدکنندگان داخلی هنوز نتوانستهاند به فناوری تولید آنها دست پیدا کنند. برای نمونه برخی کورههای دوار که در عملیاتی مس مات را تبدیل به مس بلیستر میکنند، در آنها منفذهایی برای دمش هوا تهویه شده است تا خلوص ذوب را بالا ببرد، از اینرو به نسوزهای خاص نیاز دارند که شرکتهای داخلی به تولید آن دست نیافتهاند؛ چون این کورهها به نسوزهایی با کیفیت بالاتر و مقاومت بیشتر نیاز دارند. وی در پاسخ به این پرسش که آیا برای تولید این نسوزها مشکل مواد اولیه وجود ندارد، گفت: مشکل نسوزهای خاص، فناوری تولید است. البته مواد اولیهای که کشورهای اروپایی استفاده میکنند از منابع خالصتر و با کیفیت بالاتری تامین میشود. اما در کل در تولید این نسوزها فرآیند و فناوری تولید تاثیر بیشتری دارد. کارشناس واحد تعمیرات نسوز شرکت صنایع ملی مس ایران با اشاره به شرایط تحریمها عنوان کرد: از قبل درخواستهایی برای نسوز داشتیم که باید از خارج تامین میشد، از اینرو برخی قراردادهای خارجی به دلیل تحریمها نیمهکاره رها شد و ما نیز سعی کردیم بخشی از این نسوزها را از داخل تامین کنیم. مرادی با تاکید بر اینکه تحریمها سبب خودباوری ما در زمینه صنعت میشود، عنوان کرد: اگر واحدهای داخلی تلاش بیشتری انجام دهند، همین ۵ درصد نسوز خارجی را نیز میتوانند در داخل تولید کنند. وی در ادامه خاطرنشان کرد: اگر شرکتهای تولیدکننده با شرکتهای مصرفکننده هماهنگ باشند، میتوانند بستر مناسبی را برای رشد فراهم کنند. شرکتهای تولیدکننده بیشتر به حجم فروش توجه دارند. البته برخی نسوزها ممکن است مصرف کمتری داشته باشند بنابراین مجبور به واردات هستیم. کارشناس واحد تعمیرات نسوز شرکت صنایع ملی مس ایران در ادامه عنوان کرد: البته اگر واحدهای تولید نسوز با یکدیگر کنسرسیوم تشکیل دهند و فناوریهایشان را در اختیار هم قرار دهند، میتوانند بسیار موفقتر عمل کنند. این درحالی است که بسیاری از شرکتهای نسوز در ایران جزیرهای عمل میکنند. درحالیکه بیشتر شرکتهای کوچک با ایجاد کنسرسیوم با شرکتهای بزرگ میتوانند کارهای بزرگی انجام دهند.