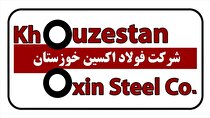
به گزارش می متالز، مهندس یزدیزاده در این پنل گفت: قطعهسازی در ذوبآهن از همان ابتدای احداث این شرکت وجود داشته است و اکنون به تکنولوژیهای روز دنیا مجهز شده است. این شرکت ورود به فرآیندسازی را شروع کرده و از قطعهسازی گذشته است.
وی اظهار داشت: در حوزه ریختهگری هم توفیقات خوبی به دست آمدهاند. در حوزه تولید محصول پروژه تولید ریل را اجرا کردیم و به دنبال قطع وابستگی در تولید این محصول هستیم.
مدیرعامل ذوبآهن اصفهان گفت: این مجتمع عظیم صنعتی ۸۰ درصد قطعات و تجهیزات مورد نیاز خود را بومیسازی کرده است. بومیسازی دربهای فکلسیبل باتریهای ککسازی ذوبآهن که نماد خود باوری در شرایط تحریم است ایران را در جمع معدود کشورهای برخوردار دنیا از این تکنولوژی قرار داد.
وی اظهار داشت: بیش از 95 درصد از مراحل ساخت این دربها در ذوبآهن اصفهان اجرا شده و بخش جزیی آنکه امکان ساخت در شرکت نیز داشت تنها برای سرعت در روند طرح به شرکتهای بیرونی واگذار شده است.
مهندس یزدی زاده تصریح کرد: هم اکنون بیش از 85 درصد از قطعات و تجهیزات مکانیکی ذوبآهن اصفهان بومیسازی شده است و مابقی نیز به جزء اندکی که در حال حاضر امکان تامین آنها در داخل کشور وجود ندارد، با توجه به دستیابی به دانش فنی وتکنولوژی ساخت آنها در کارخانه، به دلیل محدودیتهای تجهیزاتی از طریق سازندگان توانمند داخل کشور بومیسازی و تامین میشوند.
مدیرعامل ذوبآهن اصفهان گفت: علاوه بر تولید ریل و تیرآهن H30 و دیگر محصولات جدید، طرح تزریق پودر زغال به کوره بلند (PCI) که مرحله تست نهایی را میگذراند ریومپینگ ایستگاه هفت ریختهگری بدون حضور کارشناسان خارجی، افزایش آمار صادرات محصولات، رکوردهای مستمر تولید و ... دستاوردهای بسیار بزرگی است که در دوران تحریم در کارنامه پرافتخار ذوبآهن اصفهان ثبت گردید و میراثی ماندگار برای آیندگان به شمار میرود. خوشبختانه ذوبآهن قادر است برای اولین بار در کشور ساخت کامل یک ایستگاه ریختهگری را به عهده بگیرد .