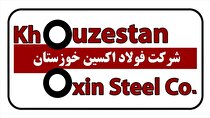
به گزارش می متالز، برای سالها وقتی از آلودگی زیستمحیطی شهربابک سخن گفته میشد انگشتهای اتهام به سمت ذوب خاتونآباد میرفت. تکنولوژی ذوب فلش مجتمع مس شهربابک واقع در خاتونآباد دچار مشکلاتی بود که مدتها گفته میشد برای حلشان تنها راهحل، اجرای طرحهای توسعهای جدید است. کارشناسان داخلی و خارجی میگفتند تنها زمانی میتوان مشکلات ذوب را از میان برداشت و آلودگی را کم کرد که طرحهایی مثل ایجاد کارخانه اسید سولفوریک اجرایی شوند. اما مردان ذوب خاتونآباد به این راهحل اکتفا نکردند، آنها تصمیم گرفتند به توان و دانش خودشان تکیه کنند و مشکلات را از پیش پا بردارند. بهطوریکه میزان آلودگی ذوب فلش خاتونآباد هماکنون در حد استاندارد است و کورۀ فلش این مجموعه نیز با اصلاحاتی که خود پرسنل ذوب خاتونآباد روی آن انجام دادهاند، تولیدش را به بیشترین میزان ممکن رسانده است. این اتفاق چطور افتاد؟ سئوالی که در میزگردی با حضور «علی کریمیفر»، مدیر ذوب خاتونآباد، «پیمان جمالی»، رئیس عملیات، «احمد کرمی»، سرپرست کورۀ فلش و «حسن محمودی»، سرپرست الکتروفیلتر مطرح کردهایم و پاسخ گرفتهایم: «با شکستن تابوی نمیتوانیم».
کریمیفر: در ذوب خاتونآباد، معمولاً تصمیمها و کارها بهصورت تیمی انجام میشود و شخص تصمیمگیرنده نیست؛ تمام افراد همکارِ هم هستند و نظام رئیس و مرئوسی در این مجموعه کار نمیکند. تمام پرسنل اعم از شرکتی، پیمانکاری و... همکارِ هم هستند و همدلی و کار تیمی این افراد با هم، موجب موفقیتهای زیادی شده است.
همانطور که گفتید در چند سال اخیر کارهای بزرگی در این مجموعه انجام شده که یکی از آنها حل مشکلات کورۀ فلش بود. بهدلیل شرایطی که این کوره داشت، دو سال پیش باید تعمیر میشد و این مستلزم این بود که کارخانه یک ماه تا 40 روز تعطیل و تولید متوقف شود، اما با کارهایی که انجام دادیم، همۀ این هزینهها از دوش شرکت برداشته شد.
فعالیت دیگر که خیلی به آن افتخار میکنیم، بهبود وضعیت زیستمحیطی ذوب خاتونآباد است که با همت پرسنل ذوب خاتونآباد و با حمایتهایی که ازسوی مدیریت ارشد مجموعه انجام گرفت؛ توانستیم مشکل زیستمحیطی مجموعه را نیز حل کنیم. جالب است اشاره کنم سالها بود دربارۀ این مشکلات بحث میشد و میگفتیم چون تکنولوژی ما قدیمی است، تحریم وجود دارد و توسعه انجام نشده است؛ بنابراین، تا توسعه صورت نگیرد، مشکلات حل نمیشود، اما پس از مدتی خودمان برای حل مشکلات اقدام کردیم؛ کارگروههای تخصصی تشکیل شد، دستبهدست هم دادیم و با کارهای تخصصی که انجام گرفت، بدون توسعه و نوسازی کوره، مشکلات را تا حد زیادی برطرف کردیم.
این کارها برای ما خیلی ارزشمند بود و دستاوردهایی که داشت، تفکر و دید ما را نسبت به تواناییهایمان تغییر داد و متوجه شدیم چه کارهای بزرگی میتوانیم انجام دهیم؛ کارهایی که در سالهای گذشته همواره میگفتیم امکانپذیر نیست؛ بهطوریکه دو سال قبل قرار بود کورۀ فلش متوقف شود؛ اما الان، به نقطۀ عطف شرکت مس تبدیل شده و این یک اتفاق بزرگ است.
کرمی: ما از دو سال پیش که مسئولیت کورۀ فلش را به عهده گرفتم، با پشتیبانی ریاست عملیات و مدیریت ذوب خاتونآباد کار را شروع کردیم. کار با این پرسشها شروع شد که چرا نباید افزایش تولید داشته باشیم؟ چرا باید از تغییر بترسیم؟ آیا همچنان روند قبل باید ادامه پیدا کند؟ یا اینکه باید در این روند تغییر ایجاد کنیم؟ در پاسخ به این سئوالات و با پشتوانۀ مدیریت ارشد ذوب خاتونآباد، ما این روحیه را پیدا کردیم که از ریسکِ کار نترسیدیم و این موجب شد دست به تغییر بزنیم.
مشکل اول کورۀ فلش این بود که وقتی کنستانتره وارد کوره میشد، بهدلایلی ذوب نمیشد و ذوب نشدن کنستانتره موجب میشد در خروج، به تجهیزات بعدی آسیب برساند؛ ازجمله در بویلر آسیب ایجاد میکرد. مشکل دیگر مسایل زیستمحیطی بود که غبار در الکتروفیلترها خوب جذب نمیشد؛ بنابراین، کار از اینجا آغاز شد که ابتدا باید عیبها را پیدا کنیم.
جمالی: دو سال پیش تصمیم گرفته شد کوره متوقف شود تا دو سال بعد با انجام توسعه، دوباره کارش را از سر بگیرد؛ بنابراین، با خودمان گفتیم وقتی قرار است دو سال صبر کنیم تا توسعه اتفاق بیفتد، چرا همین کوره را تعمیر نکنیم؛ بنابراین، شروع به عیبیابی کردیم و تکتک موارد در کارگروه مورد بررسی قرار گرفت.
الان، کورۀ فلش خاتونآباد در نقاطی نسوز ندارد و در دنیا نادر است کورهای نسوز نداشته باشد و با این ظرفیت کار کند. برای این کار، تکتک آیتمهایی که در تولید و شرایط حفظ کوره تأثیرگذار بود را شناسایی کردیم و پس از آن بهواسطۀ بیلدآپهایی که در دیوارهای کوره نشاندیم، توانستیم از آنها به جای نسوز استفاده کنیم که حدود 80 تا 90 درصد نیاز به نسوز برطرف شد؛ ضمن اینکه دیگر نیازی نبود کوره را متوقف کنیم.
بعد از آنکه نسوز را حفظ کردیم، نگران بودیم نتوانیم شارژ زیاد در کوره بریزیم؛ چراکه امکان داشت کارهایی که انجام داده بودیم، از دست برود، اما اتفاقی که برای کورۀ فلش سرچشمه افتاد و کارهای مهندسی که خود ما انجام داده بودیم، و دینی که شرکت مس بر گردن ما داشت، باعث شد که به فکر افزایش تولید بیفتیم.
مهندس کرمی، که جزء بهترینها در زمینۀ فلش است، به این نتیجه رسید که اگر عیبهای مشعلها را شناسایی کنیم، میتوانیم مشکلات را حل کنیم؛ بهطور مثال سالها زیر مشعلها یکسری بیلدآپ میبست که هیچکس به آنها توجه نمیکرد؛ درصورتیکه اگر آنها را تمیز میکردیم، اتفاقات خیلی بزرگی میافتاد؛ بنابراین، تکتک اشکالاتی که در سیستم وجود داشت را شناسایی کردیم، هر کدام از همکاران با تیمشان یک بخش را به عهده گرفتند و این کار تیمی، معجزه کرد و درنهایت شارژ کردن کوره نیز در دستور کار قرار گرفت و چون مدیریت ارشد هم از ما حمایت میکرد، کار را جلو بردیم و پس از شناسایی ایرادها، شارژ را نیز افزایش دادیم.
جمالی: الان، 46 تن شارژ در کوره میریزیم و این درحالی است که میزان شارژ در سالهای قبل 37 تن بود. در روزهای گذشته روزانه 350 تن آند تولید کردیم که رکوردی غیرقابل پیشبینی بود؛ ماه گذشته نیز نزدیک به 10 هزار و 700 تن آند تولید کردیم؛ درحالیکه دو سال پیش با بهترین شرایط، رکورد تولید آند 9200 تن بود.
لازم است یک موضوع را توضیح دهم؛ خط تولید شامل چند بخش است؛ به این ترتیب که کورۀ فلش کنستانتره را ذوب میکند، بعد در کنورتر مراحل غنیسازی و سپس در واحد ریختهگری محصول نهایی تولید میشود. البته باید عرض کنم در طول انجام این فرایند، تمام واحدهای عملیات، تعمیرات، کنترل فرایند و پشتیبانی در حصول نتیجۀ مطلوب دخیل هستند. وقتی در فلش مشکل داشته باشیم، جاهای دیگر توقف پیدا میکند؛ بنابراین، مهندس کرمی و تیمش، تصمیم گرفتند توقف را به صفر برسانند و موفقیت ما این بود که سیستم پیوسته شروع به کار کرد و توقف در مسیر کار از بین رفت.
معمولاً در کارخانهها، توقف به تولید ضربۀ زیادی میزند و تولید از دست میرود؛ بنابراین، مهندس کرمی و تیمش توقف را به صفر رساندند؛ بهطوریکه در طول ماه فقط حدود چهار ساعت توقف داریم و این توقف هم، برای بازرسی و بازدید از کوره است.
پس از کاهش توقف، واحدهای بعدی که نامشان ذکر شد، با عزمی راسخ تلاش خود را بیشتر کرده و باعث افزایش تولید شدند.
کرمی: پس از اینکه عیبها و گلوگاهها شناسایی شد، درصدد رفع گلوگاهها برآمدیم و به مرور زمان مشکلات برطرف شد؛ بهطور مثال بیلدآپهایی که زیر مشعلها ایجاد میشد، درست تمیزکاری نمیشد و از بین نمیرفت؛ بنابراین، موجب انحراف شعله، انحراف سوخت و انحراف واکنش میشد و وقتی این انحرافها وجود داشت، دهانۀ آبتیک با مشکل مواجه میشد؛ یعنی چون کنستانتره ذوب نشده بود، ذرات به مرور زمان زیر مشعلها مینشستند. در ادامه، مشکل تمیزکاری مشعلها با دورههای آموزشی که برای نیروها گذاشتیم، برطرف شد.
نکتۀ بعدی این بود که ناگزیر 10 درصد از غبار شارژ شدۀ ما هدر میرفت و این 10 درصد غبار، در تنها جایی که مشکل ایجاد میکرد، خاتونآباد بود؛ چراکه تکنولوژیهای مجموعههای دیگر عوض و بهروز شدهاند و ما فقط با مشکل مواجه بودیم. یک پرسش دیگر هم داشتیم و آن اینکه علت چسبندگی غبار چیست و چرا الکتروفیلترها غبار را جذب نمیکند؟ بنابراین، دوباره سراغ مشعلهای کمکی فلش رفتیم.
البته برای حل مشکلات، کارشناسان متعدد خارجی آوردیم، اما هیچکدام پیشنهادی نداشتند و همه میگفتند کارخانه باید بهروزرسانی شود.
در ادامه، به این فکر کردیم که چه کار کنیم چسبندگی ایجاد نشود و غبار به این شکل از دودکشها بیرون نرود. در این رابطه کارگروهی با حضور کارکنان بویلر، الکتروفیلتر و فلش –مجموعهای که درگیر مشکل بود- تشکیل شد و با تجربهای که داشتیم، پس از بررسی مشعلها متوجه شدیم مشکل همین جاست؛ چراکه وقتی مشعلها را از مدار خارج میکردیم، جذب الکتروفیلتر افزایش مییافت و وقتی وارد مدار میشدند، جذب الکتروفیلتر اُفت میکرد که نشان میداد واکنش مشعل خوب انجام نمیشود و احتراق ناقص به سمت بویلر میرود.
با کامل کردن احتراق مشعلها، عملیات سولفاتایزینگ غبار بهتر انجام گرفت، چسبندگی غبار بهشدت کاهش یافت، توانستیم مشکلات بویلر را کاهش دهیم و راندمان الکتروفیلترها نیز بهبود یافت و به عدد 250 میلیگرم در فیلترهای فلاش رسیدیم.
کرمی: خیر، استاندارد هنوز از این رقم پایینتر بود. در ادامه، تغییرات دیگری را اعمال کردیم تا استاندارد به 150 برسد. با کارهای اصلاحی که پرسنل الکتروفیلترها انجام دادند و اکسیژن اضافیای که علاوه بر اکسیژن مورد نیاز فرستادیم، میزان غبار به عدد 170 رسید که به عدد استاندارد بسیار نزدیک است.
برای اصلاح نسوز کوره هم که دو سال پیش باید تعمیر یا حداقل تعمیر گرم و اصلاح میشد نیز، یک کارگروه با حضور پرسنل واحد تعمیرات نسوز، واحد متالورژی و واحد فلاش تشکیل دادیم و پس از بررسی به این پرسش رسیدیم که چرا فقط باید نسوز را عوض کنیم؟ شاید راه دیگری هم وجود داشته باشد تا بهجای اینکه به تعمیر فکر کنیم، کار دیگری انجام دهیم؟
در ادامه، یکسری مشعلها را از مدار خارج کردیم و از بیرون نیز یک سیستم خنککاری برای دیوارهها در نظر گرفتیم و فنهایی نصب شد تا از بیرون سیستم را خنک کنند.
کار دیگر این بود که غبار را پایدار کردیم. قبلاً غبار بهصورت نامنظم شارژ میشد، اما تصمیم گرفتیم غبار بهصورت ثابت به کورۀ فلش شارژ شود تا بیلدآپِ خیلی خوبی روی بدنۀ کوره بنشانیم. باید ضخامت بیلداپ را زیاد میکردیم؛ چراکه بیلداپ، کار آجر نسوز را انجام میدهد و میتواند اثر بهتری نسبت به آجر داشته باشد؛ ضمن اینکه از جنس مگنتیت است و صدمهای به آجر نمیزند؛ بنابراین، این اتفاق موجب شد خیال ما از نبود نسوز هم راحت شود.
کریمیفر: برای پاسخ به این سئوال فقط میتوانیم تولیدی را که از دست میدادیم، بیان کنیم؛ بهطور مثال وقتی یک ماه تولید را از دست میدادیم؛ یعنی حداقل تولید 9000 تن آند را از دست دادهایم که رقم خیلی بالایی است. همچنین حدود یک تا دو میلیارد تومان هزینۀ تخریب کوره، آجرچینی و نسوز مورد نیاز بود که اگر محاسبه شود، شاید حدود 100 میلیارد تومان هزینه بشود که از آن جلوگیری شد. همچنین در شرایطی که شرکت مس به تولید نیاز دارد، با این کار نهتنها سیستم متوقف نشد؛ بلکه تولید هم افزایش یافت.
کریمیفر: بله، دقیقا و خوشحال هستیم. کاری که ما کردیم شاید هیچ کارشناس خبرهای در زمینۀ ذوب نمیتوانست انجام دهد و با همین تجربه و امکاناتی که داشتیم، توانستیم این کار بزرگ را انجام دهیم و به این باور رسیدیم که حتی میتوانیم کارهای بزرگتر را نیز انجام دهیم. شاید پنج سال قبل، این کار برای ما غیرقابل باور بود؛ حتی بهترین کارشناسان دنیا آمدند و گفتند تنها راه برای کاهش آلودگی خاتونآباد توسعه است، اما ثابت کردیم که اینگونه نیست و اکنون کورهای که هیچ آجر نسوزی ندارد، دارد با ظرفیت قابل توجهی تولید میکند و آلودگی آن هم بسیار پایینتر از قبل است.
نکتۀ مهمتر اینکه با دورههای آموزشی که گذاشته شد، تمامی همکاران درک کردند که علت این اقدامات چیست و چون در این مجموعه کار به شکل تیمی انجام میشود؛ همۀ پرسنل درگیر کار شدند و اکنون همه، علت اقدامات را میدانند که بهطور مثال چرا باید تمیزکاری مداوم انجام شود. این کار برای ما مایه افتخار است که توانستیم به مملکت و شرکت مس خدمت کنیم.
کرمی: زمانی که کار تیمی را شروع کردیم، صرفهجوییهای دیگری هم انجام گرفت. وقتی یک مشعل را خاموش میکردیم، از ادامۀ تخریب و صدمه زدن به کوره جلوگیری میکرد که صرفهجویی اقتصادی هم داشت. اکنون، بدون اینکه به سیستم صدمه بزند، دو مشعل خاموش شده و با این اقدام مصرف 200 لیتر بر ساعت مازوت نیز کاهش پیدا کرده و تمام این اقدامات بهواسطۀ همدلی بین کارکنان و مدیران ایجاد شد.
جمالی: و البته شکستن تابوها مهمترین نتیجه است. وقتی چیزی در تفکر ما جا میافتد، میگوییم همین است و دیگر نمیتوانیم، اما وقتی تابو شکست، کارها به خوبی پیش میرود.
مهندس محمودی، معاون ذوب و مهندس کریمیفر نیز، پای این کار ایستادند و به ما انرژی دادند و تمام همکاران این مجموعه، فعلِ خواستن را صرف کردند تا موفق شدیم. اینکه اگر کوره پایین ریخت، دنبال مقصر بگردیم، کنار رفت و گفتیم همه با هم این کار را شروع میکنیم و اگر هم مشکلی پیش آمد، همه با هم پاسخگو خواهیم بود.
جمالی: از زمانی که این کارخانه راهاندازی شد، هیچ آشناییای با الکتروفیلترها وجود نداشت و نمیدانستیم چه اتفاقی در آنها میافتد. پس از اینکه مشکلات مشخص شد، مقرر شد الکتروفیلترها را عوض کنیم که تعویض آنها در سال 86، 18 میلیارد تومان هزینه داشت؛ بنابراین، تصمیم گرفتیم با استفاده از نیروی بومی، سیستم بهبود پیدا کند. در ادامه، 17 نفر نیرو مشغول به کار شدند تا روی الکتروفیلترها مطالعه کنند و عیبیابی انجام گرفت.
این تیم که در حال حاضر مهندس محمودی، سرپرست آن است، در دنیا حرف برای گفتن دارد و اقداماتی که انجام گرفته حتی برای کارشناسان اروپایی هم تعجببرانگیز شده است.
محمودی: ما در سال 88 در قالب یک تیم 17 نفره وارد مس خاتونآباد شدیم و قرار شد مشکلات الکتروفیلترها را برطرف کنیم. آن زمان هیچوقت باور نمیکردم که امروز به اینجا برسیم. خروجی فلش در آن زمان حدود 20 تا 30 هزار میلیگرم بر مترمکعب بود و در درایر، حدود 8 تا 10 هزار میلیگرم بر مترمکعب؛ اگرچه همه میخواستیم شرایطی ایجاد کنیم تا غبار کاهش پیدا کند، اما هیچگاه عددهایی که امروز مشاهده میکنیم، در خواب شب هم نمیدیدیم.
نکتهای که برای من خیلی اهمیت داشت، این بود که به هم اعتماد کردیم و حتی کوچکترین کارها بهصورت تیمی و با تأیید همه انجام میشد. خوشبختانه مدیریت مجموعه هم به من و همکارانم اعتماد کردند و همۀ امکانات را در اختیار ما گذاشتند و درنهایت موفق شدیم.
محمودی: بله، مطمئنا.
حجم و نوع کار برای 18 نفر تیمی که این کار را به عهده گرفته بودند، مهم نبود؛ همه در تمام کارها همکاری میکردیم و هزینهها از صفر تا صد برای ما مهم بود.
آقای مهندس جمالی گفتند که کارشناسان خارجی در این کار متحیر ماندهاند، اما ابتدا وقتی به همکاران میگفتیم این کار را باید انجام دهیم، میگفتند اگر شدنی بود، دانمارکیها و فنلاندیها این کار را انجام میدادند؛ بنابراین، روزهای اول اندکی تنش وجود داشت، اما اعتماد کردند و امروز به این باور رسیدهایم که کار نشد ندارد.
کار را از سال 88 شروع کردیم، یکسری کارهای اصلاحی و یکسری کارهای عملیاتی در سیستم انجام دادیم، برنامۀ تعمیرات و عملیات را تغییر دادیم و آنچه خودمان فکر میکردیم درست است را برنامهریزی کردیم و خوشبختانه خدا هم کمک کرد و موفق شدیم.
محمودی: یکسری کارهای عملیاتی بود که با همکاری مهندس کرمی و واحد فلش انجام شد.
فیلترها، تجهیزات الکترومکانیکی هستند که با برق فشارقوی کار میکنند. یکسری صفحۀ جذب و یکسری الکترودهای دیسشارژ داریم که برق اصلی به الکترودهای دیسشارژ وصل و میدان الکتریکی تشکیل میشود و صفحات جذب نیز ارت زمین هستند. تعدادی ضربهزن هم داریم که با ضربه به صفحات، غبار روی نوارهای زنجیری که کف الکتروفیلتر قرار دارد، ریخته شده و مجدد شارژ کوره میشود.
گاز خروجی کورۀ فلش، داخل بویلر میآید، اُفت دما پیدا میکند و از بویلر، گاز بههمراه مقداری غبار به الکتروفیلتر انتقال پیدا میکند و آنجا وظیفۀ فیلترها این است که غبار را تصفیه و جذب کند تا فقط گاز تنها به محیط وارد شود.
یک قسمت هم فیلتر درایر یا خشککن داریم که خشککن، کنستانتره را خشک میکند؛ بنابراین، گاز بههمراه غباری که از کورۀ خشککن خارج میشود، به فیلتر درایر وارد میشود و آنجا غبار جذب میشود و گاز گرم وارد محیط میشود. ما روی فیلتر درایر، خودسوزی غبار داشتیم که موجب یکسری مشکلات ازجمله تابیدگی صفحات میشد؛ بنابراین، روی اکسیژن و دمای ورودی به سیستم کار کردیم و یکسری پروژههای اصلاحی نیز اجرا کردیم.
یکسری فن به نام فن پرج ایر داشتیم که با یکسری هیتر به هم نصب بودند؛ طرح اصلاحی دادیم که این فنها بهطور کلی حذف شوند. دیروز که با یکی از کارشناسان نصاب این فنها در سرچشمه صحبت میکردم، گفت ما فلان طرح را برای فنهای شما ارایه کردیم، گفتم ما ششماه پیش، فنها را حذف کردهایم.
نکتۀ مهم اینجاست که بهدنبال حذف این فنها در ششماه گذشته، حدود 200 میلیون تومان کاهش هزینۀ انرژی برق داشتیم که در یک سال، به حدود 400 میلیون تومان کاهش انرژی میرسد.
همچنین یکسری سندانهای ضربهزن داشتیم که باید هر ششماه یکبار تعویض میشدند؛ چراکه به هر دلیلی میشکستند و سیستم، اتصال کوتاه میکرد و خروجی بهشدت به عددهای نجومی میرسید.
اتصال ضربهزنها بهوسیلۀ جوشکاری انجام شده بود؛ بنابراین، تعدادی کارشناسان روی جوش قطعات کار کردند، به سازندۀ قطعات نیز نامه ارسال کردیم، اما نتوانست کاری انجام دهد تا اینکه سال 92 بررسی کردیم که چگونه میتوانیم مشکل را حل کنیم؛ بنابراین، طرح فیلتری که FLS دانمارک ساخته بود را بهطور کلی عوض کردیم و اتصالات جوشی را به اتصالات پیچومهره تغییر دادیم. در ادامه، اولین قطعه چهارم اسفند 92 داخل سیستم نصب شد و این قطعه از آن روز تاکنون فعال است؛ ضمن اینکه اورهال ششماهه، به اورهال یکساله تبدیل شده است؛ یعنی قبلاً ششماه یکبار باید تمام قطعات را تعویض میکریم و قطعۀ نو جایگزین میشد، اما اکنون قطعات یکساله تعویض میشوند؛ همچنین قبلاً نیروهای ما باید در طول سال سهبار در دمای 70 تا 80 درجه با ماسک و لباسهای مخصوص قطعهها را تعویض میکردند، اما در آخرین بار، ششماه پیش قطعه عوض شده و الان، این کار 24 ماهه انجام میشود.
از دیگر مزایای این اقدام، این است که شارژ کارخانه متوقف نشده و هزینهها نیز کاهش پیدا کرده است. همچنین عدد الکتروفیلتر درایر کارخانه از 8000 تا 10000 میلیگرم، به 100 میلیگرم کاهش یافته است که کاملاً در حد استاندارد محیط زیست است.
در بهبود وضعیت الکتروفیلترهای فلش نیز، با طرحهای اصلاحی که مهندس کرمی روی کورۀ فلش انجام داد، بیش از 80 درصد به ما کمک کرد و اگر اصلاحات تیم آقای مهندس کرمی نبود، ما به این عدد نمیرسیدیم.
قبل از اینکه این انسجام شکل بگیرد، هر کسی کار خودش را انجام میداد و میگفت مجموعۀ من مشکلی ندارد و مشکل به توسعه برمیگردد، اما وقتی همه عیبها را متوجه شدند و تیم شکل گرفت، نقطۀ بُرد ما بود و درک متقابل از یکدیگر موجب شد در هر نقطهای که مشکل وجود دارد، همه دستبهدست هم دهیم تا مشکل حل شود.
کریمیفر: قرار نیست صنعت عیبی نداشته باشد، عیب و چالش همیشه وجود دارد و این فرهنگ ایجاد شده که وقتی مشکلی وجود دارد، مربوط به تمام واحدهاست و وقتی مشکلی نیست، تمام واحدها بدون مشکل هستند. ایجاد این فرهنگ، نقطۀ عطفی در خاتونآباد است و این همدلی برای ما تجربیات بسیاری بههمراه داشته است. ازجمله تجربیات این بود که بهجای اینکه قطعات الکتروفیلتر را بیرون بریزیم، آنها را سندبلاست کنیم که مهندس محمودی در این رابطه توضیح میدهد.
محمودی: ابتدا از مهندس کرمی، مهندس زارع، سرپرست کورۀ خشککن و مهندس شیبانی، سرپرست بویلر که در زمینۀ فیلترهای فلش و درایر به ما کمک کردند، تشکر میکنم.
در فلش، یکسری اصلاحات انجام دادیم و برای اصلاحات از تکتک نیروها پیشنهاد میگرفتیم. گاهی همکاران کارگری ایدهای به آدم میدهند که هیچگاه متخصص آن رشته نمیتواند آن راهکار را ارایه کند؛ یک روز یک کارگر عزیز گفت که فلانجا قطعات را سندبلاست کردند، اما این کار هنوز در مس انجام نشده بود و یک ریسک محسوب میشد.
تعمیر هر فیلتر فلش، نزدیک به یک میلیارد تومان هزینه دارد؛ علاوه بر آن، تعطیلی 10 روزۀ خط تولید از دیگر عواقب آن است؛ بنابراین، برای اولینبار قطعات را سندبلاست کردیم که بسیار بهتر از تعویض کل فیلترها و تمام تجهیزات آن جواب داد؛ ضمن اینکه هزینۀ یک میلیاردی تعویض، به 60 میلیون تومان، آن هم فقط برای خرید تجهیزات کاهش یافت. همچنین باید هر ششماه یک بار کل تجهیزات را عوض میکردیم، اما با سندبلاست، از سال 92 تجهیزات عوض نشده است؛ بنابراین، حداقل از هزینهکرد سالانه 800 میلیون تومان جلوگیری شده است.
جمالی: یعنی با تفکری که از گفتۀ یک کارگر فنی استفاده کردیم، توانستیم 10 متر صفحه را سندبلاست کنیم که صرفهجویی قالب توجهی را در پی داشته است.
کاری که در الکتروفیلترها نمود پیدا کرد، این بود که مهندس محمودی، خودش ماسک میزد و همراه کارگرانش کار میکرد و به تیمش عشق میداد و این عشق در سازمان وی جاری شد. رساندن عدد 30 هزار به 1000 ساده است، اما برای رساندن 1000 به 100، خیلی باید کار انجام شود و الان اگر عدد الکتروفیلتر درایر از 100 به 120 برسد، همه دنبال میکنند تا مشکل برطرف شود. امیدوارم با همت و تلاش تمام پرسنل و حمایتهای مدیریت ارشد، روزبهروز شاهد بالندگی صنعت کشور باشیم.