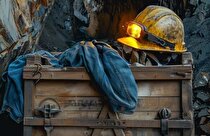
به گزارش می متالز، غلامرضا سلیمی با تشریح اهمیت بومی سازی پودر قالب ریخته گری در شرکت فولاد مبارکه اظهار داشت: مزایای فراوان ریخته گری پیوسته در تولید فولاد سبب شده است که امروزه بیش از 90 درصد از فولاد تولیدی در جهان از این روش تولید شود، اما تولید یک محصول خوب در این روش در کنار جنبه های کیفی و اقتصادی نیازمند ایجاد تمهیدات دیگر است که یکی از این تمهیدات پودر قالب است که با ترک کردن قالب و پوسته فولادی و کاهش انتقال حرارت و روغن کاری پوسته فولادی درحالت انجماد و همچنین ایجاد یک لایه محافظ بر سطح مذاب و جذب ناخالصی های آن نه تنها باعث عملی شدن ریخته گری پیوسته می شود، بلکه با جلوگیری از ایجاد ترک های مختلف و ناصافی در سطح باعث افزایش کیفیت محصول می شود.
وی افزود: امروزه با افزایش نیاز مشتریان به محصولات فولادی بسیار تمیز و قابل ماشین کاری تا ضخامت های بسیار کم از یک طرف و از طرف دیگر نیاز تولیدکنندگان به تولید پیوسته یک محصول بدون عیوب سطحی و زیرسطحی در راستای کاهش هزینه ها؛ این مساله باعث شده که پودر قالب از اهمیت بسزایی برخوردار باشد.
مدیر ناحیه فولادسازی و ریخته گری مداوم شرکت فولاد مبارکه تصریح کرد: امروزه پودر قالب ریخته گری که به اختصار «پودر قالب» هم نامیده می شود براساس فرمولی که شیشه تولید می شود و با درنظر گرفتن پارامترهایی چون دمای ذوب و نحوه تغییرات ویسکوزیته بر حسب دما طراحی شده و انواع آنها بر اساس نوع فولاد و شرایط ریخته گری مورد استفاده قرار می گیرد و
ترکیب شیمیایی فولاد، سرعت ریخته گری، سرعت سرد شدن و بسیاری از پارامترهای دیگر نقش مهمی در تعیین «پودر قالب» به منظور افزایش کیفیت محصولات نهایی ریخته گری بازی می کند.
وی اضافه کرد: در یک مجتمع تولید فولاد به روش ریخته گری مداوم، «پودر قالب» به دلیل نقش مهمی که در تولید یک محصول خوب برعهده دارد از جایگاه ویژه ای برخوردار است. این وظایف عبارتند از محافظت سطح مذاب از اکسیداسیون، ایجاد یک لایه محافظ حرارتی در سطح مذاب برای جلوگیری از انجماد سطح فولاد و جذب ناخالصی های مضر موجود در مذاب مانند اکسید آلومینویم، اکسید تیتانیوم در سرباره، روغنکاری پوسته فولادی تشییع شده در سطح مشترک پوسته فولادی و قالب ایجاد انتقال حرارت یکسان در سطح مشترک پوسته فولادی و قالب که برای تامین هرچه بیشتر این وظایف پودر قالب می بایست در یک محدوده حرارتی مناسب ذوب شده و یک فاز مناسب هم وزن و یک دست ایجاد کند؛ در غیر این صورت به یک توده ای از مواد در سطح توده مذاب فولاد تبدیل خواهد شد.
سلیمی بیان داشت: مذاب تشییع شده از پودر قالب می بایست از ویسکوزیته مناسب جهت اهداف روغن کاری برخوردار باشد، این ویسکوزیته همچنین بر میزان نفوذ پودر قالب بین سطح مشترک پوسته فولاد و قالب تاثیرگذار است. مذاب تشکیل شده از پودر قالب می بایست از توانایی ترک کردن یکنواخت مذاب فولاد را داشته باشد، زمانی که پودر مذاب به عنوان عامل روغن کاری کننده به سطح مشترک پوسته فولاد و قالب نفوذ می کند، نمی بایست تمایلی به تشکیل حلقه های سرباره در محل تماس با دیواره قالب داشته باشد و همچنین مذاب پودر قالب نباید هیچ تمایلی به کریستالیزاسیون مجدد در طی انجماد داشته باشد؛ چرا که این امر خطر پارگی شمش را در تولید محصول در اثر چسبیدن به قالب افزایش می دهد.
وی افزود: عملکرد نامناسب پودر در هر کدام از موارد ذیل شده می تواند باعث ایجاد عیوبی در محصول نهایی و یا پارگی خط و توقف تولید می شود. در واقع پودر قالب به عنوان ماده ای سرامیکی با خواص عایق کاری نسبتا خوب امکان انجماد آهسته و یکنواخت مذاب را فراهم می کند و به این ترتیب از ایجاد عیوبی همچون ترک سطحی و زیرسطحی جلوگیری می کند.
مدیر ناحیه فولادسازی و ریخته گری مداوم شرکت فولاد مبارکه با اشاره به اینکه در این میان عواملی همچون ویسکوزیته مذاب پودر و نحوه جریان یابی آن در فضای بین پوسته فولادی و دیواره قالب دمای کریستالیزاسیون و چگونگی انتقال حرارت نقش بسیار مهمی درتشکیل یا عدم تشکیل عیوب محصول بازی می کند، گفت: عایق کاری حرارتی مناسب و کنترل ضخامت فولادی مناسب می تواند از تشکیل ترک های طولی اجتناب کند و ترک های طولی بیشتر در فولادهای کربن متوسط حاوی فازهای مختلفی از جمله فازهای آستنیتی و سمتنتیتی خود را نشان می دهد.
وی افزود: نقش «پودر قالب» در کاهش این عیب از طریق کنترل انتقال حرارت بسیار مهم است. از دیگر عیوب رایج در محصولات فولادی عیب اثر اسیلاتو است. این عیب فرو رفتگی های افقی هستند که در فواصل منظم در امتداد سطح پوسته فولادی رخ می دهد. دلیل تشکیل اثر اسیلاتو نوسان های قالب است که باعث نوسان های قالب است که باعث حرکت پوسته فولادی به بالا و پایین و شکل گیری شکاف در سطح پوسته می شود.
سلیمی گفت: با عایق کاری مناسب به کمک «پودر قالب» می توان عمق این شکاف ها را پر کرد و یا حتی به نحوی از تشکیل آنها جلوگیری کرد. ازطرف دیگر سرد شدن و انجماد غیریکنواخت پوسته فولادی باعث تشکیل فرورفتگی های طولی در پوسته خواهد شد که انتقال حرارت یکنواخت ناشی از عملکرد مناسب پودر می تواند از بروز آن جلوگیری کند.
وی اضافه کرد: یکی دیگر از عیوب رایج در ریخته گری پیوسته چسبیدن پوسته فولادی در نقاطی به دیواره قالب است در وقوع این عیب رابطه مستقیمی با عملکرد پودر قالب دارد، به گونه ای که افزایش میزان انتقال حرارت و کاهش دمای سطح پوسته فولادی باعث کاهش این عیب می شود. علاوه بر این روان سازی و روغن کاری مناسب پودر قالب نقش اساسی برای جلوگیری از چسبندگی ایفا می کند.
مدیر ناحیه فولادسازی و ریخته گری مداوم شرکت فولاد مبارکه با اشاره به یکی دیگر از وظایف «پودر قالب» که روغن کاری سطح است، گفت: درواقع از مهمترین دلایل استفاده از پودر در فرایند ریخته گری پیوسته روغن کاری آن است و برای رسیدن به شرایط مناسب روغن کاری باید ویسکوزیته را به نحوی طراحی کرد که مذاب پودر همواره در مسیر انجماد در جریان باشد؛ در صورتی که ویسکوزیته بالا باشد طبیعی است که مذاب پودر جریان یابی خوبی بین دیواره قالب و پوسته فولادی نخواهد داشت و در نتیجه عیوب متعددی به وجود خواهد آورد. در نتیجه طراحی ویسکوزیته پودر قالب نیز از اهمیت بسزایی در جلوگیری از تشکیل عیوب در ریخته گری پیوسته دارد و باید با توجه به شرایط کاری و تجهیزاتی از مقدار بهینه ای برخوردار باشد.
وی افزود: علاوه بر تمامی پارامترهای ذکر شده کریستالیزاسیون و شیشه ای شدن لایه مذاب «پودر قالب» هم در فضای بین پوسته و دیواره قالب نیز به دلیل تاثیر بر میزان انتقال حرارت و پارامتر های روغن کاری و در نتیجه تشکیل عیوب بسیار مهم در ریخته گری پیوسته برخوردار است. عامل مهم در کنترل کریستالیزاسیون «پودر قالب» واسیزیته پودر است، به گونه ای که با افزایش این نسبت میزان کریستالیزاسیون افزایش می یابد و در نتیجه عامل موثری جهت کنترل کریستالیزاسیون پودر خواهد بود.
وی افزود: در شرکت فولاد مبارکه در حال حاضر 7 میلیون تن تختال در گریدهای مختلف فوق کم کربن، کم کربن، کربن متوسط و کربن بالا تولید می شود که بیش از 4 هزار تن پودر قالب در گریدهای مختلف مصرف می شود.
سلیمی به این مهم که در سالهای گذشته «پودر قالب» از شرکت های خارجی تامین می شد، اشاره کرد و گفت: با توجه به اینکه کنترل و کیفیت پودر، در دسترس بودن تامین کننده و عدم نگرانی دربحث تامین «پودر قالب» مهم است؛ پروژه ای در زمینه بومی سازی گریدهای مختلف پودر قالب با توجه به تنوع گریدهای فولادی تولیدی درمجتمع فولاد مبارکه تعریف و با همکاری دو شرکت دانش بنیان پروژه مذکور اغاز شد.
وی افزود: با استفاده از دانش و تجربیات متخصصان فولاد مبارکه این دو شرکت دانش بنیان موفق به تولید پودر قالب شدند که پس از طی کردن آزمایشات مختلف پودر تولیدی و اخذ تاییدهای لازم از نظر خواص فیزیکی و شیمیایی پودرهای بومی سازی شده جایگزین پودرهای خارجی در مجتمع فولاد شد و در حال حاضر بیش از 80 درصد از مصرف «پودر قالب» در فولاد مبارکه از پودرهای قالب بومی سازی شده است که با توجه به کیفیت بالای پودرهای قالبی تولید در داخل، در آینده پودرهای داخلی به طور صددرصد جایگزین پودرهای خارجی می شود.
مدیر ناحیه فولادسازی و ریخته گری مداوم شرکت فولاد مبارکه بیان داشت: با توجه به اینکه گریدهای مختلف فولادی در شرکت فولاد مبارکه گسترش می یابد و این واحد صنعتی به سمت تولید گریدهای خاص برای مصارف خاص از جمله گریدهای مورد نیاز صنایع نفت و گاز خودرو می رود؛ نیاز به تولید پودرهای قالب مخصوص جهت تولید گریدهای فولاد ویژه است که شرکت های دانش بنیان این توانایی را خواهند داشت که بتوانند گریدهای مخصوص را تولید کنند.