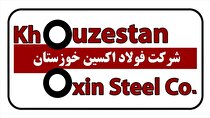
به گزارش می متالز به نقل از عصر مس آنلاین، نبض صنعت مس در کارخانجات تغلیظ میتپد. در کارخانجات تغلیظ است که سنگ معدن با پشت سر گذاشتن مراحل پُرعیارکنی تبدیل به محصولی با مشتریان جهانی میشود. به همین دلیل است که هر اتفاقی که در این کارخانجات بیفتد تولید را مستقیماً متأثر میکند. در فازهای یک و دو تغلیظ مجتمع مس سرچشمه در سالهای اخیر اتفاقاتی افتاده که افزایش تولید و صرفهجویی در مصرف انرژی الکتریکی را به همراه داشته است. «غلامرضا لنگریزاده»، مدیر امور تغلیظ مجتمع مس سرچشمه از این اقدامات با عنوان «تعمیرات خط متوقف سالانه» یاد میکند. به گفته لنگریزاده در جریان این تعمیرات بسیاری از قطعات مورد نیاز کارخانجات تغلیظ بومیسازی شدهاند.
با توجه به شرایط کارخانه سرچشمه من عنوان «تعمیرات خط متوقف سالانه» را برای اقدامات انجامشده بیشتر از «اورهال» میپسندم؛ چراکه تعریف اورهال در دنیا این است که یک دستگاه در حال کار را خاموش کنیم تا تعدادی قطعه تعویض شود. درصورتیکه در کارخانجات تغلیظ مجتمع مس سرچشمه، اگر نیاز به تعویض قطعهای باشد با توجه به وجود تجهیزات موازی این کار را در تعمیرات پیشگیرانه برنامهریزیشده در طول سال انجام میدهیم. با این حال، ما در سه کارخانه موجود، مشترکاتی داریم که برای اصلاح و تعمیر این موارد مجبور هستیم کل خط را سالانه 10 تا 15 روز متوقف کنیم. ازسوی دیگر، از آنجا که تقریباً پنج درصد مصرف انرژی در دنیا و دو سوم مصرف انرژی کارخانههای فرآوری مس مربوط به خردایش است، با خاموش کردن این بخش در زمان انجام اورهال میتوانیم به میزان قابلتوجهی صرفهجویی در مصرف انرژی داشته باشیم. نکته دیگر این است که امور تغلیظ مجتمع مس سرچشمه پیش از این اورهال را در بازه زمانی اردیبهشت تا بهمن انجام میداد؛ اما در چند سال اخیر این کار را از 15 تیرماه تا 15 شهریور انجام میدهد که همین تغییر زمانی باعث شده با توجه به پیک مصرف برق در کشور در این بازه زمانی به دستاوردهای خوبی در زمینه هزینههای مصرف انرژی برسیم. امسال هم به همان منوال تعمیرات سالانه را انجام خواهیم داد و از هماکنون برنامهریزی برای اورهال، در حال انجام است. هدف ما از برنامهریزی این است که با انجام کارها بهصورت موازی باعث کوتاهتر شدن طول دوره اورهال بشویم؛ مثلاً سال گذشته لاینرهای دو آسیاب خودشکن را همزمان با هم در دوره اورهال تعویض کردیم که قبلاً این کار انجام نمیشد و باعث کوتاهتر شدن زمان اورهال شد. از طرف دیگر لاینرهای کارخانه دو بار در سال باید عوض بشوند؛ اما این برنامهریزی طوری انجام شد تا یکبار از این دو بار در اورهال تابستانه که تمام دستگاهها خاموش میشوند، انجام شود. همه اینها بهنوعی کوتاه کردن زمان با یک برنامهریزی درست است که با این برنامهریزیهای درست کارهای زیادی در زمینه نوسازی انجام دادهایم.
رویکرد امور تغلیظ در زمینه استفاده از قطعات بومی و ساخت داخلی دستگاهها و قطعات از دهه 1370 شروع شد. در سال 1374 این امور به سمت قطعاتی که امکان ساخت آنها در داخل وجود داشت رفت و الآن کل قطعات مکانیکی، ضد سایش و محورهای کارخانه و حتی بعضی از موتورها که امکان ساخت داخلی را دارند در داخل تولید میشود. قطعات خارجی مورد استفاده در کارخانه تغلیظ بسیار محدود و در حد قطعات خیلی خاص ابزار دقیق و کنترل هستند که استفاده از آنها نیز به دلیل این است که ساخت بعضی از این قطعات برای ما صرفه اقتصادی ندارند چون نمیتوان برای ساختن یک یا دو عدد از یک قطعه خط تولید آن را راهاندازی کنیم.
برنامه امسال امور تغلیظ مجتمع مس سرچشمه تولید 28 میلیون و 500 هزار تن سنگ معدن و تولید حدود 660 هزار تن کنسانتره مس و حدود 6000 تن کنسانتره مولیبدن هست.
همانطور که میدانید تمام معادن مس دنیا با این چالش مواجه هستند؛ یعنی با افزایش عمر معادن، عیار مس پایین میآید. بنابراین برای جبران کاهش تولید مس محتوی معمولاً شرکتهای دنیا دست به توسعه میزنند. شرکت ملی صنایع مس ایران هم در این زمینه دست به اقدام زده است. اما در رابطه با افزایش کیفیت کنسانتره مس، من معتقدم اگر بخواهیم یک تولید باکیفیت داشته باشیم باید یک کارخانه سالم داشته باشیم. این در حالی است که کارخانه تغلیظ فاز صفر ما که به تغلیظ یک هم معروف است حدود 35 سال از شروع به کارش میگذرد. به همین دلیل ما در 5 سال گذشته یک روند نوسازی را شروع کردیم تا بدون عقب ماندن از برنامه تولید، تکتک بخشهای کارخانه را بازسازی کنیم؛ بهطوریکه در سالهای 92، 93 و 94 همواره یک ردیف از سلولهای کارخانه ( 12.5 درصد ظرفیت فاز صفر) در حال بازسازی بوده؛ اما تولید بههیچوجه کاهش نداشته است و برای تحقق این هدف دسترسی به بقیه تجهیزات را افزایش دادهایم.
بهعنوانمثال در سال 1380 معمولاً امور تغلیظ 6 یا نهایتاً 7 آسیا بیشتر در خط نداشت؛ اما در سال گذشته ما 7.34 آسیای در حال کار داشتیم که باعث شده آمادهبهکاری تجهیزات از 85 درصد به 92درصد افزایش یابد؛ بنابراین توانستیم افزایش ظرفیت را با بهبود شرایط برنامهریزی تعمیرات و انجام تعمیرات بهموقع محقق کنیم که باعث افزایش تولید هم شده است. همانطور که میدانید امور تغلیظ در فاز صفر، یک و دو کارخانه تغلیظ دارد که بالای ظرفیت اسمی کار میکند و این کار وقتی ارزش دارد که ما فشار مضاعف به تجهیزات نیاوریم و این زمانی عملی میشود که دسترسی تجهیزاتی ما بیشتر شود. خوشبختانه در سالهای گذشته با فعال کردن واحد برنامهریزی امور، واحد پایش وضعیت و واحد قابلیت اطمینان توانستهایم میزان دسترسی به تجهیزات را افزایش دهیم و تولید را هم بالای ظرفیت اسمی ببریم.
برنامه امور تغلیظ این بود که تا اواسط سال 95، تجهیزات اصلی در کارخانه تغلیظ نوسازی شود که این اتفاق افتاد و بازسازی و نوسازی انجام شد. از آن زمان به بعد تلاش کردیم تا کیفیت کار را بهبود ببخشیم که با کمک امور تحقیقوتوسعه و یک شرکت دانشبنیان طرحی آغاز شد که به بهینهسازی فرآیندها معروف است؛ در این طرح سعی کردهایم فرایندهای عملیاتی را استاندارد کنیم؛ اما این طرح بهرغم اینکه به هدفمند کردن فرآیند نوسازی و بازسازی کمک میکند، نقشی در بازسازی و نوسازی فیزیکی تجهیزات ندارد.
شاخصترین این بومیسازیها، لاینرهای آسیای سگمیل (نیمه خودشکن) بود. امور تغلیظ در سال 1384 با چالش شکست لاینرهای آسیای نیمه خودشکن مواجه شد. راهحلهای پیشنهادی برای حل مشکل از طرف شرکت خارجی طراح، کاهش قطر گلوله بود که درنهایت کاهش ظرفیت را در پی داشت. اما ما به سمت بومیسازی رفتیم و با همکاری واحد تحقیقوتوسعه و دانشگاه کرمان، شکل لاینرها تغییر کرد و جنس لاینرها بهبود یافت. درنهایت با چند شرکت ایرانی شروع به کار کردیم و توانستیم قطعهای به سنگینی دو تُن را بهرغم اینکه ساخت آن با توجه بهسختی، میزان سایش و مقاومت به شکست دارای پیچیدگیهای زیادی بود، بومیسازی و تولید کنیم. با چنین اقدامی امروز امور تغلیظ با لاینرهای آسیای سگمیل ایرانی با کیفیت خوب و قیمت مناسب کار میکند.
از طرف دیگر با بررسیهایی که در قسمت متالورژی انجام گرفته بود، به این نتیجه رسیدیم که در کل دنیا برای افزایش ظرفیت با تعویض لاینرها، لاینرهای با شکل قبلی بسته نمیشود و با توجه به شرایط عملیات شکل لاینرها عوض میشود. بنابراین ما نیز این کار را انجام دادیم و از سال 1393 شروع به تغییر شکل لاینرها با شبیهسازی عملکرد کردیم که هر بار با تعویض تعدادی لاینر تغییری در جهت افزایش ظرفیت و بازدهی آن انجام میشود و هنوز هم این کار متوقف نشده است. این لاینرها با کمک فنی امور تغلیظ در شرکتهای ایرانی که در اصفهان و ساری هستند ساخته میشوند و البته با یک شرکت کرمانی هم تعامل و همکاری را شروع کردهایم.
بسیار مشتاق هستیم که این کار را انجام دهیم؛ اما مشکلی که در این زمینه وجود دارد بحث سرمایهگذاری است که در حال حاضر کمرنگ است. با توجه به اینکه تغلیظ یک تکنولوژی بومیسازیشده ایرانی است، اگر شرکتها و سرمایهگذارها به سمت سرمایهگذاری در کرمان بیایند امور تغلیظ حتماً از آنها استفاده میکند. تلاشهایی هم در این زمینه ازسوی شرکتهای خصوصی انجام شده است که امیدواریم به ثمر بنشیند.
یک نکته که باید به آن توجه داشت این است که سنگ موجود در معدن رو به سختتر شدن است و لاجرم با این اتفاق باید افزایش مصرف گلوله در کارخانه تغلیظ داشته باشیم. اما این اتفاق نیفتاده است. زیرا با توجه به تغییراتی که در شرایط آسیا و لاینرها دادیم بهرغم سخت شدن سنگ تغییری در مصرف گلوله نداشتهایم و در سال گذشته حدود 3 درصد کاهش مصرف گلوله هم داشتیم. بهعلاوه در زمینه این گلولهها یک پروژه تحقیقاتی بزرگ از سال 1379 شروع شد تا ببینیم آیا گلوله مورد استفاده ما در کارخانه تغلیظ درست است یا خیر؟ نتیجه این پروژه درنهایت منجر به تعویض اندازه گلوله در تغلیظ یک و بهینه شدن آن در تغلیظ دو شد. الان با توجه به سایز و شرایط گلوله، مصرف گلوله تقریباً با سخت شدن سنگ، ثابت مانده است.