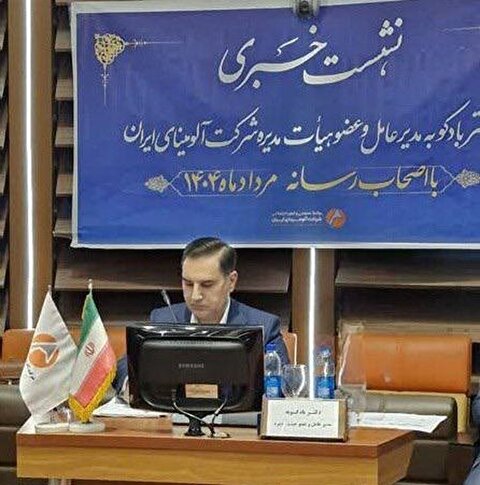
استحکام کششی آن در حالت خالص تقریبا ۴۹ Mpa و در حالت آلیاژی تا ۴۰۰ Mpa نیز می رسد. چگالی آن تقریبا یک سوم چگالی آهن است و داکتیل و چکش خواری بالایی دارد و به راحتی ریخته گری یا ماشینکاری می شود. به دلیل وجود اکسید آلومینیوم بر روی سطح آن، مقاومت خوردگی و ماندگاری بسیار بالایی دارد. این فلز رسانایی بسیار خوبی برای حرارت و گرما است.
چینی ها تقریبا از سال ۳۰۰ قبل از میلاد از آلومینیوم استفاده می کردند. در سال ۱۷۶۱ میلادی گیتون موروی (Guyton de Morveau) پیشنهاد کرد که فلز پایه آلوم را آلومین نام گذاری نمایند. در سال ۱۸۰۸ همفری دیوی(Humphry Davy) این فلز را شناسایی نمود و آن را ابتدا آلومیوم(Alumium) و سپس آلومینیوم(Aluminum) نام نهاد.
فریدریش وهلر (Friedrich Wohler) از طریق مخلوط کردن کلرید آلومینیوم بی آب با پتاسیوم در سال ۱۸۲۷ توانست آلومینوم را جدا نماید. البته دو سال بعد توسط شیمیدان و فیزیکدان دانمارکی به نام هانس کریستین اورستد(Hans Christian Orsted) آلومینوم به شکل ناخالص تولید شد. از این رو از وی به عنوان اولین کسی که توانست آلومینیوم را کشف نماید یاد می شود. روش وهلر در سال ۱۸۴۶ توسط دانشمند فرانسوی به نام هنری دویل (Henri Saint Claire Deville) اصلاح یافت و در این روش بهبود، سدیم جایگزین پتاسیمی گردید که بسیار گران بود.
در سال ۱۸۸۶ مقاله ای توسط چارلز مارتین هال (Charles Martin Hall) منتشر شد که در آن فرآیند الکترولیتی برای استخراج آلومینیوم توضیح داده شده بود که مشابه با روشی بود که همزمان توسط پاول هرولت (Pault Heroult) در اروپا ارایه شده بود. این روش که بنام روش هال-هرولت نامیده می شود، سبب شد که روش استخراج آلومینیوم از کانی ها بسیار ارزان شده که هنوز هم از روش های اصلی برای استخراج آلومینیوم در سراسر دنیا محسوب می شود. البته یادآوری این نکته مهم است که با این روش استحصال آلومینیوم بسیار خالص ممکن نیست.
این عنصردر فولاد سازی، اکسیژن زدایی بسیار قوی بوده، پایدار کننده نیتروژن و اصلاح کننده اندازه دانه است. برای این منظور درصد آلومینیوم کمتری نیاز است. آلومینیوم باعث پایداری فاز فریت در ریزساختار می شود. در درصدهای حدود ۱%، فاز فریت بطور کامل پایدار می شود.
به دلیل ماهیت فیزیکی و شیمیایی این عنصر در ترکیب با اکسیژن، فیلم سطحی بسیار محکم اکسید آلومینیوم در سطح تشکیل می دهد که مقاومت خوردگی سطحی را افزایش می دهد. اگر در نقطه ای این فیلم آسیب بیند، دوباره آن سطح اکسیدشده و فیلم اکسیدی تازه ای بر روی آن تشکیل می شود. ضخامت اکسیدی در حدود nm ۱۰ و بالاتر است. این خاصیت را توانایی حفاظت از خود (Self-protective capability) می گویند.
البته برای بهبود مقاومت خوردگی بیشتر از کروم به میزان ۱۰% و بالاتر استفاده می کنند ولی این عنصر گران است و مقرون به صرفه نیست. افزودن آلومینیوم به ترکیب فولاد تاثیرات نامطلوب ناخواسته دیگری نیز در پی دارد. آنچه که باید در نظر گرفت این است که قبل از اینکه مقاومت خوردگی را بیافزاید، فریت زا است. قابلیت انحلال آلومینیوم در فریت تقریبا ۳۵% است که در درصدهای بالا، تمایل به تشکیل محلول جامد با درجه نظم بالا (Fe۳Al) زیاد می شود. اگر استحاله برگشت پذیر آلفا به گاما وجود نداشته باشد، مشکل بزرگ شدن دانه ها وجود خواهد داشت بنابراین محدودیت هایی در چقرمگی و داکتیلتی بوجود می آید.
آلومینیوم تاثیر عالی بر روی مقاومت در برابر پیرکرنشی داشته و به علت تشکیل ذرات سخت نیترید آلومینیوم، بیشتر به عنوان عنصر آلیاژی در فولادهای نیتروره شونده بکار می رود. در فولادهای رسوب سختی شونده، با تشکیل ترکیبات بین فلزی، استحکام در شرایط پیر شده را افزایش می دهد.
قابلیت انحلال آلومینوم در گاما و آلفا به ترتیب ۱.۱ و ۳۵% است که با افزایش درصد کربن در فولاد، درصد انحلال در گاما افزایش می یابد. آلومینیوم با تشکیل محلول جامد، استحکام فریت را زیاد کرده و اگر در گاما حل شود، سختی پذیری را تا حد متوسطی افزایش می دهد. از طرفی تمایل چندانی به تشکیل کاربید ندارد ولی به عنوان گرافیت زا عمل می کند.
در بین عناصر آلیاژی کنترل کننده اندازه دانه آستنیتی، آلومینیوم بیشترین تاثیر را دارد. آخرین تئوری که این عملکرد آلومینوم را توضیح می دهد این است که آلومینیوم با تشکیل نیترید آلومینوم مانعی در برابر حرکت مرزدانه های آستنیت تشکیل می دهد. فولادهای کربنی ساده حاوی آلومینیوم مقاومت پیرکرنشی بالایی داشته و استحکام ضربه اشان بهبود می یابد. از طرفی بدلیل یکنواختی ساختارشان، قابلیت ماشینکاری آنها اصلاح می شود.
اکسیژن زدایی با آلومینیوم تاثیر بسیار زیادی بر اندازه، شکل و توزیع آخالهای سولفیدی دارد. در مطالعه تاثیرات آلومینیوم، این نکته حاصل شد که در صورت کافی نبودن درصد آلومینیوم برای اکسیژن زدایی، آخالهای سولفیدی بصورت اشکال کروی با اندازه های متفاوت و توزیع تصادفی در می آیند که تیپ یک را تشکیل می دهند. اگر فولادها بطور کامل با آلومینیوم اکسیژن زدایی شده باشند ولی درصد اضافی از این عنصر در ترکیب فولاد موجود نباشد، در این حالت شکل آخالها کره های بسیار ریز با شکل یوتکتیکی بوده که در مرزدانه های اولیه قرار می گیرند (تیپ دو). تیپ سه در صورتی بدست می آید که اولاً فولاد بطور کامل اکسیژن زدایی شده و از طرف دیگر درصدی از این عنصر در ترکیب وجود داشته باشد. در این حالت، شکل آخالها کروی درشت و حجیم با توزیع تصادفی خواهد بود.
کمترین داکتیلیتی در تیپ دو بدست می آید که بدترین حالت می باشد. در حالیکه بهترین حالت و بالاترین داکتیلیتی در تیپ یک بدست می آید. مقدار آلومینیوم در تیپ یک در محدوده ۰.۰۱۵-۰.۰۲۵% و درصد آن در تیپ سه برابر ۰.۰۱۰% می باشد.
در نیتریداسیون فولادهای غیرآلیاژی، نیتریدهای آهن (Fe۴N,Fe۲N) تشکیل می شود که بسیار نرم هستند و سختی آنها کمتر از ۲۰۰ HB خواهد بود. در فولادهای نیتروآلوی، نیتریدهای آلومینیوم و کروم بسیار پایدار بوده و لایه سطحی سختی بالایی خواهند داشت ولی ضخامت این لایه چندان بالا نیست (۰.۰۰۴ in) در فولادهایی که دارای ۱% Al می باشند، نیتریدهای آهن بسیار ترد در سطح تشکیل می شوند بنابراین در این گونه موارد برای جلوگیری از پوسته شدن در حین کار، بهتر است سطح به میزان ۰.۰۰۱ in سنگ زنی شود.
آلیاژهای مغناطیس نیکل- آلومینیوم دارای ۶-۱۳% آلومینیوم می باشند. این در حالی است که استحاله مارتنزیتی با ایجاد تنش های داخلی، خواص مغناطیسی به فولادهای مغناطیس معمولی می دهد. در این آلیاژها سخت گردانی مغناطیسی با مکانیسم رسوب ایجاد می شود. آلیاژ مغناطیس دایم Alni دارای ۳.۵% Cu۲۴% ، Ni۱۳% ،Al است. آلیاژ با نرخ بحرانی از دمای انحلال سرد می شود و در طی سرد کردن در محدوده ۱۲۰۰-۸۰۰ درجه سانتیگراد غیرمغناطیس بوده و فازهای با توزیع ریز رسوب می کند. تنش های داخلی در طی سرد شدن اشاعه یافته و توزیع رسوب پراکنده شرایط خوبی را برای خواص مغناطیس دایمی فراهم می آورد.
آلیاژهای مغناطیس دایم که دارای آلومینیوم هستند، بیشترین HB در مقایسه با مغناطیس های حاوی کبالت و تنگستن معمولی دارند از جمله Alnico,Alomax,Ticonal,Hycomax.
آلومینیوم به همراه تیتانیوم به ترکیب برخی از آلیاژهای پایه نیکلی که دردماهای بالا بکار می روند، اضافه می شود تا تشکیل رسوبات پراکنده در دماهای پایین را تسهیل دهد. این رسوبات ترکیبات نیکل- آلومینیوم-تیتانیوم هستند. آلیاژ Nimonic با این مکانیسم سخت گردانی می شود و امکان دارد که در دمای ۷۰۰ درجه سانتیگراد رسوب سختی شود. در شرایط عملیات حرارتی شده، این آلیاژ نسبت استحکام به وزن خوب، تنش شکست خوب در دماهای بالا و مقاومت خزشی قابل قبول داشته و در موتورهای هواپیماهای مدرن که در معرض دماهای بسیار بالا هستند، کاربرد دارند.
در آلیاژ Nitralloy N آلومینیوم بدو منظور گسترش رسوب سختی و نیز تاثیر آن در نیتریداسیون وجود دارد. بعد از نیتریداسیون، یک سطح سخت معمولی تشکیل می شود ولی در همان زمان مرکز قطعه به اندازه ۱۵-۲۰ ton/in۲ بدلیل فرآیند رسوب سختی استحکام گردانی می شود.
آلومینیوم می تواند در مواد ۱۸/۸ تاثیر بسزایی در رسوب سختی آنها داشته باشد. در چنین مواردی ۱% Al اضافه می شود. با این درصد آلومینیوم، مقدار مشخصی از فریت دلتا در ریزساختار تشکیل می شود که کارپذیری گرم را تا حد زیادی کاهش می دهد. از آلیاژهای این نوع می توان به ۱۷/۷ PH و ۱۵/۵ PH اشاره کرد. مواد PH (رسوب سختی شونده) این مزیت را در مقایسه با فولادهای سخت شونده عادی دارند که مکانیسم رسوب تحت تاثیر اثرات اندازه دانه نبوده و در کل مقطع می توان به سخت گردانی یکنواختی دست یافت.
مقاومت اکسیداسیون آلیاژهای کروم-آهن در دماهای بالا با افزودن آلومینیوم بهتر می شود. آلیاژ Fe-۲۰%Cr-۵%Al مقاومت (Resistivity) در حدود یک پنجم برابر بیشتر از مواد کروم-نیکل معمولی دارد. اگر مقدار آلومینیوم این آلیاژ تا ۱۰% بیشتر شود، مقاومت آن دو برابر مواد کروم – نیکل می شود.
چدنها با آلومینیوم تا ۲% می توانند بصورت افزودنی جامد، آلیاژی شوند. ولی اگر بخواهیم درصد آلومینیوم بیشتر از این مقدار باشد باید دو ذوب با هم مخلوط شوند. فیلم اکسیدی محکمی بر روی ذوب تشکیل می شود که اگر در ریخته گری دقت لازم نشود، افت خواص مکانیکی و ریخته گری را در پی خواهد داشت.
در چدنها، آلومینیوم تا ۴% گرافیت زایی را افزایش می دهد. از ۴-۱۰% Al کاربید یوتکتیــک پایدار می شـود و بین ۱۰-۱۸% Al کاربید ها دیگر غالب هستند. بین ۱۸-۲۴% Al گرافیت زایی مجدداً اتفاق افتاده و با افزایش درصد آن، گرافیت زایی ارتقاء می یابد و در ۲۴% Al کل کربن بصورت گرافیت در می آید. با افزایش درصد آلومینیوم پایداری کاربید نیز بیشتر می شود و در ۲۹% Al هیچ گونه گرافیتی در ریزساختار دیده نمی شود.
چدنهای با آلومینیوم بالا، مقاومت خوبی در برابر رشد دانه و پوسته برداری Scalling دارند. در درصدهای بالای ۳، پوسته برداری یک دفعه کاهش می یابد. در کمتر این مقدار تاثیر چندانی بر رشد ندارد ولی در درصدهای بالاتر از آن، با افزایش درصد آلومینیوم مقدار آن شدیداً کاهش می یابد و در محدوده ۸-۲۰% به یک مقدار مینیموم می رسد که در آن گرافیتی وجود ندارد و یا اگر وجود داشته باشد خیلی کم است. آلیاژی بنام Crafler بهترین مقاومت در برابر رشد و پوسته برداری دردماهای بالاتر از ۱۰۰۰ درجه سانتیگراد را دارد و در ترکیب آن ۷-۷.۵% Al و ۰.۷۵% Cr می توان یافت.
آلومینیوم در ترکیب فروسیلیس ها و یا سایر فروآلیاژهای حاوی سیلیس وجود دارد و اگر بخواهیم جوانه زنی بنحو احسن انجام شود، بهتر است درصد آلومینیوم در این آلیاژهای بیشتر از ۱% باشد.
افزودن ۰.۰۲%Al به ترکیب چدن مالیبل، جوانه زنی کروی را بیشتر کرده و بدلیل احتمال ترکیب آن با نیتروژن، مالیبلیزاسیون را تسهیل می سازد.