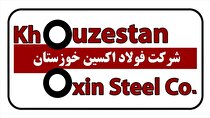
به گزارش میمتالز، بر همین اساس تعریف و اجرای پروژه «بهینهسازی فرآیند احتراق کوره آهک شماره یک و دو بخش اگلومراسیون» به عنوان یک پروژه منحصر به فرد و نوآورانه، در راستای پروژههای محیط زیستی کارخانه و ذیل طرحهای در دست اقدام واحد اکولوژی مدیریت هماهنگی امور مهندسی و نظارت و با همکاری واحد پخت آهک مدیریت آگلومراسیون صورت پذیرفت که در درجه اول به منظور رفع مغایرت گاز و غبار خروجی کوره و تطبیق پارامترهای مختلف بهره برداری (گاز و غبار) آن با ظرفیت سیستم غبارگیر موجود (ESP and Cyclone) تعریف گردید و اهدافی از جمله کاهش و بهینه سازی مصارف انرژی حرارتی وذالکتریکی خط تولید نیز برای آن تعریف گردید.
در همین راستا پس از ممیزی فنی مجموعه خط تولید کورههای آهک شماره ۱ و ۲ و پیرو جلسات فنی مشترک با مدیریتهای مختلف و ذی ربط، اجرای آن برای کوره آهک شماره ۲ طی ۶ ماه (از خردادماه تا آذرماه ۱۴۰۰) و پس از کسب تجارب موفقیت آمیز از این پروژه، در بهار ۱۴۰۱ نیز برای کوره آهک شماره یک طی ۶ ماه از اردیبهشت تا آبان ۱۴۰۱ به انجام رسید.
در چارچوب ممیزی فنی خط تولید از منظر فرآیندی و باتوجه به اندازه گیری و پایش پارامترهای فرآیندی کوره آهک و تطبیق شرایط فعلی (Actual) با طراحی اولیه کارخانه (Design)، مشخص گردید راندمان احتراق مشعل افت محسوسی داشته و مصرف سوخت به ازاء هر کیلوگرم محصول تولیدی، بسیار بالاست که ضمن تحمیل زیان مالی به کارخانه، ازعوامل انتشار آلودگی نیز میباشد. به نحوی که راندمان پایین مشعل کوره علاوه بر مصرف سوخت بیشتر، باعث افزایش حجم هوای مازاد درکوره شده و به تبع آن افزایش سرعت و دبی گاز در سیستم غبارگیری (ESP and Cyclone) را به دنبال دارد. به طوری که گازهای حاصل از احتراق با حجم بیشتری تولید و به دلیل سرعت افزوده شده گاز غبار بیشتر (مصرف سوخت بیشتر => حجم محصولات احتراق بیشتر + ثابت بودن مقطع عبورگاز=> سرعت عبور بالاتر گاز + مواد پودری موجود در مسیر گاز => حجم گاز و غبار بیشتر به همراه گاز) ازکوره به سمت پیش گرمکن و نهایتاً الکتروفیلتر منتقل شده که تأثیرات نامطلوبی بر روی راندمان الکتروفیلتروسیکلونها (چرا که سیکلونها و الکتروفیلتر برای دبی گاز و غبار و دمای کمتر که شرایط طرح بوده طراحی شده اند) ایجاد و نتیجه آن را به صورت افت راندمان غبارگیری و خروجی غبار و گازهای آلاینده فراتر از حد استاندارد سازمان حفاظت محیط زیست مشاهده میشود.
در گام اول پروژه برنامه پایش فرآیندی تدوین و اطلاعات فرآیندی مورد نیاز ازطریق امکانات خط تولید و با افزودن ۳ دستگاه نمایشگر فشار (Pressure Gauge) به صورت روزانه ثبت و مورد ارزیابی قرارگرفت. همچنین تمام پارامترهای فرآیندی خط تولید طبق برنامه توسط آزمایشگاه معتمد سازمان حفاظت محیط زیست (مرحله قبل ازاعمال تغییرات فرآیندی) اندازه گیری و ملاک تحلیل کارشناسان پروژه قرارگرفت. سپس شرایط فعلی خط تولید با طراحی اولیه تطبیق داده شد و مغایرتها تعیین گردید.
درگام دوم شرایط موجود با نرم افزارهای مدل سازی و با استفاده از رایانههای مجهز (Super Computer)، بررسی و تحلیل شده و با تشخیص نتایج شعله فعلی، خروجی مدلها تحلیل و سپس تغییرات مورد نظر ابتدا در همان محیط نرم افزار شبیه سازی اعمال و تحلیل و پس ازاطمینان از مدل ها، طی کمتر از یک هفته تغییرات در یونیت احتراق مشعل و هوا و گاز ورودی کوره اعمال گردید که ضمن حفظ ظرفیت تولید و بدون تحمیل هرگونه تنشی به تجهیزات خط تولید، اهداف بهینه سازی فرآیند احتراق تماماً محقق گردید.
با این روش تمامی مراحل امکان سنجی و بهینه سازی ابتدا در نرم افزار مورد تحلیل قرار گرفته و بدون هیچگونه نگرانی ناشی از وارد آمدن تنش به کوره، بهبود حاصل گردید و نتایج آن ضمن مشاهده در پارامترهایی، چون مصرف گاز روزانه مشعل، با پایش فرآیندی مرحله دوم (پس از اجرای بهبود) توسط همان آزمایشگاه ارزیابی و درگام پایانی، طی۴ ماه نیز شرایط جدیدتحت کنترل قرار گرفته و کاملاً تثبیت شد.
۱ - بهبود شرایط و پارامترهای بهرهبرداری
۲- عدم تغییر در کیفیت آهک خروجی (محصول) و بالا بودن میزان درصد خلوص (۹۵درصد)
۳- صرفهجویی در سوخت مصرفی (گاز طبیعی)
۴ – بهبود شرایط سیستم غبارگیری
۵ - کاهش بار حرارتی موجود در کورهها محاسن زیر را به دنبال دارد:
۶ - صرفهجویی در انرژی الکتریکی:
منبع: ذوب آهن اصفهان