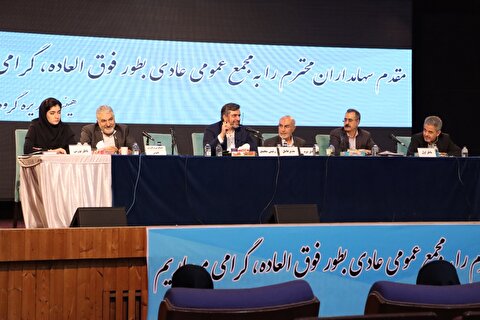
به گزارش می متالز، بهعنوان نمونه، تغییر فناوری کوره ریورب به فلش در واحدهای تابع شرکت ملی صنایع مس، یک اتفاق بزرگ و دستاورد مطلوب بود. با این وجود، گازهای خروجی از کوره ریورب (فناوری قدیمی) ۰.۷ تا ۱ درصد SO۲ دارد اما در کورههای فلش حاوی حدود ۲۶ درصد SO۲ است. در نتیجه، یکی از مهمترین اقدامات مورد نیاز در کنار ساخت کورههای فلش، راهاندازی کارخانههای اسید است تا حجم آلایندگیهای زیستمحیطی را به کمترین میزان کاهش دهد. در این زمینه، همزمان با طرح تغییر فناوری از ریورب به فلش، ساخت کارخانههای اسید از سوی شرکت ملی صنایع مس ایران پیگیری شده است. در فرآیند تولید برخی فلزات اساسی مانند مس، گاز دیاکسید گوگرد بهعنوان یک محصول جانبی تولید میشود و برای جلوگیری از ورود این گاز (بهعنوان یک آلاینده)، باید راهکاری برای حذف آن پیدا کرد. تبدیل این گاز به اسیدسولفوریک، یکی از بهصرفهترین کارهایی است که میتوان برای جلوگیری از انتشار آن در محیط انجام داد. درنتیجه میتوان گفت اسید سولفوریک یک الزام برای کارخانه فلش است. پروژه اسید در شرکت مس زمانی مطرح شد که کارخانه ذوب سرچشمه از سال ۱۳۸۹ تغییر فناوری ذوب از ریورب به فلش را آغاز کرد. ظرفیت طراحی کارخانههای اسید در سرچشمه و خاتونآباد ۶۰۰ هزار تن اسید ۵.۹۸ درصد است اما کارخانه اسید سرچشمه با صرف هزینهای معقول و تعویض برخی تجهیزات، قابلیت افزایش ظرفیت تولید تا یکمیلیون تن اسید در سال را دارد. برای اینکه از چه فناوری در این پروژه استفاده شده است باید گفت فناوریهای برتر جهان در ساخت کارخانه اسید چند مورد بیشتر نیستند. برترین فناوری، متعلق به شرکت مونسانتوی امریکاست که کارخانههای اسید چین بیشتر به وسیله همین شرکت ساخته شدهاند. در مقام دوم نیز اتوتک قرار دارد. با توجه به زمینههای همکاری زیاد شرکت مس و اتوتک، شرکت مس تصمیم گرفت کارخانههای اسید در مجتمع مس سرچشمه و خاتونآباد بر اساس فناوری جذب مضاعف (Absorption Double) طراحی شوند که صاحب این فناوری، شرکت اتوتک آلمان است. هزینه سرمایهگذاری ارزی و ریالی ۲ پروژه اسید با احتساب کارخانههای تصفیهپساب و اضافهکاریهای مرتبط، حدود ۲۰۶ میلیون یورو و ۱۰۰ میلیارد تومان بوده است.
محمدرضا سرحدی / مجری ساخت شرکت ملی صنایع مس ایران