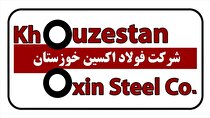
به گزارش میمتالز، تقاضای داخلی سیمان نیز در سال ۱۴۰۲ رشدی قابل توجه را تجربه کرد (افزایش حدود ۱۰.۹٪ نسبت به سال قبل)، ضمن آنکه دولت برای تکمیل پروژههای عمرانی بودجهای بالغ بر ۳۰۰۰ هزار میلیارد تومان (۶ میلیارد دلار) تا پایان سال ۱۴۰۳ اختصاص داده بود که حدود دو سوم مصرف سیمان را تامین میکرد.
علاوه بر این، ایران توانسته مازاد تولید را به کشورهای همسایه صادر کند (حدود ۶.۵ میلیون تن کلینکر و سیمان در نیمه اول ۱۴۰۳). تقریباً تمام نیاز داخلی از ظرفیت داخلی تأمین شده و بخش عمدهای از ماشینآلات و تجهیزات صنعت سیمان (حدود ۸۵٪) تولید داخل است. به این ترتیب، سیمان بهعنوان کالایی استراتژیک در اقتصاد ایران نهتنها به جذب سرمایههای دولتی و خصوصی منجر شده، بلکه زمینهساز اشتغال و رونق کسبوکار در مناطق معدنی و صنعتی شده است.
با وجود اهمیت فوق، صنعت سیمان ایران با چالشهای ساختاری جدی مواجه است. از نظر تجهیزات، بخش قابل توجهی از کارخانهها عمر بالا دارد و بخشی از ظرفیت تولید (بیش از ۳۰ کارخانه) به دلیل کمبود سوخت عملاً غیرفعال شده است.
بهعنوان مثال، در سال ۱۴۰۳، ۲۲ واحد تولیدی بزرگ سیمان بهدلیل کمبود گاز طبیعی تعطیل شدند و تابستان گذشته سهمیهبندی برق بیش از ۷۰٪ خطوط تولید را از مدار خارج کرداین محدودیتهای انرژی موجب افت تولید، افزایش بهای تمامشده و ایجاد توقفهای مکرر در تولید شده و قیمت سیمان در بازار داخلی را تا ۹۰٪ افزایش داده است.
علاوه بر این، سیاستهای قیمتگذاری دستوری دولت که قیمت سیمان را در حدود ۳۵ دلار در هر تن ثابت نگاه داشته است، حاشیه سود کارخانهها را کاهش داده و انگیزه سرمایهگذاری در بهبود کارایی را تضعیف میکند. در بخش صادرات نیز مشکلات جدی وجود دارد: با اینکه سالانه حدود ۱۴ میلیون تن سیمان و کلینکر به کشورهای همسایه صادر میشود، ناترازی ارزی (بازنگرداندن ارز حاصل از صادرات) جایگاه ایران را در بازارهای جهانی ضعیف کرده و تعهدات ارزی صادرکنندگان را با چالش مواجه نموده است.
بهعلاوه موانع تجاری و تعرفهای نیز بازارهای صادراتی را تهدید میکند (برای نمونه ارمنستان واردات سیمان ایران را برای شش ماه تمدید کرد).
در مجموع، «فرسودگی تجهیزات»، «هزینه بالای انرژی»، «سیاستهای دستوری قیمت»، و «مشکلات ارزی در صادرات» بهعنوان چهار پاشنه آشیل صنعت سیمان شناسایی میشوند که بدون رفع آنها بازده سرمایهگذاری در این بخش کاهش یافته و پایداری صنعت را تهدید میکنند.
دلایل فنی و اقتصادی فراوانی ایجاب میکند که سرمایهگذاری گستردهای در نوسازی و بهینهسازی این صنعت صورت گیرد. اولین و مهمترین دلیل، کاهش هزینههای عملیاتی از طریق افزایش بازده انرژی است. تجربیات جهانی نشان میدهد شدت انرژی (انرژی مصرفی بهازای هر تن سیمان) در ۴ دهه گذشته از حدود ۷٫۳ MBtu به ۴٫۵ MBtu کاهش یافته است.
این پتانسیل نشان میدهد با استفاده از فناوریهای نوین میتوان مصرف سوخت و برق را بهمقدار قابل توجهی پایین آورده و هزینههای تولید را کاهش داد. برای نمونه در کارخانههای UltraTech هند، بهکارگیری سوختهای جایگزین آلی (مانند باگاس و زغال سنگ اصلاحشده) توانست هزینه برق را بهمیزان ۰٫۶۴ روپیه در هر کیلوواتساعت کاهش داده و معادل ۷۳۸ لک روپیه صرفهجویی ایجاد کند. مشابه این، استفاده از مدلهای هوش مصنوعی در خط تولید کورهها پایداری عملیات را افزایش داده و تولید کلینکر را بهطور ملموسی بالا برد. (بهعنوان مثال سه تن در ساعت کلینکر بیشتر در طرح شرکت UltraTech تولید شده است.)
از منظر اقتصادی نیز محاسبه بازده سرمایهگذاری (ROI) بهنفع نوسازی سخن میگوید. متوسط قیمت نفت و سوخت گاز بهعنوان مؤلفهای مهم در قیمت تمامشده هر تن سیمان است.
با کاهش مصرف سوخت و بهرهگیری از فناوریهای پیشرفته، میتوان دوره بازگشت سرمایه را کوتاه کرد. بهعنوان مثال، پروژه توسعه ظرفیت UltraTech به هزینه ۷۶ دلار بهازای هر تن بوده که با فرض قیمتهای صادراتی بالای ۶۰ دلار بازده مناسبی پیشبینی میشود.
در کل، طبق بررسیهای بینالمللی، با ترکیبی از روشهای نوین تولید، بازیافت حرارت، بهینهسازی فرآیند و هوشمندسازی تجهیزات، امکان کاهش ۱۰–۱۵ درصدی مصرف انرژی و بهبود ۵–۱۰ درصدی ضریب تولید در دوره یک تا سه ساله فراهم است. این اعداد زمانی معنادار میشوند که توجه کنیم هر درصد صرفهجویی در انرژی معادل میلیونها دلار صرفه اقتصادی سالانه است.
تجربه مشابه در سایر کشورها (برای مثال پیشگامی چین در نصب فیلترهای کیسهای و سیستمهای کنترل هوشمند) نیز حاکی از جذب سرمایههای خارجی و بهکارگیری تکنولوژیهای برتر است. بنابراین، ترکیب تحلیل فنی (بازده انرژی و تولید) با محاسبات مالی دوره بازگشت سرمایه و IRR نشان میدهد که سرمایهگذاری در نوسازی غیرفیزیکی (هوشمندسازی) و فیزیکی، هر دو از منظر اقتصادی کاملاً توجیهپذیر و سودآور هستند.
نوسازی فیزیکی به اصلاح یا جایگزینی تجهیزات و خطوط تولید مربوط میشود: از نصب کورههای مدرن با بهرهوری بالاتر و آسیابهای پیشرفته تا بهینهسازی سیستمهای انتقال مواد و ذخیرهسازی. این نوع نوسازی هزینههای سرمایهای بالایی دارد، اما افزایش ظرفیت و راندمان تولید را به دنبال دارد. بهعنوان نمونه، تعویض یک کوره قدیمی با کورههای پیشگرمکن مدرن میتواند مصرف سوخت را حدود ۱۰–۱۵ درصد کاهش دهد و بازده تولید را بهطور چشمگیری ارتقا بخشد.
از سوی دیگر، هوشمندسازی شامل نصب سیستمهای کنترل دیجیتال، حسگرهای اینترنت اشیا، سامانههای پیشبینی بهرهبرداری و هوش مصنوعی در خطوط تولید است. این سرمایهگذاریها معمولاً هزینه کمتری نسبت به نوسازی فیزیکی دارند و نتایج ملموس آنها (افزایش پایداری فرآیند، کاهش توقفات اضطراری و بهبود کیفیت محصول) در کوتاهمدت خود را نشان میدهد. برای مثال، سامانه AI در کارخانه UltraTech ثبات عملیاتی کوره را بهبود داده و تولید کلینکر را سه تن در ساعت افزایش داد، بدون نیاز به تغییرات فیزیکی اساسی در خط.
همچنین، با توجه به درصد بالای بومیسازی ماشینآلات (بیش از ۸۵٪ قطعات داخلی)، نوسازی فیزیکی از طریق سازندگان داخلی قابل انجام است، در حالی که راهاندازی سامانههای هوشمند میتواند زمینهساز انتقال فناوری و توسعه شرکتهای دانشبنیان شود. بهطور خلاصه، نوسازی فیزیکی افزایش ظرفیت و کاهش مصرف انرژی را در پی دارد و بهرهوری را از طریق پیشرفتهای سختافزاری زیاد میکند، در حالی که هوشمندسازی با اصلاح نرمافزاری و اطلاعاتی فرآیندها موجب بهبود بهرهوری عملیاتی و کاهش هزینههای جاری میشود. ترکیب این دو رویکرد، بهویژه در کارخانههای بزرگ یا قدیمی، بیشترین بازده سرمایهگذاری را به دنبال خواهد داشت.
برای تجمیع منابع مالی و تخصصی لازم، پیشنهاد میشود یک کنسرسیوم چندجانبه تحت قالب شرکت پروژه (SPV) تشکیل شود. SPV یا شرکت با هدف خاص، یک شرکت حقوقی مستقل است که تنها برای انجام یک پروژه خاص (مثلاً نوسازی یک خط تولید، ساخت یک کارخانه یا اجرای پروژه زیرساختی) ایجاد میشود. در این ساختار، شرکتهای تولیدکننده سیمان عمده (اعم از دولتی، خصوصی و صندوقهای سرمایهگذاری صنعتی) بهصورت سهامداران اصلی و همراه با نهادهای مالی (بانکها، صندوق توسعه ملی، بیمهها) و سرمایهگذاران خارجی واجد شرایط مشارکت میکنند. مدل حقوقی SPV میتواند بهصورت یک شرکت سهامی خاص با اساسنامهای متمرکز بر اهداف پروژه باشد تا ضمن شفافیت حاکمیتی، مسوولیتهای پروژه مشخص شود.
از سوی دیگر، مطابق قانون تشویق و حمایت سرمایهگذاری خارجی، این ساختار امکان جذب سرمایهگذاری بینالمللی را نیز دارد. تامین مالی پروژهها میتواند از طریق ترکیبی از آورده نقدی سهامداران و تسهیلات بانکی بلندمدت صورت گیرد.
بهعنوان نمونه، برنامه توسعه ظرفیت UltraTech با ترکیبی از بدهی بانکی و سود انباشته شرکت تأمین مالی شده بود؛ مشابه این مدل میتواند در ایران نیز اجرایی شود. نقش دولت میتواند در تضمین بخشی از تسهیلات، ارائه مشوقهای مالیاتی یا تضمین خرید محصول (تهاتر بخشی از خروجی با کالاهای مصرفی یا ارزی) متمرکز باشد. بهکارگیری سازوکارهای کنسرسیومی اجازه میدهد ریسکها و سرمایه لازم میان چند شرکت تقسیم شود و مزایای مقیاس (نظیر خرید تجهیزات و سوخت ارزانتر) برآورده گردد.
بهعلاوه، مشارکت بازیگران متنوع (دولتی، بخش خصوصی، بانکها و شرکتهای فناوری) تضمین میکند که از یک سو منابع مالی و تخصص فنی تأمین شود و از سوی دیگر کنترل و نظارت کافی بر طرحها اعمال گردد. ساختار SPV عملاً میتواند نقشی مانند صندوق توسعه صنعت سیمان ایفا کند که پروژههای نوسازی در چندین واحد را مدیریت کرده و ضمن تضمین بازپرداخت سرمایهگذاران، منافع ملی را نیز حفاظت نماید.
برای نوسازی صنعت سیمان نمیتوان به بودجه دولت یا سرمایهگذاری سنتی کارخانهها دل بست. پیشنهاد مشخص، تشکیل یک کنسرسیوم مشترک (SPV) متشکل از سه رکن است:
۱. دولت (وزارت نیرو + صمت)
ارائه مشوق تعرفهای برای برق صرفهجوییشده
تخصیص تسهیلات انرژیبر پایه صرفهجویی واقعی
تسهیل صدور مجوز واردات تکنولوژی نوین
۲. بخش خصوصی (کارخانههای سیمان + شرکتهای مشاور)
تعهد به اجرای پروژههای ارتقای بهرهوری انرژی
ارائه اسناد صرفهجویی واقعی انرژی و کاهش CO₂
۳. سرمایهگذار توسعهای (مانند بانک صنعت و معدن + صندوق توسعه ملی)
تأمین مالی پروژهها از محل بازگشت صرفهجویی انرژی یا صدور گواهی صرفهجویی
ساختار قراردادی مبتنی بر EPCF یا BOT
این ساختار میتواند مشابه تجربههای موفق جهانی مانند هند، ترکیه و اندونزی اجرا شود.
شرکت UltraTech Cement از بزرگترین تولیدکنندگان سیمان در جهان (سومین تولیدکننده بزرگ خارج از چین) با ظرفیت حدود ۱۲۰ میلیون تن در سال است. این شرکت دارای ۲۲ کارخانه یکپارچه و ۲۷ واحد آسیاب است و برای توسعه ظرفیتهای جدید مبلغ ۱۲۸۸۶ کرور روپیه (حدود ۱٫۵ میلیارد دلار) سرمایهگذاری کرده است. UltraTech بهعنوان پیشگام در بهرهوری صنعتی، از فناوریهای مدرن از جمله سیستمهای کنترل پیشرفته استفاده کرده است. در کارخانه ۴ میلیون تنی “ویکرام” سامانه هوش مصنوعی مستقر در کوره، پارامترهای عملیات را بهینه کرده و به ثبات تولید کمک کرده است (افزایش تولید کلینکر به میزان ۳ تن در ساعت). همچنین استفاده از سوختهای جایگزین در نیروگاه-محرک (افزایش تا ۲۵٪ سهم سوخت جانبی) هزینه انرژی را ۰٫۶۴ روپیه در هر کیلوواتساعت کاهش داده و صرفهجویی ۷۳۸ لک روپیهای (معادل حدود ۱.۵ میلیون دلار) بهدنبال داشته است. تامین مالی چنین پروژههایی از ترکیبی از بدهی بانکی و منابع داخلی صورت گرفته است؛ بهطوری که UltraTech بخش عمده توسعه آتی خود را از طریق ترکیب این دو منبع تأمین میکند. این تجربه نشان میدهد که با فناوری مناسب و ساختار مالی قوی، میتوان نهتنها بازده عملیاتی را بهبود بخشید، بلکه جذب سرمایه بزرگ را نیز توجیه و متقاضی نمود.
شرکت UltraTech Cement هند بهعنوان بزرگترین تولیدکننده سیمان در آسیا، در سالهای اخیر پروژهای وسیع برای کاهش شدت انرژی و کربن اجرا کرده است:
نتیجه این اقدامات، کاهش بیش از ۱۵٪ مصرف انرژی ویژه (MJ/ton) در عرض ۵ سال بوده است. در حالی که دولت هند، مشوقهایی مانند “کاهش مالیات بر سود کارخانههای کمکربن” و “صدور مجوز صادرات کربن اعتباری” به UltraTech اعطا کرده است.
حل مشکل بازگشت ارز حاصل از صادرات سیمان نیازمند اقدامات دیپلماتیک و تجاری نوآورانه است. در درجه اول، هماهنگی با کشورهای همسایه و شرکای تجاری برای سازوکارهای تهاتری یا تسویه ارزی ضروری است. تجربهها نشان میدهد کشورهایی مانند چین و ویتنام در دورههای تحریم یا فشار ارزی، بخشی از مبادلات خود را به تجارت تهاتری یا نظامهای مبادله کالا تبدیل کردهاند. در مورد سیمان ایران نیز میتوان در برخی قراردادها بهجای واردات کالا با ارز، معادل کالایی یا خدمات دریافت نمود.
بهعنوان مثال، در نشستهای اخیر اتاق بازرگانی تأکید شده که “عدم بازگشت ارز صادراتی” موجب کاهش رقابتپذیری سیمان ایران شده است. همچنین وزیر صمت گزارش کرده است که “برخی سیاستهای فعلی بازگشت ارز با سیاستهای تجاری مغایرت دارد و بخشی از تجارت را فلج کرده است”، امری که با اصلاح مقررات ارزی و مشوقهای صادراتی میتوان برطرف کرد.
در واقع، تأمین ثبات در بازارهای هدف نیازمند دیپلماسی فعال صنعتی است: بازاریابی مشترک، شرکت در نمایشگاههای تخصصی بینالمللی و انعقاد توافقهای دولتی–دولتی (مثلاً توافق تهاتر سیمان با کالاهای مورد نیاز مانند ماشینآلات یا فناوری) میتواند ضمن تثبیت فروش، راه بازگشت سریعتر ارز را نیز فراهم آورد. به کارگیری مکانیزمهای تسویه با ارزهای منطقهای یا راهاندازی کانالهای مالی خاص (مانند «اینستکس» نوع صنعتی) از دیگر راهکارهایی است که تجربه کشورهای توسعهیافته در این وضعیت نشان داده است.
ناترازی برق، تهدیدی جدی برای اقتصاد تولیدمحور ایران و بهویژه صنایع انرژیبر همچون سیمان است.
در سالهای اخیر، رشد نامتوازن مصرف و تولید برق، بهویژه در فصول گرم، باعث شده تا بخش صنعت با قطعیهای گسترده، سهمیهبندی یا اجبار به کاهش بار مواجه شود. این روند نهتنها تولید را مختل میکند، بلکه هزینههای پنهان زیادی از جمله توقف تولید، کاهش عمر تجهیزات و افت بهرهوری در پی دارد. در این میان، صنعت سیمان که از بزرگترین مصرفکنندگان انرژی در کشور است، بهدلیل ساختار قدیمی تجهیزات و فرآیندهای تولید، بیشتر از سایر صنایع در معرض آسیب قرار دارد. از همین رو، استمرار وضعیت موجود میتواند جایگاه رقابتی این صنعت در داخل و خارج کشور را به خطر بیندازد.
اما در دل این بحران، فرصتی نهفته است؛ فرصتی برای نوسازی، ارتقاء بهرهوری و کاهش وابستگی به انرژی فسیلی.
ناترازی انرژی، اگرچه در ظاهر یک تهدید است، اما میتواند نقش یک «کاتالیزور تحول» را ایفا کند. بسیاری از زیرساختهای صنعتی ایران طی چند دهه گذشته بهروز نشدهاند و بخشی از مصرف بالای انرژی بهدلیل راندمان پایین تجهیزات قدیمی است. این بحران، بهجای آنکه تنها به محدودیت تعبیر شود، میتواند بهانهای برای شروع موج نوسازی و بهینهسازی باشد؛ اقدامی که سالها به دلایل مالی یا سیاستی به تعویق افتاده است. کاهش اتکا به برق شبکه، تنوعبخشی به منابع انرژی و استفاده از فناوریهای کممصرف، مزایایی هستند که نهفقط در شرایط بحران، بلکه در مسیر توسعه بلندمدت نیز مزیتزا خواهند بود.
صنعت سیمان، بهعنوان یکی از قدیمیترین و پرمصرفترین صنایع کشور، میتواند پیشگام تحول در بهرهوری انرژی باشد و با اجرای پروژههای نوسازی فناورانه، از یک مصرفکننده بزرگ به یک نمونه موفق در صرفهجویی و تابآوری تبدیل شود.
صنعت سیمان در ایران نهتنها از نظر حجم تولید، بلکه بهواسطهی شبکه گسترده کارخانههای فعال در سراسر کشور، قابلیت تبدیلشدن به الگوی تحول فناورانه را دارد. پروژههایی نظیر نصب درایوهای VFD، استفاده از خنککنندههای جدید (گریتکولرهای با راندمان بالا)، دیجیتالیسازی مانیتورینگ انرژی، بهینهسازی آسیابها و کاهش ضایعات حرارتی، میتوانند در مقیاس صنعتی اجرا شوند. تجربه ثابت کرده که پیشگامی یک صنعت مادر در اصلاحات بهرهوری، اثرات دنبالهداری بر سایر صنایع و حتی سیاستگذاریهای دولت دارد. از این منظر، سیمان میتواند نهتنها بخشی از راهحل ناترازی باشد، بلکه الهامبخش سایر صنایع نیز بشود.
تشکیل کنسرسیومهای نوسازی با مدل SPV، بهرهگیری از فناوریهای نوین و ایجاد پیوند مؤثر میان دولت، بخش خصوصی و سرمایهگذاران، میتواند این مسیر را هموار سازد.
نوسازی زیرساختهای صنعتی نیازمند سرمایهگذاری سنگین، دانش فنی بهروز و هماهنگی چندجانبه است. مدل SPV (شرکت پروژهای) بهدلیل استقلال حقوقی، ساختار شفاف و امکان جذب منابع مالی متنوع، بهعنوان یک ابزار اجرایی مؤثر شناخته میشود. تشکیل کنسرسیومهایی با حضور شرکتهای سیمانی، شرکتهای دانشبنیان، سرمایهگذاران خطرپذیر و نهادهای حاکمیتی، امکان تسهیم ریسک، انتقال فناوری و اجرای پروژههای مقیاسپذیر را فراهم میکند. در واقع، این مدل میتواند مانع پراکندگی منابع شده و با هدفگذاری مشترک، نوسازی صنعت سیمان را از سطح شعار به واقعیت نزدیک کند.
تجربه کشورهایی مانند هند نشان میدهد که با اراده، سیاستگذاری هوشمند و مشارکت چندجانبه، میتوان مسیر تحول را آغاز کرد و از تهدید ناترازی، فرصت رشد و بهرهوری ساخت.
هند طی دو دهه گذشته با چالشهای مشابهی روبهرو بوده، اما با اجرای طرحهایی، چون PAT Scheme (Perform, Achieve and Trade) و ایجاد مشوقهای بهرهوری انرژی، موفق شده است مصرف انرژی در صنایع انرژیبر را کاهش داده و تابآوری شبکه برق را تقویت کند. شرکت UltraTech Cement، بهعنوان بزرگترین تولیدکننده سیمان هند، نمونهای موفق از یک گذار فناورانه با حمایت سیاستگذار و مشارکت در کنسرسیومهای نوآورانه است. ایران نیز میتواند با الگوبرداری بومی از این تجربهها، رویکردی مشابه در پیش گیرد و از تجربههای بینالمللی برای کوتاهکردن منحنی یادگیری استفاده کند.
اکنون زمان تصمیمگیری است: یا در برابر بحران منفعل بمانیم، یا آن را به اهرمی برای بازآفرینی صنعت و تقویت زیرساختهای ملی تبدیل کنیم. آینده انرژیپایدار صنعت ایران، در گرو همین انتخاب است.
این لحظه تاریخی، نقطهای حساس در سرنوشت صنعت ایران است. اگر امروز برای نوسازی، دیجیتالسازی و بهرهوری انرژی تصمیم جدی اتخاذ نشود، بحران ناترازی نهتنها مزمنتر خواهد شد، بلکه مزیت رقابتی بسیاری از صنایع از بین خواهد رفت. اما اگر این تهدید با اراده ملی به فرصت تبدیل شود، میتوان صنعتی مقتدر، کممصرف و آماده حضور در بازارهای جهانی ساخت. آینده صنعت کشور وابسته به تصمیمات امروز ماست؛ تصمیماتی که میتوانند مسیر توسعه را تعیین کنند.
این راهبردها زمینهساز تحولی پایدار در صنعت سیمان خواهند بود، بهطوری که ضمن جلب اعتماد سرمایهگذاران، منافع اقتصادی و محیطزیستی کشور را حداکثری کنند.
امین معصومی
منبع: سیمان خبر