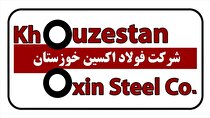
به گزارش می متالز، یکی از بزرگترین صنایع مصرفکننده آب، صنعت سرامیک بوده و بهطور متوسط برای تولید هر مترمربع کاشی و سرامیک حدود ۱۵لیتر آب نیاز است که از این مقدار بسته به میزان وزن کاشی حدود ۱۳لیتر آب بهوسیله اسپری بخار شده و خارج میشود.
در تمام کشورها نوع صنایع و روش تولید، براساس شرایط اقلیمی آن کشور است. برزیل به عنوان دومین تولیدکننده بزرگ کاشی و سرامیک جهان، نمونه موفقی در استفاده از این شبکه است که ۸۵درصد از تولید ۷۰۰میلیون مترمربعی خود را با این روش انجام میدهد. در ایران نیز با توجه به مشکل کمآبی یکی از بهترین روشهای تولید کاشی و سرامیک استفاده از پودر خشک بوده که لازم است بررسی و مطالعات بیشتری روی این روش و همچنین معادن جدید و سایر موارد مربوط انجام شود. در این روش، خاکهای ورودی به کارخانه خردایش و میکرونیزه شده و پس از تولید پودر میکرونیزه با دانهبندی موردنیاز که تابعی از نوع خاک و نوع محصول تولیدی است، وارد دستگاه رطوبتزن و گرانولاتور میشود. در این مرحله با استفاده از نازل، آب به پودر بهدست آمده افزوده و تبدیل به گرانول با منحنی دانهبندی موردنیاز میشود. سپس گرانول بهدست آمده آماده پرس و پخت میشود. ازاینرو نیازی به مصرف آب برای دوغابسازی و در پی آن سوخت برای تبخیر آب مصرف شده نیست.
نخستین کارخانه تولید کاشی و سرامیک استان یزد به روش پودر خشک در شهرستان میبد، روزانه ۷هزار مترمربع سرامیک تولید میکند و با صرفهجویی در مصرف آب، هزینه مصرف انرژی را نیز تا ۵۰درصد کاهش میدهد.
همچنین نخستین واحد تولیدی گرانول به روش پودر خشک کشور در میبد با ظرفیت ۴هزار تن، مواد اولیه شرکتهایی که بدون قسمت خاکسازی هستند را با فرمولسازی و رطوبت خاص تامین میکند تا پس از پرس، به شکل بیسکویت کاشی درآید.
روش پودر خشک در صنعت کاشی و سرامیک همراه با مزایایی بوده که در ادامه عنوان شده است:
- با توجه به حذف اسپری و دوغاب میزان مصرف آب حدود ۹۰درصد کاهش مییابد. برای تولید یک مترمربع کاشی با وزن حدود ۲۰کیلوگرم ۱۳لیتر آب در روش اسپری (تر) در واحد تولید گرانول موردنیاز است. این مقدار در روش پودر خشک با توجه به رطوبت ۵درصدی خاک ۰.۸لیتر برای هر مترمربع است.
- در این روش احتیاج به مصرف گاز در اسپری درایر نیست. درحالیکه برای تبخیر ۱۳لیتر آب در روش اسپری ۱.۴مترمکعب گاز طبیعی موردنیاز است. ازاینرو با نرخهای جاری، میزان صرفهجویی ریالی یک کارخانه کاشی با ظرفیت ۶ میلیون مترمربع در سال حدود ۷میلیارد ریال است.
- مصرف برق به میزان ۶۰درصد در واحد تولید گرانول کاهش مییابد. مصرف برق به ازای هر تن خاک به روش تر ۷۲کیلو بر تن و برای خط خشک ۲۴کیلو بر تن است و با احتساب ۲۰کیلوگرم خاک برای هر مترمربع و نرخ ۴۷۰ریال برای هر کیلووات ساعت برق، برای هر مترمربع ۴۵۱ریال اضافه هزینه است.
- استفاده نکردن از روانساز که باعث صرفهجویی ۲۰۰ریالی به ازای هر مترمربع میشود.
- استفاده نکردن از گلوله که با توجه به میزان مصرف ۵۰۰گرم به ازای هر تن خاک باعث صرفهجویی ۲۲۰ریالی به ازای هر مترمربع میشود.
- خاکهای مورداستفاده در تولید کاشی کف بدنه قرمز و دیوار از نوع ارزانقیمت است. در این روش ویسکوز بودن خاک با توجه به تشکیل نشدن دوغاب اهمیتی ندارد.
- با توجه به حذف سنگشکن و استفاده از خاکهای نرم و حذف اسپری درایر، همچنین کاهش میزان مصرف برق و مصرف نشدن گاز، این روش در حفظ محیطزیست اثر بسزایی دارد.
- میزان سرمایهگذاری برای واحد تولید گرانول ازجمله ساختمان، ماشینآلات و تاسیسات با ظرفیت مشابه حدود ۵۰درصد کاهش مییابد.
ماشینآلات تهیه بدنه خشک از شرکت مانفردینی ایتالیاست که یکی از معتبرترین خطوط تهیه بدنه خشک را در جهان ارائه میکند. درحالحاضر عمده تولید کاشی در ایران بر اساس گرانول تر (اسپری داریر) انجام میشود و فقط تعداد محدودی واحد به تولید کاشی با گرانول خشک میپردازند.
بیشتر کاشی تولید شده با گرانول خشک در ایران در اندازههای کوچک تولید میشود. درواقع فرآیند تولید کاشی از گرانول تر و خشک پس از ماشین پرس مشابه بوده و تنها آمادهسازی اولیه سنگ و تولید گرانول متفاوت خواهد بود.