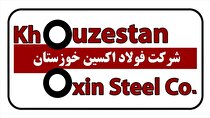
شرکت ذوب روی بافق یکی از بزرگترین واحدهای تولید شمش روی در کشور بوده که به دلیل دارا بودن واحد تشویه، تنها تولیدکننده روی در ایران است که امکان تولید همزمان شمش روی از منابع سولفوره و اکسیده با عیار 99.98 درصد را دارد. این شرکت با دارا بودن واحدهای مختلفی نظیر هویمدیا، خردایش، تشویه، لیچ سولفوره، لیچ اکسیده، تصفیه محلول، الکترولیز، ذوب، واحد BZS، پودر روی و اسیدسولفوریک، یکی از کاملترین مجتمعهای تولیدکننده فلز روی در کشور است که امکان تولید شمش روی با بالاترین کیفیت، منطبق با استانداردهای بینالمللی را دارد.
این شرکت در سال 1370 سال ثبت و به عنوان شرکت سهامی خاص شناخته شد. تاریخ اخذ جواز فعالیت مجموعه به سال 1372 برمیگردد و تاریخ راهاندازی و افتتاح مجتمع در مرداد ماه سال 1379 و پس از طراحی و نصب تجهیزات و انتقال دانش فنی از شرکت NFC چین صورت پذیرفت. متاسفانه در بین سالهای 1382 تا 1384 به دلایل مختلف، عملیات تولید مجتمع متوقف شد و به همین دلیل در سال 1383 بیش از 98.17 درصد سهام شرکت ذوب روی بافق توسط هلدینگ توسعه معادن روی ایران خریداری شد. پس از این تغییر و تحولات مدیریتی در شرکت، عملیات بازسازی، تعمیرات اساسی و تغییر خط تولید از سولفوره به اکسیده در سال 1385 انجام شد.
بر اساس پروانه بهرهبرداری که در تاریخ فروردین ماه 1386 صادر شد، ظرفیت تولید سالانه شرکت حدود 30 هزار تن شمش روی و 30 هزار تن اسیدسولفوریک در سال بود ولی بر اساس مجوز جدید پروانه بهرهبرداری که در تیرماه سال 1392 صادر شد، ظرفیت تولید به حدود 60 هزار تن شمش روی و 60 هزار تن اسیدسولفوریک در سال افزایش یافت. از سال 1385 تا آبان ماه سال 1392 تولیدات شرکت با خاک اکسیده صورت میگرفت و بهرهبرداری از واحد تولید کنسانتره روی به روش هویمدیا با خرید تجهیزات مربوطه از آفریقای جنوبی در سال 1393 تحقق یافت.
از طرفی راهاندازی مجدد خط تولید بر مبنای خاک سولفوره از آبان 1392 آغاز و تا به امروز ادامه دارد. با این حال، تولیدات شرکت آن هم به صورت همزمان و با ماده معدنی و کنسانترههای اکسیده و سولفوره، از اسفندماه سال 1395 آغاز و تا به امروز نیز همچنان ادامه دارد. علاوهبراین، عملیات اکتشاف و استخراج از معدن سرب و روی انجیره در سال 1396 و آغاز بهرهبرداری از آن در اوایل سال 1397 یکی از تحولات عظیم این شرکت بود که جزئی از مطالعات معدنی و اکتشافی در معادن استان و استانهای همجوار از سال 1395 به این طرف بود.
کنسانتره یا خاک سولفوره پرعیار از شرکتهای معادن بافق (معدن کوشک)، شاهین، باما، معدنکاران انگوران، تیران، امین خرمدشت و شرکت تهیه و تولید مواد معدنی ایران (معدن انگوران) با عیار روی بین 42 تا 50 درصد تامین میشود و ماده معدنی اکسیده روی کالامین مهدیآباد و معادن کوچک ایران مرکزی با عیار روی بین 8 تا 10 درصد نیز در این مجتمع استفاده میشود.
در حال حاضر تنها یک معدن به نام معدن سرب و روی انجیره با میزان ذخیره 37 هزار تن و میانگین عیار 12.5 درصد در اختیار شرکت ذوب روی بافق قرار دارد.
ظرفیت اسمی تولید شمش روی در شرکت ذوب روی بافق سالانه 30 هزار تن است که با توجه به مشکلاتی که در جهت تامین مواد اولیه و همچنین فرسودگی تجهیزات وجود دارد در حال حاضر با 60 درصد ظرفیت، معادل تقریبا 18 هزار تن در سال تولید داریم و همچنین ظرفیت اسمی تولید اسیدسولفوریک در این واحد سالانه 60 هزار تن است که در حال حاضر میزان تولید آن نیز به 30 هزار تن در سال رسیده است.
در سالها اخیر خوراک مصرفی شرکت ذوب روی بافق که عمدتا کنسانتره سولفوره است توسط معادن صادر میشد و شرکت جهت تامین مواد اولیه با مشکلات عمدهای مواجه بود ولی خوشبختانه با تمهیداتی که وزارت صمت در ماههای گذشته -شامل اخذ عوارض از صادرات مواد خام معدنی- در نظر گرفت این مشکل تا حد زیادی رفع گردید و در حال حاضر، شرکت ذوب روی بافق با توان و قدرت بیشتری در حال تولید شمش روی است و برای نمونه میتوان گفت که در آذر ماه امسال با تولید یک هزار و 805 تن ورق روی توانست برای دومین بار رکورد ادوار گذشته را بشکند.
به طور میانگین برای تولید هر تن شمش روی از کنسانتره سولفوره و اکسیده دو الی پنج تن کیک فیلتر (باطله) ایجاد میشود. در مورد فرآیندهایی که روی باطلهها انجام میشود، باید اشاره کرد که طی فرآیند کیکشویی، حداکثر روی محتوی از آن استحصال میشود و جهت دپوسازی به دپوی باطله انتقال مییابد تا در سالهای آینده با استفاده از فناوریهای بهروز، امکان استحصال حداکثری روی موجود و بقیه عناصر ارزشمند از قبیل نیکل و کبالت امکانپذیر شود.
از تکنولوژیهای فرآوری شامل واحدهای خردایش و هویمدیا، پایرومتالورژی شامل واحدهای تشویه و اسیدسولفوریک، هیدرومتالورژی شامل واحدهای لیچ اکسیده، لیچ سولفوره، تصفیه محلول، الکترولیز و ذوب و ریختهگری در این مجتمع استفاده میشود. تبدیل سولفید روی به اکسید روی (کلسین) که خوراک اصلی واحد لیچ سولفوره است در واحد تشویه انجام میشود.
به منظور جلوگیری از آلودگی محیطزیست گاز SO2 تولیدی جهت تولید اسید به واحد اسیدسولفوریک ارسال میشود. ظرفیت خوراک ورودی این واحد حدود 200 تن در روز است. همچنین باید اشاره کرد که مجتمع ذوب روی بافق تنها شرکتی در ایران است که با توجه به داشتن کوره تشویه، توانایی استفاده از خاک سولفوره جهت تولید شمش روی را دارد.
تجهیزات واحد تشویه شامل انبار کنسانتره، سیستم انتقال خاک، کوره تشویه و سیستم گاز خروجی است. ظرفیت انبار کنسانتره به عنوان محل تخلیه و اختلاط خوراک ورودی به کوره تشویه، 10 هزار تن است؛ سیستم انتقال خاک از انبار کنسانتره به کوره تشویه نیز شامل چند نوار نقاله، خردکن، بگ فیلتر و توزینگر است. کوره تشویه یک کوره بستر سیال است که خاک سولفوره با هوای دمیده شده از پایین کوره، در دمای 850 تا 900 درجه سانتیگراد تشویه شده و گوگرد موجود در آن به گاز SO2 تبدیل و خاک سولفوره به اصطلاح پختهشده و جهت انجام عملیات اسیدشویی آماده میشود؛ ظرفیت این کوره هشت تن در ساعت است.
در بویلر (بازیافت حرارتی) گاز SO2 خروجی از کوره تشویه جهت ارسال به واحد اسید خنک میشود؛ ضمن پایین آمدن دمای گاز به حدود 400 درجه سانتیگراد، بخار آب به میزان 7.5 تن در ساعت با فشار 15 بار تولید میشود.
همچنین خاک پختهشده (کلسین) حاصل از کوره تشویه به منظور ریزتر شدن وارد بالمیل (آسیاب) شده و به دانهبندی ریزتر از 100 میکرون تبدیل میشود؛ ظرفیت این آسیاب نیز 6 تن در ساعت است.
در تجهیز ESP (غبارگیر برقی) ذرات بسیار ریز گرد و غبار همراه گاز SO2 خروجی از کوره تشویه به وسیله قطبهای مثبت و منفی که با برق 40 کیلوولت ایجادشده، جمعآوری و به سیلوی ذخیره خاک انتقال داده میشود.
سیکلونهای چهار تایی و 6 تایی نیز حد واسط بویلر بازیافت حرارتی و ESP واقعشده است و به غبارزدایی از گاز SO2 کمک مینماید؛ ذرات غبار تحت تاثیر نیروی گریز از مرکز به بدنه سیکلون و بعد به پایین سیکلون منتقل میشود.
هر جا سخن از آلودگی به میان میآید، آنچه بیش از هر چیز اذهان را به خود مشغول میکند موضوع آلودگی محیط زیست شامل آب، خاک و هوا است. شرکت ذوب روی بافق برای کمک به حفظ محیط زیست، اقدامات کاربردی زیادی انجام داده است؛ راهاندازی واحد اسیدسولفوریک در جهت استفاده از گاز SO2 خروجی کوره تشویه و ترمیم و نوسازی بخشهای مختلف واحد اسیدسولفوریک مهمترین اقدام شرکت در راستای جلوگیری از آلودگی هوا بوده است.
احداث تصفیهخانه فاضلاب جهت جلوگیری از آلودگی خاک و آب و استفاده از پساب تصفیهخانه جهت آبیاری قطرهای فضای سبز شرکت از دیگر اقدامات محیط زیستی شرکت بوده که با توجه به کمبود آب در استان، از اهمیت بسزایی برخوردار است. علاوه بر این، فضای سبز به میزان 30 درصد از اراضی واحد توسعه یافته است در حالی که بر اساس قانون حفاظت محیط زیست، ایجاد فضای سبز به میزان تنها 10 درصد از اراضی واحدهای صنعتی الزامی محسوب میشود.
در خصوص مدیریت پسماندها نیز اقدامات قابل توجهی انجام شده است که از جمله آنها میتوان به تفکیک زبالهها به دو نوع بازیافتی و زبالههای خانگی (زبالههای عادی)، جمعآوری اولیه زبالههای تر و انتقال به لند فیلد شهری توسط شرکت پیمانکار و پایشهای زیستمحیطی منظم اشاره کرد؛ همچنین در راستای مدیریت پسماند ویژه، در مرحله اول نسبت به ساماندهی و بهبود انباشت کیکهای باطله شرکت اقدامات عاجل به عملآمد. همچنین در جهت مدیریت استفاده بهینه از کیکهای باطله، روزانه 300 تن از کیکهای باطله واحد لیچ، تحت فرآیند BZS فرآوری و محصول کنسانتره حاصله در فرآیند تولید مصرف میشود.
در راستای کاهش هزینههای تولید و برنامه بهبود شرایط محیطزیستی، با همکاری واحد تحقیق و توسعه شرکت، ماده شیمیایی سولفات آهن از فرآیند حذف شده و به جای آن از ضایعات آهن استفاده میشود؛ در ضمن به جای استفاده از کربنات منگنز، لجن آندی که به عنوان باطله محسوب میشود، مورد استفاده قرار میگیرد.
استفاده از گاز طبیعی به عنوان سوخت پاکتر به جای سوختهای فسیلی ازجمله مازوت و گازوئیل از دیگر اقدامات انجام شده در جهت کاهش انتشار آلایندههای محیط زیست بوده است؛ همچنین برای جلوگیری از انتشار ذرات معلق دودکش کوره القایی، با یک شرکت پیمانکار، قرارداد طراحی، ساخت و نصب یک دستگاه بگ فیلتر منعقد شده است.
کلیه فروشهای این شرکت و نیز سایر شرکتهای تولیدکننده شمش روی در هلدینگ توسعه معادن روی ایران، توسط شرکت بازرگانی توسعه صنعت روی به مصرفکنندگان داخلی و خارجی عرضه میشود.
در این زمینه برنامههای بسیاری را مدنظر قرار دادهایم که میتوان به برخی از آنها همانند پروژه افزایش ظرفیت واحد لیچ اکسیدی در جهت بالا بردن ظرفیت تولید در واحد هیدرومتالورژی، پروژه افزایش ظرفیت تولید کنسانتره BZS و پروژه تعویض بویلر بازیافت حرارتی واحد تشویه در جهت افزایش ظرفیت تولید در واحد پایرومتالورژی اشاره کرد.