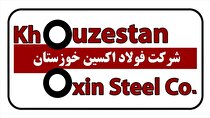
به گزارش می متالز، سنگ ها و کانی های موجود در معدن سنگ آهن حاوی ترکیبات آهن دار می باشند، سنگ آهن با استفاده از فرایندهای فیزیکی و شیمیایی در کارخانه های فولادسازی، فراوری می شوند و آهن آن از دیگر مواد و ترکیبات جدا سازی میشود.
کاربرد فولاد درصنعت از ابتدای انقلاب صنعتی در اروپا به شدت ضرورت یافت. با بالا رفتن تقاضای فولاد، تولید کنسانتره آهن نیز بالا رفت، یکی از مهمترین فرآیندهای زنجیره ساخت فولاد فرآوری سنگآهن می باشد، فرآوری سنگآهن با توجه به محصول ساخته شده به دو دسته تقسیم میگردد: تولید سنگآهن دانهبندی شده و تولید کنسانتره سنگآهن در حال حاضر استان کرمان با بیشترین ذخیره سنگ آهن با شرکت های مختلف به دنبال ایجاد ذنجیره فولاد در کشور است که محصولات مختلفی را نیز از این زنجیره ایجاد کرده است .
شرکت هایی مانند، گل گهر میدکو، فولاد ایرانیان، فولاد زرند و .... غیره در حال تولید فولاد هستند که از کنسانتره تا تولید شمش آهن تولیدات خوبی را در راستای فراوری و صادارت به کشورهای مختلف جهان تولید می شوند اما اینکه محصولاتی که تولید می شوند؛ چه هستند و چه کاربردی دارند سعی می شود در ذیل به آنها پرداخت گرچه در ابتدا تمام شرکت های معدنی به دنبال خردایش و جدا سازی سنگ آهن بوده و ان را خام صادر می کردند اما اکنون به دنبال فراوری هستند گرچه هنوز تا تولید نهایی محصول راه درازی را دارند اما با تکمیل زنجیره فولاد بی شک به این مهم استان کرمان دست خواهد یافت .
از اوایل انقلاب صنعتی در اروپا، استفاده از فولاد به بخش ضروری صنعت تبدیل شده است، با افزایش تقاضای فولاد، تولید کنسانتره آهن نیز افزایش یافت. فرآوری سنگآهن یکی از مهمترین فرآیندهای زنجیره تولید فولاد است.
فرآوری سنگآهن براساس محصول تولیدی به دو دسته تقسیم میشود: تولید سنگآهن دانهبندی شده و تولید کنسانتره سنگآهن. تولید سنگآهن دانهبندی بهصورت خشک و بدون آب انجام میشود. سپس با استفاده از روشهای جدایش فیزیکی (به روش مغناطیسی) سنگآهن پرعیار از باطله کم عیار جدا میشود.
این محصول که سنگآهن دانهبندی نامیده میشود، به علت پایین بودن عیار، قابل استفاده در سیستم احیای مستقیم نیست اما در کوره بلند میتوان از آن استفاده کرد.
در کانسارها عیار متوسط سنگآهن پایین است و مقدار عناصر بیش از حد مورد قبول است به همین دلیل برای پرعیارسازی از روشهای پیشرفتهتر و مدار پیچیدهتری اقدام به تولید کنسانتره میشود.
مدار فرآوری به طور کلی از واحدهای خردایش، آسیابکنی، پرعیارسازی و آبگیری تشکیل شده است. در کنار این واحدها، حملونقل، تامین آب، تاسیسات و... بهعنوان واحدهای جانبی هستند نخستین مرحله (خردایش) در کارخانه با ورود ماده معدنی به سنگشکن آغاز میشود.
در این بخش قطعات بین ۲۰-۲۵ تا ۱۰۰ سانتیمتر به ابعاد کوچکتر از ۲۵-۲۰ سانتیمتر خرد میشوند. البته در ورودی سنگشکن سرند ثابت گریزلی نصب میشود که روزنههای آن برابر با ابعاد محصول خروجی از سنگشکن هستند. به این ترتیب ابعاد ریزتر وارد سنگشکن نمیشوند تا مبادا خردتر شوند و سپس مواد معدنی خرد شده با نوار نقاله وارد مرحله بعدی سنگشکن و سرند میشوند.
در این بخش که بسته به ابعاد و ویژگیهای مواد معدنی ممکن است از ۲ مرحله سنگشکنی خشک تشکیل شده باشد، از سنگشکن مخروطی استفاده میشود و ابعاد مواد معدنی تا اندازه ۳۰ میلیمتر کاهش پیدا میکند. خردایش چند مرحلهای به منظور کنترل دانهبندی و جلوگیری از خردایش بیش از حد ماده معدنی انجام میشود.
مرحله دوم آسیابکنی است، مواد معدنی با ابعاد کمتر از ۳۰ میلیمتر، به منظور خردایش بیشتر وارد مرحله آسیابکنی میشود که بهصورت«تر» انجام میشود در این مرحله، مواد به وسیله آسیاب خودشکن یا نیمه خودشکن یا غلتکی فشاری تا اندازه ۱-۰/۵ میلیمتر آسیاب میشوند.
این ماده با ابعاد ۱-۰/۵ سپس به مرحله بعدی هدایت میشود و در آنجا به وسیله آسیابهای گلولهای مورد خردایش بیشتر قرار میگیرد در این قسمتها خردایش در محیط «تر» انجام میشود، ابعاد خردایش به وسیله هیدروسیکلونها کنترل میشود و هدایت مواد که در آب شناور هستند و ترکیب دوغاب (اسلاری) را ایجاد کردهاند، به وسیله پمپها انجام میشود.
مرحله سوم پرعیارسازی است در این مرحله ذرات پس از عبور از مرحله آسیاب کنی به ابعاد بسیار ریز مورد نظر رسیدهاند و لازم است به منظور جدا کردن مواد باارزش از ترکیبات باطله داخل اسلاری، وارد مرحله بعدی شوند اسلاری به وسیله پمپ به مرحله جدایش مغناطیسی هدایت میشود.
جداکنندههای مغناطیسی تر، جداکنندههای نوع درام هستند. اسلاری از روی این درامها که دارای ویژگی مغناطیسی هستند عبور داده میشود کانیهای آهندار به درام میچسبند. در انتهای درام به وسیله یک تیغه از روی درام جمعآوری میشوند. سایر کانیهای موجود در دوغاب نیز از ته ریز تجهیز خارج میشوند.
این جداکنندههای مغناطیسی دارای انواع شدت پایین، شدت متوسط، شدت بالا و گرادیان (کمیت عدد) بالا هستند که انتخاب آنها براساس ویژگی مواد معدنی و آزمون فرآوری که روی ماده معدنی به انجام رسیده است، انجام میشود و در صورتی که عناصری مانند فسفر و گوگرد در کنسانتره وجود داشته باشد، از روش فلوتاسیون برای جدایش مواد مزاحم از کنسانتره استفاده میشود.
مرحله چهارم نیز آبگیری است وسنگآهن پرعیار شده حاوی مقادیری آب است که باید آبگیری و خشک شود و رطوبت آن به ۱۰-۹ درصد برسد. بدین منظور از فیلترهایی برای جدایش آب کنسانتره بهدست آمده، استفاده میشود سپس کنسانتره آبگیری شده به انبار محصول منتقل و در آنجا دپو میشود. باطله نیز برای آبگیری به سمت تجهیزاتی به نام تیکنر هدایت میشود.
در آنجا مواد جامد تهنشین شده و آب به صورت سرریز از بالای تیکنرخارج میشود ذرات جامد تهنشین شده نیز به وسیله بازوی جمعکننده کف تیکنر به سمت مرکز و به وسیله پمپ به سمت سد باطله هدایت میشوند. برای افزایش سرعت تهنشینی از مواد شیمیایی پلیمری به نام فلوکولانت استفاده میشود که باعث چسبیدن ذرات باطله به یکدیگر و افزایش سرعت سقوط آنها میشود.
سنگهای آهن مهمترین و عمدهترین مواد اولیه را برای تولید گندله تشکیل میدهند گندله؛ یعنی گلولههای تولید شده از نرمه سنگآهن و سایر مواد افزودنی که نخست خام و سپس پخته شده و سخت میشود و برای احیا به روش سنتی تولید آهن در کوره بلند یا روشهای متعدد احیای مستقیم به کار میرود.
گندله ماده اولیه برای تولید آهن خام است و باید در کورههای احیا ویژگی مکانیکی شیمیایی و حرارتی مطلوبی را داشته باشد برای تولید گندله خام، نرمه سنگآهن شامل مواد افزودنی که ۹۰درصد آن زیر ۳۲۵ مش (معادل ۴۵ میکرون) است با محلولهای ترکننده مانند آب برای دستیابی به شکل کروی، در دستگاههای گندله ساز به چرخش درآروده میشوند تا گندله خام تولیدشود.
در هنگام تولید گندله خام ممکن است مواد افزودنی و چسبنده مانند هیدروکسید کلسیم برای افزایش کیفیت و ویژگی متالورژیکی مکانیکی گندله به آن اضافه شود در این مرحله گندله با ابعاد مطلوب و استحکام مکانیکی کافی تولید و برای حملونقل تا دستگاه سخت کردن یا پخت ارسال میشود.
در مرحله دوم گندلههای خام، به منظور سخت شدن در اتمسفر اکسیدکننده به دقت تا زیر دمای نرم شدن سنگآهن در دستگاهی حرارت داده میشوند تا نخست خشک و سپس پخته شوند، به گونهای که درجه تخلخل آنها کاهش پیدا نکند. در این مرحله با پیوند بین ذرات سنگآهن و مواد دیگر بار گندله، ساختار بلوری سنگ تغییر پیدا میکند و واکنشهایی بین مواد سرباره ساز و اکسیدهای آهن نیز انجام میشود.
در این مرحله نخست مواد با یکدیگر مبادله شده و ترکیبات خنثی یا بازی بین دانههای اکسیدهای آهن تشکیل میشوند در پایان مرحله پخت، سرد کردن گندله داغ باید به گونهای انجام شود که ترک در آنها ایجاد نشود.
گندلهها دارای این ویژگیها هستند: توزیع یکنواخت ابعاد بهطور عمده از ۹ تا ۱۶ میلیمتر، تخلخل زیاد و یکنواخت ۲۵ تا ۳۰درصد، ترکیب کانیشناختی یکنواخت به شکل هماتیت یا ترکیبات هماتیتدار احیاشونده، استحکام مکانیکی زیاد و یکنواخت، مقاومت به سایش، استحکام مکانیکی کافی حتی در برابر تنش گرمایی در محیطهای احیاکننده و قابلیت چسبندگی کم. برای تبدیل کنسانتره آهن به گندله باید مراحل مختلفی مانند انتقال مواد خام، آسیاب و خردایش مواد اولیه، مخلوطسازی مواد اولیه، تولید گندله خام، کوره پخت گندله، غبارگیری، تامین آب خنککننده، انتقال محصول نهایی، سیستم تصفیه آب، تولید هوای فشرده و آزمایشگاه انجام شود.
.شکل ظاهری آهن اسفنجی بصورت قطعات کروی (گندله) متخلخل که دارای ظاهری اسفنجی می باشد که به همین دلیل به آن اهن اسفنجی می گویند. آهن اسفنجی دارای عیار بالای آهن بوده که امروزه با توجه به کمبود ضایعات آهن و افزایش قیمت آن و همچنین مشکلات زیست محیطی رواج بیشتری دارد.
عیار و میزان آهن موجود در sponge iron، بین ۸۴ الی ۹۵ درصد است، عیار بالای اهن اسفنجی موجب شده منبع مناسبی برای تولید آهن و فولاد است و همان طور که اشاره شد اهن اسفنجی از بازیافت کانی آهن طبیعی یا فرآوری شده که به دمای ذوب نرسیده است، حاصل می شود. احیا سنگ آهن در ایران اغلب با استفاده از فن آوری میدرکس انجام می شود.
در این فن آوری بصورت بی واسطه گندله سنگ آهن را با گازهای شکسته شده احیا می کنند. به این صورت که ابتدا گاز طبیعی وارد واحد شکست گاز (ریفرمر) می شود و بخاطر اثر حرارت وارد شده و وجود کاتالیزورهای مخصوص شکسته می شود و به H۲ و CO تفکیک می گردد. هیدروژن و مونوکسیدکربن آزاد شده وارد کوره احیاء شده و با اکسیژن موجود در گندله مذاب ترکیب و به این ترتیب سنگ آهن احیا می شود.
در این شیوه گندله سنگ آهن که عیار ۶۷% دارد احیا شده و اهن اسفنجی (گندله متخلخل) با متالیزاسیون Fe (نزدیک ۹۲ درجه) تولید می گردد. محصولی که در واحد احیاء تولید می شود قسمت خنک کاری در کوره را طی نمی کند و با دمای در نزدیک به ۶۰۰ درجه سانتی گراد به وسیله سیستم انتقال مواد ویژه به قسمت فولادسازی برای شارژ مستقیم کوره منتقل می شود.به احیای مستقیم سنگ آهن DRI نیز گویند.
اهن اسفنجی پس از ذوب و احیا در فولاد سازی، در فرآیند ریخته گری به سه شکل اسلب (تختال)، بیلت( شمش) و میلگرد کاربرد دارند. اکنون حدود ۵% از فولاد جهان از اهن اسفنجی (DRI) به دست می آید و این روند در حال افزایش می باشد. گندله ترکیبی از آهن است که از تغلیظ سنگ آهن (کنتسانتره ) تولید می گردد. مقدار گندله استفاده شده در تولید DRI به ازای هر تن محصول نزدیک به ۴۵/۱ تن می باشد.
شایان ذکر است که انتخاب روش احیای مستقیم سنگ آهن، به مکان قرارگیری کارخانه تولیدکننده و منابع موجود در دسترس بستگی دارد. مثلاً در ایران، با توجه به منابع غنی گازی، انتخاب منابع گازی، انتخابی منطقی تر است و گاز بعنوان ماده احیا کننده کاربرد دارد. همانگونه که اطلاع دارید، بکاربردن منابع زغال سنگ برای احیاسازی، مشکلات آلودگی هوا را نیز به دنبال دارد و همچنین معادن آن به سهولت در دسترس قرار ندارند. اما هم اکنون بزرگترین تولیدکننده اهن اسفنجی در دنیا، کشور هندوستان است که با تکیه برمنابع زغال سنگ به احیای سنگ آهن می پردازد.
اهن اسفنجی جایگزین مناسبی برای ضایعات آهن است در نتیجه می توان با استفاده از این ماده درصد بالایی از مواد اولیه برای فراهم آوردن ذوب مورد نیاز واحدهای فولادسازی را بجای بهره گیری از ضایعات، تهیه نمود.
یکی از مهم ترین کاربردهای آهن اسفنجی در کوره های القائی می باشد. در کوره های القائی ای امکان وجود دارد که نزدیک به ۵۰ درصد آهن اسفنجی را جایگزین قراضه نمود. البته این نکته را در نظر بگیرید که برای استفاده از آن در کوره القایی، به دانش فنی و تجربه نیاز می باشد. بعلاوه اهن اسفنجی تحول بزرگی در ریخته گری مداوم صنعت فولاد ایجاد نموده است.
بریکت همان آهن اسفنجی یا DRI می باشد. با این تفاوت که در زمان تولید، بصورت فشرده شکل گرفته و از نظر نوع و دمای فرآیند تولید به ۳ نوع ذیل تولید می شود لذا انواع بریکت:بریکت گرم آهن اسفنجی، بریکت نرمه آهن اسفنجی، بریکت سرد آهن اسفنجی نام دارند.
HBI شکل تغلیظ شده و فشرده DRI است که برای انبار کردن و حملونقل آسان طراحی شده است DRI را میتوان در کارخانهها و واحدهای فولادسازی که در آنجا در واحدهای احیا در کنار واحد فولادسازیها صورت میپذیرد استفاده کرد.
DRI در جهان یک ماده شارژ کاملا خالص و مرغوب محسوب میشود بریکت آهن اسفنجی محصولی است که در فرآیند بریکت سازی از آهن اسفنجی تولید شده و در بسیاری از واحدهای فولادسازی دنیا مورد استفاده قرار می گیرد. فرآیند بریکت سازی آهن اسفنجی با توجه به دمای آهن اسفنجی ورودی به ماشین بریکت زنی، به دو گروه بریکت سازی سرد و بریکتسازی گرم تقسیم بندی می شود.
در فرآیند بریکت سازی سرد، مواد ورودی در دمای محیط به ماشین بریکتزنی وارد میشوند. در این فرآیند با توجه به نوع مواد ورودی به ماشین بریکتزنی، دو نوع محصول شناخته شده است. که عبارتند از بریکت نرمه آهن اسفنجی و بریکت سرد آهن اسفنجی.
بریکت گرم آهن اسفنجی (HBI) محصولی است که در فرآیند بریکتسازی از آهن اسفنجی گرم (HDRI) و در دمای بیش از 650 درجه سانتی گراد تولید میشود. این نوع بریکت شناخته شده ترین محصول جهت حمل و نقل آسان و ایمن آهن اسفنجی در سطح جهان به شمار می رود.
شمش فولادی اولین محصول قابل حمل و جابهجایی به دست آمده از فرایندهای فولادسازی (پس از استخراج آهن و تولید فولاد خام) است که بهصورت جامد و در ابعاد قابل حمل میباشد. در حقیقت فرایند شمش سازی یکی از فرایندهای میانی نورد فولادها است که مادهی اولیهی صنایع پاییندستی محسوب میشوند. شمش سازی، در اثر انجماد فلز مذاب در قالب انجام میشود و چندین هدف را دنبال میکند.
شمش فولادی (ingot) قطعاتی مستطیلی بوده که اغلب سطح مقطع آنها به دلیل قالبگیری دستی، سهولت در خارج کردن از قالب و حمل و نقل آسان مطابق شکل 1 به صورت ذوزنقه بوده و طول هر شاخه حداکثر به دو متر میرسد. این محصول عموماً در کارگاههای کوچک تولید میگردد.
در صنایع بزرگ فولادی عموماً واژه شمش فولادی به انواع بلوم، بیلت یا اسلب اطلاق میگردد. همچنین شمشها دارای گریدهای مختلفی از جمله 3SP-5SP( استاندارد روسی)، St37-St52 (استاندارد DIN آلمان) است که با وجود درصدهای مختلف از عناصر گوناگون موجود در فولاد دارای خواص مکانیکی متفاوت مثل انعطافپذیری، خمش، کشش و پیچش بوده و کاربردهای متنوعی را میطلبد.
بیلت (Billet) یا شمشال یک نوع شمش فولادی با طول زیاد و سطح مقطع مربع و یا دایره دارد. اگر حداکثر عرض بیلت ۱۵ سانتیمتر و دارای سطح مقطع ۲۳۰ سانتی متر مربع باشد، بلوم (Bloom) یا شمشه را میتوان همان بیلتی دانست که عرضی بیشتر از ۱۵ سانتیمتر داشته و دارای سطح مقطع بزرگتری است مانند شکل 2. از این جهت این دو محصول در یک دسته طبقهبندی میشوند که به سه روش، کوره بلند، احیاء مستقیم و کوره تونلی احیاو استخراج می شوند.
با این عناوین مطالب به نظر مآید صنعت فولادی انقدر عظیم و گسترده است که هرچه در تولیدات جانبی آن تلاش شود هنوز هم جایی برای حرف داشته باشند لذا استان کرمان که بهشت معادن، پایتخت طلای سبز نام گرفته است امیدواریم به زودی نام بام فولادی را هم به خود اختصاص دهد.