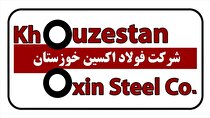
نویسنده: حسین عزیز طائمه – طراح پلنت های احیا مستقیم
می متالز - در طی دوره های مختلف صنعت سبز و دوست دار محیط زیست تعابیر مختلفی داشته اند. در گذشته ای نه چندان دور با ایجاد فضای سبز در محیط اطراف صنایع، سبز بودن آن صنعت را معرفی می کردند. هر چند ایجاد فضای سبز پسندیده بود، اما این طرح ها بیش تر ظواهر را مورد نظر قرار می دادند. بعدها با بهینه سازی مصارف انرژی و بالا بردن بازدهی ها، کاهش مصرف سوخت و جلوگیری از اتلاف انرژی در نظر گرفته شد. در حال حاضر پلنت های صنعتی به روز شده تا حد ممکن در نقطه بهینه کار می کنند و از این منظر پتانسیل آن چنان زیادی برای کاهش آلودگی های محیط زیستی ندارند. شاید هیچ وقت مانند امروز تعریف دقیق و واضحی از صنعت سبز در اختیار نداشته ایم. در سال ۲۰۱۵ توافق نامه پاریس با اجماع جهانی تصویب شد و در سال ۲۰۱۶ امضا گردید. مطابق با این توافق نامه مقرر شد که با کاهش گازهای گلخانه ای افزایش دمای زمین تا سال ۲۰۵۰ در مقایسه با پیش از عصر صنعتی شدن کم تر از ۲ درجه سانتی گراد و مطلوب تر ۱.۵ درجه سانتی گراد باشد.
بر این اساس کاهش ۸۰ تا ۹۵ درصدی گازهای گلخانه ای در صنایع مختلف مورد نظر قرار گرفته است تا اهداف این توافق نامه قابل حصول باشند. این تعریف که مبنای آن کاهش گازهای گلخانه ای است ضرورتا افزایش بازدهی واحدهای عملیاتی و عدم استفاده از سوخت های فسیلی را در خود جای داده است.
پنج گاز گلخانه ای عمده را میتوان به صورت زیر بیان کرد:
گاز دی اکسیدکربن حدود ۷۶% از گازهای گلخانه ای منتشر شده توسط فعالیت های انسانی را شامل می شود ومدت زمان بسیار طولانی در اتمسفر باقی می ماند. حدود چهل درصد از آن تا یک صد سال و بیست درصد تا حدود هزار سال و ده درصد از آن تا حدود ده هزار سال پس از انتشار در جَو حفظ می شود.
ماندگاری متان در اتمسفر نسبت به دی اکسیدکربن بسیار کم تر است، اما با وزن یکسان اثر گلخانه ای بسیار قوی تری دارد. تاثیر آن بر گرمایش جهانی حدود ۲۵ برابر دی اکسید کربن در دوره صدساله است. این گاز حدود ۱۶% از گازهای گلخانه ای منتشر شده توسط فعالیت های انسانی را شامل می شود.
تاثیر اکسید نیتروژن بر گرمایش جهانی حدود ۳۰۰ برابر دی اکسید کربن در دوره صدساله است. ماندگاری این گاز در اتمسفر کمی بیش تر از صد سال است. این گاز حدود ۶% از گازهای گلخانه ای منتشر شده توسط فعالیت های انسانی را شامل می شود.
چهار دسته اصلی از گازهای فلوئوردار شامل هیدروفلوئوروکربن ها، پرفلوئوروکربن ها، هگزا فلوراید گوگرد و تری فلوراید نیتروژن می شوند. این گازها حدود ۲% از گازهای گلخانه ای منتشر شده توسط فعالیت های انسانی را شامل می شوند، اما تاثیر آنها بر گرمایش جهانی و ماندگاری آنها در اتمسفر هزاران برابر است.
بخار آب فراوان ترین گاز گلخانه ای است، اما تغییرات آن در اتمسفر به فعالیت های انسانی مرتبط نیست.
مطابق با توافق نامه پاریس هر کدام از صنایع مختلف با توجه به گازهای گلخانه ای عمده منتشر شده در آن صنعت، اهداف خود را تعیین و برای رسیدن به آن تلاش می کنند. گاز گلخانه ای اصلی منتشر شده در فرآیندهای زنجیره فولاد، دی اکسید کربن است. این گاز هم در طی استفاده از منابع فسیلی به عنوان سوخت و هم در طی فرآیندهای اصلی تولید محصولات و هم حاصل از فرآیند تولید برق استفاده شده در تجهیزات می باشد. علاوه بر این مراحل جانبی مانند نقل و انتقالات مواد اولیه و محصولات نیز نباید از نظر دور بمانند. بر این اساس صنعت فولادسازی کاهش ۸۰ تا ۹۵ درصدی دی اکسید کربن را به عنوان یک هدف مشخص برای رسیدن به فولاد سبز برای خود تعریف کرده است. همان طورکه قبلا اشاره شد بیش تر کارخانه های به روزشده حداکثر بهینه سازی را در فرآیندهای جاری اعمال کرده اند و پیش بینی می شود که با انجام اصلاحات و بهینه سازی های بیش تر حداکثر به پانزده درصد کاهش بیش تر در انتشار دی اکسیدکربن دست بیابند.
صنعت فولاد عامل انتشار تقریبا ۳۰ درصد از گاز دی اکسیدکربن صنعتی جهان و حدود ۹ درصد از کل دی اکسیدکربن است. اگر فقط اروپا را در نظر بگیریم، ۳ درصد از کل انتشار دی اکسیدکربن و ۲۲ درصد از انتشار دی اکسیدکربن صنعتی به صنایع فولادی اختصاص دارد.
تولید فولاد در جهان از طریق دو مسیر مختلف انجام می شود. مسیر اول که با استفاده از زغال/کک انجام می شود شامل فرآیند های کوره بلند/کوره اکسیژن پایه است. در حال حاضر بیش از ۵۸% از فولاد اروپا به این روش تولید می شود. مسیر دومِ فولادسازی استفاده از احیامستقیم و کوره قوس الکتریکی است. این روش در مناطقی انجام می شود که دسترسی به منابع گاز طبیعی مهیا است. علاوه بر این استفاده از قراضه و ذوب آن در کوره قوس الکتریکی در کشورهای صنعتی که به اندازه کافی قراضه در اختیار دارند نیز مسیر معمول است. در حال حاضر حدود ۴۲% از فولاد اروپا توسط روش ذوب قراضه تولید می شود.
تولید فولاد به روش کوره بلند باعث انتشار حدود ۲ تن دی اکسیدکربن به ازای هر تن فولاد می شود، در حالی که استفاده از قراضه در کوره قوس الکتریکی باعث انتشار مقدار دی اکسید کربن کم تر از ۵۰۰ کیلوگرم به ازای هر تن فولاد می گردد. باید در نظر داشت که مسیر کامل احیامستقیم-کوره قوس الکتریکی به ازای هر تن فولاد حدودا کم تر از یک تن دی اکسیدکربن منتشر می کند.
کاهش بیش تر انتشار دی اکسیدکربن و رسیدن به فولاد سبز با هدف کاهش بیش از هشتاد درصدی دی اکسید کربن با تکنولوژی هایی که به طور معمول در حال حاضر استفاده می شود امکان پذیر نیست. برای نیل به این هدف روش های مختلفی متصور است. به طورکلی این روش ها به دو دسته اصلی تقسیم می شوند: اول جذب و ذخیره سازی دی اکسیدکربن به همراه استفاده هوشمند از کربن. دوم جایگزینی کربن در کاربری های سوخت و گاز احیا کننده با سایر روش ها به منظور جلوگیری از تولید دی اکسیدکربن.
روش های مختلفی برای تولید فولاد سبز پیشنهاد شده است که بسیاری از آنها یا در مرحله پژوهش هستند و یا تجاری سازی آنها صرفه اقتصادی ندارد. از بین روش های مختلف پیشنهادی، احیا مستقیم با استفاده از عامل احیا کننده هیدروژن تقریبا مورد توافق قریب به اتفاق مجامع صنعتی فولادی قرار گرفته است. در این روش به دلیل استفاده از هیدروژن مطابق واکنش زیر محصول احیا مستقیم، بخار آب خواهد بود.
Fe۲O۳+۳H۲=>۲Fe+۳H۲O
در اکثر پلنت های احیا مستقیم فعلی گاز طبیعی به عنوان منبع تولید گاز احیا کننده به کار گرفته می شود و مطابق واکنش های زیر گازهای منوکسیدکربن و هیدروژن از ریفورمینگ گاز طبیعی به وجود می آید:
CH۴+CO۲=>۲CO+۲H۲ , CH۴+H۲O=>CO+۳H۲
سوال اصلی که تولید فولاد سبز با استفاده از هیدروژن با آن مواجه است روش تولید هیدروژن است. هیدروژن در حال حاضر غالبا با استفاده از ریفورمینگ گاز طبیعی با بخار آب انجام می شود. محصول حاصل از واکنش های کاتالیستی ریفورمینگ به رآکتور شیفت-گس هدایت می شود و در آنجا با تزریق بخار آب اضافی، واکنش به سمت تولید هیدروژن حرکت می کند. البته برای خالص سازی بیش تر، از برج های جذب برای ارائه هیدروژن خالص استفاده می گردد.
CO + H۲O => CO۲ + H۲
همانطورکه در واکنش های ریفورمینگ و نیز واکنش شیفت-گس مشاهده می شود، محصول شامل دی اکسیدکربن نیز است. به این دلیل هیدروژن تولید شده توسط ریفورمینگ با بخار آب به هیدروژن خاکستری نام گذاری شود تا این نام نشان دهنده سبز نبودن فرآیند تولید این هیدروژن باشد. البته اگر دی اکسیدکربن حاصل شده در طی فرآیند تولید هیدروژن به این روش، جذب و ذخیره سازی شود آنگاه هیدروژن تولیدی را با کد رنگی آبی معین می کنند. در حقیقت این کدهای رنگی نمایان گر فرآیند تولید هیدروژن و میزان دوست دار محیط زیست بودن آن است.
با در نظر گرفتن توضیحات فوق الذکر، هیدروژن تولید شده توسط روش ریفورمینگ گاز طبیعی کمکی به تولید فولاد سبز نمی کند. در حقیقت برای تولید فولاد سبز با هیدروژن باید از هیدروژن سبز استفاده گردد. چندین روش برای تولید هیدروژن سبز شناخته شده است که از بین آنها الکترولیز آب، روش مورد پذیرش و قابل صنعتی سازی در مقیاس های مورد نیاز برای فولادسازی شناخته شده است.
اگر در فرآیند احیا مستقیم بخواهیم کاملا از هیدروژن استفاده کنیم حدودا هشتصد مترمکعب به ازای هر تن آهن اسفنجی هیدروژن مورد نیاز است که این مقدار هم برای استفاده به عنوان گاز احیا کننده و هم به عنوان سوخت مورد نیاز برای گرمایش مورد نیاز است.
پژوهش های مختلف در زمینه احیا مستقیم با هیدروژن انجام شده است و استفاده از آهن اسفنجی بدون کربن را در کوره قوس الکتریکی ممکن دانسته است، اما با این حال برای تنظیم میزان کربن مورد نیاز در آهن اسفنجی در حدود ۱.۵% که نیاز فولاد سازی را پوشش می دهد می توان از پنجاه مترمکعب گاز طبیعی به ازای هر تن محصول استفاده کرد.
برای تولید هیدروژن به روش الکترولیز آب با توجه به بازدهی فرآیند حدود پنجاه تا شصت کیلووات ساعت برق به ازای هر کیلوگرم هیدروژن مورد نیاز است. در بهترین حالت مقدار برق مورد نیاز برای تولید هیدروژن مورد نیاز برای هر تن آهن اسفنجی حدود ۲۵۰۰ کیلووات ساعت است. با در نظر گرفتن برق مصرفی پلنت های احیا مستقیم فعلی که حدود ۱۲۰ کیلووات ساعت به ازای هر تن آهن اسفنجی است، می توان میزان بسیار زیاد برق مصرفی در این فرآیند را ملاحظه کرد. البته قابل ذکر است که تنها در صورتی فولاد تولید شده با استفاده از هیدروژن حاصل از الکترولیز آب، سبز می باشد که برق مورد نیاز برای آن از انرژی های تجدید پذیر مانند باد و انرژی خورشیدی و ... تولید شده باشد.
البته برق مصرفی در کوره قوس الکتریکی به ازای هر تن فولاد خام و با توجه به نسبت قراضه به آهن اسفنجی که تا حدود ۶۵۰ کیلووات ساعت می رسد نیز باید مورد توجه قرار بگیرد.
در حال حاضر میزان انتشار گاز دی اکسید کربن در پلنت های احیا مستقیم بر مبنای گاز طبیعی حدود ۴۵۰ کیلوگرم به ازای هر تن آهن اسفنجی است. جایگزین کردن گاز طبیعی با هیدروژن میزان انتشار دی اکسیدکربن در پلنت احیا مستقیم را بیش از ده برابر کاهش می دهد.
با توجه به هدف گذاری های انجام شده بر طبق توافق نامه پاریس برای کاهش بیش از هشتاد درصدی میزان انتشار گاز دی-اکسید کربن در صنعت فولاد و با توجه به تکنولوژی های موجود، از میان مسیرهای فعلی برای تولید فولاد سبز، مسیر ارجح احیا مستقیم با هیدروژن و به دنبال آن استفاده از کوره قوس الکتریکی است. هم چنین با در نظر گرفتن تکنولوژی های موجود برای تولید هیدروژن، تکنولوژی مناسب برای تولید هیدروژن مورد نیاز برای فولاد سبز، الکترولیز آب با استفاده از انرژی الکتریسیته حاصل از منابع تجدیدپذیر مانند باد و خورشید است. مشکلی که در این راستا صنعت فولاد با آن مواجه است تامین برق بسیار زیاد مورد نیاز این فرآیندها است. در حال حاضر کشورهای اروپایی با در نظر گرفتن تمام این مسائل برای تولید ۲۵ میلیون تن فولاد سبز تا چند سال آینده هدف گذاری کرده اند. اما هنوز پلنت های احیا مستقیم که در ایران در حال برگزاری مناقصه و مراحل اولیه هستند، هیچ گونه نگاهی به آینده و کاهش انتشار دی اکسیدکربن ندارند. بدیهی است مالیات هایی که در آینده بر روی انتشار دی اکسیدکربن در نظر گرفته خواهد شد، بسیاری از فولادسازی های غیر سبز را با معضلات پیچیده ای مواجه خواهد کرد.