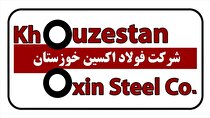
به گزارش میمتالز، در صنعت آهن و فولاد، انرژی گرمایی زیادی تلف میشود. مطالعات اثبات کرده بخش عمدهای از این اتلاف انرژی حاصل از سرباره تولیدی است. جایگزین کردن فرایند گرانوله کردن (اتمیزه کردن) خشک بهجای گرانوله کردن تَر سرباره میتواند یک گام اساسی در کاهش مصرف انرژی و حتی بازیابی انرژی مصرفی باشد.
صنعت آهن و فولاد بهعنوان صنعت مادر، نقشی حیاتی در اقتصاد هر کشور ایفا میکند. با توجه به اینکه صنعت فولاد یکی از اصلیترین مصرفکنندههای انرژی در میان صنایع مختلف در جهان است، هر راهکاری که با هدف ذخیرهسازی انرژی مصرفی و کاهش تلفات آن در صنعت فولاد پیشنهاد گردد، میتواند به کاهش مصرف انرژی و خطرات زیستمحیطی ناشی از آن کمک شایانی کند. یکی از ایدههایی که فولادسازان دنیا بر آن تمرکز کردهاند، بازیابی انرژی حرارتی تلفشده در فرایند تولید فولاد است. بر همین اساس، توسعه فناوریهای بازیابی انرژی گرمایی در بخشهای مختلف تولید فولاد به یک موضوع پرطرفدار برای تولیدکنندگان تبدیل شده است.
دادههای جمعآوریشده اثبات میکند انرژی حرارتی تلفشده با درجه حرارت بالا در صنعت آهن و فولاد، عموماً از سرباره مذاب و گازهای خروجی نشئت میگیرد. گزارش شده است که سرباره تولیدی کوره بلند با دمای حدوداً C ۱۵۰۰ تقریباً ۱۰درصد از کل انرژی تلفشده در صنعت فولاد و ۳۵ درصد از انرژی گرمایی تلفشده با دمای بالا در این صنعت را در برمیگیرد. بااینحال، این منبع حرارتی تلفشده از چرخه بازیابی خوبی در صنعت فولاد به دلیل فقدان فناوریهای پربازده بازیابی انرژی برخوردار نیست. گزارش شده است که سالانه حدود ۴۰۰ میلیون تن سرباره کوره بلند با دمای بالا در سرتاسر جهان تولید میشود. در حال حاضر، گرانوله کردن سرباره ((Granulated Blast Furnace Slag (GBFS) با روشهای گرانوله کردن آبی (تَر) یکی از روشهای رایج در سرد کردن سرباره مذاب و تبدیل آن به یک محصول جانبی برای کاربردهای مختلف است. بااینحال، این روش مستلزم استفاده از مقدار زیادی آب است؛ بهگونهای که برای خنک کردن یک تن سرباره به بیش از ۸ تن آب نیاز است. از سویی دیگر، در حال حاضر هیچ روشی در مقیاس صنعتی برای بازیابی انرژی گرمایی باقیمانده در سرباره (حرارت بالای آن) که حدوداً ۱.۷ گیگاژول به ازای هر تن است، وجود ندارد و این منبع انرژی گرانبها به هدر میرود (این مقدار انرژی میتواند برای ماهها سوخت یک خودرو الکتریکی را تأمین کند). از طرفی، استفاده از آب برای تولید محصول گرانوله از سرباره و مجدداً تصفیه آن بهخودیخود نیز میزان زیادی انرژی اضافی به سیستم فولادسازی تحمیل میکند.
در سالهای اخیر، فولادسازان مختلف بر اجرایی کردن و توسعه فناوری گرانوله کردن خشک سرباره مذاب با هوا، بازیابی بالای انرژی و تولید سرباره با کیفیت بهعنوان یک محصول جانبی تمرکز کردهاند. برای نخستین بار، شرکت فولاد فوست آلپیته (Voestalpine) در اتریش با راهاندازی یک واحد نیمهصنعتی، امکانسنجی گرانوله کردن سرباره با هوا را اثبات کرد. اساس کار در فرایند اتمیزه کردن سرباره با هوا بسیار آسان است. در شکل ۱ شماتیکی از فرایند گرانوله کردن خشک سرباره با هوا برای کارخانههای با جریان سرباره کوره بلند t/min ۲ نشان داده شده است.
در این روش، سرباره از سوراخ تعبیهشده در کوره بلند، بهطور مستقیم به گرانولاتور تغذیه میشود. با ورود سرباره مذاب به گرانولاتور، سرباره به یک قطعه فنجانی شکل در حال چرخش تعبیهشده در مرکز برخورد میکند و با فشار ناشی از نیروی گریز از مرکز به اطراف پرتاب میشود. قطرات مذاب در این شرایط اندازهای در حدود mm ۵/۰ تا mm ۳ دارند و با فشار به دیوارههای شیبدار کناری که توسط آب در حال خنک شدن است، برخورد میکنند. این قطرات بهصورت جامد روی بستری از گرانول سیال فرود میآیند و با کمک هوا خنک میشوند. در این موقعیت، هوای زیادی از پایین وارد و از بالا با دمای حدوداً C ۵۰۰ خارج میگردد و توسط غبارگیرها جمعآوری میشود تا مجدداً این هوای گرم در بخشی از صنعت فولاد مورد استفاده قرار گیرد. در پایان، محصول نهایی با نوار نقاله از ته محفظه خارج میشود. شکل ۲ نیز تصویر دیسک فنجانیشکل در حال چرخش که سرباره مذاب را به اطراف پرتاب میکند نشان میدهد.
اکنون، محققین پریمتالز (Primetals) بر روی راهاندازی چندین سیستم تصویربرداری برای نظارت، کنترل و ارزیابی فرایند دانهبندی جهت امکان بهینهسازی سرعت چرخش فنجان دوار و تطبیق دینامیکی آنها با پارامترهایی مانند جریان سرباره و دما با هدف ارتقای عملکرد فرایند و کیفیت محصول تمرکز کردهاند. پارامتر کلیدی در کیفیت سرباره، محتوای فاز شیشهای آن است که باید بیش از ۹۵ درصد باشد تا بهعنوان یک محصول جانبی بتواند در صنایع دیگر نظیر صنعت سیمان مورد استفاده قرار گیرد. این موضوع هنوز بهعنوان یک چالش برای فرایند گرانوله کردن خشک شناخته میشود. استفاده از روش خنک کردن با آب به دلیل بالا بودن نرخ سرمایش، بهراحتی امکان دستیابی به مقدار بالای فاز شیشهای را فراهم میکند. با وجود این، آنالیز نتایج نشان داد که گرانوله کردن خشک بهینه نیز میتواند محتوای فاز شیشهای در سرباره را در محدوده ۸۴ تا ۹۷ درصد حفظ کند که نتیجه قابلقبولی است. شکل ۳ محصول نهایی فرایند گرانوله کردن خشک را که حاوی مقدار فاز شیشهای خوبی است نشان میدهد که میتواند بهعنوان یک محصول جانبی قابلاتکا استفاده شود.
تخمین زده شده است که اگر تنها نیمی از کورههای بلندی که امروزه در حال کار است، روش گرانوله کردن خشک را جایگزین گرانوله کردن تَر کنند، انرژی صرفهجویی و بازیابیشده برای تأمین انرژی پایدار بیش از ۳.۵ میلیون خانوار در تمام سال کافی است. بهعنوان مثالی دیگر، انرژی حاصل از سرباره که اکنون تقریباً بهطور کامل تلف میشود، برای تأمین انرژی ۶.۵ میلیون خودروی الکتریکی با فرض مسافت پیمودهشده معمولی کافی است. همچنین، این ایده کاهش ۸ میلیون تن تنی انتشار گازهای گلخانهای در سال را نیز به دنبال خواهد داشت. ازاینرو، محققین صنعت فولاد متقاعد شدهاند که روش گرانوله کردن خشک سرباره گامی مهم بهسوی آینده سبز فولادسازی خواهد بود.