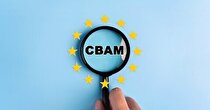
فرهاد فرمانی - مدیرعامل و عضو هیات مدیره شرکت وریا طرح پارس - در گفت و گوی اختصاصی با خبرنگاران "می متالز" با شکیبایی و دقت به بررسی پروژه ها و وضعیت صنعت فولاد کشور پرداخته که در ادامه و در ذیل آن را خواهید خواند:
با تشکر از زمانی که در اختیار من گذاشتید، باید بگویم من از ابتدای شروع ساخت فولاد مبارکه تا زمان بهره برداری در این شرکت فعالیت داشته و بعد از آن حدود 14 سال در سمت مدیر عاملی شرکت ایریتک در اجرای متعدد پروژه های توسعه ای کشور مشارکت کرده ام. در سال 89 بعد از اتمام مسئولیتم درایریتک بر پایه تجارب و اطلاعاتی که کسب کرده بودم به اتفاق سایرهمکارانی که از ایریتک خارج شده و تجارب ارزنده وسابقه خدمات متعدد و طولانی در ایریتک داشتند، اقدام به تاسیس شرکت وریا طرح پارس نمودیم. به دلیل شناختی که گروهمان از مهندسی و صنعت داشت، تمرکز بر توسعه مهندسی تکنولوژی گذاشتیم. در زمینه مهندسی عمومی ومشاوره شرکت های زیادی در حال فعالیت هستند و ما سعی کردیم در زمینه مهندسی پایه وصنعتی بیشتر فعالیت داشته باشیم. بعلاوه بخشی از خدماتمان را صرف پشتیبانی، ایجاد و پیاده سازی ساختارهای جدید شرکت های پیمانکار عمومی وشرکت های مهندسی درهنگام تاسیس نمودیم.
هم اکنون شرکت وریا طرح پارس به عنوان یک شرکت "طراحی و مهندسی " و" مدیریت طرح "(MC) شناخته می شود. عمدتاً در زمینه صنایع متالورژی و بلاخص در بخش فولاد متمرکز می باشد. یکی از خلاء های مهندسی که در صنایع ما احساس می شود بحث جانمایی و طراحی زیر ساخت مجموعه های بزرگ صنعتی است. شرکت سعی نموده تجارب کارشناسان کشور را در مهندسی و استقرار مناطق و مجتمع های صنعتی بکار گرفته واجرایی نماید. اولین پروژه ما طرح جامع معدن گل گهر بود. این منطقه صنعتی در بر گیرنده مجموعه ای از شرکت های صنعتی تولیدی با هویت حقوقی مختلف و 6 معدن بزرگ سنگ آهن با بهره برداران وهویت حقوقی متفاوت که بخش هایی از آن در حال اجرا بوده بویژه پیاده سازی مجموعه طرح های فولاد سازی با ظرفیت 5 میلیون تن شامل بیلت و ورق که میبایستی استقرار آنها درکنار معادن با هم هماهنگ باشند. از طرفی به دلیل وجود زیرساخت های مشترک نیز به جانمایی دقیق وهماهنگ نیاز داشت. بنابراین شرکت با سازماندهی مجموعه ای از کارشناسان داخلی، دانشگاهی و خارجی طرحی به عنوان طرح جامع گل گهر برای افق1404به آن مجموعه ارایه نمود. زمان طراحی و اجرای مطالعه پروژه حدود 2 سال و خدمات بعد ازتهیه طرح جهت خدمات پیاده سازی 2سال دیگر ادامه داشت. با توجه به نتایج خوب طرح ، سازمان ایمیدرو جلساتی برای انتقال تجارب بدست آمده از این طرح جهت مشاورین طرح معدن سنگان به منظور مشابه پردازی ترتیب داد. درحال حاضر نیز شرکت مشغول مطالعه طرح جامع توسعه فولاد خراسان در نیشابور در یک افق 20 ساله می باشد. تهیه طراحی های اساسی و تفصیلی پروژه های صنعتی و زیرساخت مرتبط و مدیریت طرح (MC)پروژه های صنعتی نیز از عمده فعالیت های شرکت می باشد.
اردکان دارای مطالعه و طرح اولیه بلند مدتی می باشد و برهمین اساس طرح های صنعتی آن بتدریج استقراریافته است. شرکت چادرملو طراحی و ساخت وراه اندازی یک واحد مگا مدول را به کنسرسیوم پامیدکو / CPG واگذار کرده است. کنسرسیوم از این شرکت درخواست انجام طراحی و خدمات مهندسی خرید و پروسس گارانتی طرح را نمود.
در خواست کنسرسیوم مشتمل بر طراحی یک کارخانه تولید فولاد ازطریق احیای مستقیم با شارژگرم آهن اسفنجی به کوره های ذوب بود که اولین تجربه از این نوع تکنولوژی در ایران می باشد. ظرفیت کارخانه 1.7 میلیون تن است. در واقع ظرفیت عملکردی مورد انتظار کارفرما 1.5 میلیون تن در سال است اما با پیش بینی هایی که در زمینه تزریق گاز اکسیژن نموده ایم ظرفیت کارخانه می تواند به 1.7 میلیون تن برسد.
کل مهندسی در ایران انجام شده است. در بخش مهندسی شرکت سعی کرد نظر Kobe Steel را که دارنده لیسانس احیاء مستقیم میدرکس است جلب نماید تا بتوانیم یک واحد احیای مستقیم مگامدول با شارژگرم آهن اسفنجی برای فولاد سازی طراحی کنیم. Kobe Steel موافقت کرد و شرکت از طریق ایریتک یک Sublicense دریافت کرد زیرا فقط شرکت MMTE و IRITEC دارای انحصار لیسانس Kobe Steel هستند. طراحی کل این پروژه توسط شرکت وریا طرح پارس صورت گرفته است و performance و Process Guarantee هم به عهده این شرکت است اما پیمانکار عمومی کنسرسیوم CPG و Pamidco تامین مگا مدول را عهده دار می باشد.
در بخش مهندسی حدود 85 درصد کارانجام شده است و در بخش عملیاتی نیز کنسرسیوم همه سفارشات خرید را گذاشته و در حال اجرا است. بخشی از سفارشات از داخل کشورتهیه شده و برخی نیز از خارج از کشورتامین شده که در حال حمل و تحویل به ایران است. در ماه آینده همکاران ما به ایتالیا می روند تا سیستم کنترل را تست کرده و تحویل بگیرند. پیش بینی می شود در سال آینده قبل از پایان نیمه اول سال پروژه قابل راه اندازی باشد.
در ایران به بحث تامین مالی و نقدینگی (Cash Flow) پروژه بخصوص در بخش داخل اهمیت چندانی داده نمی شود. در واقع اگر کارفرما به تامین به موقع منابع مالی پروژه اهمیت دهد، می تواند به انجام بموقع پروژه بسیار کمک کند. برای شرکت های خارجی یک مکانیزم فاینانس و یا LC گشوده می شود که جریان پرداخت های مالی به صورت مطمئنی شکل می گیرد و شرکت های خارجی در مقاطعی که کار خود را به انجام می رسانند امکان دریافت مطمئن پول را خواهند داشت. اما در بخش داخلی هیچ گونه تضمینی برای پرداخت به موقع پول داده نمی شود ودر صورت عدول کارفرما از پرداخت منظم صورتحساب ها ساختار برنامه و فعالیت های پیمانکار به هم می ریزد. پیمانکاران نمی توانند طبق برنامه زمان بندی مد نظر فعالیت های خود را به پایان برسانند.
در پروژه اردکان پیش بینی می شود پروژه حدود چهارسال بطول انجامد اگر چه در کشوراین دوره زمانی احداث کارخانه معمول بوده اما بدلیل همزمانی اجرای این پروژه با اجرای پروژه ذوب توسط کارفرما تمرکزتخصیص منابع در اولویت به واحد فولاد سازی بدلیل نزدیکی زمان راه اندازی داده شد. خوشبختانه با راه اندازی فولادسازی طرح احیا نیز در مرکز توجه کامل کارفرما قرار گرفته است.
در حالی که همواره سعی نموده ایم که کارهای مهندسی را به موقع پیش ببریم. اما تاخیر در ارسال برخی از سفارشات و خرید باعث تاخیر در نرسیدن اطلاعات به دست مهندسی و عدم تکمیل به موقع آن می شود. بنابراین همه چیز به صورت یک زنجیر به هم وابسته است. البته مشکلات دیگری نیز وجود دارد مانند ضعف ساختاری، تجارب و مهارت های نیروی انسانی، امکانات و روند اداری که در ایران وجود دارد نیز در اجراو تاخیر ها ی پروژه ها تاثیر گذار است. در هر حال اگر چه کارفرمایان با ارجاع کار به پیمانکاران ایرانی با مشکلاتی مواجه می شوند اما این هزینه کرد رفته رفته باعث افزایش دانش و تجارب پیمانکاران و سازند گی آنها خواهد شد نتیجتا" کشور از توانمندی بالاتری برخوردار خواهد شد.
شرکت معدنی صنعتی چادرملو دارای امکانات استخراج سنگ آهن و تولید کنسانتره در کنار معدن بوده ودر اردکان نیزیک واحد گندله سازی در حال تولید دارد، بنابراین به منظورتولید ارزش افزوده بیشتر و توسعه امکاناتش ، با توجه به محدودیت توسه افقی به توسعه عمودی پرداخته و در ابتدا تصمیم به احداث یک واحد ذوب گرفته شده که این واحد هم اکنون راه اندازی و احداث شده است. سپس به خلا بین تولید گندله سازی و مواد اولیه مورد نیاز فولاد سازی - یعنی آهن اسفنجی - مورد توجه قرارگرفته و تصمیم به احداث یک واحد تولید آهن اسفنجی شده است که هم اکنون در دست احداث می باشد. از طرفی به دلیل اینکه شرکت های MMTE و ایریتک معتقد به انجام کار به صورت یکپارچهEPC بودند پروژه به آنها واگذار نشد. از کنسرسیومCPG و پامیدکو استفاده شد. زیرا تامین مالی پروژه نیز به صورت یکباره امکان پذیر نبود در بخش مهندسی نیز از شرکت وریا طرح پارس استفاده شد. شرکت نیز با کسب مجوز از کوبه استیل این کار را آغاز نموده است. این پروژه در نوع خود در ایران بی نظیر است زیرا به جای اینکه مانند کارخانه های قدیمی آهن اسفنجی بعد از تولید سرد و به فولادسازی انتقال داده شود محصول به صورت گرم اصطلاحا" شارژ گرم به واحد ذوب انتقال داده می شود.
خیر، HBI وقتی است که فولاد سازی در کنار پروژه قرار نداشته باشد. آهن اسفنجی را به صورت بریکت در آورده و به آن Hot Briquette گفته می شود. روش جدید بکار گرفته شده در اردکان در واقع HDRI و یا شارژ گرم می باشد. در پروژه های قدیم ما Cold Briquette داشتیم . اگر فولاد سازی در کنار واحد احیا استفرار یابد دیگر نیازی به بریکت کردن آهن اسفنجی نیست. می توان آهن اسفنجی را با دمای 600 درجه به واحد فولاد سازی انتقال داد. در این صورت انرژی لازم برای رساندن بریکت به این درجه حرارت را ذخیره کرده و ظرفیت تولید ذوب حدود 10 تا 15 درصد افزایش می یابد. سیکل معمول ذوب حدود 65 دقیقه است و در این روش نیاز به 56 تا 58 دقیقه برای تامین ذوب می باشد و این باعث سریعتر استارت خوردن ذوب بعدی می گردد. این تکنولوژی برای اولین بار در ایران در حال انجام است. البته MMTE درتوسعه آهن و فولاد گل گهرنیز این طراحی را انجام داده است اما در آن پروژه کارگاه فولادسازی آماده نیست و هنوز عملیاتی نگردیده است. در پروژه اردکان فولادسازی در دست بهره برداری بوده و به محض راه اندازی احیا عملیاتی می گردد.
در مجموع ممکن است هزینه های سرمایه گذاری اولیه(Capital Costs) حدود 10 درصد بالا برود اما با افزایش 10 تا 15 درصدی تولید طی هر سال این هزینه جبران می گردد. هزینه عمدتا" مربوط به نوار نقاله خاصی است که محصول گرم آهن اسفنجی را انتقال می دهد کمی پیچیده و گران تر از نوارهای معمول است. این نوار نقاله به صورت سقف بسته بوده و گازخنثی به روی مواد دمیده می شود تا بدون اکسیده شدن آهن اسفنجی گرم را انتقال دهد.
در عمان و همچنین در حدید عربستان این تکنولوژی بکارگرفته شده است. با وجود تعداد بسیار زیاد کارخانه ها ی احیا، در این زمینه تعداد کمی از واحد های خارجی از این تکنولوژی بهره می برند و در ایران نیز ما در ابتدای راه هستیم.
ببینید در ابتدا مشخصه ای که مورد نیاز هر کارخانه برای اجرای این تکنولوژی است قرار گرفتن واحد احیا در فاصله 100 متری واحد فولاد سازی است. اگر دراتصال به ورودی واحد فولاد سازی فضای خالی به فاصله 100 متری وجود داشته باشد امکان انجام گرفتن این کار وجود دارد. به عنوان مثال در مبارکه به علت نحوه قرار گرفتن مدول های احیا با فاصله زیاد از فولاد سازی که در مکان های متفاوتی می باشد امکان انتقال محصول گرم به این صورت به فولاد سازی میسر نمی باشد. در پروژه های جدید فولاد مبارکه نیز در این مورد مکانی در نظر گرفته نشده است. توصیه ما در پروژه های جدید همواره به اختصاص دادن فضایی در نزدیکی فولاد سازی به احیا بوده است. مشکل دیگری که ما در اردکان با آن مواجه بوده ایم کمبود آب است. سیستم برج های خنک کننده (Cooling Towers ) که در آن آب هنگام خنک سازی بخار می گردد باعث از دست رفتن بخشی از آب می شود. برای جلوگیری از این مشکل ما یک سیکل بسته سیستم خنک سازی آب با هوا Air Cooler طراحی کرده ایم که مصرف آب را به اندازه 50 درصد میزان مصرف کنونی کاهش داده ایم. در ایران این اولین بار است که اجرا می گردد. اخیرا Kobe Steel تکنولوژی های دیگری را نیز مطرح نموده و مدعی است که مصرف آب را به 40 درصد از میزان موجود کاهش می دهد البته در ایران هنوز مشتری برای این سیستم پیدا نکرده است. درقطر آب دریا را وارد واحد احیا کرده وبرای خنک سازی استفاده و دوباره به دریا برمی گردانند با این کار میزان آب مصرفی را به 30 درصد از میزان مصرف موجود رسانده اند. زیرا حجم بسیار زیادی آب وارد می شود و سیستم ها را خنک می کند بنابراین مصرف آب به میزان قابل توجهی کاهش می یابد. در پروژه های ایران که نزدیک دریا هستند مانند فولاد هرمزگان و یا کاوه امکان استفاده از این سیستم وجود دارد اما فعلا ازهمان سیستم Cooling Tower استفاده می کنند.
شرکت وریا طرح پارس در پروژه های دیگری مانند فولاد جهان آرا اروند که در خرمشهر واقع شده است نیز فعالیت دارد. در این پروژه جانمایی مجموعه صنعتی و طراحی زیر ساخت ها را انجام می دهیم. ظرفیت تولید این پروژه 1 میلیون و 400 هزار تن محصولات تخت فولادی (تختال یا Slab ) می باشد. طرح فولاد سازی آن توسط شرکت اسپانیایی Saralle در حال اجراست تایید طرح (Drawing Approval) و جانمایی به عهده ماست. بسته به منابع مالی موجود طرح توسعه می یابد. بدین ترتیب که ابتدا فولاد سازی عملیاتی و راه اندازی خواهد شد و آهن اسفنجی به عنوان مواد اولیه از بازار تهیه می گردد با افزایش منابع مالی توسعه احداث گندله سازی ،احیای مستقیم و نورد نیز انجام خواهد شد.
توسعه فولاد در ایران از مزیت های نسبی زیر برخوردار است :
مهمترین چالش توسعه فولاد کشور تامین منابع مالی است که بخش عمده آن بایستی از طریق فاینانس و بانک ها با پوشش شرکت های بیمه خارجی صورت پذیرد. در مقابل نیاز به شفاف سازی مکانیزم ها و بستر سازی داخلی جهت ارایه تضامین متقابل به تامین کنندگان منابع خارجی از جانب مقامات ذیربط در ایران برای بخش خصوصی می باشد. تامین نقدینگی مطمئن نظیر LC جهت پیمانکاران داخلی نیز در تسریع و انجام بموقع پروژه ها موثر می باشد.
توسعه طرح های های فولاد سازی نیز باید مبتنی بر بازار و تکنولوژی های روز باشد. در این صورت تکنولوژی های جدید وارد صنعت فولاد ما شده و تحولاتی در مدیریت و به کارگیری این تجهیزات به وجود خواهد آمد. برای کاهش هزینه ها و رقابتی شدن لاجرم از استفاده تکنولوژی نو می باشیم. تکنولوژی های ما سنتی هستند و باید بهبود وتوسعه یابند. بحث بعدی تحقیقات و آموزش است. پایداری و زیرساخت صنایع فولاد متاثر از تحقیقات و نوآوری خواهد بود که توسط خودمان باید ایجاد شود. سرمایه گذاری در این زمینه به ما امکان اداره صنایع خودمان را می دهد. البته ما هنوز در ابتدای راه هستیم و قدم های خوبی در این زمینه برداشته ایم.
در حال حاضرکارفرمایان با تمام توان بر روی مساله تولید متمرکز شده اند و میزان تولید حدود 20 میلیون تن رسیده است برای تحقق 55 میلیون تن در فاصله زمانی کمی که پیش بینی شده باید امکانات زیادی از داخل و خارج و منابع خارجی به کار گرفته شود تا به اهداف این برنامه دست یابیم. اگر شرایط تامین سرمایه گذاری از خارج در ایران حاصل نشود امکان توسعه تا سطح پیش بینی شده وجود نخواهد داشت زیرا منابع داخلی کفاف نمی دهد و تامین منابع خارجی نیز در گروشرایط بین المللی است که مشوق حضور بانک ها و شرکت های خارجی در ایران خواهد شد .
ما در مجموع دارای 60 نفر نیروی ثابت مستقیم هستیم که در دفتر تهران و خرمشهر و گل گهر فعالیت دارند به همین میزان نیز قرارداد با نیروهای نیمه وقت تخصصی خارج از سازمان داریم.
شرکت وریا طرح پارس در زمینه مهندسی و مدیریت طرحهای متالورژی فعال می باشد و متمرکز بر طرح ها و تکنولوژی های فلزات آهنی و غیر آهنی می باشد. در فولاد سازی، گندله سازی ونورد فعالیم، همچنین در مس وآلومینیوم آمادگی انجام فعالیت داریم .
شرکت در بخش فرآوری مواد معدنی یعنی کنستانتره به بعد فعال است . در معدن گل گهر در زمینه برنامه ریزی احداث واحد های کنستانتره و گندله و زیرساخت صنایع معدنی فعال می باشد بعلاوه در معدن گل گهر شرکت طراحی پایه جهت نوار نقاله ای بطول شش کیلومتربه منظورانتقال گندله به نقطه توزیع و فروش ارایه کرده است بطوریکه به جای حمل ونقل کامیونی پتانسیل انتقال 6 میلیون تن در سال گندله بصورت مکانیزه ایجاد شده و بدین ترتیب راندمان حمل ونقل در منطقه افزایش یافته است
دیدگاه بلند مدت: کشور ما برای پروژه های بزرگ صنعتی در بخش هائی به تکنولوژی خارجی وابسته است. رشد و توسعه نوآوری و تکنولوژی در گرو وجود بسترهای تحقیقاتی کاربردی، نمونه سازی، مهندسی و تولید انبوه هر محصول مورد نیاز می باشد. به لحاظ دستیابی به چنین توانمندی لازم است در کشوربرنامه ریزی و توجه به توسعه مراکز تحقیقاتی کاربردی و تبدیل ایده های نظری به کاربردی و انجام مهندسی شود.
این مهم برنامه ریزی، تامین منابع و ساختارهای مرتبط را می طلبد که در بلند مدت نتایج آن حاصل می شود. اجرای اصل واگذاری کل کار به شرکت های ایرانی و الزام این شرکت ها به استفاده از پتانسیل داخلی و تلفیق آن با تکنولوژی های روز فرآیند توانمند سازی شرکت های ایرانی را گسترش می دهد. در واقع بومی شدن مدیریت پروژه های احیای مستقیم در کشور همین مسیر را طی نموده است. در حال حاضر مدیریت، مهندسی و توزیع و تقسیم کار بین متخصصان داخلی و خارجی و و اجرا و ضمانت عملکردی کارخانه ها توسط شرکت های ایرانی انجام می شود.
در مقطع کنونی: با توجه به توانمندی خوبی که در سطح سازندگان و پیمانکاران داخلی ایجاده شده است شرکت ها ناگزیر از واردات تکنولوژی های روز و تلفیق آن با تکنولوژی و توانمندی داخلی هستند و بدین ترتیب بتدریج امکانات و توانمندی داخلی گسترش می یابد. در این راستا لازم است کارفرمایان و سرمایه گذاران بستر سازی کنند که شرکت های ایرانی مدیریت طرح ها و پروژه های صنعتی را در اختیار گرفته و این تلفیق با نهایت بکارگیری و توانمندی امکانات داخلی صورت پذیرد و یا حداقل در چهارچوب مشارکت ها و یا Joint Venture ها این مدیریت انجام شود تا توانمندی های داخلی توسعه یابد.
این خدمات قابلیت صادر کردن دارند اما چون بحث لیسانس و تکنولوژی تجربه شده روز مطرح است کمی پیچیده می باشد. مجوز استفاده از هر تکنولوژی توسط صاحب تکنولوژی به صورت منطقه ای است. به عنوان مثال Kobe فقط به دو شرکت در منطقه ایران لیسانس داده و همینطور در اروپا ، امریکا و ژاپن تعداد محدودی می توانند لیسانس داشته باشند. چنانچه برپایه تحقیقات کاربردی تکنولوژی توسط شرکت های داخلی توسعه یابد یقینا" قابل صادرات می باشد.
به عنوان عضو کوچکی از جامعه مهندسی کشور سعی بر توسعه خود جهت ایجاد توانمندی ارایه خدمات مهندسی اساسی طرح های صنعتی و مدیریت طرح ها داریم . یکی از ضعف های صنعت کشور ما نداشتن سازمان های مهندسی قوی است. علت آن هم عدم وجود بستر های مورد نیاز رشد این شرکت ها و عدم اهمیت و توجه کارفرمایان به امر مهندسی است. بنابراین شرکت های مهندسی درآمد موجهی نداشته و نیروهای آنها علیرغم کار آمدی از درآمد متناسبی برخوردار نیستند به همین دلیل دچار چالش و مشکل هستند. سازمان های مهندسی باید در کنار شرکت های EPC قرار گیرند تا بخشی از منابع حاصله ازتامین وخرید به مهندسی تعلق داده شده و باعث بهبود و توسعه مهندسی شود.