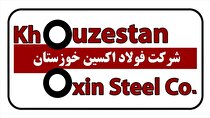
به گزارش میمتالز، از آنجا که پتانسیل کاهش دی اکسید کربن در فولادسازیهای فعلی کم است، برای رسیدن به این هدف استفاده از فناوریهای پیشرفته ضروری است. فولادسازیِ مبتنی بر هیدروژن یکی از راهکارهای تحقق فولادسازی بدون انتشار دی اکسید کربن است. بر این اساس احیا مستقیم بر پایه گاز طبیعی (N.G.) میتواند به عنوان پایهای برای اولین مرحله از این دوران گذار به کار گرفته شود. انعطاف پذیری زیاد این روش امکان افزایش تدریجی هیدروژن را فراهم میکند تا در بلند مدت، نهایتا این فرآیند فقط با هیدروژن خالص کار کند.
هیدروژن سادهترین و فراوانترین عنصر موجود بر روی زمین است و به راحتی با سایر عناصر شیمیایی ترکیب میشود و به عنوان بخشی از مواد دیگر مانند آب، هیدروکربنها و یا الکل یافت میشود. هیدروژن در مواد زیستی طبیعی) بقایا و مواد مشتق شده از موجودات زنده) نیز یافت میشود. به این دلیل که هیدروژن در طبیعت به صورت خالص وجود ندارد و از منابع دیگر به دست میآید و به عنوان حامل انرژی در نظر گرفته میشود نه منبع انرژی.
هیدروژن را میتوان از منابعی مانند گاز طبیعی و زغالسنگ، مواد زیستی طبیعی و با استفاده از منابع انرژی تجدیدناپذیر مانند سوختهای فسیلی، انرژی هستهای و یا منابع انرژی تجدیدپذیر مانند خورشید، باد، هیدروالکتریک یا انرژی حرارتی موجود در پوسته زمین تولید کرد. این تنوع منابع، هیدروژن را به یک حامل انرژی امیدبخش تبدیل میکند. امکان تولید هیدروژن با استفاده از منابع و فرایندهای مختلف یکی از جنبههای مورد توجه واقع شدن آن است.
هیدروژن از طریق فناوریهای مختلفی قابل دستیابی است؛ از جمله فرآیندهای حرارتی (ریفورمینگ گاز طبیعی، اکسیداسیون جزئی، ریفورمینگ مایعات مشتق شده از مواد زیستی و نیز گسیفیکیشن زغالسنگ)، الکترولیز (تجزیه آب با استفاده از منابع مختلف انرژی) و فتولیتیک (تفکیک آب با استفاده از نور خورشید از طریق بیولوژیکی و مواد الکتروشیمیایی). اما دو روش اصلی تهیه هیدروژن در حال حاضر استفاده از ریفورمینگ گاز طبیعی با بخار آب و نیز الکترولیز آب است.
در حال حاضر، کاربردهای اصلی هیدروژن در سراسر جهان شامل سنتز آمونیاک، پالایشگاههای شیمیایی و پتروشیمی و تولید متانول است. تولید سالیانه هیدروژن در سال ۲۰۲۰ به حدود ۸۰ میلیون تن رسیده است.
امروزه هیدروژن عمدتا از روش ریفورمینگ گاز طبیعی با بخار آب تولید میشود، فرآیندی که منجر به انتشار حجم عظیمی از گازهای گلخانهای میشود. در گزارش منتشر شده در سال ۲۰۱۸ نزدیک به ۴۸ درصد از تقاضای جهانی برای هیدروژن از این روش تامین میشود، حدود ۳۰ درصد از ریفورمینگ نفت/نفتا در پالایشگاهها/گازهای خروجی صنایع شیمیایی، ۱۸ درصد از گسیفیکیشن زغالسنگ، ۳.۹ درصد از الکترولیز آب و ۰.۱ درصد از منابع دیگر تولید میگردد. فرآیندهای الکترولیتی و پلاسما برای تولید هیدروژن راندمان بالایی از خود نشان میدهند، اما متاسفانه انرژی زیادی مصرف میکنند.
هیدروژن (H۲) یک گاز بی رنگ است، اما معمولاً بازار بین منبع تولید هیدروژن تمایز قائل میشود، به ویژه برای تشخیص هیدروژن مبتنی بر منابع فسیلی تجدید ناپذیر از هیدروژن با منابع تجدیدپذیر. کدهای رنگی هیدروژن به صورت زیر است.
هیدروژن خاکستری حاصل سوختهای فسیلی است، مانند ریفورمینگ متان با بخار آب یا گسیفیکیشن زغالسنگ. تولید هیدروژن خاکستری باعث ایجاد مقادیر قابل توجهی دی اکسید کربن میشود.
CH۴ + ۲H۲O –> ۴H۲ + CO۲
هیدروژن آبی نیز از روشی مشابه با هیدروژن خاکستری تولید میشود. با این تفاوت که دی اکسید کربن حاصل شده در فرآیند تولید هیدروژن جداسازی و ذخیره سازی میشود. راندمان روشهای جداسازی در بهترین حالت ۸۵ تا ۹۵ درصد است. این بدان معناست که هنوز ۵ تا ۱۵ درصد از دی اکسید کربن در اتمسفر رها میشود. البته با توجه به اینکه در عمل این ماکزیمم درصد جداسازی قابل دستیابی نیست، میتوان نتیجه گرفت که هیدروژن آبی به عنوان یک روش کوتاه مدت برای حذف گازهای گلخانهای در نظر گرفته میشود.
هیدروژن فیروزهای محصول جانبی پیرولیز متان است که متان را به گاز هیدروژن و کربن جامد تفکیک میکند. از طریق فرآیند پیرولیز، کربن موجود در متان تبدیل به کربن سیاه یا دوده صنعتی میشود. برای این کربن سیاه در حال حاضر بازارهایی نیز وجود دارد که جریان درآمد اضافی را فراهم میکند. قابل ذکر است که دوده صنعتی بسیارراحتتر از دی اکسید کربن گازی ذخیره میشود. در حال حاضر، تولید هیدروژن فیروزهای هنوز در مرحله آزمایشی است.
در میان کدهای رنگی مختلف هیدروژن، هیدروژن سبز به معنی هیدروژن تولید شده ازانرژی تجدیدپذیراست. بهترین گزینه فنآوری ایجاد شده برای تولید هیدروژن سبز الکترولیز آب است جایی که برق از منابع تجدیدپذیر مانند خورشید و باد تامین میشود. راهکارهای دیگری نیز مبتنی بر انرژی تجدیدپذیر وجود دارند. با این حال، به جز ریفورمینگ بیوگازها با بخار آب، این فناوریها هنوز در مقیاس تجاری ارائه نشده اند. هزینههای کم انرژی تجدیدپذیر و پیشرفت تکنولوژی، هزینههای تولید هیدروژن سبز را کاهش میدهند و به همین دلیل، روش الکترولیز در تولید هیدروژن مورد توجه قرار گرفته است.
هیدروژن «صورتی» هیدروژنی است که از طریق الکترولیزی تولید میشود که برق آن توسط انرژی هستهای تامین میشود.
برخی از هیدروژن «زرد» برای اشاره به هیدروژن تولید شده از طریق الکترولیز با انرژی خورشیدی، یا هیدروژن الکترولیز شده با استفاده از مخلوط انرژی تجدیدپذیر و فسیلی استفاده میکنند.
«هیدروژن سفید» هم یک هیدروژن زمین شناسی طبیعی است که در کانسارهای زیرزمینی یافت میشود و از طریق فراکینگ ایجاد میشود.
صنعت آهن و فولاد به عنوان یکی از بزرگترین تولیدکنندگان دی اکسید کربن، تقریباً عامل انتشار ۷ تا ۹ درصد دی اکسید کربن صنعتی جهان و حدود ۳۰ درصد از انشار دی اکسید کربن صنایع است. تنها در اروپا صنعت آهن و فولاد ۳ درصد از تولید کل دی اکسید کربن و در قسمتهای صنعتی ۲۲ درصد این آلاینده را به خود اختصاص داده است.
حدود ۷۵% از آهن جهان توسط روش BF-BOF تولید میشود. این روش کک را به عنوان منبع انرژی و همچنین عامل احیا کننده به کار میبرد. در حال حاضر، تولید فولاد خام در اتحادیه اروپا تقریباً بین فرآیندهای کوره بلند/کوره اکسیژن بازی یا قلیایی (BF/BOF) و کوره قوس الکتریکی قراضه (EAF) تقسیم شده است. در سال ۲۰۱۸، ۵۸.۳ ٪ فولاد از طریق BF/BOF تولید شد، در حالی که ۴۱.۷ درصد فولاد خام از طریق کوره قوس تولید گردید. برای دستیابی به هدف کاهش ۸۰ درصدی دی اکسید کربن، پیاده سازی اصطلاحاً «فناوریهای پیشرفته» در سیستمهای فولادسازی آینده ضروری است. از آنجا که فرآیندهای تولید فولاد در حال حاضر نزدیک به محدوده ترمودینامیکی خود عمل میکنند، پتانسیل کاهش دی اکسید کربن در این روشها محدود است. در مورد رایجترین روش یعنی BF/BOF به طور متوسط به ازای هر تن فولاد خام حدود ۱.۶ تا ۲ تن دی اکسید کربن (بسته به تکنولوژی استفاده شده) منتشر میشود. اما با روش DRI-EAF از مرحله سنگ تا تولید فولاد میزان انتشار دی اکسید کربن ۱.۱ تا ۱.۲ است که البته با اضافه شدن سیستم حذف دی اکسید کربن در مرحله احیا مستقیم میتوان یک سوم این مقدار انتشار دی اکسید کربن را نیز حذف کرد. پتانسیل کاهش دی اکسید کربن قابل دستیابی با روشهای تولید واقعی (با توجه به کاهش شدت دی اکسید کربن در بخش برق و همچنین افزایش در دسترس بودن ضایعات) بین سالهای ۲۰۱۰ و ۲۰۵۰ حداکثر ۱۵ درصد پیش بینی میشود. به دلیل رد پای کمتر کربن در روش کوره قوس مبتنی بر استفاده از قراضه، این فرایند به وضوح از نظر انتشار دی اکسید کربن (۴۵۵ کیلوگرم دی اکسید کربن به ازای هر تن فولاد خام) نسبت به فرآیند دیگر برتری دارد.
برای دستیابی به کاهش قابل توجه دی اکسید کربن در صنعت فولاد، دو رویکرد اصلی قابل تشخیص است:
استفاده هوشمند از کربن ((SCU شامل اقدامات یکپارچه برای کاهش استفاده از کربن در فرایندهای موجود و استفاده از دی اکسید کربن حاصل شده به عنوان ماده اولیه برای تبدیلهای شیمیایی (جذب و استفاده از کربن)، که در کنار آن جذب و ذخیره کربن (CCS) به عنوان گزینه جایگزین باشد.
جایگزینی کربن با برق تجدیدپذیر و/یا احیا کنندههای غیر فسیلی برای جلوگیری از انتشار مستقیم دی اکسید کربن یا (CDA).
فرآیندهای CDA را میتوان عمدتا به فرآیندهای احیا مبتنی بر هیدروژن و برق تقسیم کرد. فناوریهای احیای آهن مبتنی بر برق برای تولید فولاد، از الکترولیز سنگ آهن در درجه حرارتهای مختلف استفاده میکنند (الکترودینگ آهن در دمای پایین، پیروالکترولیز در دمای بالا). این فناوریها پتانسیل بالایی برای کاهش دی اکسید کربن تا ۹۵ درصد در صورت استفاده صد درصدی از برق تجدیدپذیر دارند. این فرایندها در حال حاضر در حال توسعه هستند.
همین امر در مورد فرآیندهای جایگزینی عوامل احیا کننده حاوی کربن با هیدروژن، در حالت جامد (احیا مستقیم (DR)) یا در حالت مایع (plasma smelting reduction) نیز صدق میکند. plasma smelting reduction مستقیما ریز سنگ آهن را از طریق هیدروژن به شکل یونیزه به فولاد مایع تبدیل میکند. پلاسما هیدروژن برای احیای اکسیدهای آهن استفاده میشود و همزمان حرارت را برای ذوب آهن فلزی فراهم میکند.
فرآیندهای احیا مستقیم همراه با کوره قوس الکتریکی زمینه کاهش دی اکسید کربن را در صنعت فولاد فراهم میکند. استفاده از گاز طبیعی به عنوان منبع تولید عامل احیا کننده باعث میشود تقریباً یک سوم انتشار دی اکسید کربن در مقایسه با روش BF/BOF کم شود. این کاهش به دلیل محتوای هیدروژن بیشتر گاز طبیعی است که به عنوان عامل احیا کننده عمل میکند.
در حال حاضر سه فناوری اصلی برای فرآیندهای احیا مستقیم مبتنی بر گاز طبیعی وجود دارند HYL/Energiron و MIDREX و PERED.
فرایند میدرکس حدود ۶۵ درصد از کل فرایندهای احیا مستقیم در سراسر جهان برای تولید آهن اسفنجی را در اختیار دارد. بخش اصلی پلنتهای احیا مستقیم، کوره است محلی که فرآیند احیای آهن در آن صورت میگیرد.
Fe۲O۳+۳H۲à۲Fe+۳H۲O ΔHR = ۹۹ kJ/mol @۲۵oC
Fe۲O۳+۳COà۲Fe+۳CO۲ ΔHR = -۲۴ kJ/mol @۲۵oC
گازهای حاصل که عمدتا شامل H۲O و CO۲ است پس از شستشو و خنک شدن در تاپ گس اسکرابر مجددا در چرخه فرآیند احیا باقی مانده و مورد استفاده قرار میگیرند. دو سوم این گاز پس از مخلوط شدن با گاز طبیعی به عنوان خوراک ریفورمر استفاده میشود و باقی آن به عنوان منبع حرارتی ریفورمر صرف تامین گرمای مورد نیاز واکنشهای ریفورمینگ میشود.
گاز از درون لولههای ریفورمر که با کاتالیست نیکل پر شده اند عبور میکند و واکنشهای ریفورمینگ با بخار آب و ریفورمینگ خشک در دمای بالای ۹۰۰ درجه سانتی گراد صورت میپذیرند. در نتیجه بخشی از CO۲ تولید شده به CO تبدیل میگردد که مجددا در فرآیند احیا استفاده میشود.
CH۴+CO۲à۲CO+۲H۲ ΔHR = ۲۴۷ kJ/ mol @۲۵oC
CH۴+H۲OàCO+۳H۲ ΔHR = ۲۰۶ kJ/mol @۲۵oC
گازهای احیای حاصل از ریفورمینگ شامل ۵۵ درصد هیدروژن و ۳۵ درصد منوکسید کربن است. به عنوان یک روش جایگزین برای کاهش بیشتر دی اکسید کربن منتشر شده میتوان از هیدروژن تجدیدپذیر به عنوان عامل احیا کننده یا منبع حرارتی استفاده کرد. با توجه به اینکه گاز خروجی ریفورمر بالای ۵۵ درصد هیدروژن دارد این امکان وجود دارد که بخشی از گاز طبیعی با هیدروژن تجدیدپذیر جایگزین گردد. جایگزینی ۳۰ درصدی گاز طبیعی با هیدروژن در فرآیندهای احیای موجود نیازمند تغییر خاصی در آن پلنتها نمیباشد.
برای کاهش گازهای گلخانهای تحقیقات زیادی در حال انجام است. در زیر نتایج برخی از این تحقیقات و چالشهای پیش رو و نتایج آن ذکر میگردد.
اگرهیدروژن به عنوان تنها عامل احیاکننده استفاده شود، در این صورت دیگر به ریفورمر نیاز نیست. فقط برای تامین دمای مناسب برای گاز احیا کننده، گرم کن مورد نیاز است. منابعی مانند هیدروژن یا منابع سازگارتر با محیط زیست (NG، برق سبز، گرمای تلف شده) میتوانند به عنوان سوخت برای این گرم کن مورد استفاده قرار گیرند.
اگر هیدروژن کاملا جایگزین گردد، ۵۵۰ تا ۶۵۰ نرمال مترمکعب بر تن برای فرآیند و ۲۵۰ نرمال مترمکعب بر تن برای گرم کن نیاز میباشد. با این روش میزان انتشار دی اکسیدکربن تا حدود ۸۰ درصد نسبت به روش BF/BOF کاهش مییابد.
با استفاده از هیدروژن در پلنتهای احیای موجود، سرعت احیای سنگ آهن را افزایش مییابد، اما ماهیت گرماگیر واکنش گندله با هیدروژن و پتانسل احیا و سایر تاثیرات آن باید در نظر گرفته شود.
با توجه به اینکه پلنت احیا بر پایه هیدروژن برای تولید فولاد سبز نبایستی با سوختهای فسیلی کار کند پس باید از جایگزینهای دیگر استفاده گردد. همانگونه که قبلا ذکرشد در حال حاضر آینده دارترین تکنولوژی برای هیدروژن سبز الکترولیز آب است. توجه به این نکته نیز مهم است که هیدروژن دانسیته انرژی زیادی به ازای وزن دارد در حالیکه دانسیته انرژی کمی به ازای حجم دارد.
تقریباً ۳۴۰۰ تا ۳۶۰۰ کیلووات ساعت به ازاء هر تن آهن اسفنجی برای تولید هیدروژن فرآیند و گرم کردن گاز احیا مورد نیاز است. این مقدار با در نظر گرفتن بازدهی ۷۵ درصدی الکترولیز و HHV هیدروژن، ۳.۵۴ KWh/m۳ محاسبه شده است.
اگر انرژی مورد نیاز گرم کردن بتواند از انرژی هدر رفته تامین شود راندمان بالاتری خواهیم داشت. در این صورت میزان برق مصرفی به ۲۳۰۰ تا ۲۵۰۰ کیلووات ساعت بر تن آهن اسفنجی کاهش مییابد. ۸۰ تا ۱۲۵ کیلووات ساعت به ازای هر تن آهن اسفنجی نیز برای کمپرسورها، تامین آب و تاسیسات جانبی نیاز است. عملیات فولادسازی در کوره قوس هم ۳۱۰-۶۴۰ کیلووات ساعت بر تن فولاد خام بسته به نسبت قراضه/آهن اسفنجی مصرفی (مقدار بیشتر آهن اسفنجی مصرف انرژی را افزایش میدهد) و دمای آهن اسفنجی خروجی، دانسیته سرباره و انرژی نیازدارد.
منبع اصلی آلودگی، گازهای خروجی از ریفورمر است که ۱۲۴ کیلوگرم کربن بر تن آهن اسفنجی است. این مقدار حدود ۵۰۰ کیلوگرم دی اکسید کربن بر تن آهن اسفنجی است. این آلودگی برای پلنت بر پایه هیدروژن به حدود ۴۰ کیلوگرم دی اکسید کربن بر تن آهن اسفنجی میرسد.
مقدار گاز طبیعی هم که برای تنظیم کربن اضافه میگردد و در کوره قوس میسوزد ۷۲ تا ۱۸۰ کیلوگرم دی اکسید کربن به ازای هر تن فولاد خام تولید میکند.
برای بررسی رد پای کربن در یک فرایند احیا مستقیم، نه تنها انتشار مستقیم گاز دی اکسید کربن در خود فرآیند بلکه انتشار غیر مستقیم از برق مصرفی نیز باید مورد توجه قرار گیرد. شکل زیر میزان دی اکسید کربن حاصل از تولید برق را نشان میدهد. همانطور که در این شکل مشخص است در مورد هیدروژن نبایستی از ۱۲۰ گرم دی اکسید کربن به ازاء هر کیلووات ساعت فراتر برود تا نسبت به پلنت بر پایه گاز طبیعی ارجح باشد.
وابستگی انتشار دی اکسید کربن فرآیند احیا مستقیم به دی اکسید کربن منتشر شده از برق
با ادامه چرخه فولاد کنونی، اهداف توافقنامه پاریس دست نیافتنی است. تکنولوژی استفاده از هیدروژن دستاوردی نو در این زمینه است که همچنان در حال ارزیابی است. همانگونه که در بالا ذکر شد ارزیابیها حدود ۹۰ درصد کاهش دی اکسید کربن را نشان میدهند، اما در این خصوص تولید هیدروژن موضوع اصلی است. هیدروژن بایستی از الکترولیز تولید شود و برای تامین برق آن منابع تجدیدپذیر به کار گرفته شود. در کنار همه این موارد باید آلودگی و برق تمام مراحل بالادستی و پایین دستی فولاد نیز در دستیابی به فولاد سبز در نظر گرفته شود.
علاوه بر این سوالات فنی در زمینه تکنولوژی استفاده از هیدروژن بایستی بررسی گردد. سوالات فنی مربوط به فناوری الکترولیز، گذار از سیستمهای تولید انرژی موجود به انرژیهای تجدیدپذیر نیز باید تحقق یابد. در کنار همه اینها عرضه مداوم و پایای منابع تجدیدپذیر برق در طول سال نیز باید برای پلنت تأمین شود.
با توجه به این واقعیت که تقاضای برق از منابع تجدیدپذیر در آینده به شدت افزایش مییابد، حدود ۳۵۰۰ کیلووات ساعت برق برای هر تن آهن اسفنجی برای پلنت بر پایه هیدروژنی نیاز است. تولید فولاد با ردپای کمتر کربن در سطح اروپا، تقاضای اضافی سالانه انرژی ۴۰۰-۵۰۰ TWh را ایجاد میکند. با توجه به اینکه مصرف برق صنعت فولاد در حال حاضر ۷۵ TWh است این افزایش تقاضا خودش ۱۸ درصد تولید کنونی برق اتحادیه اروپا است.
حتی اگر تقاضای انرژی اضافی برای استفاده از قراضه یا روشهای تولید فولاد مبتنی بر ضایعات کاهش یابد باز هم
توسعه الکترولیزرهای مناسب و تامین کافی مقدار انرژی تجدیدپذیر برای تمام بخشهای درگیر در صنعت فولاد چالش برانگیزخواهد بود.
*نویسنده: حسین عزیز طائمه؛ طراح پلنتهای احیا مستقیم
*نویسنده: سودابه خادمی؛ طراح پلنتهای احیا مستقیم
منبع: اقتصاد آنلاین