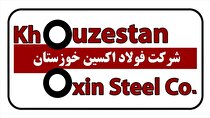
به گزارش میمتالز، محمد امین یوسف زاده مدیر مهندسی نورد ذوب آهن اصفهان در این خصوص گفت: در ایام دهه مبارک فجر به همت بخش طراحی کالیبر این مدیریت و متخصصان فنی تولید در نورد ۶۵۰، مشکلات مربوط به تولید تیرآهنهای سنگین ۲۷ و ۳۰ (که با تولید ۳۰ شروع شده است) که وابستگی صد درصدی به تامین غلتکهای ۴۰ تنی فورج خارجی داشتند و با ریسک بالای توقف تولید مواجه بود، مرتفع گردید.
وی اظهار داشت: این اقدام به دنبال بروز مشکل بسیار جدی در تامین غلتکهای فورج وارداتی برای تولید تیراهنهای ۲۷ و ۳۰ و سایر Hهای سنگین (که قیمت بالایی هم دارند) در قفسه ۹۰۰ (BD) در کارگاه نورد ۶۵۰، که با وجود سه سال پیگیری هنوز تامین نشده است، صورت گرفت.
مدیر مهندسی نورد افزود: به دنبال مواجه با تحریمها و مسیر بسیار دشوار تامین غلتکهای فورج، از حدود ۶ ماه پیش و به دنبال دو مرحله استفاده ناموفق از غلتکهای ریخته گری تولید داخل و بروز حادثه برای آنها، با ارائه طرحی جسورانه، برای کاهش نیروی نوردی و جلوگیری از حادثه اقدام نمودیم.
یوسف زاده با اشاره به اینکه مراحل کامل محاسبات مهندسی و طراحی در چهار ماه به کمک نرم افزار شبیه سازی، صورت گرفت، بیان کرد: در این راستا به لطف وجود قفسه جدید آلمانی ۵ A و تغییر صد در صدی در طراحی، با تراش و آماده سازی غلتکهای مربوطه، آنها آماده ورود به خط شدند.
وی افزود: بعد از این مرحله، قطعات تکنولوژی تکیمیلی از جمله هادیهای جدید آماده سازی شده و در نوزدهم بهمن ماه به خط برده شدند و خوشبختانه بیستم بهمن ماه پروفیل تیرآهن ۳۰ بر اساس استاندارد ملی با موفقیت تولید گردید.
مدیر مهندسی نورد ذوب آهن در پاسخ به این سوال که طراحی جدید چه مزایایی را در پی داشته است چنین گفت: نیاز به واردات غلتکهای فورج صفر میشود، انتظار داریم با بکارگیری سیستم تاندم میل که به لطف وجود قفسه چهار غلتکی جدید (انیورسال جدید ۵ A) میسر شد تاثیر قابل توجهی در کیفیت تولید و کاهش مصرف فلز و همچنین شاخههای طول کوتاه در تیرآهن ۳۰ را داشته باشد و همچنین این روش منجر به کاهش قابل توجه مصرف غلتک خواهد شد ودر استند میانی ۸۰۰ که قبلاً با تناژ حدود ۶۰۰۰۰ تن اسقاط میشد تا تناژ حدود سیصد هزار تن افزایش ظرفیت پیدا میکند.
علیرضا مهرابی سرپرست خدمات فنی و تولید مدیریت مهندسی نورد نیز در ادامه گفت: تولید تیرآهن ۳۰ با طراحی جدید، یک امتحان کامل برای بخش مهندسی نورد بود و خداوند را شاکریم که توانستیم سربلند از آن بیرون بیاییم.
وی افزود: زمان تکمیل طرحهای جدید در نورد معمولاً دو تا سه دوره کاری در یک پروسه یک ماهه به طول میانجامد، این پروفیل در اولین مرحله تولید و در یک روز، به نتیجه نهایی رسید و پروفیل IPE ۳۰ مورد نیاز ذوب آهن را آماده تحویل به مشتری نمود؛ لذا با اطمینان میتوان گفت بلوغ صنعتی، نتیجه این پروژه بزرگ صنعتی است که با حداقل هزینه اجرا شد.
سرپرست خدمات فنی و تولید مدیریت مهندسی نورد تصریح کرد: افزایش کیفیت و کاهش هزینههای تولید همیشه هدف اصلی تیمهای صنعتی به شمار میرود که در این زمینه نیز با انتخاب هدف از پیش تعیین شده و تعریف درست از مراحل طراحی و تولید با بهترین شکل این تولید محقق شد.
مهرابی خاطر نشان کرد: اواخر دهه ۷۰ برای اولین بار تیرآهن ۳۰ تولید شد و پس از تولید چند ساله، با نهایت تاسف این محصول از سبد ذوب آهن به دلیل ریجکتی بالای ۳۰ درصد (خرابی فلزی و پلیسه نوردی) و ضرر ده بودن آن، حذف شد، اما به دلیل نیاز شدید بازار حدود پنج سال پیش مجدداً با همان طراحی، به خط تولید برگشت. طی این چند سال دغدغه مهندسی نورد، بهبود شرایط تولید و کیفیت محصول بود که با طراحی منحصر به فرد و خاص طراحی کالیبر و به کارگیری قفسه ۵ A (تولید ریل) این مهم محقق گردید. این موفقیت را به مدیریت و پرسنل مهندسی نورد و به ویژه تیم طراحی کالیبر مهندسی نورد، مردان خستگی ناپذیر کارگاه نورد ۶۵۰ و کارگاه میانی نورد تبریک میگویم.
منبع: ذوب آهن اصفهان