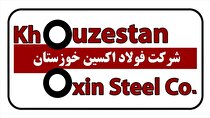
به گزارش میمتالز، در فرآیند تولید فولاد در کنار کورههای قوس الکتریکی و ماشینهای ریختهگری مداوم بخشهای متعددی ایفای نقش میکنند تا فولادی باکیفیت و مطابق با سفارش مشتری تولید شود. یکی از این قسمتها که نقش بسیار حساس و مهمی بر عهده دارد، واحد عملیات ثانویه است که مسیب فتاحالمنان مدیر عملیات ثانویه فولاد مبارکه به آن پرداخته است.
واحد متالورژی ثانویه یکی از بخشهای ناحیه فولادسازی و ریختهگری مداوم است. در این واحد، فولاد مذاب از کورههای قوس الکتریکی تحویل گرفته میشود و ازنظر دما، آنالیز شیمیایی، تصفیه و حذف ناخالصیها مورد بررسی و تحلیل قرار میگیرد و پس از انجام عملیات لازم، به واحد ریختهگری جهت تبدیل فولاد مذاب به تختال که محصول نهایی فولادسازی است ارسال میشود.
این عملیات با استفاده از هفت کارگاه یا کوره پاتیلی، واحد گاززدایی، ۴۸ پاتیل مذاب هریک به ظرفیت ۲۰۰ تن و حدود ۱۰۰ تجهیز جرثقیل سبک و سنگین که با ظرفیت ۱۶ تا ۴۵ تن وظیفه جابهجایی مذاب و تجهیزات و قطعات را بر عهده دارند، انجام میشود.
تجهیزات خطوط ظرفیت تولید بالقوهای دارند و نیروی انسانی میتواند آن ظرفیت را محقق کند. تلاش و پویایی مستمر نیروی انسانی در حین فرآیندها میتواند ظرفیت بهرهوری تجهیزات را ارتقا بخشد. ازآنجاکه خرابیها منجر به افت و توقف تولید میشود، سرویس و نگهداری تجهیزات با همکاری تیمهای دفتر فنی تعمیرات و کارشناسان تعمیرات خطوط بهصورت مرتب انجام میشود. هرچه این رسیدگیها و تعمیرات کیفیتر انجام گیرد، تجهیزات آمادهبهکارتر هستند و تولید بهتر و کیفیتر را شاهد خواهیم بود. چارهاندیشی برای حل مشکلات و خرابیها و همچنین بهینهسازی آنها از مهمترین تلاشهایی است که در این حوزه انجام میشود. بههرحال تمامی تلاش مجموعه بر آن است که تجهیزات همواره بهروز و آمادهبهکار باشند تا شاهد تولید مستمر و پایدار باشیم.
بهروزرسانی کورههای پاتیلی که از سال ۱۳۷۳ در مدار بهرهبرداری بودند در قالب یک پروژه در حال پیگیری و پیشرفت است و پیشبینی میشود که بتوانیم تا دو سال آینده با جایگزین کردن تجهیزات نو از تکنولوژی جدید در فرآیند استفاده کنیم و با توان مضاعف به کار تولید همت گماریم.
بهموازات افزایش تولید باید به کاهش هزینهها و همچنین کاهش ضایعات توجه داشته باشیم. تاکنون با انجام پروژههای متعددی از جمله کاهش برگشت تهمانده ذوب از ریختهگری و کنترل فرآیند دما، ۵ درصد بهبود داشتهایم و این اقدام تا به صفر رساندن برگشت تهمانده پاتیلهای برگشتی ادامه خواهد یافت.
توقفات سه دسته هستند: توقفاتی که از بیرون از فولاد مبارکه به دلیل محدودیت در منابع به شرکت تحمیل میشوند؛ توقفاتی که برنامهریزیشده هستند و غالباً برای انجام عملیات تعمیرات در سیستم در نظر گرفته میشوند و توقفات اضطراری که ناخواسته و غیرقابلپیشبینی اتفاق میافتند و باید با عکسالعمل سریع و مناسب، برای رفع عیب و آمادهبهکار نگه داشتن تجهیز اقدام کنیم. البته برای هر سه دسته توقفات تدابیری در سطح ناحیه اندیشیده شده و عملیاتی شده است. هنگامی که با توقفات ناشی از عوامل بیرونی مانند محدودیت برق در تابستان مواجهیم، سعی میکنیم برنامههای تعمیراتی شرکت را در آن زمانها انجام دهیم و خط تولید را برای تولید در زمانهای مناسب آمادهسازی کنیم. درخصوص توقفات ناخواسته نیز تلاش میکنیم با بهبود سطح کیفی قطعات و آمادهبهکاری آنها و همچنین با تقویت و آموزش نیروی انسانی، میزان توقفات اضطراری را کاهش دهیم.
محدودیت انرژی محدودیتی است که کمتر قابلکنترل است و فولاد مبارکه کمتر میتواند در آن تغییر ایجاد کند. بااینحال تلاش میکنیم با تغییر و زمانبندی صحیح و هوشمندانه برنامههای تعمیرات و توقفات این محدودیتها را مدیریت کنیم. اگرچه مواقعی که با محدودیت انرژی و منابع مواجه نبودهایم، بهترین عملکرد و بیشترین تولید را داشتهایم.
فرآیند تولید برخی از آنها از ناحیه آهنسازی شروع میشود و در خطوط نورد سرد و گرم پایان میپذیرد. تولید محصولات خاص و ویژه ارزشافزوده بالاتری برای سازمان دارد. گریدها و محصولات کمکربن نمونهای از این محصولات هستند که سیکل تولید آن با محصولات معمولی متفاوت است. در فرآیند تولید این محصولات واحد گاززدایی تحت خلأ که از طریق واحد RH آمادهسازی میشود نقش بسزایی دارد. در حال حاضر با رشد فزاینده تولید محصولات خاص در شرکت مواجهیم؛ ازاینرو آمادهبهکاری تجهیزات، تولید کیفی و کنترلهایی که منجر به تولید با سیکل گاززدایی RH میشود در دست اقدام است تا بتوانیم پاسخگوی سفارشهای ویژه مشتریان باشیم.
تحریمها همواره بودهاند و اگرچه شرایط را سخت کردهاند، اما در همین شرایط سخت همانگونه که اشاره شد، تهدیدها را به فرصت تبدیل کردهایم. نگاه و تأکید حمایتی مدیریت شرکت بر افزایش توان فنی سازندگان داخلی باعث شده در برخی موارد، شاهد تولید کیفیتر از نمونه خارجی در داخل کشور باشیم. فولاد مبارکه، شرکتهای دانشبنیان و سازندگان در فرآیند بومیسازی به نتایج درخشانی دستیافتهاند. دستیابی به دانش فنی و توان ساخت داخل از یک سو برای شرکتهای دانشبنیان و سازندگان داخلی از یک سو و تأمین باکیفیت و باصرفه اقتصادی و مهمتر از آن تولید پایدار با دسترسی آسانتر به تجهیزات و خدمات پس از فروش از دیگر سو دستاوردهایی بوده که نصیب فولاد مبارکه شده است. در این فرآیند سازندگان و شرکتهای دانشبنیان به عرصههای بینالمللی معرفی شده و میتوانند محصولات خود را حتی به بازارهای جهانی عرضه کنند.
بومیسازی ماشین تزریق وایر در کوره پاتیلی که وظیفه تزریق وایرهای آلومینیوم یا کلسیم با سرعت مناسب را دارد از تکنولوژی خاصی برخوردار است که پیش از بومیسازی از کشور آلمان وارد میشده و خوشبختانه نمونههای بومیسازی و نصبشده بهخوبی در حال کار است.
در حال حاضر چندین پروژه با این شرکتها تعریف شده و در حال اجراست. در شرایطی که به بار نشستن این پروژه بهشدت مورد تردید بود، خوشبختانه شاهد این هستیم که برخی موارد آنها به نتیجه رسیده و مورد بهرهبرداری قرار گرفته است. یکی از این موارد رینگهای پاتیل مذاب بود که وظیفه این رینگ تشخیص سرباره هنگام خروج از پاتیل مذاب به تاندیش است که کیفیت تولید و جلوگیری از حوادث را نیز در پی دارد. این رینگ با حضور و تلاش شبانهروزی یکی از همین شرکت دانشبنیان ساختهشده و با موفقیت روی پاتیلها نصب شده و باکیفیت مطلوب در حال بهرهبرداری است. موفقیت اقلام بومیسازی شده نقطه عطفی برای ورود به بومیسازی بسیاری از اقلام دیگر است.
منبع: پایگاه خبری - تحلیلی ایراسین