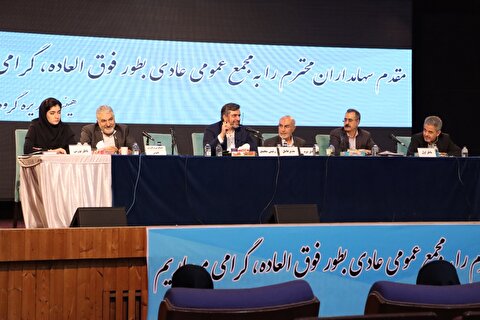
به گزارش میمتالز، «سیدبهادر احرامیان» عضو هیات مدیره انجمن تولیدکنندگان فولاد ایران در این نشست تخصصی به چالشهای اصلی صنعت فولاد ایران پرداخت و عنوان کرد: این روزها انرژی یکی از مهمترین چالشهای صنعت فولاد به شمار میرود. در ناترازی انرژی، صنعت فولاد یکی از صنایعی است که مظلوم واقع شده، این در حالی است که جدول داده - ستاندهها به درستی بیان نمیشود و جامعه ما از نقش واقعی صنعت فولاد و اثر مثبت آن در اقتصاد کشور آگاه نیست.
دانلود کنید: صنعت فولاد ایران از افسانه تا واقعیت؛ پنل ششمین جشنواره و نمایشگاه ملی فولاد ایران
احرامیان در ادامه خاطرنشان کرد: البته مشکل ما در اخبار و رسانههاست که در آن به نوعی جنگ روایتها مطرح است، بدین معنا که از یکسو این روایت مطرح میشود که صنعت فولاد از انرژی ارزان و رانت بهره میگیرد و حتی ناترازی برق به خاطر وجود فولادسازان است، اما در روایت مقابل شاهد اطلاعرسانی برای اثرات مثبت صنعت فولاد در رسانهها نیستیم.
وی در ادامه به بررسی جایگاه صنعت فولاد ایران پرداخت و افزود: صنعت فولاد ایران با ۳۲ میلیون تن تولید جایگاه دهم فولاد در دنیا را دارد، این در حالی است که با تولید حداکثر ۴ میلیون تن بیشتر ایران میتواند جایگاه هفتمین تولیدکننده فولاد دنیا را به خود اختصاص بدهد، چراکه کشور آلمان با ۳۵ میلیون تن تولید در رتبه هفتم قرار دارد. همچنین صنعت فولاد با همین میزان تولید ۵ درصد جیدیپی GDP کشور را به خود اختصاص داده است که اگر این تولید به ظرفیت نصبشده ۵۰ میلیون نت (خالص) افزایش پیدا کند، ممکن است ۷ تا ۸ درصد جیدیپی را به خود اختصاص دهد. همچنین در بخش اشتغال صنعت فولاد ۸ درصد اشتغالزایی مستقیم و غیرمستقیم را به خود اختصاص داده است.
این عضو هیات مدیره انجمن تولیدکنندگان فولاد ایران همچنین به سهم ارزش صادراتی فولاد نیز پرداخت و گفت: صنعت فولاد هم جایگزین واردات شده و هم صادرات انجام میدهد که این صنعت با همین میزان تولید با میانگین ۵۰۰ دلار در تن محصول، ۱۵ میلیارد دلار اثر مثبت در تراز تجاری کشور دارد. ۷ میلیارد دلار ارزش صادراتی زنجیره فولاد است.
احرامیان در ادامه با اشاره به اثر صنعت فولاد در صنایع پاییندستی تصریح کرد: بارها از افزایش قیمت فولاد روی افزایش قیمت مسکن مطرح میشود، اما واقعیت این است که آمار نشان میدهد که برای ساخت هر مترمربع مسکن حدود ۵۰ کیلوگرم فولاد مصرف میشود که با فرض قیمت ۲۵ هزار تومان حدود یک میلیون تومان مصرف فولاد در هر مترمربع میشود. بین ۱.۵ تا ۲ درصد اثر کل هزینه فولاد در ساخت مسکن کشور است؛ بنابراین قیمت فولاد روی تورم مسکن عدد ناچیزی است. این اعداد نیز بر اساس آمار رسمی کشور بیان میشود و احیانا اگر کسی به این اعداد شک دارد، میتواند در این زمینه راستیآزمایی انجام بدهد.
وی در ادامه با اشاره به این موضوع که یکی از هجمههایی که به صنعت فولاد وارد میشود در زمینه آب، برق و گاز است، گفت: صنعت فولاد ایران بر پایه تولید آهن اسفنجی به روش احیای مستقیم است. در دنیا روش غالب فولادسازی به روش کوره بلند است و برای تولید هر تن فولاد در روش کوره بلند به میزان ۲.۵ تن کربن تولید میشود، اما در روش احیای مستقیم ۱.۲ تن بیشتر کربن به ازای هر تن فولاد تولید نمیشود. در زمینه سایر گازهای آلاینده دیگر نیز همین نسبت وجود دارد. همچنین اکثر فولادسازان در کشور ما با آخرین فناوریها روز دنیا در حال فعالیت هستند و به طور متوسط صنعت فولاد ایران از دنیا جلوتر است و از نظر محیطزیستی هیچ مستندی بر آلودگی صنعت فولاد در ایران وجود ندارد. از سوی دیگر شهرهای تهران و مشهد که جزو آلودهترین شهرهای ایران به شمار میروند هیچ کارخانه فولادی در اطراف آنها وجود ندارد. آلودگی این شهرها به عوامل دیگری بستگی دارد همبستگی بیشتری بین مصرف گاز خانگی با آلودگی شهرها وجود دارد. از سوی دیگر کارخانههای فولاد با شهرها فاصله دارند.
این عضو هیات مدیره انجمن تولیدکنندگان فولاد ایران همچنین به موضوع آب پرداخت و عنوان کرد: در زمینه آب نیز بر اساس آمار وزارت کشاورزی و وزارت نیرو در کشور ۱۰۰ میلیارد مترمکعب آب از منابع کشور برداشت میشود که صنعت فولاد با حدود ۳۱ میلیون تن تولید و بر اساس برآورد دست بالای مصرف ۵ مترمکعب آب برای تولید هر تن فولاد، حداکثر ۱۵۰ میلیون مترمکعب خواهد بود، این در حالی است که کارخانههای کنار خلیج فارس از جمله فولاد هرمزگان و صبا فولاد خلیج فارس که آب مورد نیاز خود را از خلیج فارس برمیدارند، از این آمار کم نکردهایم. همچنین کارخانههای بسیاری در داخل کشور از آب پساب و فاضلاب استفاده میکنند را نیز کسر نکردیم. سوم اینکه خط انتقال آب از خلیج فارس به گلگهر، چادرملو و فولاد مبارکه را در نظر نگرفتهایم. با این وجود اگر ۱۵۰ میلیون تن مترمکعب را تقسیم بر ۱۰۰ میلیارد مترمکعب کنیم، ۰.۱۵ درصد سهم مصرف آب صنعت فولاد میشود. اگر سه مورد عنوان شده را کسر کنیم، مصرف آب فولاد به ۷۰ تا ۸۰ مترمکعب بیشتر نمیرسد و اثر واقعی آن حدود ۰.۷ تا ۰.۸ درصد است. اینک چرا نام صنعت فولاد را با بحران کمآبی در یک ردیف قرار میدهند، جای سوال دارد، در حالی که صنعت فولاد به بحران کمآبی و فرونشست دشتها هیچ ارتباطی ندارد.
احرامیان درباره ناترازی برق نیز تصریح کرد: درباره ناترازی برق بحثهای بسیاری انجام شده است. البته که صنعت فولاد کشور، بالاترین میزان تولید برق را نسبت به سایر صنایع ایجاد کرده و ۵۰ تا ۶۰ درصد برق مورد نیاز خود را تامین کرده است، در حالی که با بیشترین میزان محدودیت مواجه شده و بالای ۹۰ درصد با قطعی برق روبهرو بوده است.
وی ادامه داد: در زمینه محدودیتهای گاز نیز صنعت فولاد در تیررس قرار دارد. در کشور حدود ۳۰۰ میلیارد مترمکعب گاز مصرف میشود که صنعت فولاد حداکثر ۱۵ میلیارد مترمکعب مصرف گاز دارد که کمتر از ۵ درصد مصرف کشور را به خود اختصاص داده است، البته این موضوع را در برابر جیدیپی و اشتغالزایی این صنعت باید در نظر گرفت.
این عضو هیات مدیره انجمن تولیدکنندگان فولاد ایران درباره داده - ستانده صنعت فولاد، گفت: صنعت فولاد چند ورودی دارد که از جمله میتوان به ماده اولیه و سرمایه اشاره کرد، برای تولید یک تن فولاد باید هزار دلار سرمایهگذاری کرد، همچنین این صنعت به سرمایه در گردش بالایی نیاز دارد. علاوه بر این هزینه تامین مالی صنعت فولاد را باید بر اساس هزینههای برق، گاز و نیروی انسانی و ... محاسبه کرد و آن وقت نتیجه گرفت که آیا صنعت فولاد در ایران مزیتی دارد یا خیر، بنابراین در مجموع از نظر مزیت تفاوت چندانی بین فولادسازان ایران با فولادسازان جهان وجود ندارد.
احرامیان همچنین یادآور شد: در زمینه تامین مالی، نرخ تامین مالی صنعت فولاد در دنیا حداکثر ۵ درصد است، این نرخ در ایران دو برابر و حدود ۱۰ درصد است. در زمینه نیروی انسانی نیز ممکن است در کشور نیروی انسانی ارزانتر در اختیار داشته باشیم، اما میزان بهرهوری نیروی انسانی در ایران در سطح پایینتری قرار دارد.
وی افزود: در زمینه قیمت نیز برخی مدعی هستند که فولاد به قیمت ارزان صادر میشود و در داخل گرانتر فروخته میشود، در این راستا باید اذعان کرد که قیمت فوب هر کشور، قیمت یک کشتی محصول آهن است و یک تاجر با ریسک بالا در شرایط تحریم، صادرات انجام میدهد. البته آنچه مصرفکننده ایرانی از داخل میخرد، از هر قیمتی در دنیا ارزانتر است. در زمینه قیمت محصولات فولادی، ایران را با هر کشور دیگری میتوان مقایسه کرد.
«محمدیاسر طیبنیا» مدیرعامل فولاد مبارکه اصفهان در ادامه این نشست تخصصی عنوان کرد: بر اساس آمار ۱۱ ماهه سال ۲۰۲۴ میزان تولید فولاد ایران ۲۸ میلیون تن اعلام شده که این تولید نسبت به سال گذشته ثابت باقی مانده است و کاهش نداشته، این در حالی است که ناترازیهای انرژی طی سالهای اخیر فزاینده بوده است و این موضوع مرهون هوشمندی واحدهای فولادی است که از سه سال قبل آغاز کردهاند.
طیبنیا در ادامه تصریح کرد: موضوع ناترازی در فولاد تنها منحصر به برق و گاز نیست. تا پیش از این موضوع ناترازی روی مواد اولیه بود. موضوع بعدی محدودیت آب در فصل تابستان برای فولادسازان بود. چالش بعدی موضوع حملونقل بود و پس از آن به ناترازی برق و گاز رسیدیم و گلوگاههای قبلی را پشتسر گذاشتیم و هم اکنون دیگر کسی صحبت از کمبود آب نمیکند، چراکه ناترازی انرژی گلوگاه نخست صنعتگران فولاد شده است.
وی در ادامه افزود: در راستای برطرف کردن ناترازی انرژی از سه سال پیش برخی فولادسازان روی موضوع آب و انرژی سرمایهگذاری انجام دادند. ما نیز در فولاد مبارکه در زمینه آب پروژههایی را آغاز کردیم، از جمله جمعآوری پساب آب شهری بود که امروز نزدیک به نیمی از نیاز خود را از این طریق تامین میکنیم و به ازای تولید هر تن فولاد به مصرف ۲.۲ مترمکعب آب رسیدهایم. نیم دیگر مصرف آب را نیز از طریق انتقال آب خلیج فارس انجام دادهایم. امسال امکان انتقال ۷۰ میلیون مترمکعب آب شیرین برای رفع نیاز کل صنایع استان اصفهان به یُِمن وجود صنعت فولاد فراهم شده که این اتفاق در استانهای دیگر نیز روی داده است.
مدیرعامل فولاد مبارکه ادامه داد: در زمینه مواد اولیه نیز سرمایهگذاری انجام دادیم و از خرید مواد اولیه تا سرمایهگذاری در معادن این نیاز خود را تامین کردهایم و با سرمایهگذاری در معدن کوچک و متوسط سالانه ۳ میلیون تن سنگ آهن استخراج میکنیم.
طیبنیا افزود: در زمینه برق نیز فولاد مبارکه جزو نخستین شرکتهایی است که نیروگاه ۹۱۴ مگاواتی تجدیدپذیر و نیروگاه ۶۰۰ مگاواتی خورشیدی و نیروگاه ۲۰۰ مگاواتی بادی در منطقه خواف در دست اقدام دارد که فاز نخست نیروگاه تجدیدپذیر وارد مدار شده و ۴۰ مگاوات نیروگاه خورشیدی را نیز وارد مدار کردهایم که قرار است ماهانه ۲۰ مگاوات این نیروگاه وارد مدار شود. اگر امسال نیروگاه فولاد مبارکه وارد مدار نمیشد، صنعت فولاد ایران قادر نبود رتبه دهم جهانی خود را حفظ کند.
وی همچنین درباره ناترازی گاز گفت: در بحث ناترازی گاز نیز از سه سال پیش کار را آغاز کردیم و میادین گازی را معرفی کردیم و توافق نهایی ما با وزارت نفت انجام شده و قرارداد ما آماده امضا است.
مدیرعامل فولاد مبارکه ادامه داد: در زمینه دانش و بومیسازی نیز میتوانیم ادعا کنیم که صنعت فولاد با ۹۰ درصد ساخت داخل به خودکفایی رسیده است. الکترود گرافیتی اردکان امسال به مدار میآید و با راهاندازی آن، تقریبا صنعت فولاد ایران بینیاز از واردات میشود.
طیبنیا همچنین درباره تولید فولاد سبز خاطرنشان کرد: تولید فولاد سبز در دنیا یک موضوع جدی است. در انگلستان مشوقهایی برای تبدیل کورههای فولادسازی به کوره قوس در نظر گرفته شده است، زیرا کوره قوس به صنعت سبز نزدیکتر است، ما در کشور خود این ظرفیت را داریم. آنها مشوقهای مالیاتی برای این امر در نظر گرفتند؛ همچنین ۵۰ درصد هزینه برق را نیز کاهش میدهند تا به سمت صنعت سبز پیش بروند.
وی در ادامه با اشاره به این موضوع که صنایع باید برای این نوع ناترازیهای انرژی چارهاندیشی کنند، گفت: فولادسازان باید جهتگیری خودتامینی را در پیش بگیرند؛ البته با این پیشفرض که سیاستهای اقتصادی و صنعتی برای سرمایهگذاران قابل پیشبینی باشد و واحدهای فولادساز باید از سیاستهای دولت تا چشمانداز ۱۴۱۰ آگاه باشند تا بتواند سرمایهگذاری کنند. واحدهای صنعتی متقاضی یارانه دولتی نیستند، اما حداقل خواهان مشخص بودن سیاستهای دولت برای سالهای آینده هستند.
مدیرعامل فولاد مبارکه در ادامه یادآور شد: نیروگاهی که فولاد مبارکه احداث کرده خردادماه امسال وارد مدار شد، اما بحث بر سر این بود که برق این واحد فولادسازی نیز باید قطع شود، اگر بناست نیروگاه ایجاد کنیم، اما گاز این نیروگاه در زمان ناترازی تامین نشود، باید به سمت پیدا کردن میدان گازی نیز پیش برویم و اگر سرمایهگذاری انجام دادیم و دولت گازی به ما ندهد، چه باید کرد؟ سیاستهای دولت باید مشخص باشد و باید تعهدات دولت به صورت تضمینی پای کار باشد. البته به تازگی وزارت صنعت، معدن و تجارت در راستای جبران خسارت ناشی از ناترازیهای انرژی، بستهای را برای فولادسازان آماده کرده است.
«امین ابراهیمی» مدیرعامل شرکت فولاد خوزستان در ادامه این نشست تخصصی عنوان کرد: صنعت فولاد به عنوان یک صنعت مادر و صنعتساز به برکت انقلاب اسلامی و با سرمایهگذاری نزدیک به ۴۰ میلیارد دلار ایجاد شده است. اگر صورتهای مالی ۶ ماهه ۱۶ شرکت بزرگ معدن، فولاد و نورد را ملاحظه کنیم با یک بازار معادل ۸۱۰ همت روبهرو هستیم که ارزش جایگزینی آن حداقل سه برابر است؛ اما در عمل سود ۶ ماهه این شرکتها نزدیک به ۸۵ همت شده است؛ حال اگر شرکتهای بزرگ معدنی و فولاد مبارکه را کنار بگذاریم تقریبا سود مجموعه این شرکتها با یک سرمایهای نزدیک به ۴۰۰ همت، به زیر ۱۵ همت رسیده است. ارزش بازگشت سرمایه این صنعت امروز به زیر ۱۰ درصد و حاشیه سود این صنعت به زیر ۷ درصد رسیده است. این مهمترین شاخصی است که بنگاههای قتصادی را تهدید میکند و اعلام میکند که نفسهای این صنعت صنعتساز که ۱۶ درصد صادرات و ۶ درصد جیدیپی را به خود اختصاص داده، به شماره افتاده است. حاشیه سودی که شرکتها امروز گزارش میدهند حاشیه سود واقعی نیست، زیرا اگر تجدید ارزیابی کنند، مشخص میشود که استهلاک را در نظر نگرفتهاند.
ابراهیمی با تاکید بر این موضوع که مزیتی که بر اساس آن صنعت فولاد شکل گرفت، دیگر در کشور وجود ندارد، گفت: یک موضوع، افزایش هزینههاست که سالانه نزدیک به ۴۰ درصد افزایش پیدا میکند، آیا در برابر این هزینهها، درآمدها نیز افزایش یافته است. وقتی فولادساز مکلف به عرضه محصول خود به نرخ نیمایی است - هرچند ظرف یک ماه گذشته این موضوع ارز اصلاح شده است - چه انگیزهای برای صادرات باقی میماند.
وی افزود: طی دو سه سال گذشته ما در مجموعه خود ۴.۵ میلیارد دلار ارز صادر کردیم و فقط نزدیک به ۵۰ همت ناشی از اختلاف نرخ ارز را از دست دادهایم به خاطر اینکه مکلف بودیم که ارز خود را به نیما عرضه کنیم.
مدیرعامل فولاد خوزستان ادامه داد: تورم نرخ فروش فولاد حدود ۴.۵ درصد بوده و قیمت فروش ما در یک ماه گذشته معادل اردیبهشت ۱۴۰۰ بوده است؛ هزینهها افزایش یافته، اما درآمدها همچنان ثابت مانده است؛ این در شرایطی است که همواره صنعت فولاد مورد هجمه قرار گرفته است و کمبود برق و گاز را به گردن این صنعت انداختهاند. البته در این دوره نگاهها در وزارت صمت تغییر کرده و حداقل صنعت فولاد به عنوان محکوم شناسایی نمیشود و سازمان توسعه و نوسازی معادن و صنایع معدنی ایران (ایمیدرو) پیگیریهای خوبی را انجام میدهد. هرچند اداره برق و گاز مسوول قطع کردن هستند و اداره مالیات مسوول حسابرسی است و گویی همه از قوه قهریه استفاده میکنند تا این صنعت را از بین ببرند. این پرسش مهمی است که از حکمرانان این صنعت باید پرسید که آیا صنعت فولاد همچنان به عنوان مزیت محسوب میشود یا خیر؟ اگر مزیت است باید نوع نگاه و حمایت دولت نسبت به این صنعت تغییر کند. ما نمیتوانیم در کشور جزیرهای فکر کنیم و برق و گاز و اداره مالیات تنها به فکر برطرف کردن مشکل خود باشند؛ این برخوردهای قهری، انگیزه بخش خصوصی را برای سرمایهگذاری میگیرد و در چنین شرایطی نرخ بازگشت سرمایه دیگر توجیهپذیر نخواهد بود.
ابراهیمی با تاکید بر این موضوع که ما باید صنعت فولاد را به عنوان یک بسته ببینیم، افزود: ما نمیتوانیم مسوولیتهای اجتماعی صنعت فولاد را نادیده بگیریم، نمیتوانیم باشگاهداری که به این صنعت تحمیل شده است را نادیده بگیریم، نمیتوانیم نیروی انسانی که چهار برابر نیاز این صنعت به آن تحمیل شده است را نادیده بگیریم، اما میتوانیم تامین انرژی آن را نادیده بگیریم؛ در حالی که هزینه برق فولادسازی ۲۵ یورو در هر مگاوات ساعت است که تقریبا برابر با قیمتهای جهانی است.
همچنین در ادامه این نشست تخصصی، «سعید شجاعی» معاون برنامهریزی، نوآوری و هوشمندسازی وزارت صنعت، معدن و تجارت عنوان کرد: ما در کشور با زنگ خطری به عنوان پدیده صنعتزدایی روبهرو هستیم که اگر برای آن چارهاندیشی نداشته باشیم، موضوع توسعه و رفاه نیز تحت شعاع قرار میگیرد. در سه ماهه نخست امسال رشد بخش صنعت کشور بیش از ۳ درصد بوده است که در تابستان این رشد به زیر یک درصد رسید. در مهرماه محدودیتهای انرژی کمتر اعمال شد و دوباره رشد معناداری را تجربه کردیم. از آبانماه دوباره سیر نزولی اتفاق افتاد که علت عمده آن به موضوع ناترازی در فصلهای گرم و سرد سال بازمیگردد که با آن مواجه هستیم.
شجاعی ادامه داد: سرمایهگذاری در ماشینآلات که محرک رشد صنعت است در سه ماهه نخست امسال به ۰.۷ درصد رسیده که تابعی از نااطمینانی است که در فضای سرمایهگذاری وجود دارد.
اگر از تابستان عبور کنیم، برآورد ما ۱۷۳ همت (هزار میلیارد تومان) عدمالنفع از محدودیت برق است. در صنعت فولاد در ابتدای آبانماه محدودیتها از ۲۰ درصد آغاز شد و به ۳۱ درصد، ۳۸ درصد، ۴۷ درصد و ۶۸ درصد در ۱۷ آذرماه رسید که به ۱۷ میلیون مترمکعب گاز در روز برای اختصاص آن به بخش فولاد رسیدیم. پس از آن جلسههای متعددی برگزار شد و ۶۸ درصد محدودیت را به ۴۸ درصد رساندیم. پیشبینی ما ۱۳۰ همت عدمالنفع برای محدودیتهای گاز است.
کارگروه ویژهای را در وزارت کشور و در استانها شکل دادهایم که هدف این کارگروه این است که هر میزان صرفهجویی که در زمینه انرژی رخ داد آن را به سمت صنعت سرازیر کنند. در نهایت یک بسته حمایتی حول سه محور مالیات، بیمه و تسهیلات برای جبران خسارت محدودیتهای انرژی برای فولادسازان تدوین شده است.
وی همچنین افزود: راهکار میانمدت ما، بحث ظرفیت ماده ۲۵ قانون بهبود محیط کسبوکار است که در دو سطح تدارک دیده شده که اگر از سوی اداره برق و گاز خلف وعدهای شود، مطابق قرارداد باید جبران خسارت بکنند. در سطح دوم نیز اگر محدودیتهای بیشتری اعمال شود، دولت در بودجه سنواتی باید جبران خسارت کند. این موضوع را امسال در قالب یک بسته پوشش میدهیم، اما برای سال آینده یک ردیف بودجهای برای ماده ۲۵ در نظر خواهیم گرفت که جبران خسارتی از این محل صورت بگیرد.
«اردشیر افضلی» مدیرعامل شرکت ذوب آهن اصفهان نیز در ادامه این نشست تخصصی عنوان کرد: ما در کشور برخی مجوزها را برای فولادسازی صادر کردیم، اما به فکر زیرساختهای آن مانند مواد اولیه، حملونقل و پذیرش این کارخانه در منطقه و وضعیت جغرافیایی نبودهایم. هم اکنون برای این مجوزها در زمینه تامین انرژی با مشکل مواجه شدهایم.
افضلی ادامه داد: در زمینه آلودگی محیط زیست نیز در بدترین حالت ۱۵ درصد آلایندگی مربوط به صنعت است. ۸۰ درصد تولید فولاد در دنیا به روش کوره بلند است که انرژی کمتری مصرف میکند. در دنیا مشکل انرژی وجود ندارد و در چند روز گذشته قیمت برق آلمان صفر یورو شده است، در حالی که در ایران صحبت از مزیت رقابتی میشود.
وی با تاکید بر این موضوع که تولید در ایران با مسائلی مختلف روبهرو است و برخی بنگاهها با مازاد نیروی انسانی مواجه شدهاند، عنوان کرد: زمانی تولید فولاد در کشور مزیت رقابتی داشت، در شرایط کنونی دیگر وضعیت رقابتی برای این صنعت باقی نمانده است. اگر این شرایط ادامه پیدا کند، طی چند سال آینده کارخانههای آهن و فولاد تعطیل خواهند شد. کارخانههای بزرگ فولاد، امسال سود چندانی نداشتند، چه برسد به ذوبآهنی که یارانه ندارد و کک زغال سنگ را باید آزاد بخرد.
مدیرعامل ذوب آهن اصفهان تاکید کرد: زمان آن فرا رسیده است که ما از یک ساختار کارگرگرا به سمت یک ساختار ساختارگرا پیش برویم. اگر این اتفاق در صنعت فولاد روی بدهد، جزیرهای تصمیم گرفتن از بین میرود و بسیاری از مشکلات حل میشود. ما باید با دنیا رقابت کنیم و صنعت را نگه داریم و هیچ راه دیگری نداریم. تمام صنایع باید دست به دست هم بدهند و دولت باید صنعتستیزی نکند و سیاست صنعتپروری را پیشروی خود قرار بدهد.