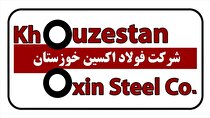
به گزارش میمتالز، تغییر در سیستمها بهندرت یکشبه اتفاق میافتد و میتوان آن را مانند یک سفر در نظر گرفت. این تغییرات نیز مانند سفر، با اولین قدمها آغاز میشوند؛ یعنی کاری که امروز میتوانیم انجام دهیم. بهرهوری انرژی، از جمله استفاده مستقیم از الکتریسیته در هر جایی که قابلاجرا باشد، یک نقطه شروع آشکار است. با این حال، اساساً نیروی محرکه برای این گذار هزینه تعرفه انتشار دیاکسیدکربن است. بهطورکلی، این انگیزه هنوز برای دوام بخشیدن به گامهای بزرگتر در طول گذار، از جمله اراده کافی برای سرمایهگذاری انبوه در سیستمهای تأمین برق سبز، بسیار ناچیز است. در حال حاضر در بیشتر نقاط جهان هنوز حتی هزینهای برای انتشار دیاکسیدکربن وجود ندارد. سیاستگذاران باید مطمئن شوند که مکانیسم هزینه، ترجیحاً به روشی هماهنگ، معرفی و اجرا شود و از عمل به سیاستهایی که به نفع فناوریهای کربن خنثی هستند دفاع کنند. برای این اهداف باید توافقات چندملیتی یا در صورت امکان جهانی برقرار شوند.
در چشمانداز جهانی ژئوپلیتیک و اقتصاد در حال تغییر امروز این موضوع چالشبرانگیز به نظر میرسد. کارخانههای فولاد یکپارچه که فولاد را از سنگ آهن تولید میکنند، ۷۰ درصد از تولید جهانی فولاد را تشکیل میدهند، اما تقریباً ۹۰ درصد از دیاکسیدکربن این صنعت را منتشر میکنند (۲.۳ تن دیاکسیدکربن در هر تن فولاد تولیدشده برای محدوده ۱-۳). در مقابل، کارخانجات کوچک یا بهاصطلاح مینیمیلها (mini-mills) که از فرآیند کوره قوس الکتریکی (EAF) بر پایه قراضه بازیافتی بهعنوان خوراک اولیه استفاده میکنند، ۳۰ درصد از تولید جهانی فولاد را تشکیل میدهند؛ اما تنها باعث ۱۰ درصد از انتشارات میشوند، زیرا ۰.۶ تن دیاکسیدکربن در هر تن فولاد تولید میکنند. فولاد تولیدشده با این حال، در بخشهایی از جهان که شاهد رشد سریع تولید فولاد هستیم، مانند هند، عرضه محدودی از قراضه محلی وجود دارد و رشد تولید فولاد بر اساس خوراک سنگ آهن است که عمدتاً در کارخانههای یکپارچه استفاده میشود. درحالیکه مینیمیلها پتانسیل حذف تقریباً تمام انتشار دیاکسیدکربن خود را دارند (با استفاده از انرژی الکتریکی تجدیدپذیر و هیدروژن سبز در کارخانههای خود)، پلنتهای یکپارچه نمیتوانند به انتشار صفر برسند. مثلاً در یک کارخانه یکپارچه فرآیند کوره بلند برای کار به حداقل سطح مشخصی از کک نیاز دارد (حدود ۳۰۰ کیلوگرم بر تن) که استفاده آن باعث انتشار دیاکسیدکربن خواهد شد. بنابراین، پلنتهای یکپارچه یا به راههایی برای جذب و جداسازی انتشارات دیاکسیدکربن خود نیاز دارند، یا نیاز به تغییر اساسی در مسیر فرآیند تولید با پیامدهای CAPEX و OPEX بالایی دارند.
معادلات جهانی بهشدت دچار تغییر شدهاند و صنعت فولاد نیز از قاعده مستثنا نیست. ظرفیت تولید فولاد چین بهتنهایی بیشتر از جمع آمریکا، اتحادیه اروپا و ژاپن است (حدود ۵۵ درصد از فولاد جهان در چین تولید میشود). این رشد عظیم در تولید فولاد چین طی ۳۰ سال اخیر اتفاق افتاده است و بیشتر کارخانهها بر پایه مسیر کوره بلند هستند. این در حالی است که کل تولید فولاد در ۷ کشور صنعتی (G۷) حدود ۲۰ درصد تولید جهانی و با ردپای کربن بسیار پایینتر از متوسط ۸۰ درصد دیگر است؛ بنابراین باید به دنبال توافقنامهها و اقداماتی بود که چنین ناترازیهایی را در پیششرطها به شیوهای سازنده در نظر بگیرد و همچنین دربرگیرنده گسترش آینده تولید فولاد در آفریقا و سایر مناطق جغرافیایی باشد. یک بحث چندقطبی محترمانه و سازنده برای رسیدگی و حلوفصل این مسائل جهانی ضروری به نظر میرسد. بهموازات توسعه موافقتنامههای بینالمللی، اقدامات فوری میتوان انجام داد، که بسیاری از آنها کمهزینه یا با دوره بازپرداخت کوتاه هستند. علاوه بر اقداماتی که بهمنظور افزایش بهرهوری انرژی انجام میگیرد، مسیرهای بیشتری وجود دارند که میتوان برای دستیابی به نتایج کوتاهمدت طی کرد.
در دسترس بودن منبع مناسب هیدروژن سبز به نیروی برق سبز و افزایش مقیاس الکترولایزرها بستگی دارد. خصوصاً مورد اول در مناطق مختلف جغرافیایی، مثلاً، در اروپا چالشبرانگیز است. هیدروژن آبی (blue)، با این حال، میتواند در مقیاس نسبتاً بزرگ در بسیاری از مناطق در دسترس باشد و جایگزین مناسبی حداقل در طول دوره گذار تلقی شود. تولید و استفاده از هیدروژن آبی نیاز به جذب و غنیسازی کربن (CCS) دارد، جایگزینی که میتواند در کارخانههای مبتنی بر کوره بلند و احیا مستقیم با استفاده از گاز طبیعی استفاده شود. گفتنی است که انتقال دیاکسیدکربن بسیار راحتتر از هیدروژن است. هنگام ارزیابی گزینههای مختلف، پیشنهاد میشود برای مقایسه با هزینه CCS، از آن بهعنوان هزینه فرصت استفاده شود. احتمالات دیگری نیز در این پلنتها وجود دارد؛ بهعنوان مثال، تبدیل گازهای خروجی به گاز فرآیندی یا زیستتوده برای تولید سوخت کمکربن که میتواند بهعنوان یک عامل احیاکننده استفاده شود. مثال دیگر اصلاح گاز ککسازی برای به دست آوردن H۲ - ترکیب شده با CCS - برای استفاده بهعنوان احیاکننده یا سوخت است. در کارخانههای مبتنی بر EAF حجم هیدروژن نسبتاً محدودی موردنیاز است تا با جایگزینی سوختهای فسیلی در موارد استفادهای، چون تزریق EAF، پیشگرمکنهای پاتیلها و کورههای پیشگرمکننده، ردپای کربن (محدوده ۱) به نزدیک به صفر کاهش یابد. اگر فناوریهایی برای افزایش بهرهوری انرژی در دسترس باشد، مثلاً، احتراق سوخت اکسیژنی، این کارخانهها برای جایگزینی همه سوختهای فسیلی تنها به ۱۲ کیلوگرم هیدروژن در هر تن فولاد نیاز دارند. در مقام مقایسه، تولید DRI تنها با استفاده از هیدروژن بهعنوان احیاکننده به حدود ۶۰ کیلوگرم هیدروژن در هر تن آهن نیاز دارد. بر این اساس، هیدروژن یک مینیمیل معمولی میتواند در محل کارخانه از یک الکترولایزر ۵۰ تا ۱۰۰ مگاواتی تأمین شود، که امروزه بهخوبی با مقیاس الکترولیزهای PEM و برق سبز موجود در مناطق خاص مطابقت دارد.