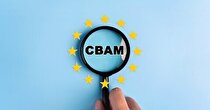
به گزارش می متالز، قاسم سلطانی با اعلام این خبر گفت: خوشبختانه از روزهای نخستین سال جاری، در راستای عمل به شعار سال (جهش تولید)، ظرفیتهای اضافه شده به تولید، محقق شده و در چهار ماه نخست سال سه مرتبه رکوردهای تولید پیشین این واحد ارتقا یافت که آخرین رکورد تولید ۱۸ هزار و ۹۶۰ تن ثبت شده است.
وی درباره شرایط و اهمیت تولید بریکیت گفتگویی دارد که متن کامل آن را در ادامه میخوانید:
قاسم سلطانی هستم، دارای مدرک لیسانس مهندسی شیمی از دانشکده فنی دانشگاه تهران؛ در اواخر سال ۶۶ با حضور داوطلبانه در جبهه و به واسطه دوستانی که آن موقع در مجتمع فولاد اهواز مشغول به کار بودند با شرکت آشنا شده و پس از مراجعه در سال ۶۷ بورسیه شرکت شدم و در فروردین ماه سال ۶۹ رسما به استخدام شرکت درآمدم. از بدو ورود به شرکت در واحدهای مختلفی در بخش احیا مانند احیا ۲، احیا ۳، برنامهریزی تولید و از سال ۷۵ در واحد بازیافت ضایعات صنعتی (احیا یک) مشغول به کار هستم. در طول ایام خدمت دورههایی همچون، دوره فرآیند احیای مستقیم در شرکت هامبورگ اشتالورگ کشور آلمان، در رابطه با بریکتسازی و دو دوره ۱۰ روزه در فرانسه و تعداد زیادی دورههای مدیریتی و فنی را گذراندهام.
در زمان راهاندازی فولاد خوزستان که تقریبا مقارن با ورود من به شرکت بود واحد بریکت سرد وجود نداشت و نرمههای اسفنجی تولید شده یا درون بشکههای ۲۰۰ لیتری ریخته شده و با زنبیل شارژ کوره قوس میشد و یا درون محوطهها دپو میگردید که دردسرهای فراوانی برای شرکت به دنبال داشت. از زمانی که واحد تولید بریکت گرم در شرکت متوقف شد، واحد با طراحی متفاوت و تماما بومی، تغییر کاربری شد. مسیر شارژ نرمه اسفنجی به ماشینهای بریکتزنی، مسیر خروجی بریکت تولید شده از ماشین، مخلوط کننده و سایر متعلقاتی که ماشین بریکتزنی را دارا است، بومیسازی گشته و سالها است که واحد در حال بهرهبرداری و تولید هست.
نرمه آهن اسفنجی که مواد اولیه بریکتسازی به شمار میآید، در فرآیند احیای مستقیم، همزمان با حرکت گندله در کوره احیای مستقیم و عملیات احیا ایجاد میشود. این نرمه با درجه فلزی و میل ترکیبی بالا، در کوره قوس الکتریکی به بار فلزی تبدیل نشده و همزمان با شروع قوس در بیشتر مواقع، شعله کشیده و به بار فلزی تبدیل نمیشود و با میل ترکیبی بالا امکان ایجاد آتشسوزی گسترده در خطوط شارژ میکند.
برای پیشگیری از این امر، نرمه آهن اسفنجی در اسکرینهای پیش از ورود به کورههای قوس، غربال شده و با جداسازی آن خوراک واحد بریکتسازی میشود. در ماشینهای بریکتزنی با استفاده از مخلوط (سیلیکات سدیم و آهک هیدراته با نسبت یک به چهار) چسبی آماده میشود که با ورود به مخازن بریکتزنی، با استفاده از یک حلزونی مابین دو دستگاه قرارگرفته و با فشاری حدود ۱۶۰ بار تبدیل به خشته یا بریکت میشود.
بریکت یک ماده بسیار با ارزش است، در بیان دیگر، نرمهای که به هیچوجه قابلیت تبدیل به بار فلزی را ندارد، به یک ماده بسیار با ارزش تبدیل میشود که حتی قابلیت جایگزینی آهن قراضه را دارد. البته موارد مصرف و مشتریان بسیاری دارد که به دلیل کمبود بار فلزی، مورد مصرف خود شرکت فولاد خوزستان قرار میگیرد.
از ۶ ماه پیش، به دلیل افزایش ظرفیت تولید شرکت و به تبع آن افزایش تولید نرمه، واحد بازیافت ضایعات صنعتی با حجم بیسابقهای از ورود نرمه آهن اسفنجی مواجه شد، به گونهای که ظرفیت تولید واحد با میزان نرمه ورودی متناسب نبود. این امر منجر به انباشتگی بسیاری از نرمه آهن اسفنجی در اطراف واحد شد.به دلیل میل ترکیبی بالا با اکسیژن، درجه و خلوص فلزی آن از دست رفته و در کنار ایجاد شرایط ناایمن، هدررفت پول را به همراه داشت.
در زمان مواجهه با این چالش، به همراه دیگر همکاران واحد، بر روی گلوگاهها و تنگناها تمرکز شد و خوشبختانه با دو طرح ابتکاری که نتیجهی یک کار تیمی به شمار میآید، ظرفیت تولید واحد بدون اضافه نمودن ماشینآلات بالا برده شد. خوشبختانه از روزهای نخستین سال جاری، در راستای عمل به شعار سال (جهش تولید)، ظرفیتهای اضافه شده به تولید، محقق شده و در چهار ماه نخست سال سه مرتبه رکوردهای تولید پیشین این واحد ارتقا یافت که آخرین رکورد تولید ۱۸ هزار و ۹۶۰ تن ثبت شده است.
رکورد تولید در فروردین ماه ۱۸ هزار و ۳۰۰ تن، اردیبهشتماه ۱۸ هزار و ۴۰۰ تن و در تیرماه ۱۸ هزار و ۸۰۰ تن به ثبت رسید که تا حدی عقبافتادگی خردادماه جبران شد.
با انتشار کرونا در جامعه، علیرغم رعایت پروتکلهای بهداشتی، از ابتدای فروردینماه تعداد از کارکنان واحد دچار کرونا شده و تعداد کارکنانی که سالم مانده بودند، تمامی ایام تعطیل و کاری را به صورت دو شیفت، در شرایط بسیار سخت و طاقتفرسا با ایثارگری به انجام کار پرداختند.
فروش گندله در ایام کرونا، نقش کلیدی و حیاتی برای شرکت داشته است؛ زیرا برخی از فروشندگان، آهن اسفنجی را در قبال معاوضه با گندله به شرکت میدادند. سیستم فروش و بارگیری گندله نیز در این واحد انجام میشد که به دلیل تردد بیش از حد رانندگان کامیونها و رانندگان بیرون از شرکت با وجود رعایت پروتکلها بهداشتی، شاید یکی از دلایل اصلی شیوع بیماری در این واحد بوده باشد.
بومیسازی قطعات از چند سال پیش با توجه به تحریمها، آغاز شد. بریکتسازی در عین کوچک بودن به لحاظ وسعتی، بسیار گرانقیمت است. هزینه تعمیر و نگهداری تجهیزات و قطعات یدکی واحد مانند، زیگمنتهای بریکتسازی که هر ست خارجی آن ۱۵۰ هزار یورو قیمت دارد بالا بوده و در سال که چهار ست زیگمنت مصرف شود، ۶۰۰ هزار یورو به شرکت تحمیل مینمود.
خوشبختانه با در اختیار گذاشتن اطلاعات پردازشی و فنی، قطعه سازان داخلی موفق شدند که با یک ششم قیمت خارجی این قطعه بسیار مهم را تولید کنند. همچنین با همت همکاران واحد ساخت و در میان گذاشتن اطلاعات و مسائل فنی، بسیاری از مواردی که در سالهای قبل گریبان گیر واحد بود، برطرف شد. البته قرار گرفتن در تنگناهای تحریم به نوعی سبب خیر گشته که با تلاش تمامی همکاران در حال حاضر حدود ۹۰ درصد از نیازهای قطعاتی واحد در داخل تولید میشود.
با پیگیریها و رعایت دستورالعملها و استانداردها و موارد گشت VIP و نظارت دقیق حوادث تا حدود زیادی کنترل شده است.
گشت VIP، گشتهای ایمنی، محیط زیست و بهداشت شرکت هستند که به صورت گروهی، از بخشهای مختلف بهرهبرداری بازدید کرده و موارد مربوط به ایمنی، بهداشت و محیط زیست را بررسی نموده و ایرادهای موجود را به واحد مربوطه منعکس نموده و آن واحد، موظف است در یک زمان و با برنامه مشخص موارد اشکال را رفع نموده و گزارش آن را به دبیر کمیته VIP منعکس نماید. در نهایت نمرهای که گشت VIP به یک واحد میدهد در ارزیابی عملکرد این واحد تاثیر به سزایی دارد.