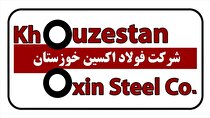
به گزارش میمتالز، حتما شما هم میدانید که در بازار انواع مختلفی از ورق فولادی وجود دارد که هر کدام کاربردی اختصاصی داشته و برای یک هدف خاص مورد استفاده قرار میگیرند. ورق سیاه، یکی از این محصولات است که حجم فروش آن در بازار آهن ایران و حتی جهان بسیار بالاست.
به طور کلی برای تولید انواع ورق فولادی میتوان از دو روش مختلف به نامهای نورد سرد و نورد گرم استفاده کرد. محصولی که به عنوان خروجی از فرآیند تولید نورد گرم خارج میشود؛ ورق سیاه و محصولی که به روش نورد سرد تولید میشود؛ ورق روغنی نام دارد.
حال شاید برای شما این سوال پیش بیاید که اصلا نورد به چه معنایی است؟ نورد در واقع یک فرآیند تولید در صنعت فولاد است. در این شیوه، ورق فولادی با استفاده از حرارت گرم شده و طی یک فرآیند کششی، تبدیل به محصول نهایی میشود. از ورقهای فولادی تولید شده به این شیوه بیشتر برای ساخت انواع ظروف آشپزخانه استفاده میشود. کارخانه فولاد مبارکه اصفهان، بزرگترین تولیدکننده این نوع ورقها در کشورمان محسوب میشود.
در شیوه تولید نورد گرم، ابتدا شمشهای ریختهگری به بیلت و شمش تبدیل میشوند تا فرآیند تولید ورق با سرعت بیشتری انجام شود. سپس بسته به نوع محصولی که قرار است تولید شود؛ نوبت به مرحله شکلدهی میرسد. به عنوان مثال عملیات شکلدهی محصولی مانند مفتول متفاوت از فرآیندی است که در این مرحله برای تولید مقاطع ساختمانی، میلگرد و ورق انجام میشود.
نورد سرد نیز که دومین روش تولید انواع مقاطع فولادی است؛ با حرارت کمتری انجام میشود. در این شیوه تولید، شمش در دمایی پایینتر از دمای تبلور مجدد قرار گرفته و تبدیل به محصول نهایی میشود. در اکثر کارخانهها برای تولید تسمه و ورق از این شیوه استفاده میشود. یکی از اصلیترین تفاوتهای بین محصولات تولیدی به روش نورد سرد و نوردگرم، کیفیت ابعاد و مشخصات مکانیکی بهتر محصولات گروه اول است.
ورق سیاه یک صفحه آهنی است که به دو صورت رول و شیت یا همان برش خورده به بازار عرضه میشود. اما چرا به این محصول ورق سیاه گفته میشود؟ همانطور که در بالا نیز به آن اشاره شد؛ ورق سیاه با استفاده از تکنولوژی نورد گرم تولید میشود. از آنجایی که در این شیوه تولید، مواد اولیه در معرض دمای بالا قرار گرفته و ذوب میشود؛ رنگ تیره و کدری به خود میگیرد. به همین خاطر در بازار به این ورقها که ظاهر و رنگ تیرهتری دارند؛ ورق سیاه گفته میشود.
برای تولید محصولی به نام ورق سیاه، ابتدا تختال تولید شده در کورههای مخصوصی به نام کورههای پیش گرم در معرض دمای بالا قرار میگیرد. در این فرآیند روی سطح تختال پوستهای اکسیدی شکل میگیرد. در مرحله بعدی برای حذف این پوسته، عملیاتی به نام پوستهشویی انجام میشود. این عملیات علاوه بر از بین بردن پوسته اکسیدی، باعث کاهش دمای تختال نیز خواهد شد.
مرحله بعدی نورد خشن نام دارد که در آن قطعه کار چندین مرتبه از بین غلتکهای مخصوصی عبور داده میشود تا به ابعاد و ضخامت مورد نظر برسد. دمای توزیع شده در این فرایند تحت تاثیر عواملی مانند انتقال حرارت به محیط و گرمای ناشی از تغییر شکل پلاستیک است. این تغییرات باعث میشوند که ضخامت تختال بین ۱۵ تا ۳۰ درصد کاهش پیدا کند.
در خط تولید نورد گرم، اصلیترین اجزا عبارتند از:
کوره پیش گرم محلی است که در آن تختال به دمای تقریبی ۱۲۰۰ تا ۱۲۵۰ درجه سانتیگراد میرسد. این مرحله کمک میکند تا عناصر آلیاژی داخل تختال حل شده و عیوب ساختاری آن که معمولا ناشی از ریختهگری هستند رفع شود. رساندن دمای ماده اولیه به حدی که نه در استفاده از انرژی اسراف شود و نه رسوب سختی که ناشی از دمای پیش گرم پایین است تشکیل شود؛ بسیار مهم است.
این مرحله در واقع همان مرحله پوستهشویی است که توسط آب انجام شده و تختالها را آماده ورود به قفسههای خشن کار میکند. ضخامت تختالها در چندی مرحله نورد خشن، تا حدود ۷۵ درصد کاهش پیدا میکند. این کاهش ضخامت، به معنی افزایش عرض ورق است. برای جلوگیری از افزایش عرض بیرویه، غلتکهای عمودی در اطراف این قفسهها تعبیه شده که کارشان کنترل عرض ورق میباشد. تختالها بعد از کاهش ضخامت در این مرحله، یا باید وارد جعبه کلاف شده و یا به صورت مستقیم وارد قفسههای نورد نهایی شوند.
در میز انتقال تختال بین قفسههای خشن و نورد نهایی، جعبه کلاف واقع شده است. وظیفه اصلی این جعبه، کلاف طول خط نورد میباشد. شکستن پوستهها، همگنسازی دمای ورق که موجب ایجاد خواص مکانیکی یکنواخت در محصول میشود و افزایش ظرفیت تولید از دیگر مزایای استفاده از جعبه کلاف در خط تولید ورق سیاه است. در انتهای مسیر این میز، ورق از حالت کلاف خارج میشود. چرا که باید قبل از ورود به قفسههای نورد نهایی پوستهزدایی شود.
در این مرحله تولید، بین ۵ تا ۷ قفسه وجود دارد که پشت سر هم واقع شدهاند. بعد از رسیدن ورق به دمای مناسب، وارد اولین قفسه از نورد نهایی شده و سپس پشت سر هم، از قفسههای دیگر نیز عبور میکند. ورقها باید با سرعتی بین ۱۰ تا ۲۰ متر بر ثانیه از این قفسهها عبور کنند تا ضخامتشان به ۱ تا ۴ میلیمتر برسد. قفسههای نورد نهایی نیز مانند قفسههای خشن کار معمولا دارای ۴ غلتک هستند. یکی از اصلیترین مراحل تولید، اندازهگیری ضخامت و دمای ورق در ورود به خط نهایی و زمان خروج از آن است. در این مرحله سیستم خودکار کنترل، وظیفه اندازهگیری و کنترل ضخامت ورق و تغییر سرعت نورد نیز وظیفه اندازهگیری و کنترل دمای آن را بر عهده دارد.
بعد از خروج ورقها از قفسههای نورد نهایی، باید دمای آنها کاهش پیدا کرده و اصطلاحا خنک شوند. این مرحله حتما باید تحت شرایط کنترل شدهای انجام شود. هدف نهایی نیز رسیدن دمای ورق از ۸۵۰ درجه سانتیگراد به دمای مناسب برای کلافپیچی یعنی ۵۸۰ درجه سانتیگراد است. بعد از رسیدن به این دما، ورق سیاه به صورت کلاف درآمده و مرحله کاهش دما و آمادهسازی برای بارگیری انجام میشود.
دمای ورقها بعد از خروج از مرحله خنککاری اندازهگیری میشود تا اگر به حد استاندارد رسیده باشد؛ مرحله کلافپیچی انجام شده و محصول آماده ورود به بازار شود.
خروجی مراحلی که تشریح کردیم؛ یا ورق سیاه صنعتی یا ورق سیاه معمولی است. تفاوت عمده این دو محصول، استانداردی است که در تولیدشان مورد استفاده قرار میگیرد. ورقهای سیاه صنعتی معمولا با نام تجاری ST۳۷ به بازار عرضه شده؛ اما ورقهای سیاه معمولی را میتوان با نامهایی نظیر A۵۱۶-GR۶۰,۷۰، A۲۸۵-GR C، A۲۸۳-GR C و ST۵۲ در بازار یافت.
صنایع مهمی مانند پتروشیمی، سدسازی، تانکرسازی، ساختمان و ساخت و ساز سنگین فلزی بیشترین تقاضا را برای خرید این نوع ورق دارند.
منبع: خبر آنلاین