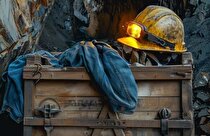
به گزارش میمتالز، در این یادداشت، مهندس مهدی پروان مدیر برنامه ریزی و توسعه شرکت صنعتی و معدنی توسعه فراگیر سناباد (سیمیدکو) به تشریح تفاوت روشهای مذکور پرداخته است.
از لحاظ فرآیندی مرحله اول و دوم گندله سازی در این دو تکنولوژی یکسان بوده و تفاوت دو روش آلیس چالمرز و لورگی در نحوه پخت متفاوت و نوع کورههای پخت این دو تکنولوژی میباشد.
در روش آلیس چالمرز که با الهام از کورههای طراحی شده در صنایع سیمان میباشد، پخت گندله در سیستم گریت- کوره دوار در چهار مرحله خشک شدن، پیش گرمایش، پخت، خنک کن صورت میگیرد.
در روش لورگی، گندلهها در کوره پخت روی هم قرار گرفته و حرکت داده میشوند که با عبور هوا از درون بستر گندله در مناطق مختلف دمش، مکش، پیش گرمایش، پخت و خنک کن عملیات سخت کردن به انجام میرسد.
در مقایسهای که از لحاظ فنی و اقتصادی بین این دو روش صورت گرفته است مهمترین تفاوتهای این دو روش مورد بررسی قرار گرفته است.
حداکثر ظرفیت نصب شده: در حال حاضر ظرفیت پلنتهای نصب شده در جهان برای تکنولوژی آلیس چالمرز ۶ میلیون تن در سال توسط کوبه استیل در بحرین و پلنت ۹٫۲۵ میلیون تن در سال سامارکو ۴ در برزیل با تکنولوژی لورگی میباشد.
محدوده ظرفیتهای تولید: پلنتهای لورگی محدوده وسیعی از ظرفیتهای تولید از ظرفیتهای پایین شامل ۱ تا ۱٫۲ میلیون تن، ۲٫۵ تا ۳ میلیون تنی، ۵ میلیون تن و بیشتر از ۵ میلیون تنی را شامل میشود. در تکنولوژی آلیس چالمرز پلنتها با ظرفیت ۱٫۲ میلیون تنی ۲٫۵ و ۳٫۴ میلیون تن و ۶میلیون تنی موجود میباشد.
ظرفیت جهانی تولید: ظرفیت جهانی تولید در پلنتهای آلیس چالمرز تاکنون ۱۳۸٫۴ میلیون تن و برای تکنولوژی لورگی ۳۶۰ میلیون تن بوده است.
مکان پلنتها: در دهههای اخیر بیشترین احداث پلنتهای آلیس چالمرز در چین صورت گرفته است. ظرفیت پلنتهای احداث شده در چین با این روش عموما پایین بوده و در جهت افزایش حجم تولید گندله در چین صورت گرفته است. در تکنولوژی لورگی توزیع پلنتهای احداث شده یکنواختتر بوده و بیشتر در محدوده آمریکا و آسیا گسترده شده است.
ظرفیت پلنتهای در حال تولید در ایران: تنها پلنت موجود در حال کار در ایران به روش آلیس چالمرز پلنت ۳٫۴ میلیون تنی اردکان بوده، اما در حال حاضر سه پلنت در حال کار به روش لورگی در ایران وجود دارد که شامل پلنتهای مبارکه خوزستان و گل گهر با ظرفیت تولید ۱۷٫۵ میلیون تن در سال میباشد.
CAPEX: میزان Capex برای پلنتهای آلیس چالمرز با تکنولوژی اروپایی بالاتر از پلنتهای لورگی با همان ظرفیت میباشد.
کل زمان عملیات پخت: زمان عملیات پخت در پلنتهای آلیس چالمرز بالاتر بوده و بسته به طراحی به طور تقریبی تا ۷۰ دقیقه و برای پلنت لورگی زمان پخت تقریبی حدود ۴۰ دقیقه خواهد بود.
نحوه انتقال حرارت: نحوه انتقال حرارت در این دو تکنولوژی با هم متفاوت میباشد. در تکنولوژی آلیس چالمرز بیشتر انتقال حرارت به روش تشعشعی انجام گرفته و نقش کانوکشن و جریانهای همرفتی در انتقال حرارت ناچیز میباشد. انتقال حرارت در پلنتهای لورگی به روش همرفت و کانوکشن صورت گرفته و نقش تشعش در آن ناچیز میباشد.
پروفایل حرارتی: در تکنووژی لورگی بسته به مواد اولیه ورودی امکان تنظیم پروفایل حرارتی و تغییر آن برای کنترل فرآیند پخت در داخل کوره با استفاده از مشعلها و کنترل دماهای نواحی داخل کوره وجود دارد. در رابطه با تکنولوژی آلیس چالمرز به دلیل تک مشعلی بودن روتاری کیلن و انجام عملیات Firing در این ناحیه امکان تغییر پروفایل حرارتی وجود ندارد.
مقدار FeO: در تکنولوژی لورگی مقدار FeO باقیمانده در محصول کمتر بوده، اما در تکنولوژی آلیس چالمرز مقدار FeO محصول بیشتر است.
احتراق گوگرد: در تکنولوژی لورگی مقدار گوگرد باقیمانده در مرحله پخت ناچیز بوده، اما در تکنولوژی آلیس چالمرز مقدار از گوگرد در مرحله خنک کن وارد شده و واکنش در آنجا ادامه مییابد.
تعداد فنهای فرآیندی: فنهای فرآیندی در تکنولوژی آلیس چالمرز ۸ عدد و در تکنولوژی لورگی ۵-۶ عدد میباشد.
ارتفاع سالن پخت: ارتفاع سالن پخت در تکنولوژی آلیس چالمرز بیش از لورگی میباشد.
تعداد مشعل ها: در فرآیند آلیس چالمرز یک مشعل در روتاری کیلن وجود دارد در حالیکه در فرآیند لورگی تعداد مشعلها زیاد و حدود ۳۴ تا ۳۶ مشعل است که نیاز به تعمیرات و نگهداری بیشتری خواهد داشت.
درصد تولید نرمه: به دلیل تعداد نقاط ریزش و نحوه حرکت مواد در روتاری کیلن میزان تولید نرمه در تکنولوژی آلیس چالمرز بالا بوده و حدود ۷-۸ درصد میباشد در حالیکه این مقدار در تکنولوژی لورگی حدود ۳ درصد است.
نحوه حرکت مواد در کوره: در قسمت اول تکنولوژی آلیس چالمرز مواد بر روی گریت ثابت بوده و در آلیس چالمرز در قسمت روتاری کیلن حرکتی غلطشی دارند. در لورگی مواد بر روی تراولینگ گریت ثابت و بدون حرکت میباشند.
تشکیل غبار: مقدار غبار ایجاد شده در فرآیند آلیس چالمرز بیشتر میباشد. این امر به دلیل تعداد نقاط ریزش بیشتر و حرکت غلطشی در داخل روتاری کیلن میباشد که موجب ایجاد نرمه بیشتر و تشکیل غبار بیشتر در این تکنولوژی است.
مزیت نوع حرکت مواد: در تکنولوژی آلیس چالمرز حرکت مواد باعث انتقال حرارت بهتر و پخت یکنواختتر گندلهها میشود در حالیکه در تکنولوژی لورگی به دلیل ثابت بودن حرکت مواد انتقال حرارت در لایههای مختلف بستر جامد متفاوت بوده و این امر بر میزان پخت گندله در لایههای مختلف تاثیر میگذارد.
گرید گندلههای تولیدی: گندلههای تولیدی در هر دو تکنولوژی برای استفاده در فرآیند احیا مستقیم و کوره بلند مناسبند. البته باید به این مساله توجه داشت که در رابطه با تکنولوژی آلیس چالمرز به دلیل سطح صافتر و پخت بیشتر مسیرهای عبور گاز در گندله تا حدی بسته شده و میزان نفوذ پذیری گندلهها کاهش مییابد این امر باعث کاهش امکان نفوذ گاز در فرآیند احیا مستقیم به داخل گندله شده و احیا پذیری گندله کاهش مییابد.
ارتفاع بستر جامد: در تکنولوژی لورگی ارتفاع بستر جامد بیشتر است. این ارتفاع در تکنولوژی لورگی ۲۵-۳۸ سانتی متر به طور تقریبی بوده و در تکنولوژی آلیس چالمرز به طور تقریبی ۱۲-۲۳ سانتی متر میباشد.
سیکل حراتی: در آلیس چالمرز فرآیند پخت در سه تجهیز مجزا صورت میگیرد. (گریت، روتاری کیلن، کولر)، اما در لورگی مراحل پخت در یک تجهیز به نام تراولینگ گریتانجام میشود.
لایه محافظ: در تکنولوژی لورگی به دلیل استفاده از پلت کارها برای حرکت مواد در داخل کوره و امکان آسیب به پلتها در دمای بالا ابتدا یک لایه محافظ بر روی پلتها ریخته شده سپس گندلههای خام بر روی این لایه قرار میگیرد در حالی که تکنولوژی آلیس چالمرز نیازی به این لایه محافظ ندارد.
تعمیرات و نگهداری: میزان تعمیرات و نگهداری در تکنولوژی آلیس چالمرز بیشتر از تکنولوژی لورگی میباشد. این امر در رابطه با فرسایش بخش گریت، تماس نسوزها با مواد در کیلن که موجب تشکیل چانک و فرسایش نسوزها میشود و عمر مفید نسوزها را به شدت کاهش میدهد و تعیرات احتمالی ناشی از خستگی رینگ کوره روتاری کیلن است. تعمیرات کیلن و نسوز چینی آن احتیاج به توقف و سرد کردن کوره دارد تا بتوان نسوز چینی مجدد انجام داد و این امر علاوه بر هزینه بالاتر تعمیرات بر مقدار در دسترس بودن پلنت تاثیر گذاشته و مقدار ساعت کاری پلنت در سال را کاهش میدهد. در تکنولوژی لورگی مواد اولیه با نسوزها تماس نداشته و مواد بر روی پلت کارها ریخته میشوند که امکان تعویض آنها در مدت کوتاه وجود دارد.
در دسترس بودن پلنت: در تکنولوژی لورگی به دلیل پایین بودن حجم تعمیرات زمان طولانی تری در دسترس است که این امر بر ساعات کاری در سال و مقدار تولید تاثیر میگذارد.
امکان ساخت تجهیزات در داخل: امکان ساخت برخی از تجهیزات از جمله دیسکهای گندله سازی، سازههای فلزی، سیستمهای غبارگیر و … برای هر دو تکنولوژی وجود دارد.
استفاده از بنتونیت: در تکنولوژی آلیس چالمرز به دلیل این که گندلهها باید در مراحل فرآیند پخت استحکام بالاتری داشته باشند و استحکام میانی نیز از اهمیت برخوردار است تا میزان نرمه کمتری تولید شده و از شکست گندلهها جلوگیری شود به مقدار بنتونیت بیشتری نیاز میباشد.
امکان استفاده از بایندرهای ارگانیک: در هر دو تکنولوژی امکان استفاده از این بایندرها گزارش شده است.
نوع سوخت مورد استفاده: در تکنولوژی آلیس چالمرز امکان استفاده از سخت جامد مایع و گازی وجود دارد در حالی که در تکنولوژی لورگی تنها از سوخت مایع و گازی میتوان بهره برد و امکان استفاده از سوخت جامد وجود ندارد.
تنوع در استفاده از سوخت: در تکنولوژی آلیس چالمرز تغییر سریع در نوع سوخت باعث تغییرات شدید حرارتی شده که بر کیفیت گندلههای تولیدی تاثیر میگذارد، اما بیشترین تاثیر آن بر شوکهای حرارتی بوده که بر عمر نسوزهای کوره تاثیر میگذارد. در حالیکه در تکنولوژی لورگی شوک حرارتی به نسوزها وارد نمیشود.
۳۱ابعاد طولی: تکنولوژی آلیس چالمرز نسبت به تکنولوژی لورگی ابعاد طولی کمتری دارد.
توقفهای ناگهانی: توقف ناگهانی در کوره کیلن امکانپذیر نبوده و این کوره میبایست به آهستگی سرد و تخلیه شود تا از هر نوع شوک حرارتی به کوره کیلن جلوگیری شود. در حالیکه در تکنولوژی لورگی امکان توقف ناگهانی کوره وجود دارد.
شروع مجدد: امکان شروع مجدد سریع در کوره کیلن وجود نداشته و به منظور جلوگیری از وارد آمدن شوک ناگهانی به کوره میبایست به گرم شود. در تکنولوژی لورگی امکان شروع مجدد سریع کوره وجود دارد.
مقدار برق مصرفی: مقدار برق مصرفی در تکنولوژی آلیس چالمرز کمتر از تکنولوژی لورگی میباشد. به عنوان نمونه در دو پلنت مشابه۲۵ کیلو وات ساعت بر تن در مقابل ۴۰ کیلو وات ساعت بر تن.
مقدار آب مصرفی فرآیند: مقدار آب مصرفی در تکنولوژی آلیس چالمرز بیشتر از تکنولوژی لورگی میباشد.
مقدار مصرف انرژی حرارتی: در تکنولوژی لورگی مقدار مصرف انرژی حرارتی کمتر از آلیس چالمرز است به عنوان مثال برای گندلههای مگنتیتی ۷۱۰-۹۵۰ مگا ژول بر تن در مقابل ۸۱۰-۹۵۰ مگا ژول بر تن آلیس چالمرز.
هزینه تولید: هزینه تولید گندله در روش لورگی کمتر از آلیس چالمرز میباشد. این امر به هزینههای تعمیرات بیشتر در فرآیند آلیس چالمرز و مقدار انرژی حرارتی کمتر تولیدی، سینکهای حرارتی فرآیند و … برای تولید گندله وابسته است.
انعطاف پذیری استفاده از مواد اولیه: تکنولوژی آلیس چالمرز برای مگنتیت و مخلوطی ازمگنتیت و هماتیت ثابت شده است. در رابطه با هماتیت تعداد کمی پلنت با این تکنولوژی تست شده است در حالیکه تکنولوژی لورگی برای مگنتیت، هماتیت و مخلوطی از این دو ثابت شده است.
کیفیت گندلههای تولیدی: گندلههای تولیدی در روش آلیس چالمرز پخت یکنواخت تری نسبت به تکنولوژی لورگی داشته و به دلیل نقش تشعشع در پخت گندلهها پخت سطحی بهتری دارند میزان پخت گندلهها در عمق به دلیل نقش تشعشع در انتقال حرارت کمتر است. در حالیکه نقش کانوکشن در این نوع پخت ناچیز بوده و نحوه پخت داخل گندلهها و کیفیت آنها باید مورد مطالعه قرار گیرد.
استحکام فشاری سرد: در روش آلیس چالمرز استحکام فشاری سرد بیشتر از روش لورگی است.
امکان احیا پذیری: مقدار احیا پذیری گندله به مسیرهای عبور گاز در گندله و میزان تخلخل گندله بعد از پخت بستگی دارد. در حالیکه کیفیت سطحی گندله در فرآیند آلیس چالمرز بهتر بوده و گندلهای با سطح صافتر و استحکام فشاری سرد بهتری تولید میکند در عین حال این امر مزیت احیا پذیر بودن گندله را نیز کاهش میدهد. در این فرآیند مسیرهای عبور گاز تا حدی بسته شده و امکان نفوذ گاز به داخل گندله کاهش مییابد که این امر باعث کاهش احیا پذیری گندلههای در فرآیند آلیس چالمرز خواهد بود.
امکان خوشهای شدن: به مواد افزودنی به گندلهها بستگی داشته و وابسته به تکنولوژی نیست.
ترکیب شیمیایی گندله تولیدی: به تکنولوژی بستگی نداشته و تنها در رابطه با میزان گوگرد و FeO باقیمانده تابع تکنولوژی میباشد.
امکان استفاده از تجارب پلنتهای مشابه و خدمات مشاوره ای: با توجه به وجود سه پلنت لورگی در ایران امکان استفاده از تجارب پلنتهای مشابه بیشتر از آلیس چالمرز میباشد.
مقایسه تکنولوژیهای آلیس چالمرز و لورگی نشان میدهد که در ظرفیتهای بالا و خوراکهای هماتیتی تکنولوژی لورگی بر تکنولوژی آلیس چالمرز ارجحیت دارد.
مهمترین مزیتهای این روش ظرفیتهای بالای اثبات شده، امکان استفاده برای خوراکهای صد در صد هماتیتی، توزیع یکنواختتر پلنتها در نقاط مختلف جهان، زمان پخت کمتر، امکان افزایش ظرفیت و تغییر در پروفایل حرارتی متناسب با بار ورودی، تولید نرمه کمتر، هزینههای تولید پایین تر، احیا پذیری بهتر گندله ها، امکان توقف و شروع ناگهانی، مقدار تعمیرات و نگهداری کمتر و در دسترس بودن بیشتر پلنت برای توزیع میباشد.
تکنولوژی آلیس چالمرز با مصرف برق کمتر، کیفیت بالاتر گندله تولیدی و استحکام فشاری بهتر، در صورتی که کیفیت گندله در رابطه با استحکام معیار اساسی انتخاب باشد میتواند در ظرفیتهای پایین جایگزین خوبی برای پلنتهای گندله سازی محسوب شود. به هر حال در انتخاب تکنولوژی مناسب برای فرآیند گندله سازی ابتدا باید فاکتورهای با اهمیت بیشتر برای پلنت مورد نظر شناسایی و سپس با توجه به تاثیر هر یک از پارامترها و امتیاز دهی و برتری هر پارامتر در تکنولوژیهای مورد بررسی نسبت به انتخاب تکنولوژی مناسب اقدام شود.
منبع: مجله خبری شرکت صنعتی و معدنی توسعه فراگیر سناباد