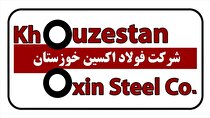
به گزارش میمتالز، علی امیری جانشین مدیریت راهبر پتاس، در بازدید خبرنگاران از مجتمع پتاس خور و بیابانک به تشریح فرآیند استخراج و فرآوری پتاسیم در این مجتمع پرداخت و از افزایش تولید و بهبود بهرهوری پس از واگذاری راهبری به بخش خصوصی خبر داد و افزود: مجتمع پتاس خور و بیابانک تنها معدن شورابهای کشور است که به بهرهبرداری رسیده و با وسعتی در حدود ۱۰۰۰ کیلومتر مربع، یکی از مهمترین منابع پتاس کشور محسوب میشود. این معدن در سال ۹۴ وارد فاز بهرهبرداری شد و فرآیند استخراج آن شامل انتقال شورابه از پوسته نمکی به استخرهای فرآوری است. سطح استخرهای این مجتمع بالغ بر ۱۳ میلیون مترمربع است که هر استخر آن یک میلیون مترمربع مساحت و بین یک تا ۱.۲ میلیون مترمکعب ظرفیت ذخیره شورابه دارد.
امیری با اشاره به تاریخچه زمینشناسی منطقه توضیح داد: این منطقه در گذشته یک دریاچه بوده که بین ۳ تا ۱۰ میلیون سال پیش خشک شده و پوستهای نمکی تشکیل داده است. شورابههای این منطقه حاوی ترکیبات مختلفی از جمله نمک طعام، نمک کلسیم، نمک منیزیم و مهمترین آن، نمک پتاسیم است که میزان آن در شورابه حدود ۵ تا ۷ گرم در لیتر است.
وی از تغییرات مثبت در فرآیند بهرهبرداری پس از واگذاری راهبری به بخش خصوصی در سال ۹۸ خبر داد و افزود:در دوره فعالیت دولتی، استخرها عمدتاً بر اساس فرآیند تبخیری عمل میکردند، اما پس از واگذاری، فرآیند به روشهای شیمیایی کنترل شد و استخرهای غیر فعال مجدداً به مدار تولید بازگشتند. این اقدامات موجب افزایش ظرفیت استخراج و بهرهوری شد.
جانشین مدیریت راهبر پتاس با اشاره به رکوردهای ثبتشده در سالهای اخیر اظهار داشت: در سال ۹۷ که آخرین سال فعالیت دولتی بود، تنها ۱۴۷ هزار تن کارنالیت استخراج شد، در حالی که در سال گذشته این میزان به ۴۲۰ هزار تن رسید. این در حالی است که شرکتهای آلمانی، ظرفیت اسمی این استخرها را حداکثر ۳۵۰ هزار تن برآورد کرده بودند، اما با تغییرات فناورانه و مدیریت بهینه، توانستیم از این سقف عبور کنیم.
وی افزود: در بخش جداسازی املاح نیز موفق شدیم سالانه حدود ۳ میلیون تن نمک طعام از استخرها خارج کنیم و فرآیندهای جدیدی را برای افزایش راندمان تولید به کار بگیریم. با همکاری شرکتهای آلمانی و متخصصان داخلی، ظرفیت تولید کارخانه فرآوری نیز به ۱۹ هزار تن افزایش یافته است.
امیری در ادامه بر چالشهای استخراج پتاس تأکید کرد و گفت: فرآیند استحصال تحت تأثیر عوامل محیطی مانند بارندگی، باد و تغییرات دمایی قرار دارد. با کنترل این عوامل و بهینهسازی فرآیندهای تولید، توانستیم راندمان تولید را افزایش دهیم و به استانداردهای بالاتری دست پیدا کنیم.
وی خاطرنشان کرد: بهرهبرداری علمی و مدون از این مجتمع معدنی، نه تنها موجب افزایش تولید و بهرهوری شده، بلکه زمینه توسعه پایدار و اشتغالزایی گسترده را نیز فراهم کرده است.
علی امیری به چالشهای این مجموعه در زمینه تأمین تجهیزات و مواد اولیه اشاره کرد و از موفقیت در بومیسازی یکی از مواد کلیدی تولید پتاس خبر داد.
وی با اشاره به مشکلات ناشی از وابستگی به تجهیزات خارجی گفت: در ابتدای راهاندازی، حدود ۹۰ درصد تجهیزات کارخانه آلمانی بود، زیرا این واحد بر اساس طراحی آلمان ساخته شده بود. اما این تجهیزات به مرور دچار فرسودگی شدند و با تحریمهای شدید، امکان تأمین قطعات یدکی و مواد اولیه وجود نداشت. مبدلهای حرارتی و سانتریفیوژهای ما با مشکلات جدی مواجه شدند و در آن زمان، به دلیل تحریمها، حتی قادر به واردات یک ماده کلیدی که کاربردهای خاصی داشت، نبودیم.
امیری با اشاره به تحریمهای شدید و ممنوعیت جهانی تأمین این ماده افزود: این ماده در لیست تحریمهای بینالمللی قرار داشت و حتی زمانی که تلاش کردیم آن را از شرکتهای دیگر تأمین کنیم، به دلیل حساسیتهای مرتبط با کاربردهای نظامی، هیچ کشوری حاضر به فروش آن نبود. در مقطعی کاملاً ناامید شده بودیم، اما تصمیم گرفتیم که به هر شکل ممکن، این ماده را در داخل کشور تولید کنیم.
وی با تأکید بر تلاشهای متخصصان داخلی اظهار داشت: با همکاری یک شرکت دانشبنیان در اصفهان، ظرف مدت تنها چهار ماه توانستیم این ماده را بومیسازی کنیم. این کار سادهای نبود، زیرا زنجیره تأمین این ماده شیمیایی بسیار پیچیده است، اما با دانش و تلاش مهندسان داخلی، توانستیم آن را تولید کنیم.
امیری به نتایج استفاده از این ماده داخلی اشاره کرد و گفت:در ابتدا، راندمان تولید با استفاده از ماده خارجی به ازای هر ۸.۵ تن ورودی یک خروجی مشخص داشت، اما زمانی که ماده داخلی را جایگزین کردیم، بسیاری از کارشناسان انتظار داشتند که راندمان به ۱۰ تن ورودی افزایش یابد. اما خوشبختانه، امروز میتوانیم بگوییم که این ماده حتی عملکردی بهتر از نمونه خارجی دارد. در حال حاضر، راندمان کارخانه به سطح ۶ تا ۶.۵ تن ورودی برای تولید یک واحد محصول رسیده است، که مطابق با استانداردهای ملی است.
منبع: خبرگزاری موج