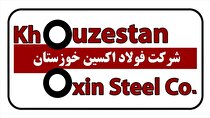
به گزارش میمتالز، نکته قابلتوجه این است که به غیر از الکترود گرافیتی، تمام مواد اولیه فولادسازان در داخل قابل تامین است و تنها نقطه آسیب در فرآیندهای مرتبط با قوس الکتریکی؛ الکترود گرافیتی است که چند سال پیش و با آغاز تحریمها شاهد بحران تهیه الکترود گرافیتی در بین فولادسازان بودیم.
البته باید یادآور شد که سنگ آهن نیز به عنوان ماده اولیه و اصلی فولادسازان به شمار میرود که اگر به چشم انداز ۵۵میلیون تن فولاد در افق چشم انداز سال ۱۴۰۴ دست پیدا کنیم، نیاز است یا معادن جدیدی در زمینه سنگ آهن اکتشاف کرده یا اینکه اقدام به واردات آن کنیم تا فولادسازان در زمینه تامین مواد اولیه خود مشکل نداشته باشند.
علاوه بر سنگ آهن به عنوان مواد اولیه فولادسازی، بین ۳۰ تا ۴۰ ماده اولیه به کار فولادسازان در کشور میآید. در این زمینه زکریا نایبی کارشناس حوزه فولاد عنوان کرد: در کارخانههای فولادسازی به روش EAF (فولادسازی به شیوه قوس الکتریکی) که در ایران رایج است، بین ۳۰ تا ۴۰ نوع ماده اولیه مورد استفاده قرار میگیرد که به ۴ گروه مهم تقسیم میشوند: در گروه نخست مواد اولیه آهن دار قرار دارند که عبارتند از: آهن قراضه و آهن اسفنجی، دسته دوم انواع فروآلیاژ هستند که شامل طیف وسیعی میشوند که پرمصرفترین آنها فروسیلیس و فرومنگنز و سیلیکو منگنز هستند. البته فروکروم، فرونیکل و... نیز در تولید فولادهای آلیاژی کاربرد دارند. برای تولید هر تن فولاد خام به ۱۵ تا ۱۷ کیلو فروآلیاژ نیاز است.
نایبی در ادامه از دسته سوم مواد اولیه موردنیاز فولادسازان نام برد و خاطرنشان کرد: دسته بعدی مواد اولیه موردنیاز فولادسازان، مواد سرباره ساز است که عمده آنها آهک و دولومیت هستند. به ازای تولید هر تن فولاد،
مورد استفاده قرار میگیرد. مقدار مصرف این مواد در شارژ کوره به میزان استفاده از قراضه یا آهن اسفنجی بستگی دارد. با افزایشدرصد آهن اسفنجی در بار کوره، مقدار سرباره ساز موردنیاز افزایش پیدا میکند، زیرا آهن اسفنجی حاوی ۲ تا ۵درصد سیلیس است که خاصیت اسیدی دارد و برای خنثی کردن آن از آهک و دولومیت که موادی قلیایی هستند، استفاده میشود.
این کارشناس حوزه فولاد در ادامه تصریح کرد: گروه سوم از مواد مصرفی موردنیاز فولادسازان، مواد نسوز هستند که انواع مختلفی از نظر ترکیب شیمیایی و شکل فیزیکی و نحوه کاربرد دارند. مواد نسوز منیزیتی و آلومینایی و اخیرا دولومیتی به شکل آجر و جرم بیشترین کاربرد را در فولادسازی دارند. جرمهای نسوز یا کوبیدنی یا ریختنی هستند. آجرهای نسوز نیز معمولا در کوره ها، پاتیلها و تاندیشها (ظروف انتقالی به عنوان واسطه بین پاتیل و قالب) مورداستفاده قرار میگیرد. به ازای تولید هر تن فولاد ۲ تا ۳ کیلوگرم نسوز استفاده میشود.
نایبی در ادامه گفت: گروه چهارم از مواد مصرفی موردنیاز فولادسازان عبارتند از: انواع کک و مواد کربن دار که برای تولید انرژی و تنظیمدرصدکربن در آنالیز فولاد مورد استفاده قرار میگیرد. وی در ادامه افزود: مواد اکسیژن زدا نیز به عنوان مواد اولیه در فولادسازی موردنیاز است که مهمترین این مواد بریکتهای اکسیژن زدا و آلومینیوم هستند. آلومینیوم قویترین اکسیژن زدا به شمار میرود که پس از آن منگنز و سیلیسیوم در رتبههای دوم و سوم اکسیژن زدایی قرار دارند.
این کارشناس فولاد در ادامه به مواد خاص موردنیاز فولادسازی اشاره کرد و گفت: سبوس برنج یکی از مواد خاص مورد استفاده در فرآیند فولادسازی است. سبوس برنج در حقیقت به عنوان یک لایه عایق حرارتی عمل میکند تا دمای مذاب دچار افت نشود. در فاصله انتقال مذاب از کوره پاتیلی به ایستگاه ریخته گری پیوسته، لایهای از سبوس برنج روی سطح مذاب در پاتیل افزوده میشود که به عنوان محافظ عمل میکند. یکی از ویژگیهای سبوس برنج داشتن ۸۰درصد سیلیس بلوری است که این نوع سیلیس بادرصد بالا در سبوس برنج یافت میشود. گفتنی است که برای تولید هر تن فولاد به نیم کیلو سبوس برنج نیاز است (البته این نوع سبوس که به فل مشهور است دقیقا با سبوس رایج که کاربرد دارویی دارد یکی نیست).
نایبی همچنین به ماده موردنیاز دیگر در فولادسازی اشاره و عنوان کرد: روغن پنبه دانه و پودر گرافیت موردنیاز در قالبهای مسی ریخته گری پیوسته مورد استفاده قرار میگیرد. کاربرد این نوع مواد، جلوگیری از چسبیدن مذاب به قالب است.
وی همچنین به کاربرد گازهای صنعتی در فولادسازی اشاره کرد و گفت: اکسیژن و آرگون گازهای پرمصرف در فولادسازی به شمار میروند. گاز اکسیژن در کوره قوس الکتریکی برای سوزاندن کربن و ایجاد حرارت و گاز مونواکسیدکربن و ایجاد سرباره پفکی و گاز آرگون در کوره پاتیلی به عنوان گاز همزن مذاب کاربرد دارند.
این کارشناس فولاد، الکترود گرافیتی را نیز ماده پرهزینه در فولادسازی برشمرد و عنوان کرد: مواد اولیه دیگر فولادسازان، الکترود گرافیتی است که در کورهها مورد استفاده قرار میگیرد. به ازای تولید هر تن فولاد، ۲ کیلوگرم الکترود گرافیتی استفاده میشود. الکترود گرافیتی سایزها و اندازههای مختلفی دارند که بر اساس مقدار جریانی که میتوانند از خود عبور دهند، تقسیم بندی میشوند. الکترودهای کوره پاتیلی کوچکتر از الکترودهای کوره قوس هستند.
نایبی در پاسخ به این پرسش که چه میزان از این مواد اولیه موردنیاز فولادسازان در داخل تهیه میشود و چه میزان وارداتی است، عنوان کرد: تمام مواد اولیه فولادسازان در داخل قابل تولید و تامین است، به غیر از الکترود گرافیتی که بعضا وارداتی است. مواد اولیه الکترود گرافیتی، گرافیت سوزنی است که در ایران قابل تولید نیست، از همین رو ناچار به واردات آن هستیم که عمدتا نیز از چین وارد ایران میشود. در سایر مواد اولیه این مواد معمولا با کیفیت بالا در داخل تولید میشوند.
این کارشناس فولاد در پاسخ به این پرسش که چنددرصد قیمت تمام شده فولادسازان شامل مواد اولیه میشود عنوان کرد: حدود ۷۰ تا ۸۵درصد قیمت تمام شده فولاد به مواد اولیه مربوط میشود که در این زمینه میتوان به ۶۰ تا ۶۵درصد آهن اسفنجی و آهن قراضه، ۵ تا ۱۰درصد الکترود گرافیتی، ۳ تا ۵درصد مواد نسوز، ۳ تا ۵درصد مواد سربارهساز و ۱ تا ۲درصد گازهای صنعتی اشاره کرد.
یکی از مواد اولیه موردنیاز فولادسازانی که ابتدای زنجیره را در اختیار دارند، تامین سنگ آهن است. در اینباره مجید محمودی، مشاور شرکت مهندسی فولاد مبارکه در گفتگو با «دنیایاقتصاد» عنوان کرد: یکی از مواد اولیه اصلی موردنیاز فولادسازان، سنگآهن است. سنگ آهن در یک فرآیندی تبدیل به کنسانتره و کنسانتره تبدیل به گندله، گندله تبدیل به آهن اسفنجی و آهن اسفنجی تبدیل به فولاد میشود. البته در کنار سنگ آهن، سایر افزودنیها مانند کک، آلومینیوم و... به فرآیند فولادسازی افزوده میشود. در فناوری کوره بلند که به زغالسنگ و کک نیاز دارد، سنگ آهن استفاده میشود و در فناوری احیای مستقیم که انرژی آن با گاز تامین شود نیز سنگ آهن موردنیاز است. در ایران ۸۰درصد فناوری فولادسازان با احیای مستقیم صورت میپذیرد. وی در ادامه افزود: بیشتر فولادسازان سنگ آهن را تبدیل به کنسانتره میکنند تا غلظت آهن آن را به ۶۵درصد برسانند، زیرا عیار سنگ آهن خام (کلوخه) استخراج شده در ایران بستگی به معادن بین ۳۵ تا ۵۰درصد دارد که ایندرصد را باید به ۶۵درصد رساند. برخی از کارخانههای فولادسازی که کنسانتره سازی نیز دارند، از همان ابتدا به سنگ آهن نیاز دارند. برخی فولادسازان گندله سازی دارند که به کنسانتره نیازمند هستند. در هر صورت یکی از اصلیترین مواد اولیه موردنیاز فولادسازان سنگ آهن است.
مشاور شرکت مهندسی فولاد مبارکه در ادامه با اشاره به قیمت سنگ آهن در ایران خاطرنشان کرد: سنگ آهن به صورت قیمتگذاری دولتی در اختیار فولادسازان قرار میگیرد و قیمت آن در پارهای اوقات حتی نصف قیمت جهانی بوده است و حتی در برخی مواقع نیز به یک سوم قیمت جهانی رسید؛ بنابراین ۴۰ تا ۵۰درصد سود فولادسازان مربوط به قیمت سنگ آهن است؛ از همین رو اگر قیمت سنگ آهن داخلی به قیمت جهانی برسد، حدود ۵۰ تا ۶۰درصد سود آنها کاهش پیدا خواهد کرد. البته باید به ارزان بودن قیمت گاز و برق در برابر قیمت جهانی نیز اشاره کرد که این انرژی ارزان سبب سود بیشتر فولادسازان در کشور نیز شده است.
محمودی در پاسخ به این پرسش که هم اکنون برای تامین سنگ آهن در کشور با مشکلی روبه رو نیستیم، گفت: سنگ آهن موردنیاز فولادسازان تاکنون تامین شده است، اما باید به این موضوع توجه داشت که اگر به برنامههای توسعه افق چشم انداز نزدیک شویم و ظرفیت و تولید فولاد کشور به ۵۵میلیون تن در سال ۱۴۰۴ نزدیک شود، بدون شک به تامین سنگ آهن بیشتری نیاز خواهیم داشت، زیرا معادن فعال سنگ آهن جوابگوی تولید ۵۵میلیون تن فولاد نخواهند بود، مگر اینکه تمام معادن سنگ آهن در کشور فعال شده یا معادن جدیدی کشف شوند که این موضوع نیاز به زمانی ۳ تا ۴ ساله خواهد داشت، در نتیجه رسیدن به چنین میزان تولیدی با توجه به معادن موجود کشور امکان پذیر نخواهد بود.
وی در پاسخ به این پرسش که آیا با توجه به این موضوع که حدود ۳ سال دیگر به افق ۱۴۰۴ ترسیم شده خواهیم رسید و رسیدن به ظرفیت ۵۵میلیون تن محقق خواهد شد، گفت: ممکن است که به ظرفیت ۵۰میلیون تن برسیم، چراکه از هم اکنون واحدهای فولادسازی جدیدی در دست اقدام هستند که تا چند سال دیگر وارد مدار تولید خواهند شد، اما امکان دارد که تمام واحدهای موجود با تمام ظرفیت خود کار نکنند. اما اگر به ظرفیت و تولید ۵۰ تا ۵۵میلیون تن فولاد برسیم، با توجه به معادن موجود در کشور ممکن است مجبور شویم به واردات سالانه ۲۰ تا ۳۰میلیون تن سنگ آهن اقدام کنیم.
محمودی در پایان تاکید کرد: یکی از گلوگاههای مهم توسعه در صنعت فولاد، تامین سنگ آهن است که همزمان با توسعه واحدهای فولادسازی باید به این مهم نیز توجه شود تا چشم انداز افق ۱۴۰۴ در صنعت فولاد و رسیدن به ۵۵میلیون تن فولاد محقق شود.
منبع: دنیای اقتصاد