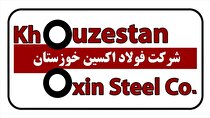
به گزارش میمتالز، اگر بخواهیم دراینبین از مثلاً نقش یک بازیکن بزرگ در تولید گازهای گلخانهای نام ببریم؛ میتوانیم به جاهایی اشاره کنیم که به تولید فولاد و آهن میپردازند: آنها تقریباً ۶.۱درصد از انتشار جهانی این آلایندهها را برعهده دارند! اینفوگرافیک حاضر که توسط مرکز تحقیقات AFRY (شرکت سوئدیِ فعال در حوزه انرژی) ارائه شده است؛ نیاز به تکامل روند و کربنزدایی تولید فولاد را نشان میدهد و اینکه چگونه هیدروژن میتواند نقشی حیاتی در انقلاب «فولاد سبز» (فولادی که بهگونهای ساخته میشود تا کمترین ردِپای کربن ممکن را طی تولید داشته باشد) ایفا کند. در سطح جهان، تولید فولاد خام در سال ۲۰۲۱ به ۱۹۵۱میلیونتن رسید. اینمیزان تولید در گستره بینالمللی؛ ازجمله «هند»، «ژاپن» و «ایالاتمتحده» پخش بوده و عمدهاش؛ یعنی ۱۰۳۳میلیونتن آن، در «چین» متمرکز شده است. البته بهرغم تولید در بسیاری از مکانهای مختلف در جوامع مختلف؛ تنها دو روش اصلی تولید این فلز درطولزمان ارائه شده و مورداستفاده قرار گرفته: «کوره قوس الکتریکی» (EAF) و «کوره بلند اکسیژن پایه» (BF-BOF). هردو روش نیز بهروش سنتی، از سوختهای فسیلی استفاده میکنند؛ که بالغبر ۳.۶گیگاتن دیاکسید کربن (CO۲) تولیدی در جهان طی سال ۲۰۱۹ حاصل فعالیت آنها بود. بههمیندلیل، یکی از راههای اصلی کربنزدایی صنعت فولاد، جایگزینی سوختهای فسیلیست. گرچه، یکی از بزرگترین چالشهای پیشروی این صنعت، نحوه کربنزدایی و تولید فولاد سبز در یک بازار رقابتیست. تولید فولاد بهعنوان یک کالای تجارت جهانی و با حاشیه هزینه خوب، با مسائل عمده ژئوپلیتیکی؛ ازجمله اختلافات تجاری و تعرفهها همراه بوده است؛ اما بهدلیل تغییرات آبوهوایی، تقاضای ناگهانی و انبوه برای تولید محصول کربندوست نیز وجود دارد؛ و اینجاست که «هیدروژن» نقش کلیدیِ خود را ایفا میکند. فولادی که بهطورسنتی در کوره بلند ساخته میشود، از «کُک» (سوختی با کربن بالا که با حرارتدادن زغالسنگ بدون هوا ساخته میشود) بهعنوان منبع سوختی برای گرمکردن گلولههای سنگآهن و مایعکردن اجزای خالص آهن استفاده میکند. تولید بااینروش، مقدار زیادی گازهای گلخانهای خارج میکند تا آهن بهاندازه لازم برای ذوب، گرم (۱۲۰۰درجهسانتیگراد) و با ضایعات مخلوط؛ و به فولاد تبدیل شود. در تولید «فولاد سبز»، از هیدروژن برای تبدیل گلولههای آهن به آهن اسفنجی، استفاده میکنند که متعاقباً برای تشکیل فولاد، پردازش خواهند شد. این فرآیند در دمایی بالا؛ اما زیر نقطه ذوبآهن (۸۰۰ تا ۱۲۰۰درجه) انجام میگیرد که باعث صرفهجویی در هزینههای انرژی میشود. با معرفی سوختهای غیرفسیلی برای تولید گندله آهن و نیز استفاده از برق تجدیدپذیر برای تبدیل آهن اسفنجی و ضایعات به فولاد، میتوان سوختهای فسیلی را از فرآیند موردنظر حذف کرد و درنتیجه، انتشار گازهای گلخانهای را بهمیزان قابلتوجه کاهش داد. باتوجهبه تقاضای عظیم جهانی برای فولاد، نیاز به هیدروژن و انرژی تجدیدپذیر موردنیاز در تولید «فولاد سبز» بههماناندازه قابلتوجه است. طبق گزارش AFRY و «آژانس جهانی انرژیهای تجدیدپذیر» (REA)؛ تولید جهانی فولاد در ۲۰۲۱ بهروش «فولاد سبز» به ۹۷.۶میلیونتن هیدروژن نیاز داشت. اینرا نیز باید درنظر داشت که برای انتقال مسیرهای تولید بهسمت روشهای بدون کربن و توسعه فولاد سبز؛ آنهم بهشکلی واقعی و صددرصد، صنعت انرژی همچنین باید بر تولید «هیدروژن سبز» بااستفادهاز «الکترولیز» تمرکز کند. درواقع، برخلاف روشهایی که گاز طبیعی را برای آزادکردن هیدروژن میسوزانند، «الکترولیز» مستلزم تقسیم «آب» (H۲O) به «اکسیژن» و «هیدروژن» بااستفادهاز منابع انرژی تجدیدپذیر است؛ بنابراین، تولید کامل «فولاد سبز» از «هیدروژن سبز»، نیازمندِ الکترولیزهای فعال بر روی انرژیهای تجدیدپذیر و انرژیهای تجدیدپذیر اضافی برای تمام بخشهای زنجیره تأمین است. اکنون، هزینههای تولید «هیدروژن سبز» بالاتر از روشهای سنتی سوختهای فسیلی بوده و به هزینههای همسطح منابع انرژی تجدیدپذیر وابسته است. اینبدانمعناستکه آنها بسته به منطقه متفاوتاند؛ اما با افزایش ظرفیت تولید و اختصاص یارانه برای انرژیهای تجدیدپذیر و هیدروژن سبز، کاهش خواهند یافت. بسیاری از تولیدکنندگان بزرگ فولاد اروپایی، با امکانات آزمایشی و در مقیاس بزرگ برای تولید «فولاد سبز» پیشرو هستند. کشور «آلمان» دراینزمینه بهتنهایی هفت پروژه دردستاقدام دارد؛ ازجمله ArcelorMittal و ThyssenKrupp که دومورد از ۱۰ فولادساز اول جهان ازنظر درآمد هستند. «ایران» نیز با تولید ۲۸.۵ میلیونتن فولاد، رتبه دهم اینردهبندی را دراختیار دارد.
مصطفی رفعت
منبع: روزنامه سراسری سایه